RAILWAYS SBG PROJECTS ACHIEVE MILESTONES TO MEET CLIENT DEMANDS
Kanpur is one of India’s most populous cities, the largest in the state of Uttar Pradesh and one of the oldest industrial townships in North India. Agra, on the other hand, is synonymous with the Taj Mahal, UP’s 3rd most populous city, the administrative headquarters of the Agra district and a major tourist hub. To take commute in these two cities to a new level, the Uttar Pradesh Metro Rail Corporation Ltd. (UPMRCL) awarded the Kanpur & Agra Metro track work project to the Railways SBG on February 2nd, 2021. Being the first such project for both cities, the client had a strict deadline for the Kanpur Metro priority section of 18.892 T-km to be completed by December 2021. Despite several challenges, the team led by Project Manager, Venigalla Venkata Ramana successfully met the client’s milestone on December 28th and the client is doubly happy because the inaugurated section has already started to generate revenue.
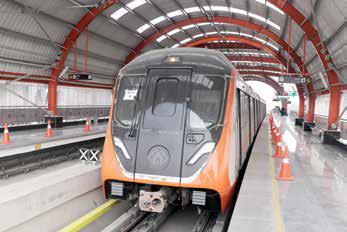
The Kanpur Agra MRTS project contours
The project involves the construction of a ballast-less track for a length of approximately 29.4 Rkms in Agra and
32 Rkms in Kanpur with a third rail DC traction on elevated and underground structures. L&T’s scope involves design, supply, installation, testing and commissioning of the ballast-less track of standard gauge in 4 elevated corridors & underground sections in Kanpur & Agra along with supply of fastening and associated ballasted/ballast-less track in four depots to be completed in 48 months with a target delivery date of January 31st, 2025.
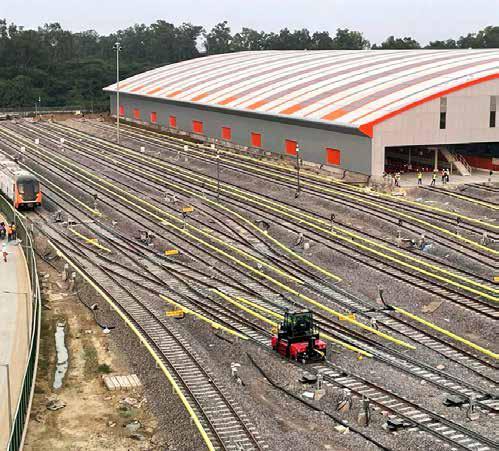
Small beginnings
“We started small,” smiles Venigalla, “for when the project began in February 2021, we had just three employees: a Project Manager, a Planning Manager, and one FLS and a team from another project was requested to commence the survey work. Things have improved since and with resources gradually increasing, we now have 24 L&T employees and their families in Kanpur and Agra.” The initial stage of mobilisation involved preparation and contractual submittals to Client, online discussions with the HQ team and vendors for finalisation and mobilisation of equipment, ballast-less fastening, identifying & finalising staff deployment, project scheduling and planning an effective work execution strategy.
Kanpur Metro
a. Corridor 1 – IIT Kalyanpur to Naubasta (23.5 RKM)
b. Corridor 2 – Agriculture University to Barra (8.9 RKM)
c. Depots – (i) Polytechnic Depot and
(ii) Agriculture University
Agra Metro
d. Corridor 1 – Sikandara to Taj East Gate (13.9 RKM)
e. Corridor 2 – Agra Cantt to Kalinda Vihar (15.4 RKM)
f. Depots – (i) Fatehabad Depot and (ii) Kalindi Vihar
COVID strikes
The pandemic waves and the subsequent lockdowns hit when the project was well on track. “Due to the state-imposed lockdown, 70% of trackwork workers from West Bengal, Jharkhand, and Madhya Pradesh left the sites and returned home,” laments Planning Manager, Emamul Pavel, “and with no local resources from Kanpur or the surrounding area available for the specialised track work, progress at the Polytechnic Depot slowed substantially.” If the first wave depleted the labour force, the second completely disrupted the supply chain cycle from May 2021 to September 2021. While the lack of oxygen brought operations to a halt, the strict lockdown meant that all the vendors experienced delays in material production and delivery timelines.
