RREC PROJECTS MAINTAIN BUSINESS CONTINUITY DESPITE DISRUPTIONS
Even as the country awaits the arrival of India’s first Bullet Train, several L&T teams are striving muscle and sinew, night and day, to build this extremely difficult infrastructure in challenging conditions and terrains at a speed unheard of in the Indian construction industry. At the MAHSR Package C-6, Task Force Leader, Mohan Ramesh, and team faces the challenge of working on the River Mahi to sink twelve wells and build the first of its kind large dia Shinso Pile of
7.2 m diameter on a National Highway. “We have to liaise with over 30 government authorities to construct the
viaduct and bridges so that the services, roads, pipelines and telecommunication networks of these utility agencies remain uninterrupted,” he shares the enormity of their mandate. “We also have to work closely with State and Central government authorities for the permissions for the crossings and the availability of work fronts.”
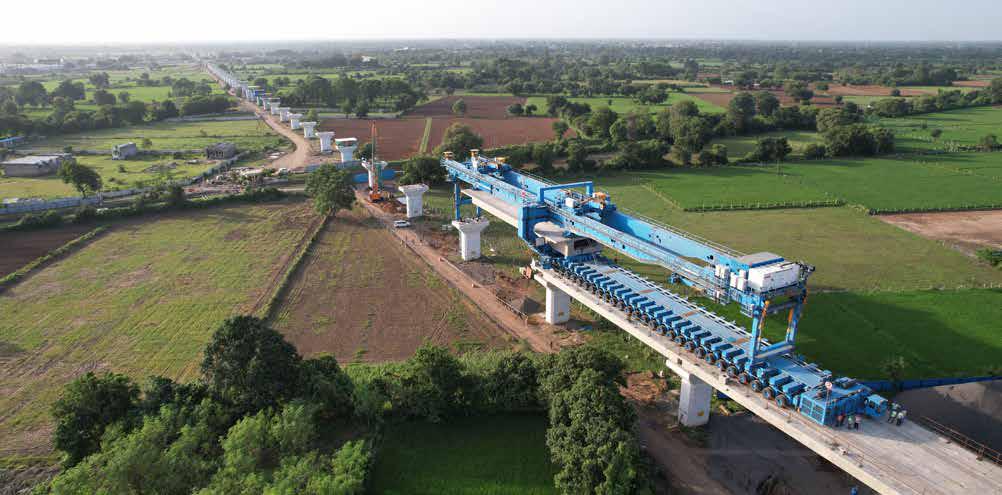
Testing the ground
Soil testing and preparation of the foundation recommendation reports were the initial deliverables that involved government testing agencies, laboratories, and academic institutes. When matters started to stick in the mud, the project team established three state-of-art testing laboratories, compliant to ISO and NABL standards at site to undertake tri-axial and consolidation tests with renowned testing equipment. “Quicker testing meant speedier reports and recommendations on the deep foundations for the viaduct and bridges,” quips Rajesh Srinivasan, Head – Technical Services. Special testing like Cross Hole Sonic Logging (CHSL) that confirms pile integrity to withstand loads were conducted on a large scale for the first time in India; special material approval committees and policies ensured that the product and services procured were compliant to meet the Employer’s requirements.
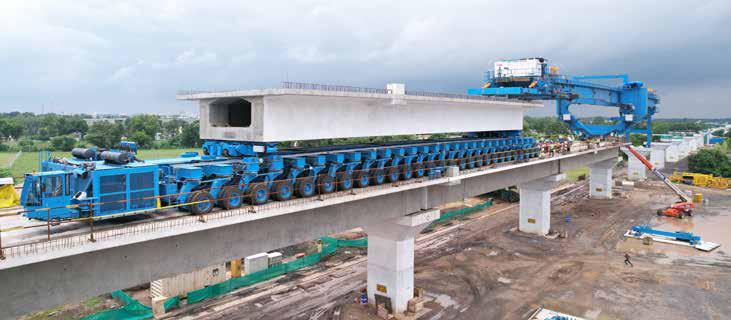
The first set of Straddle Carrier, Girder Transporter & Launching Girder was commissioned in January 2022. All sixteen sets of the moulds are now being manufactured in India, for which vendors possessing adequate skills to adopt the technology and produce fit for purpose moulds and other necessary construction equipment have been developed.
