RAILWAYS SBG CONTINUES TO BUILD ON THE NEW BY LAYING TRACKS OF PROGRESS
Tucked away in the Indian Ocean, more than 2,000 km from the African mainland, the people of Mauritius would have hoped that the Coronavirus would give them a miss. Unfortunately, it did not. A 57-day ‘national confinement’ forced the team at the Mauritius Metro Express project under the leadership of Project Director,
G Vinod to quickly re-orient and re-align themselves to make up for lost ground. “Scenario Planning is one of our new initiatives during these COVID times,” explains Planning Manager, G P Sujith, “through which we looked at different permutations and combinations based on the possible outcomes to derive measures to achieve our target in all possible scenarios.”
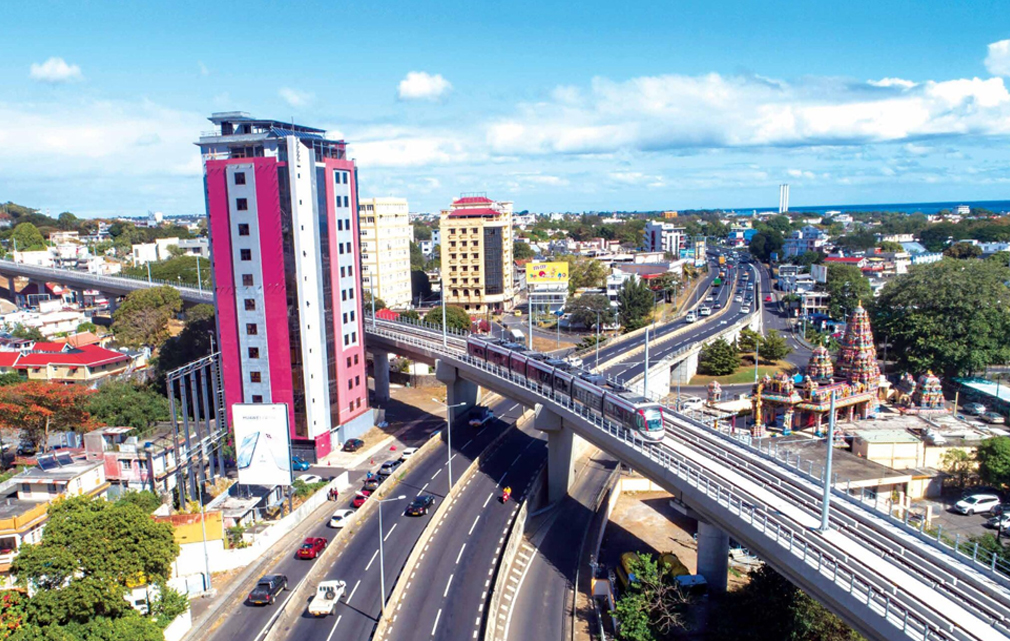
Preparing to get rolling
Even during the lockdown, the team reorganized themselves to keep the ball rolling and be prepared to hit the board running when things unlocked. A ‘Back to Work Procedures & Guidelines’ document was prepared and shared with all detailing the measures to be strictly adhered to by employees, workmen, subcontractors and other external stakeholders. Managing workmen psyche was high on Vinod’s priority list. “They were agitated with several of them wanting to return to their families in India,” shares Vinod, with a deceptively calm demeanour. “Since the borders were closed, they could not leave but we reached out to morally support them and, convinced them to focus on work since we had a lot of ground to cover. It was a delicate situation, but we handled it well and the positive fallout was a sense of solidarity and belonging that has bound the entire team.”
