PT&D PROJECTS SCALE-UP DELIVERY ACROSS GEOGRAPHIES
Even as the world seeks to tame the pandemic, PT&D projects, across geographies, have adopted country and region-specific SOPs to evolve secure work approaches, using innovative construction methods and digital tools to fast-track execution and, at the same time, assuage client apprehensions.
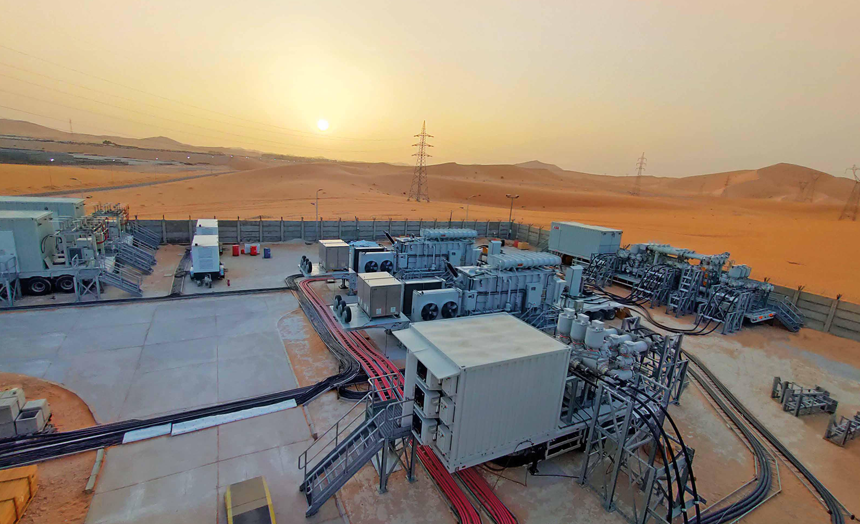
Prepping up for a quantum leap
The 275 kV Medamit-Lawas transmission line project in Malaysia is L&T’s first contract with Sarawak Energy Berhad and a vital power infrastructure scheme that will cater to the growing load demand and connect the distribution network in Lawas town to the grid through a 131 km transmission tower line. “This is easily one of our toughest overseas jobs undertaken in recent times,” puts forth Project Director, Shekar Sahu. “Usually, towers points are easy to spot, but here, it is tough to locate them as the alignment is in remote locations, running close to forests and hills. Our biggest challenge is to work across undulating terrains with no access to work locations.”
What helped Shekar and team was a detailed survey giving them insights on terrain criticalities. “Working smartly, even before hitting the ground, we developed special tower designs with longer spans for tower points across sensitive work zones such as deep valleys which reduced our scope of tower installations from 381 to 320. This in turn improved project scheduling, mitigated on-ground challenges, enhanced safety and saved close to 17% of construction time. Later, more design enhancements like tension and compression footings were added to counter the force caused by undulated soil conditions.
“We developed special tower designs with longer spans for tower points across sensitive work zones such as deep valleys which reduced our scope of tower installations from 381 to 320. This in turn improved project scheduling and saved close to 17% of construction time.”
Shekar Sahu
Project Director, 275 kV Medamit-Lawas Transmission Line Project
For the team, working at the tower points was like operating on a wet wicket. “With this region receiving almost 7 to 9 months of rainfall, accessing work spots was always a challenge,” observes Shekar, to counter which, they meticulously studied weather patterns over a ten-year period to chalk out a secure work strategy. “To maximize execution during the normal three-month season, we deployed more gangs, preparing alternative approaches using drones to identify safe routes over critical sections, roping in forest workers and logging contractors to leverage the local advantage.”