Timely availability of material & machinery
Ready availability of heavy equipment was an issue since deliveries from China were severely affected due to the pandemic, port congestions and power cuts. “With project delivery on the line, we choose to look inward rather than outward,” remarks Mohan. With the timely availability of the full span and segment moulds remaining top priority to commence round the clock operations of the casting yards, the team decided to manufacture the equipment within India, as a great example of the ‘Make in India’ spirit. As a result, the first set of Straddle Carrier, Girder Transporter
& Launching Girder was commissioned in January 2022. All sixteen sets of the moulds are now being manufactured
in India, for which vendors possessing adequate skills to adopt the technology and produce fit for purpose moulds
and other necessary construction equipment have been developed.
Global situations including the Russian aggression in Ukraine and the Beirut blast sent the price of Ammonium Nitrate skyrocketing by 80%. Yet, the team maintained 24×7 operations of the five quarries and crushers to ensure nonstop supply of aggregates.
Speed is of the essence
The project’s first 500 piles were completed in 135 days with the plan to complete 5,000 piles in 309 days. “We are gearing up to reduce the cycle time,” affirms a confident Rajesh, “as shown by performing two full span castings in one day in our casting yard at Ch 434. The River Mahi foundation works cover twelve well sinking and our teams have attained to reach up to the scour depths for each of the wells before the peak of monsoon.” With two casting yards fully operational with 16 sets of full span moulds, the full span girders are being casted rapidly to feed the viaduct construction. “Our fastest cycle time of Pile cap to Pier cap is 14 days at C6,” Rajesh reveals. The shortest Pier with Pier Cap is 4.1 m and the tallest, 22 m; the tallest Pier over River Mahi is 32.9 m.
“We are gearing up to reduce the cycle time as shown by performing two full span castings in one day in our casting yard at Ch 434. Our fastest cycle time of Pile cap to Pier cap is
14 days at C6.”
Rajesh Srinivasan
Head – Technical Services
Digitalization is further improving the speed of construction. Presently, the team is performing time and motion studies over the casting yard operations involving the movement of inner moulds, straddle carriers, productivity of rebar fixing and concreting to reduce idling time, loss of production and thereby enhance value for the Client. “We have undertaken measures such as bar coding, RFIDs on the movable assets, forms, moulds to track and measure performance to reduce production cycle time,” elaborates Mohan, “while our P&M is equipped with mechanisms to avoid down time, ensure preventive maintenance, avoid downtime and idling.”
Maintaining stringent timelines & monitoring
“A programme spread over 1370 days with 23 milestones, complex interfacing requirements and running without much float on construction activities is critical to monitor,” points out Amit Joshi, Head – Contracts. “Our various teams of planners, schedulers and construction specialists strictly control parallel work fronts enabling us to achieve our first five milestones.” The activities are planned well in advance to gather the required resources to avoid slippages to the best extent possible.
“A programme spread over 1370 days with
23 milestones, complex interfacing requirements and running without much float on construction activities is critical to monitor. Our various teams of planners, schedulers and construction specialists strictly control parallel work fronts enabling us to achieve
our first five milestones.”
Amit Joshi
Head – Contracts
A team of schedulers are controlling and monitoring resources through a three-week look ahead and reporting mechanism and working round the clock to fulfil the Client’s requirement to have an online reporting Project Management Information System [PMIS] using Oracle’s Primavera Unifier platform, which is presently running as a pilot project. The information is keyed in real time to formulate dashboards and enable high level monitoring to overcome challenges and remove site constraints.