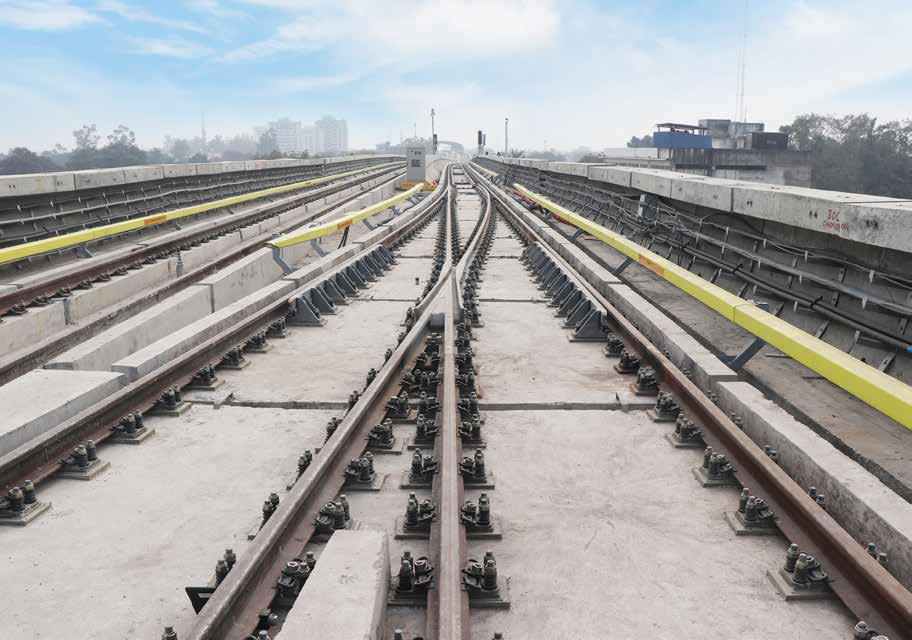
Kanpur – Agra depot entry line
Desperate situations require desperate solutions, and to make up for lost time, the team took transport material on loan from Kochi Metro and UPMRCL, Lucknow, to meet the desired per day casting target.
Emamul explains a case in point. “With the closure of the sleeper plant in Haryana, our delivery of tension clamps from China was pushed back from July to August, severely affecting our execution target. The lack of required tension clamps from Vossloh, Germany & China-PR, and base plates from Nellore, among other things, had a further negative impact on our track plinth casting.”
The order for Ballast-less Fastening was placed with Vossloh as soon as the order was approved in May 2021. “The Kanpur Metro project’s first priority section included imports from Germany and China-PR and despite the effects of the second pandemic wave and a typhoon, our logistic experts did an excellent job in obtaining clearances from the customs department for our products,” praises Venigalla. The arrival of the tension clamp and elastic pad was delayed too, forcing the the team to airlift the first lot of 21,600 numbers.
Desperate situations require desperate solutions, and to make up for lost time, the team took transport material on loan from Kochi Metro and UPMRCL, Lucknow, to meet the desired per day casting target. From June 21 to October 21, activities were planned and carried out round the clock to meet their initial deadline of commissioning the 18.892 TKM section, emphasizing on completing activities such as Flash Butt Welding, AT Welding, Plinth Casting, and Rear Works.
“At the same time, we had continuous discussions with the client (GC & UPMRCL) to agree on the list of designs & drawings, and closely coordinated with all the relevant stakeholders – EDRC, BU, SBG – to push progress,” comments Venigalla.