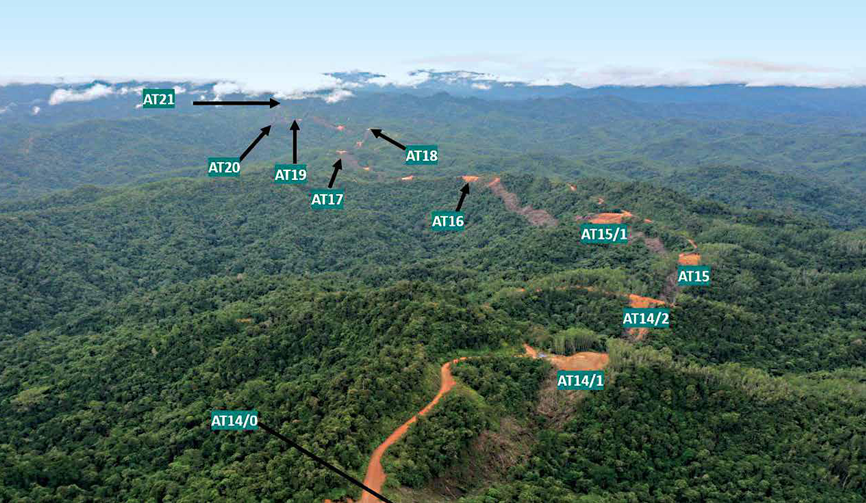
275 kV Medamit-Lawas transmission line project in Malaysia
Limited availability of skilled subcontractors was an issue for the project team, but Planning Manager, Nikhil Mundada, reassures, “We networked with the village heads who supported us with local manpower for the clearing easement works.” Similarly, the team used the services of logging companies that had the equipment infrastructure but lacked the skillset by orienting them with transmission line foundation work videos. Further, to facilitate and fast track tasks like shoring, formwork and prop set fabrication, a vendor was trained to deliver customizations that enabled the locals to do the final integration seamlessly.
Logistic management requires detailed planning and since accessing the line corridor by road was not feasible requiring VISA permits at the Brunei border and involving around 12 hours of travel, the team hit upon using the waterway to transport essential resource materials to Lawas and Sarawak. With meticulous planning, they successfully managed the major supplies comprising tower structures from India, conductors and hardware from Malaysia, disc insulators from Italy, OPGW and OFUC from China.
For Shekar and team, a lot yet needs to be done. “Commencing at a ground elevation of 8.74 m, the tower locations go up all the way up to a height of 1522.25 m with special towers standing between 25 m to 1500 m tall. Right now, we are focussing on creating safe access routes across tower points and with measures such as shoring and slope protection, we have completed 70 foundation works, established access ways across 139 locations with easement clearing and tower earthing tasks gaining momentum.”
Powering Mumbai Metro Line 7
The stakes are high for Project Manager, P L Jarotiya, at the Mumbai Metro Line 7 project to deliver a set of composite tasks comprising laying an EHV cable along the Western Express Highway between Borivali to Dahisar, constructing a 110/33-25 kV receiving substation, installing auxiliary substations across the 13 metro stations and laying 148 Km of external HT cable. While the city was locked down, the project team diligently made inroads with special permissions and closed in on some of the most challenging milestones such as laying the EHV cable. “We executed mostly during the restricted hours as it was a high-density traffic corridor with many existing underground utilities,” remarks P L Jarotiya. “Thanks to the support of the traffic police and the local authorities, we safely completed the entire trenching activity.”
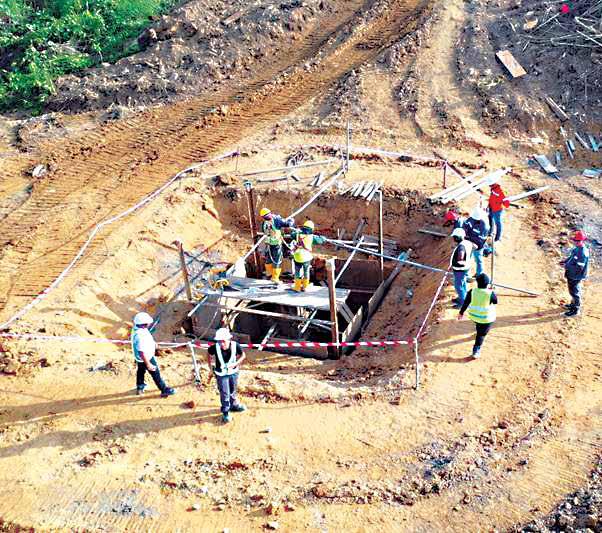
Tower foundation work
Constructing the receiving substation, a critical structure, over a 3600 sqm plot posed multiple challenges with an existing 6 m wide storm water drain running through it and a 14.5 m concrete bridge connecting the two sides of the land area. “We had to plan our execution keeping in mind safety and sustainability standards,” indicates Senior Construction Manager, G. Senthil Kumar, “as we were operating in a green zone with many trees around. We had to rework the foundation design to save the trees by increasing the depth of the foundation & size of the rafts and placing additional boulders for strengthening.”