Harnessing manpower & combatting bad weather
As the Project progressed, there was scarcity of skilled manpower, especially for pre-casting full span girders, being cast for the first time in India. With the pandemic depleting the workforce, the CSTI played a vital role to train 600 personnel in welding, steel fixing, masonry, and land survey. “Our craftsmen have successfully completed training in rebar fixing, formworks, concreting and have been absorbed into the project,” remarks Mohan.
The Cyclone Tauktae and some exceptionally heavy rains have threatened to severely disrupt operations, but the team is holding its own and pushing progress.
“The availability of moulds, launching equipment, and skilled craftsmen are inherent requirements and critical to deliver the project on time to quality,” sums up Ramesh. “Now, with a supply chain within India aware of the construction technology we have adopted, a pool of talented engineers and other skilled human resources, and future-ready manufacturing set-ups, we are well placed to deliver to our Client’s requirements.” He is happy that the site has already clocked 6.4 million safe man hours and measuring up to the immense interfacing requirements.
“The availability of moulds, launching equipment, and skilled craftsmen are inherent requirements and critical to deliver the project on time to quality. Now, with a supply chain within India aware of the construction technology we have adopted, a pool of talented engineers and other skilled human resources, and future-ready manufacturing set-ups, we are well placed to deliver to our Client’s requirements.”
Mohan Ramesh
Task Force Leader
MADHYA PRADESH EXPRESSWAY – DRIVING FOR A
TOUGH DEADLINE
The Madhya Pradesh Expressway, Package no 22 was awarded by NHAI with the clear understanding that it had be completed in 2 years. Situated near Ratlam, the team has to construct 25 km of perpetual flexible pavement,
33 Bridges, 48 Culverts, 16 Underpasses, 1 ROB and 2 interchanges involving 60 lakh cum of earthwork, 7.5 LMT of asphalt and 2.5 lakh cum of concrete. Once completed, the Delhi Vadodara Expressway, of which the MPE is a segment, will be the country’s longest under the flagship Bharat Mala programme.
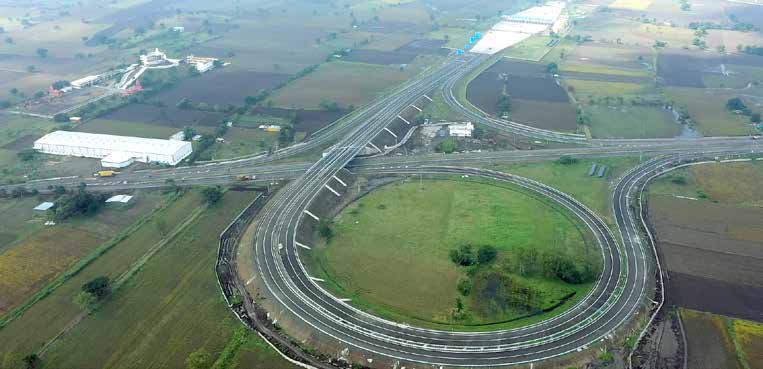
Micro-planning, strict monitoring and tireless efforts helped the team achieve their
first milestone of 10% of invoice 168 days ahead of schedule, the second milestone
(35% of invoice) 218 days ahead of schedule and third milestone (70% of invoice)
155 days ahead of the schedule.
Firing on all cylinders
Mobilization began in July 2020, almost 4 months before the appointed date, right in the middle of the monsoon and the pandemic storm. “Soon all the plants and precast yards were set up and the statutory approvals were obtained within two months,” informs Project Director, Jeeva David, who seems to be on top of things. “Our effective liaising and relationship building with the Authority, CALA and other local authorities helped to resolve local issues and obtain nearly 90% of the land on the appointed date.”
Post the RREC conclave, it was decided that 95% of the critical designs and drawings would be approved at the preconstruction stage, which was a huge head start. The team planned and ensured to run all the plants with EB power instead of DGs and installed solar plants that significantly reduced costs. “With this massive ‘push’, we commenced the WMM works in the third month and asphalt paving works in the fourth month from the Appointed Date,” informs
Project Manager, Anil Kumar Sachan.