Work with other contractors on civil packages and rolling stock was, however, difficult as none of the equipment manufacturers agreed to participate at such an early stage. Further, the civil, rolling stock, and electrical contracts were awarded by contractors much earlier and their projects were well underway. “The interfacing contractors expected us to provide immediate solutions and our technical experts, with their inherent knowledge of the subsystems, did a good job of providing information on time, and the Employer was pleased too with the project’s rapid pace of involvement,” points out Emamul.
“The interfacing contractors expected us to provide immediate solutions and our technical experts, with their inherent knowledge of the subsystems, did a good job of providing information on time, and the Employer was pleased too with the project’s rapid pace of involvement.”
Emamul Pavel
Planning Manager
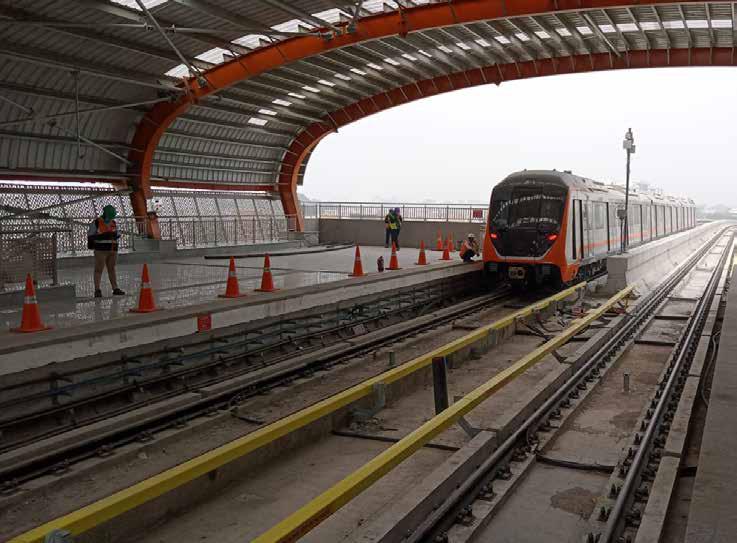
Project planning and scheduling were comprehensive, and although access was phased, the access to the viaduct, stations, and depot is updated in real time in the project schedule and translated into a prominent lookahead plan that keeps the team on track for resource and manpower engagement. “As a result, our organisation is lean and project management is asset-light,” points out Venigalla. Furthermore, the real-time schedule serves as a good trigger for material requirements and since most of the materials are from India, this early indication has proven useful to maximize project progress.
“The design and installation of the plinth ballast-less tracks have been in practice for over two decades and now extremely commoditized with strong competition from unequal players,” grimaces Venigalla; however, he brightens up about the state of his project: “Despite having a skeleton project team during the initial period, we have successfully achieved all the key dates and have been receiving continuous appreciation from the Employer and Engineer,” he sums up with a winning smile.
“Despite having a skeleton project team during the initial period, we have successfully achieved all the key dates and have been receiving continuous appreciation from the Employer and Engineer.”
Venigalla Venkata Ramana
Project Manager
SET TO CHANGE HOW THE CITY OF AHMEDABAD COMMUTES
Although the LOA was issued for the Ahmedabad Metro Phase 1 project on June 28th, 2017, the project team gained access to site only in February 2018, the actual physical installation of track work began on March 1st, 2018, with rail lifting and flash butt welding activities and the first concrete pour for track plinth was on June 13th. The criticality of the project is reflected in two PMO directives, the first in August 2018 to the Employer, Gujarat Metro Rail Corporation (GMRC), to commission the 12.9 TKM stretch from Apparel Park to Vastral Gam including Apparel Park Depot and make ready for the people of Ahmedabad by March 2019. The second directive was to complete the entire 40 TKM length of the project within a limited time frame by August 2022.
The team under Project Manager Venigalla Venkata Ramana’s leadership took the challenge to successfully complete the installation of the track, the highlight being to achieve track plinth casting of 5.6 TKM by December 2018, the highest in metro projects in India at that point of time. The section was inaugurated by the Hon’ble Prime Minister of India, commissioned on March 3rd, 2019, and revenue operations started from March 6th, 2019, much to the client’s delight. Even with several hindrances, the team surpassed their earlier benchmark to cast 28 TKM in a record
4 months, which is approximately 40% of total scope of work, with a highest track plinth/slab casting of 8.263 TKM and 8 Turnouts (all over India) in February 2022. The necessary casting activities were completed in April 2022, and all works have been handed over to the other system contractors, meeting the expectations of the Customer and still retaining the project’s profitability.