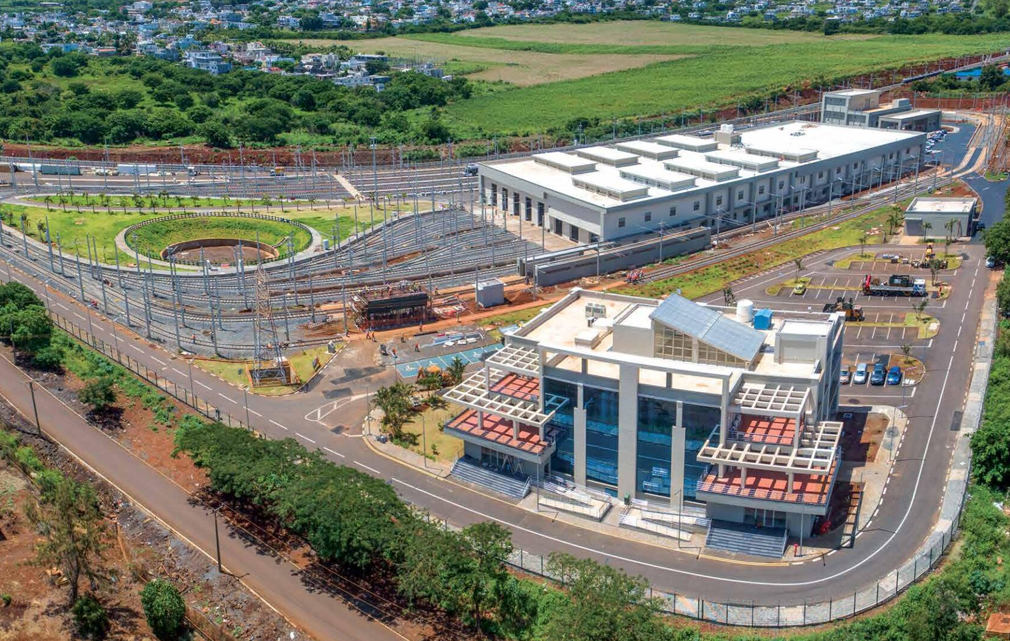
Aerial view of Mauritius Metro Depot
“Our progress has been commendable. The authorities have supported us by facilitating situations regarding health, staff and workmen who feel safe and free to work which is why we have completed 70% of execution and are effectively managing
our deadlines.”
G Vinod
Project Director, Mauritius Metro
All Work Access Permits in Mauritius for the resumption of business operations, involving major site activities, including Mauritius Metro project, were stopped since mid-March. However, thanks to the excellent stakeholder relationships and collaboration with the local authorities including the Ministry of Health, Police and the PM’s office, progressive permits for 100% of the workforce were quickly and smoothly obtained therefore when the lockdown was lifted on 21st May, the project office and site were immediately up and running.
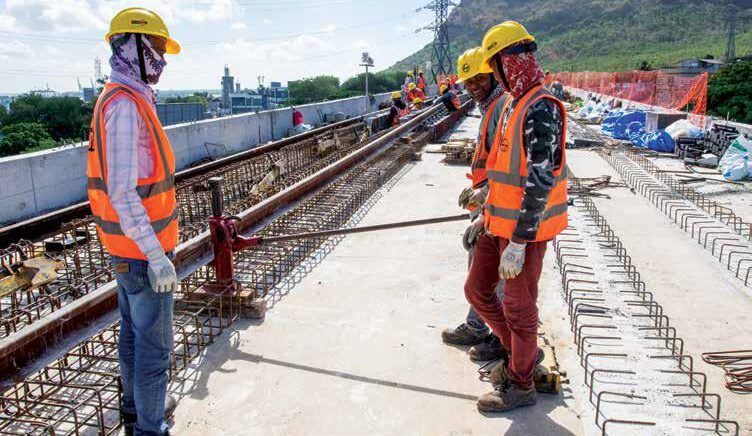
Plinth trackworks at Mauritius LRT
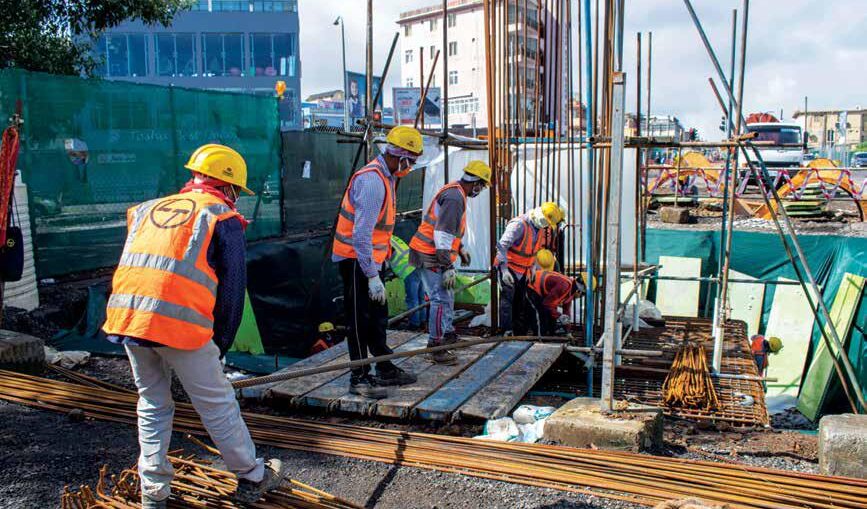
Fore planning is being forearmed
With labour under control, the disruption of supply chains could have been a huge deterrent. “Luckily, our pre-planning was spot on and we had sufficient stock of major materials and tools,” smiles Sujith, for whom this is a feather in his cap. “Since our Phase 2 was in full swing, we had advance planned our materials requirement and importation. Shipping time for new orders could be anywhere from 30 to 60 days but we are fine.”