“With this massive ‘push’, we commenced the WMM works in the third month and asphalt paving works in the fourth month from the Appointed Date.”
Anil Kumar Sachan
Project Manager
Micro-planning, strict monitoring and tireless efforts helped the team achieve their first milestone of 10% of invoice
168 days ahead of schedule, the second milestone (35% of invoice) 218 days ahead of schedule and third milestone
(70% of invoice) 155 days ahead of the schedule. “Our success is thanks to several new initiatives like using 100% crusher sand instead of river sand, constructing a Gabion wall in place of a RCC retaining wall, utilizing 4 lakh cum of rock cut materials as rock filling in the high embankment stretches and opening up fronts by talking all activities in parallel,” flags off Planning In-charge, N V Dhananjaya.
“Our success is thanks to several new initiatives like using 100% crusher sand instead of river sand, constructing a Gabion wall in place of a RCC retaining wall, utilizing 4 lakh cum of rock cut materials as rock filling in the high embankment stretches and opening up fronts by talking all activities in parallel.”
Dhananjaya N V
Planning In-charge
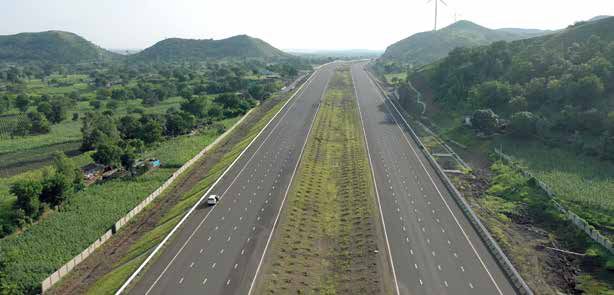
The team has laid 5,000 MT of WMM in 24 hrs, 5,000 MT of DBM in 19 hours, continuously laying 15,000 MT of DBM within a stipulated time of 69 hours and more than 80,000 MT of asphalt in the months of May and June 2022.
Overcoming disruptions
Although the pandemic proved to be a huge speed-breaker, the project team have stuck to their guns and in their concerted effort to make up for lost time, have created several records along the way. The team has laid 5,000 MT of WMM in 24 hrs, 5,000 MT of DBM in 19 hours, continuously laying 15,000 MT of DBM within a stipulated time of
69 hours and “more than 7.50 lakh MT asphalt produced and laid within a period of 15 months is the highest for any road project till date in L&T,” enthuses Anil, “and our quarry and crusher teams completed 25 LMT of crushing in a span of 15 months and crushed 17,000 MT of aggregates / GSB in a day.”
Anil is delighted that the project has not received a single customer complaint throughout the year, it has been
appreciated by NHAI and won several awards including The Best Contactor Award, the award for achieving targets within the timeline, and appreciation awards for both the Project and Liaising Managers. “It has been our constant endeavour from the word ‘go’ to never lose sight of our various milestones and to deliver a project in time to quality and safety,” sums up Project Director, Jeeva David J, visibly proud of his team’s progress till date. “All projects have their own set of unique challenges and the MPEP is no exception but the difference is in how we, as a team, are standing shoulder-to-shoulder to overcome the roadblocks and forge ahead. That our client is cognizant of our effort, appreciates our work and trusts in our capabilities are a huge bonus for us.”
“It has been our constant endeavour from the word ‘go’ to never lose sight of our various milestones and to deliver a project in time to quality and safety. That our client is cognizant of our effort, appreciates our work and trusts in our capabilities are a huge bonus for us.”