Another consideration was to create space for mobility to mitigate the challenge of working over a running storm water drain. The project team came up with a temporary bridge and erected a 20 m high tower crane with a 35 m boom reach which enabled faster completion of works with lesser manpower, ensuring safety and quality. It is commendable that the project completed the main structural and finishing works within a 3-month period thus saving close to 2.5 months from the original schedule. The substation was charged on 24th May 2021 which facilitated the overhead electrification of the line and the trail run. “It is a special milestone for us as this is the first substation commissioned by L&T for the Mumbai Metro,” shares P L Jarotiya proudly.
“The substation was charged on 24th May 2021 which facilitated the overhead electrification of the line and the trail run. It is a special milestone for us as this is the first substation commissioned by L&T for the Mumbai Metro.”
P L Jarotiya
Project Manager, Mumbai Metro Line 7 Project
“To synchronize the auxiliary substations across the 13 metro stations, the onus was on the team to ensure that overlapping deliverables were precisely handed over to other civil and electrical agencies,” says Planning Engineer, Somen Debnath. “The client was keen to complete the testing of four stations on the priority section as soon as possible, which was achieved by handing over the completed sections of work fronts to the other stake holders for integration for testing and commissioning.” Going further, the project team has completed the installation and testing works including laying the HT cable at the 7 auxiliary substations.
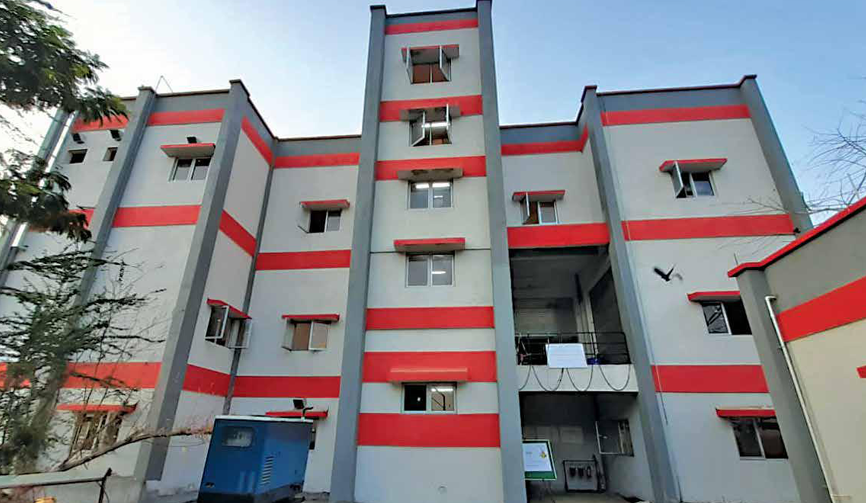
GIS Building at Mumbai Metro
P L Jarotiya attributes their success to some smart applications and proven strategies. “We installed optic view cameras at strategic locations across the GIS building, transformer yard, foundation work areas and main stores for 24/7 monitoring and real-time sharing of progress with the client.”