“Scenario Planning is one of our new initiatives during these COVID times, through which we looked at different permutations and combinations based on the possible outcomes to derive measures to achieve our target in all possible scenarios.”
G P Sujith
Planning Manager, Mauritius Metro
“Our progress has been commendable,” remarks Vinod. “The authorities have supported us by facilitating situations regarding health, staff and workmen who feel safe and free to work which is why we have completed 70% of execution and are effectively managing our deadlines.” Vinod’s positivity is certainly holding the project in good stead.
“We successfully resumed work in 100 days. The Engineer supported us to reimburse our claims for the COVID PCR Tests conducted and construct additional labour colonies to maintain social distancing. We received an Extension of Time for 66 days for the delay incurred due to COVID-19 under
the Contract.”
Sunil Khattar’s
Project Director, Dhaka Metro
Addressing issues in Dhaka
Warning bells for Project Director, Sunil Khattar’s at the Dhaka Metro Rail project rang as early as on 15th March, when he received the first notifications about delay in deliveries from global vendors. Soon thereafter, his local workmen deserted the site shrinking his workforce from 158 to just 7 in the space of 3 days. “There were travel restrictions between India and Bangladesh, the border between the two countries at Benapole was closed stopping all land deliveries and clearances at the Chittagong seaport was getting inordinately delayed.” Sunil’s expression is of a person for whom nothing more could go wrong. “We addressed these issue by issue and soon we were on firmer ground,” he says, with a brighter look.
By maintaining close contact with European manufacturers, the team ensured supply of critical project material from them. To expedite matters, Factory Acceptance Tests were conducted virtually for various Signalling items, Automatic Fare Collection Systems, Equipment and Platform Screen Doors while import e-permits and digital clearances by the Bangladeshi government helped enormously. “The material successfully arrived at our stores and was secured properly,” Planning Manager Debakash Banerjee’s relief is obvious. Some of the major materials that arrived at site during the months of April, May, June, and July included a Rectifier Transformer from Italy, Copper Conductors from Belgium, Escalators from China, Master Clock Systems from Switzerland and a host of material from India like Circular Masts, 132 kV Cables, 33 kV Switchgear, SCADA systems and
telephone systems.