Jeeva David J
Project Director
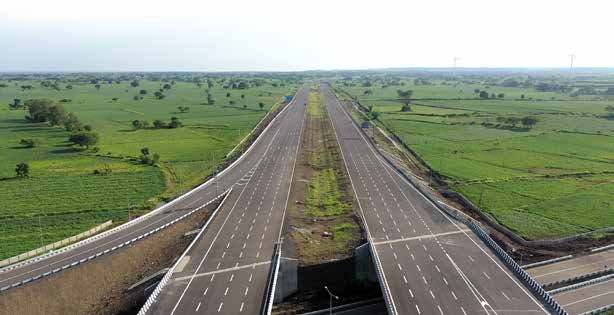
INTEGRATED TRANSIT CORRIDOR – CONSTRUCTING IN THE HEART OF BUSTLING NEW DELHI
The Integrated Transit Corridor, part of the redevelopment of Pragati Maidan, was planned by the Central Government to tackle the traffic woes due to a perpetually clogged Mathura Road and a choked Ring Road-Bhairon Road. An elaborate traffic solution has been designed to ensure that all the road crossings would be signal free, and capacities augmented. RREC is constructing a 1.6 km tunnel and 5 underpasses as part of the Pragati Maidan Project that was inaugurated on June 19th, 2022, by the Prime Minister of India.
However, when work kicked off in November 2017, Project Director, Ajay Asthana, and team were greeted by various challenges. “Shifting live utilities in an urban environment meant coordinating with different government utility agencies and despite utility shifting being in the client’s scope, we deployed our Utility Shifting coordination team to speed things up,” notes Ajay. The result was that all the major utilities were timely and quickly shifted that won PWD’s appreciation.
“Shifting live utilities in an urban environment meant coordinating with different government utility agencies and despite utility shifting being in the client’s scope, we deployed our Utility Shifting coordination team to speed things up.”
Ajay Asthana
Project Director
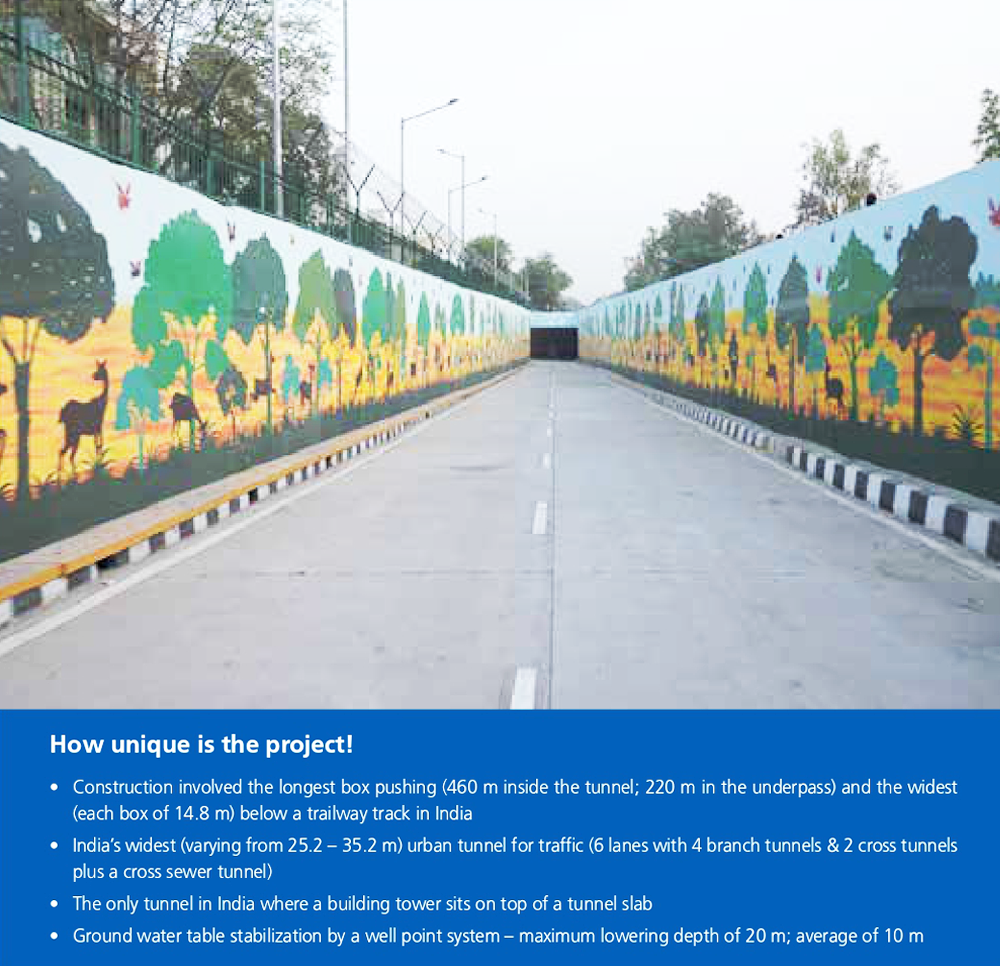
Traffic is an ever-present hazard for road projects but in this case diverting thick traffic yet maintaining a smooth flow and proceeding with construction was a huge balancing act. The team skilfully planned the diversions and ensured
that the structures could be completed without issues that again won accolades from the Government bodies and
daily commuters.