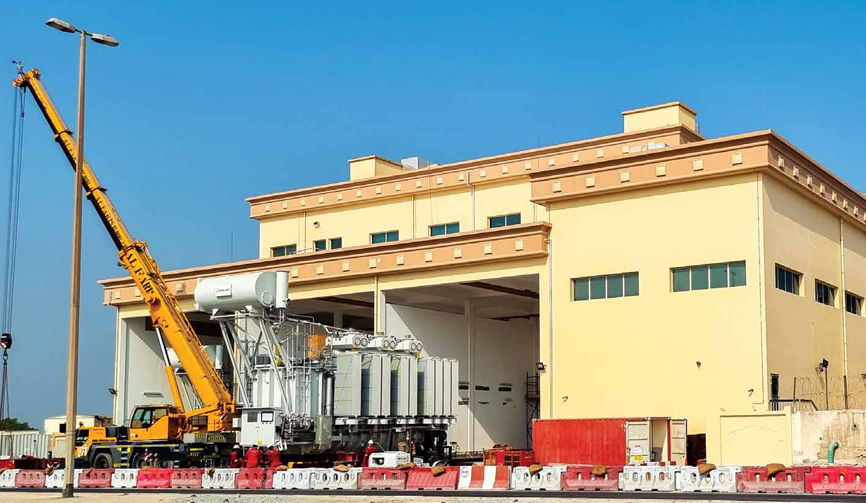
220/132 kV Layyah Substation
Building intricate power stations
With close to 96.61% of works completed at the 220/132 kV Layyah Substation in Sharjah, V. Oscar, Project Manager, has a lot to share on how the team went about achieving their milestones while overcoming the challenges of working in a brownfield project. “Our scope involved constructing a 220/132 kV substation, including 3 auto transformers to connect and regulate power from the new power plant as per the demand and transmit it to the network.”
One of the first challenges for the team was to work out a secure routing channel for the GIB connection with the new GIS building that was aligned through the existing 40-year-old power plant. “There was no detailed mapping of the existing utilities network,” mentions Planning Manager, Mohd Momin. “Finalizing the alignment was a composite task as it involved laying around 3900 m of GIB length, working out secure channels for the gas & road crossings and constructing a 12 m high & 330 MT supporting structure for the new GIB.
“To accommodate both the 132 kV and 220 kV substations in the same building, the priming of OEL was strategic. We therefore proposed suitable building expansion joints to seamlessly integrate the work fronts.”
V. Oscar
Project Manager, 220/132 kV Layyah Substation
For Oscar and his Planning Lead, the primary concern was to plug the gaps in the existing services before progressing. By coordinating closely with the plant authorities, they synchronized the tasks with the other activities undertaken by external contractors who were also working in the same area. The first milestone was to energize the 132 kV substation in 18 months, but they faced an immediate setback as the piling & pile cap works, which was under a local contractor, were not taken up. “Stepping in quickly, we suggested an alternative,” mentions, Mohd Momin. “We convinced the client to implement the common raft method by avoiding pile caps and increasing its thickness so that the drainage line embedment could be accommodated within the raft, and thus avoid the basement structural screed.” This was a significant value addition. The building base was raised up to 1 m level with the finished floor level at 2.5 m height to mitigate the risk of deep excavation considering that the site was close to the sea.
Despite the two lockdowns, the project team completed the first milestone before schedule largely due to design improvisations and some smart work. “To accommodate both the 132 kV and 220 kV substations in the same building, the priming of OEL was strategic. We therefore proposed suitable building expansion joints to seamlessly integrate the work fronts,” shares Oscar. Other initiatives like designing a single GIB structure to accommodate 2 Ckts of 132 kV GIB and 1 Ckt of 220 kV GIB helped them to achieve their milestones.
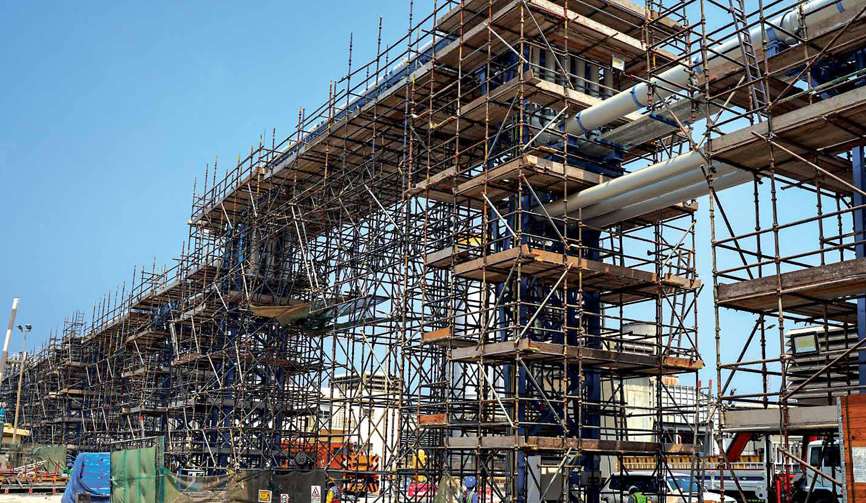
For Mohd Momin, shrinking timelines, wherever possible, was key to catch up with the deliverables. Considering the pandemic situation, the team put in place a supply chain tracker for long-lead items which included the GIS equipment from Germany, transformers from Netherlands and batteries from Italy. “We made good use of digital applications to secure engineering approvals from various stakeholders through virtual meetings, organized online FATs, obtained dispatch clearances so that when the restrictions were lifted, we could accelerate across work fronts.”