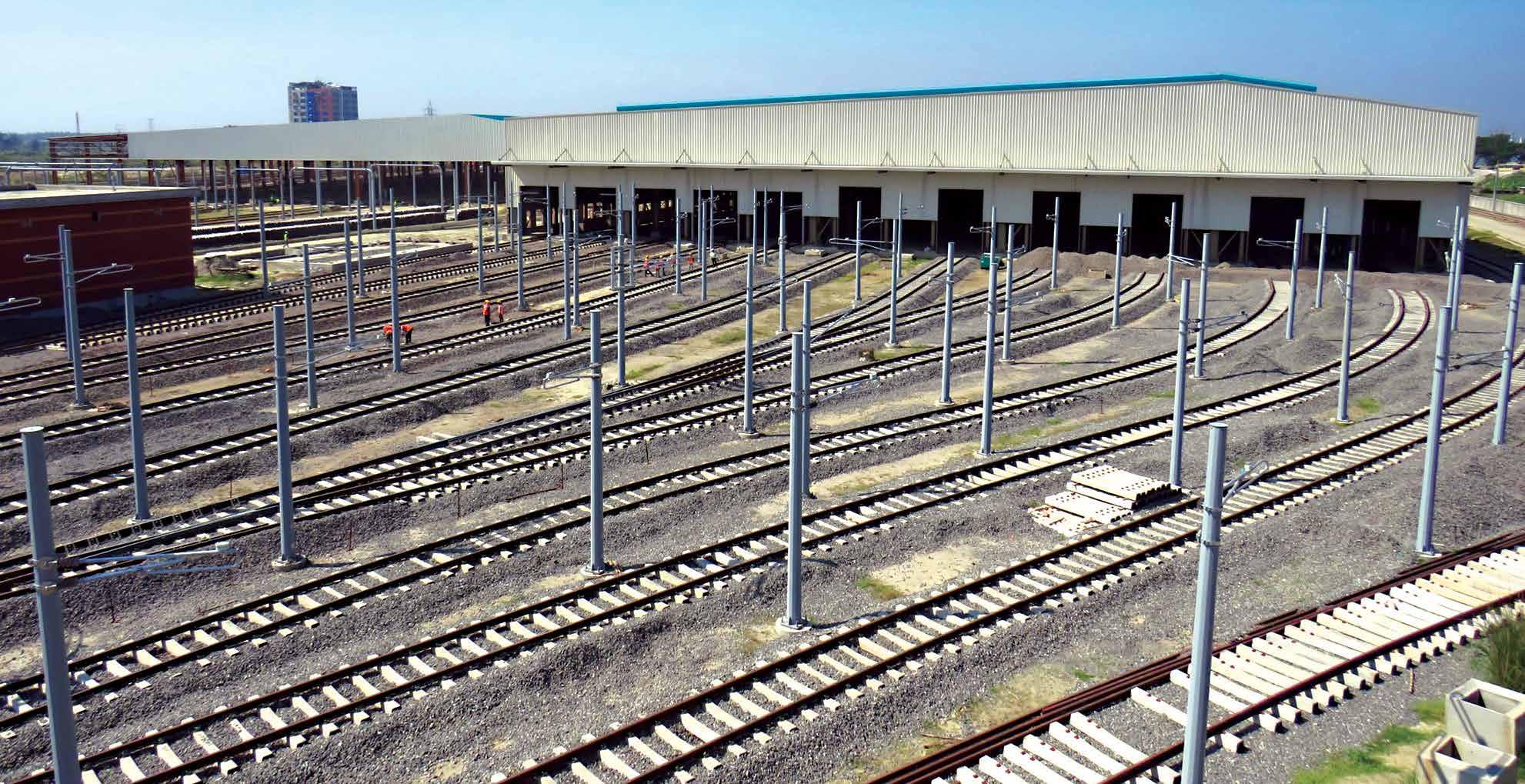
Completed section of trackworks at Dhaka Metro Depot
At the same time, the team constantly updated the Engineer about delays in manufacturing, shipments, and port clearances, listing out the material required under each sub-system, evolving strategies, and adopting measures to mitigate delays.
“We successfully resumed work in 100 days,” shares Sunil. “The Engineer supported us to reimburse our claims for the COVID PCR Tests conducted and construct additional labour colonies to maintain social distancing. We received an Extension of Time for 66 days for the delay incurred due to COVID-19 under the Contract.” What should please Sunil and his team more is that the Engineer is appreciative of their progress of completing major physical works for Trackworks (Plinth Construction for Ballastless Trackwork and Track Linking), Overhead Catenary System (OCS) Works, Receiving Sub-Station Works and Traction
Sub-station Works.