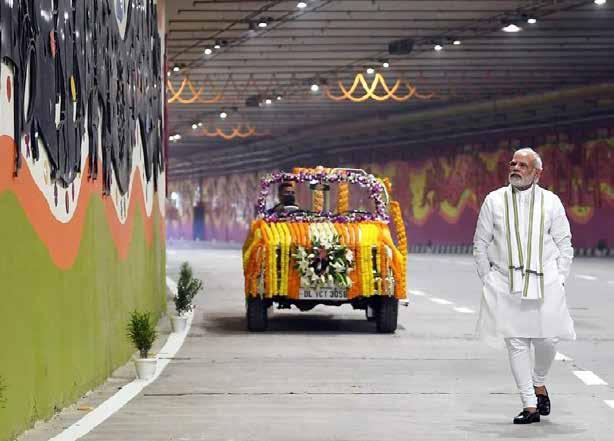
PM at Pragati
An Indian record: 70,000 sq. meters of artworks based on traditional Indian concepts
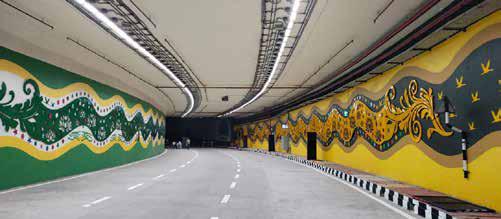
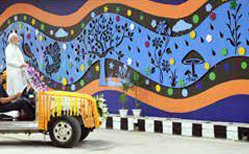
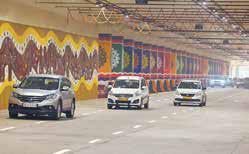
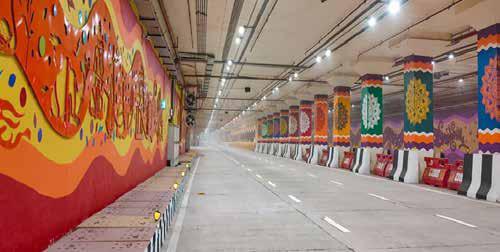
The Pragati Maidan tunnel is India’s widest urban road tunnel.
The project required excavation of up to an average depth of 8-10 m below the ground level. De-watering was a major challenge with the River Yamuna flowing close by and high ground water tables. Construction was carried out by lowering the ground water table using an elaborate Wellpoint dewatering system. Planning Manager,
Ms. Sweta Chaturvedi, refers to the box pushing method that the team adopted. “This is one of the longest & widest box-pushed tunnels below 7 railway tracks (280m length) and built such that it will not hinder future railway expansions,” she says. An exhibition Hall No.6 is being built on the slab of the tunnel resulting in a few columns resting on the tunnel with each column’s vertical load being around 3,000 tons.
“This is one of the longest & widest box-pushed tunnels below 7 railway tracks (280 m length) and built such that it will not hinder future railway expansions.”