“The 3rd Rail template fixture adaptation was a key initiative for our success which increased the progress with quality and precision as well as proved cost efficient to the project.”
Venigalla Venkata Ramana
Project Manager
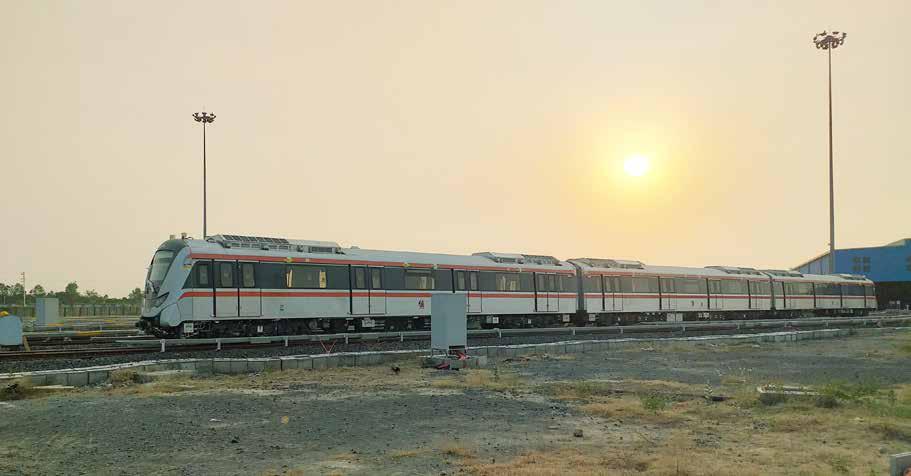
The scope, early days & challenges
The project will connect the four corners of Ahmedabad city with two corridors and 32 stations and involves design, supply, installation, testing and commissioning of ballast-less track of standard gauge: the North–South elevated corridor from APMC to Motera Stadium, the East–West corridor from Thaltej Gam to Vastral Gam in elevated and underground sections, along with ballasted/ballast-less tracks in depots at Gyaspur and Apparel Park. The total length of the Ahmedabad Metro Rail Project Phase-I is about 40.03 km, out of which approximately 6.5 km is underground and the rest elevated, and is expected to be completed in 156 weeks from LOA, tentatively April 2023.
After the initial kick-off on August 10th, 2017, a team of 4 including the Project Manager landed in Ahmedabad and initially tied up with the regional office for basic support with the focus on contractual deliverables like submission of plans, project scheduling, spotting best fit personnel for the job & resource availability in existing / closing jobs, discussions with HO team and vendors to finalize project deliverables. Subsequently, the focus shifted to other key areas like design, interface, procurement, & construction.
One huge challenge was the complexity of doing business with multiple stakeholders as L&T was the solitary contractor for the complete track construction, having to interface simultaneously for Civil & Systems works. Venigalla is all praise for the design coordinator, Ramakrishna, who managed all the interface requirements accurately and timely with multiple contractors. “The Employer was satisfied with our rapid pace too,” smiles Venigalla.