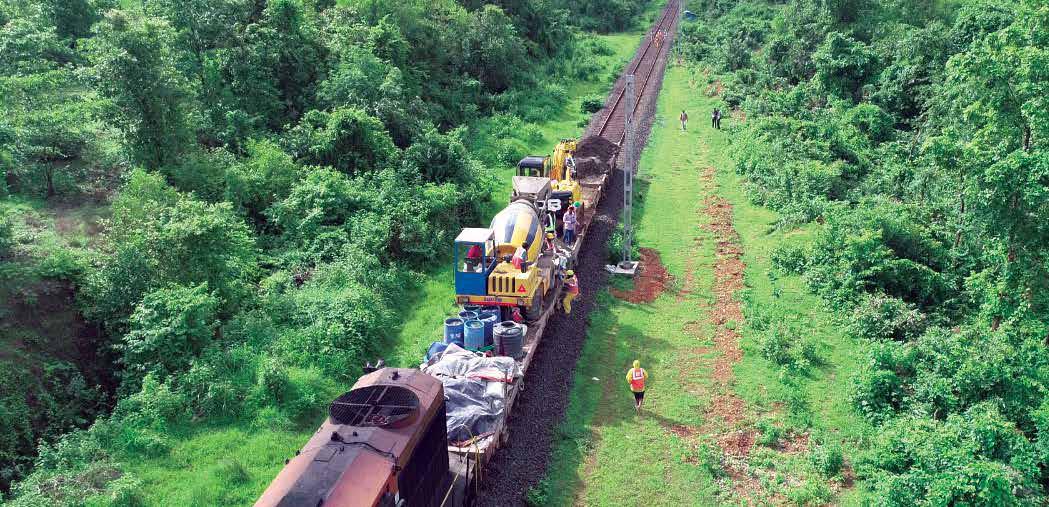
OHE foundation and mast erection at the Roha – Verna section
Concentrating on building on the new at the Roha-Verna Project
The secret of change is to focus all your energy not on fighting the old but building on the new. Taking cue from Aristotle to whom this quote is attributed, Project Manager, Prashant Soni at the Roha-Verna Project that is part of the mega Konkan Railway Electrification Project delves on the positives. “Yes, our workforce slipped from 1,000 to 300 just when we were ready to resume critical operations, but the lack of manpower forced us to use more mechanization and digitalization and those have been real game-changers,” he says with gusto. “We successfully introduced several technological innovations like OHE stringing through automatic wiring train, installing spring type automatic tensioning devices.” Construction Manager, Prashant Andhare adds, “We are using an excavator with breaker and a self-loading mixer machine on rail BFR along with our UTV that has hugely improved our productivity and tower wagons, integrated OHE wiring, impact wrenches, and more.”
“The commissioning of our priority Roha – Ratnagiri section has been planned for December 2020 and with our current resources and planning, we are sure to achieve our target with flying colours.”
Prashant Soni
Project Manager, Roha – Verna Project
Obviously one with a philosophical bent, Prashant adds, “COVID-19 has introduced us to new challenges, new perceptions and new methods.” They soon found opportunity in crisis. “Progress at a railway electrification project, depends on traffic blocks and with train traffic at a standstill during the lockdown, we used the blocks to the fullest extent possible to push forward with our construction,” shares an excited Construction Manager,
S Praveen’s, “working both day and night shifts to achieve a milestone of erecting 1,401 masts in just 20 days managing to invoice to the tune of INR 5.3 Crores!”
“Progress at a railway electrification project, depends on traffic blocks and with train traffic at a standstill during the lockdown, we used the blocks to the fullest extent possible to push forward with our construction, working both day and night shifts to achieve a milestone of erecting 1,401 masts in just 20 days managing to invoice to the tune of
INR 5.3 Crores! ”
S Praveen’s
Construction Manager,
Roha – Verna Project
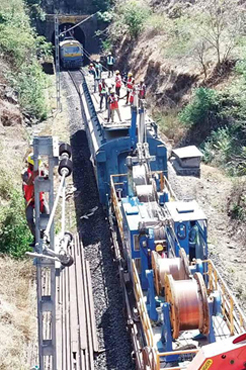
OHE stringing through automatic wiring train
The team visited villages in the vicinity, contacted the Sarpanches to identify workmen and 200+ were convinced to come to work after which they were properly inducted with technical and safety training. The team’s long association with the workmen came in handy as they were gradually able to wean them back to site. By end September, 1,000 workmen were at site with work proceeding at full steam. Prashant eagerly shares a series of achievements. “We erected about 1500 MT of steel structure in 5 months that is approximately 40% of the total steel structures erected till date since September 2018. We have erected 234 steel structures (120 MT) in a day, erected 22 Booms (21 MT) in a day and checked 108 OHE Cantilever joints again in a day.” He takes a deep breathe. “The commissioning of our priority Roha – Ratnagiri section has been planned for December 2020 and with our current resources and planning, we are sure to achieve our target with flying colours,” he declares confidently.