Ms. Sweta Chaturvedi
Planning Manager
“Managing the complexity of a high ground water table, the critical challenge of box pushing below ‘live’ railways tracks, constructing below major Delhi roads with ‘live’ traffic above and, most importantly, the extreme weather conditions that varied from 50 degrees in summer to 1 degree in winter were challenges,” points out Subhash Singh, Senior Manager-QA/ QC, “but the PM’s appreciation and achieving the final COD from client gave me immense satisfaction.”
“Managing the complexity of a high ground water table, the critical challenge of box pushing below ‘live’ railways tracks, constructing below major Delhi roads with ‘live’ traffic above and, most importantly, the extreme weather conditions that varied from 50 degrees in summer to 1 degree in winter were challenges but the PM’s appreciation and achieving the final COD from client gave me immense satisfaction.”
Subhash Singh
Senior Manager – QA/QC
Stunning murals floor the PM
This project boasts of the longest artwork of around 70,000 sqm representing various forms of Indian culture – festivals, rituals, seasons and more. During his inauguration address, the Prime Minister of India quipped that he was a little late for the event as he abandoned his buggy and walked to study and enjoy the murals. The 1.36 km long wall starts on Purana Qila Road, passes under Pragati Maidan, terminating on Ring Road. The tunnel that features an artery and four branches, slashes travel time between central and east Delhi and the satellite towns of Noida & Ghaziabad by about
15 minutes. Although ranging in width from 28.2 m to 42 m, the Pragati Maidan tunnel is India’s widest urban
road tunnel.
The project team’s challenges ran both high and low! Structures had to be constructed near the Yamuna River at
5.69 m below the water table, with two cross tunnels 8–9 m below the water table. “At the Yamuna River, we adopted a well point and deep well dewatering system, and for the cross tunnels, an open dewatering system as the soil strata is clay,” informs Udai Narain Yadav – Assistant Manager (Civil), RREC SBG. The box pushing at the Underpass 05 embankment was at a height of 19 m above ground with the team’s major challenge being the railway track that was skewed at 40 degrees. They pushed the box from a single end with the help of hydraulic jacks and power packs and have thus far successfully completed 175 m of the total 215 m.
“At the Yamuna River, we adopted a well point and deep well dewatering system, and for the cross tunnels, an open dewatering system as the soil strata is clay.”
Udai Narain Yadav
Assistant Manager (Civil), RREC SBG
“The tunnel will be equipped with the latest smart MEP features like smart lighting, active firefighting systems, passive heat sensing systems, mechanical ventilation & automatic pumping systems, a digital traffic management system with CCTV security, telephones, and public announcement systems,” informs Ajay. 28 bidirectional German-made jet fans ensure ventilation, while sensors continually measure carbon dioxide and visibility levels, and an optical-fibre-based linear mechanism will detect heat levels that will trigger sprinklers if the temperature rises above permissible levels.
The project will create a distinct ‘green’ advantage as it is estimated to help reduce CO2 by approximately 13k Tons/Year, an average saving of 8 min/vehicle of waiting time and an average fuel saving of around 55 lakhs liters per year. Besides this, 15,688 trees have been planted on the Yamuna Belt.
“Apart from the extremely complex location of the project in the heart of Delhi, we successfully overcame the several challenges of NGT/Central Pollution Control Board/various law enforcing government departments, the lengthy farmers’ agitation, CAA and Covid restrictions,” mentions a relieved Subrat Kumar Parida, Manager – FA&A. “We, however, kept up our untiring efforts under the guidance of our Project Director to successfully complete our project,” he rounds
off jubilantly.
“Apart from the extremely complex location of the project in the heart of Delhi, we successfully overcame the several challenges of NGT/Central Pollution Control Board/ various law enforcing government departments, the lengthy farmers’ agitation, CAA and Covid restrictions.”
Subrat Kumar Parida
Manager – FA&A