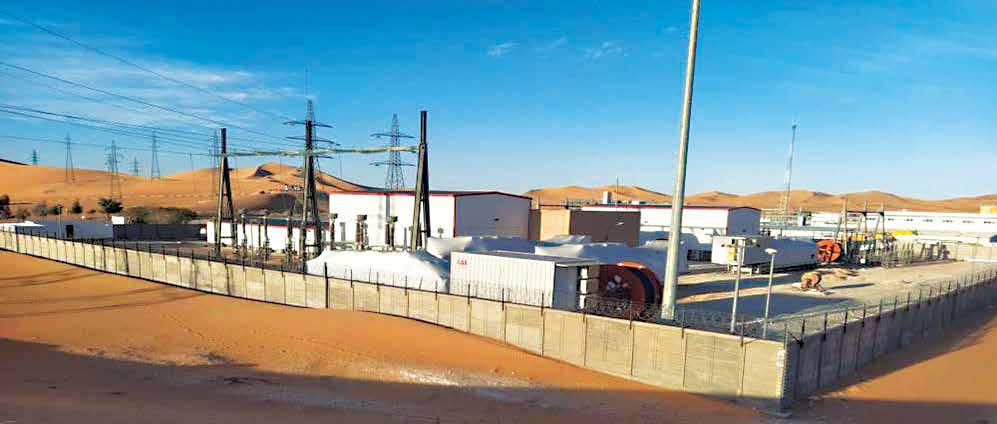
220/60 kV MLN Substation
Revamping a live network
The Rehabilitation and Upgradation of the Electricity Network of Hassi Berkine area in Algeria is a trailblazer project for PT&D where Project Director, Venkatesan Karuppaiah and team are on a mission to revamp the existing 220 kV power infrastructure in live conditions across 19 locations comprising 8 substations and 11 Central Processing Facilities.
Tracing the genesis of the project, Venkatesan recalls the considerable time spent at HQ Chennai to finalize the designs. “For over a year, the client was based at our Chennai Office working out the detailed design and execution plan before setting foot on this challenging terrain.” Several challenges awaited Project Control Manager, Shelbbyn Michael Raj at site. “Even getting to the work fronts was difficult as the alignment runs largely through the Sahara Desert with the nearest town located some 400 km from the site. From the beginning, we were escorted by an armed guard every morning to site that called for a great deal of planning to sequence the tasks.”
While the pandemic broke the workflow, digital applications enabled the team to complete 100% procurement through online/virtual FATs. “Majority of the materials were cleared from the port within the free storage period despite the stringent Algerian import regulations,” shares Venkatesan.
With the nature of this job very much like a hotline stringing, the onus was to ensure continuous power supply across three voltage levels – 220 kV, 60 kV & 30 kV that powered the oil and gas industries around this region. Sourcing the ‘as-built’ information from the two-decade old substations would have easily taken them around 4 months through conventional methods but by using 3D scanning and BIM, Venkatesan and team successfully firmed up the design deliverables in double quick time to fast track their works.
“At strategic junctions, we adapted the design to suit the infrastructure construction by proposing standalone buildings and in some cases even reducing the number of new structures.”