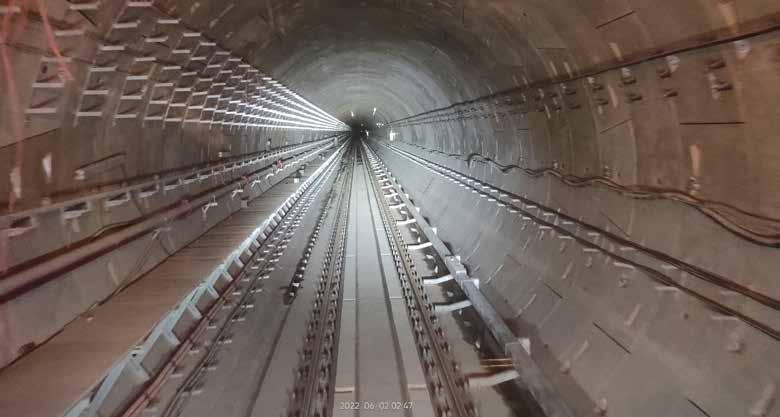
The team even surpassed their earlier benchmark to cast 28 TKM in a record 4 months, which is approximately 40% of total scope of work, with a highest track plinth/slab casting of 8.263 TKM and 8 Turnouts (all over India) in February 2022.
Procurement is key for 40% of project value is for the supply of both indigenous and imported components, including from Germany, Austria, UK, China, and Poland. “We received all the necessary technical approvals from the customer well in advance and the delivery requirements were clearly communicated and coordinated with the concerned SCM/ HO team by the Project Planning Team, led by me, supported by Manikandan,” flags off Planning Manager
H R Shashitheja “Despite the pandemic, the logistics teams did an appreciable job to timely procure the materials for execution.” As a backup, the team developed local vendors & sub-contractors to reduce delays.
The pandemic took its toll too, causing a labour exodus, throwing the supply chain into disarray, and infecting several personnel at site.
“The Employer believed in our capabilities, and we accomplished this job of installing a Mass Spring System in the underground section brilliantly within the stipulated time through meticulous planning and optimizing the required resources.”
H R Shashitheja
Planning Manager
Innovations to drive efficiencies
- 3rd Rail Template Fixture Adaptation: To start with, the Client insisted on the high-precision vertical fixing. We initially followed the concreting with a two-pour system as implemented in Kochi Metro by leaving a cavity in track plinths from the top of the derailment guard to the bottom of the plinth at the location specified by Traction, which was a tedious job to maintain quality, progress and schedules. With one of Venigalla’s innovative ideas, the project team implemented distinct prefabricated third rail dowel holding Template, which is precise, labor friendly, easy, and factory-made along with modifying the Steel Shuttering plates to Ply shutters. “This was a key initiative for our success which increased the progress with quality and precision as well as proved cost efficient to the project,” Venigalla proudly explains.
- Installing a Mass Spring System: The team was awarded a variation order to supply and install a Mass Spring System (MSS) in the underground section, being implemented for the first time in GMRC as well as for L&T. Steel Spring MSS is a specialized system for vibration attenuation technique which is precision work and requires lots of time and resources. “The Employer believed in our capabilities, and we accomplished this job of installing a Mass Spring System in the underground section brilliantly within the stipulated time through meticulous planning and optimizing the required resources,” says Shashitheja jubilantly.
Yet another deadline to meet
The Employer fixed an objective with the PMO to complete the remaining section of Phase I by August 2022 to coincide with the country’s 75th Independence Day. However, due to the pandemic, access was delayed from Civil and only 26% of total access was provided till the completion of the contractual period.
The team still took up the challenge, guided by HO, and a central team comprising Venigalla, Shashitheja, Stalin Ramar (DPM), and Ramakrishna was set up to coordinate with the Customer as well as the HO and vendors for early decisions and speedy implementation. Cluster Head Brij Mohan Sharma and BU Head Sunil Khattar effectively supported in strategizing execution to achieve benchmarking progress by assisting to arrange the necessary supervisory staff and resources. “We had initially forecasted the requirements for man, material and P&M wherein We had initially forecast the requirements for man, material, and P&M wherein we had deployed and managed 3 Flash Butt Welding Machines and 10 Track Linking teams, compared to 2–3 teams normally and 37 equipment at one point of time and other necessary tools,” adds Venigalla, who is all praise for the DPM, Stalin, for managing all the resources accurately and timely in achieving the desired task.
Further trail runs are underway in both the corridors, and the Customer is planning to commission the whole of the Ahmedabad Phase I in August 2022 and commence revenue operations by September 2022.