Meeting problems head on
At CTP-14, Project Director Shashank Pachade’s is overjoyed that his team has over-remobilized labour. “We were at 1,600 levels pre-COVID but presently have 2,600+ workmen at site, 150% more deployment!” Things looked bleak for him during the lockdown as apart from a deserting workforce, he was facing several other issues: lack of progress, disruption in design approvals, no physical followups, negative cash flows, slipping deadlines and “our invoicing was reduced by 80% compared to preCOVID days,” he laments. “Obviously, there was huge pressure from the management to resume work at the earliest to meet our expected budgeted target. Our client (DFCCIL) was also worried about delays in completion.”
When work resumed, labour and material supply were causes for concern. Soon, the project ran out of cement and steel, the supply of elastomeric bearings was delayed as the raw material had to be imported from Japan; the box girder erection launching gantry had been procured earlier from HLCM, China. “We contacted local authorities for the spare parts and significantly saved on cost and time,” says Shashank. “In the meantime, we procured full-span shuttering to complete the retaining wall of up to 6 m that required less manpower and time but was better in terms of quality and costs.”
The team approached the client for funds to remobilize labour and received a one-time payment of INR 80 Crores to get things moving. With the client keen to release funds against progress at site too, Shashank’s immediate issues have been addressed including releasing payment to 900 workmen and he is even talking to DFC for arranging special trains for labour re-mobilization.
“Before resumption, we concentrated on a few critical aspects. We ensured that our P&M was well maintained, planned to commence works based on the availability of work fronts, material and
necessary permissions.”
Anud Koul
Project Director, CP-204
Having successfully addressing their issues head-on, Shashank and team have several triumphs to share. “We achieved a 1 km tunnel breakthrough on 24th July in the presence of the Managing Director of DFCCIL,
Mr. Anurag Sachan,” shares Shashank. “The Sleeper Plant was set up in a record time of 6 months, all electrical utilities infringing the construction of bridge piles at BR 191H were cleared within 20 days and,” he adds with emphasis, “we have been progressively improving our invoicing that has touched 70%+ by September.”
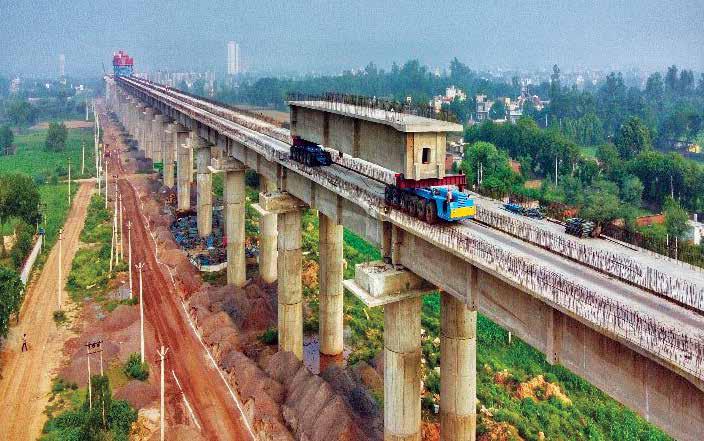
3.3 km viaduct through full span box girders of 32m spans each weighing 338t
The inspection agency Bureau Veritas India had to conduct a third-party inspection of the Auto and Scott Transformer in Japan. With intercountry travel suspended, the team co-ordinated with the agency to arrange for a local inspector in Japan. Bureau Veritas India co-ordinated with their counterparts in Singapore and arranged for a local inspector in Japan. The inspection was carried out as per schedule, with video conference inspections carried out for multiple products overseas.