Venkatesan Karuppaiah
Project Director
Their strategy was more of stage wise rehabilitation which involved deploying one set of 220/30 kV and one set of 220/60 kV mobile substation units to do the critical revamp works for the first set of substations and, thereafter, shift to the second and third set of substations. “At strategic junctions, we adapted the design to suit the infrastructure construction by proposing standalone buildings and in some cases even reducing the number of new structures,” adds Venkatesan. Having completed the engineering phase within the stipulated time, they have gained the client’s trust and are now keen to press forward. “Most of the composite works like laying 81 Km of 30 kV UG cable inside a hydrocarbon process facility have been completed and we are now aiming to finish the core infrastructure works by early 2022.”
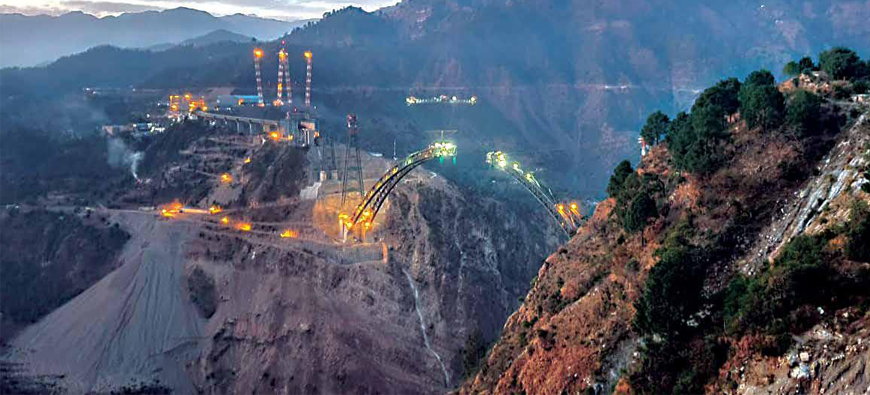
Cable laying across Chenab bridge, the world’s highest railway bridge
Scaling new heights
Another project that will soon be in PT&D’s list of tall achievements is the electrification of the T3 and T5 tunnels across the Udhampur-Srinagar-Baramulla Rail Link. Located at an altitude of over 980 m MSL, the project team has been entrusted the composite task of supply, erection, testing and commissioning of 33 kV and 11 kV HT power cable network, constructing four 33/11 kV gas insulated substations and six 11/0.430 kV substations with four of them inside the tunnel. Other major works involve cable laying inside the tunnel (HV, LV and OFC), ventilation system, lighting works, firefighting & PA systems, SCADA, and CCTV works. The scope also includes 33 kV HV cable laying over the Chenab bridge, the highest railway bridge in the world.
Delays in land finalization and nonavailability of skilled labour were Project Director, Nandalal Chandra’s initial headaches. “As further delays would have seriously impacted our deliverables, we took on the mantle of hill cutting and slope protection to develop the portal substations.”
Having set the base, the arduous task of laying the 33 kV cable weighing close to 20 Kg per meter at 6m height inside the tunnel and through the bridges is under progress. “It is a special project where the design parameters are very stringent calling for a high degree of precision as the fitting of the equipment inside the tunnel wall is being done considering the surface of dimension of the train. Added to this critical task, is the onus of ensuring safety during operations, shares, Planning Engineer, Tanmay Dwivedi.
Being a seismic zone under grade 5, it was vital to establish firm footings when executing the substation works. Since setting up a batching plant for concrete production was not feasible owing to the hilly terrain, the team networked with a local agency possessing the infrastructure and guided them to produce the approved concrete mix that not only hastened their construction of the portal works but achieved high quality standards.
“A customized movable scaffold was designed to do the cable works that was laid on box type trays with a height restriction of 6 m with precision fitting at a height of 13 to 14 m. For the record, we are installing more than 3 lakh anchor fasteners over the entire network.”
Nandalal Chandra
Project Director
Nandalal was faced with more challenges inside the tunnel “We are installing a secure ventilation system, designed to maintain the airflow and mitigate any unlikely rise in temperature in case of an incident with a capacity to release the air with speed of 3m/s. A customized movable scaffold was designed to do the cable works that was laid on box type trays with a height restriction of 6 m. For the record, we are installing more than 3 lakh anchor fasteners over the entire network,” he shares, with a wide smile.