Shashank also has his client’s glowing letter of appreciation to show for his ongoing efforts.
CP 204 gets back on rail
Project Director, Anud Koul had his hands full as his project readied to resume operations. Having to implement SOPs to the manpower at a project that stretched 420 km, managing a panicked client and PMC, having to make do with restricted transportation that hampered movement of material and essential services, lack of COVID-19 PPE, security of material and maintaining P&M. Fortunately, the lockdown gave Anud and his team time to think and plan their actions that were based on a Work Resumption Plan, a Business Continuity Plan, SOPs to combat COVID-19 and a Work Methods based SOP for site.
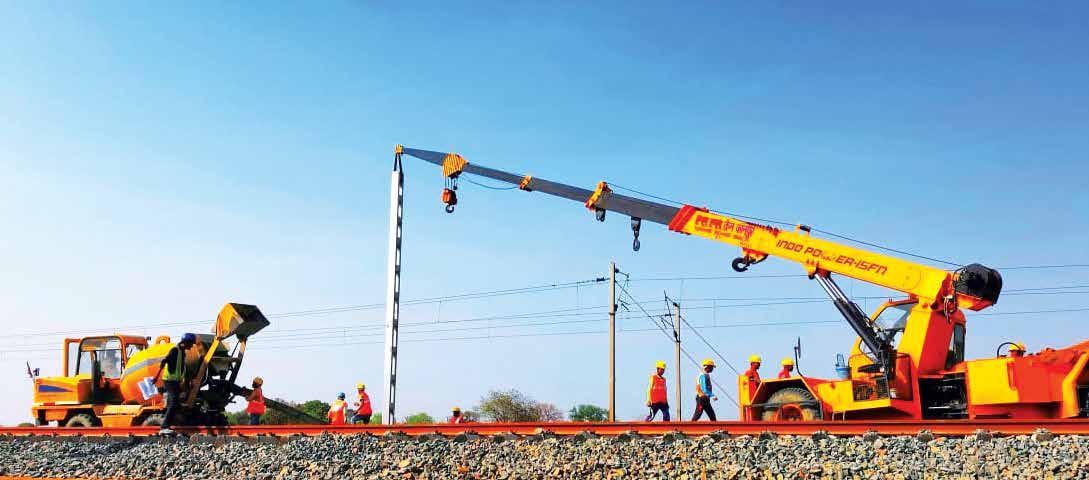
Erection of mast at CP 204
“Before resumption, we concentrated on a few critical aspects,” points out Anud. “We ensured that our P&M was well maintained, planned to commence works based on the availability of work fronts & material and necessary permissions.” We also ensured that our employees, workmen and subcontractors were trained about the new procedures and were in constant touch with our subcontractors to understand their concerns.
The planning has helped for by October, productivity and site execution have exceeded February 2020 levels, with zero COVID positive cases, no theft or damage to P&M and more than 1,000 hours clocked for training staff and workmen. To expedite supply chain issues, third party inspections were organized and Anud says, “various materials worth INR 38 Crores were delivered such as Mast Portal, SPI Steel, Copper, UPS, Cantilever Fittings, Tube etc. We ensured that our Dispute Adjudication Board (DAB) proceedings were not hampered, pursuing the Client and DAB members to conduct proceedings through MS Teams to save cost and time. DAB for a major EOT claim is currently under progress.”
“We achieved a 1 km tunnel breakthrough on 24th July in the presence of the Managing Director of DFCCIL, Mr. Anurag Sachan. The Sleeper Plant was set up in a record time of 6 months, all electrical utilities infringing the construction of bridge piles at BR 191H were cleared within 20 days and we have been progressively improving our invoicing that has touched 70%+ by September.”
Shashank Pachade’s
Project Director, CTP-14
The numbers are showing as the project has achieved INR 40 Crores of invoicing and INR 100 Crores of
collection in H1.
As a matter of fact, the results were as per expectations and Anud attributes the success to team bonding, planning and passion of the employees to drive through these tough times.
The same certainly applies to all the projects of the Railways SBG!