Despite the pandemic restrictions and the challenges of the terrain, the team has completed several key deliverables “The raft of the GIS building is in place with other civil works under progress while the electrical works will be completed by October 2022 and the balance of works by December 2022,” assures Nandalal.
Fast tracking the sun beams
Tuticorin in Tamil Nadu has been a favourite ground for the Solar BU, having established a slew of track records by having executed some of the country’s largest solar generation plants there. This time around it is another mega 230 MW (AC)/345 MWp (DC) Solar PV Plant at Ettayapuram, that the BU is closing in with Project Director, Umapathy Mohanam at the helm of affairs.
“We have completed close to 90% of the engineering and plant design, lined up 75% of our procurement with key items like invertors, transformers, switch gears all based at our stores. Delivery of the balance modules along with transmission line materials are in progress and should be available by the time the groundwork is done.”
Umapathy Mohanam
Project Director, 230 MW (AC)/345 MWp (DC) Solar PV Plant
Apart from the engineering scope, Umapathy’s initial onus was to quickly acquire the 900 acres required for the project. “It was perhaps the most challenging part, having to continuously follow up with various stake holders for clearance titles, especially for non-agriculture certifications from the National and State Highway Departments. Presently, with close to 85% of the land acquired, construction works for micro-piling, cabling, module mounting structure erection and other core activities are underway.”
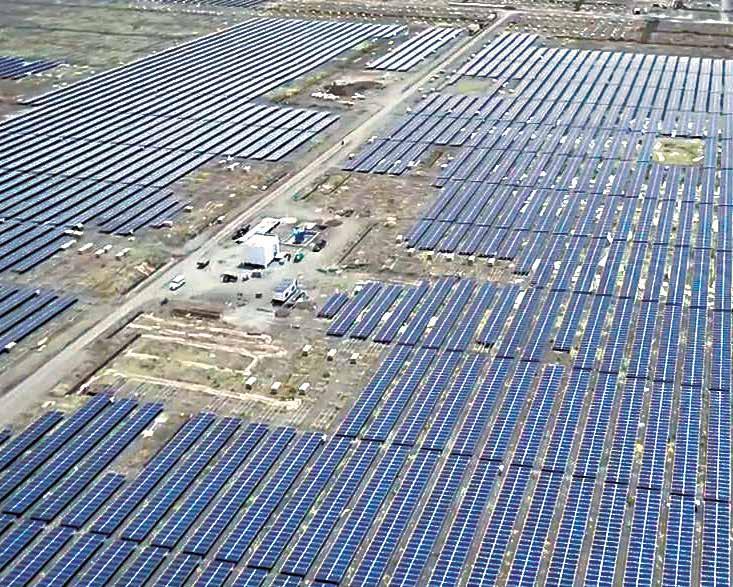
230 MW (AC)/345 MWp (DC) Solar PV Plant at Ettayapuram
While timelines are always stringent, it was more so for Umapathy‘s team as the project was bagged during the lockdown. “An extension of 5 months over the initial 18-month period has been the only saving grace though we have a range of works to cover and the only way forward is to bank on our EPC expertise and value engineering initiatives to bridge the gap.”
Several value engineering initiatives have fast tracked the project such as opting for pile foundation to do the invertor platform that has saved close to 70% of corresponding construction time, using structural steel for the superstructure that enabled them to complete the work 25 days ahead of schedule, optimizing the cable sizes through cyclic loading and thermal conductivity tests with simulation for enhanced conductivity and implementation of digital stores. “We have raised the solar operational effectiveness bar by type testing and getting the design clearance from NTPC for the country’s first 3150 A circuit breaker, sourced a suitable transmission line conductor to meet the current and voltage rating in line with technical recommendations and ensured the loading of the 33 kV HT cables aligning to the temperature and soil thermal resistivity.”
Today, the project is strategically placed with most of the prework done, thanks to some meticulous planning. “We have completed close to 90% of the engineering and plant design, lined up 75% of our procurement with key items like invertors, transformers, switch gears all based at our stores. Delivery of the balance modules along with transmission line materials are in progress and should be available by the time the groundwork is done.”