SEVERAL WET PROJECTS PUSH FOR THE FINISHING LINE
The theme of ‘making the final push to completion’ sits perfectly on all the WET IC projects featured in this article. They have, without exception, put in the hard yards, overcome lots of strife, and now stand at the threshold of completion, with their respective site leadership and teams focused on applying the critical finishing touches.
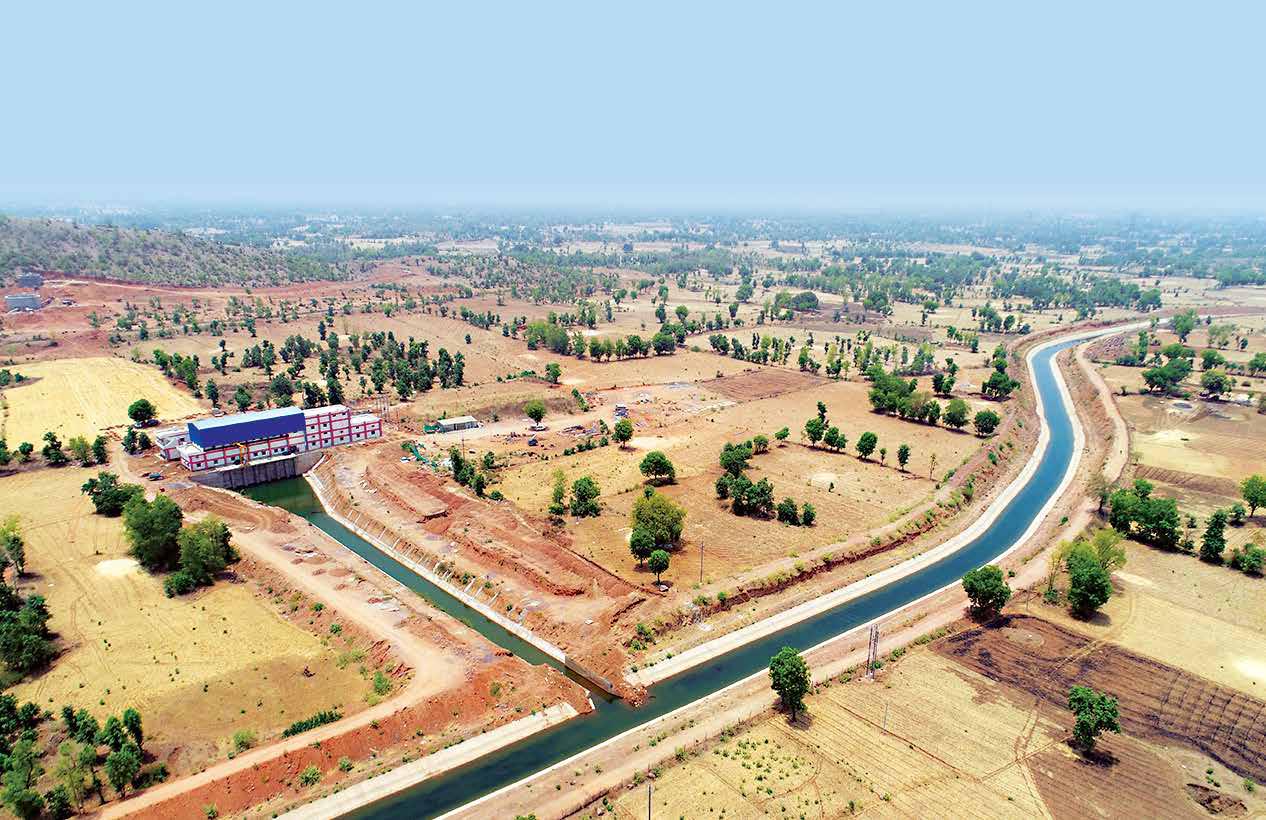
NAGAUR WATER SUPPLY PROJECT
INORDINATELY DELAYED, YET DELIVERED IN TIME
The word ‘delayed’ is perhaps the most recurring word in Project Manager Hemkant Sharma’s thoughts, for most of the activities at his project – Package 5 (CDS-02) to construct a Cluster Distribution System for 119 villages & dhanies (other habitations) of Makrana Tehsil under JICA in Nagaur, part of the Rajasthan Rural Water Supply & Fluorosis Mitigation Project – were delayed.
“We have completed the project, fulfilled all our contractual obligations in time and have harvested all the contractual benefits like EOT/claims, etc. We have completed execution as per our schedule with safety and quality without a single contractual penalty and with no lapses in contractual benefits.”
Hemkant Sharma
Project Manager,
Nagaur water supply project
“The design and approval of the EMI items were delayed by 36 months, as were the pump and motor document,” he begins. “Land clearances were delayed for the ESR locations; the design and approval of pumphouses, CWRs & ESRs, permission for State highway crossings were all delayed. The project faced acute fund crisis throughout its tenure, adding to the disruptions caused by the pandemic, and we were really with our backs to the wall.”
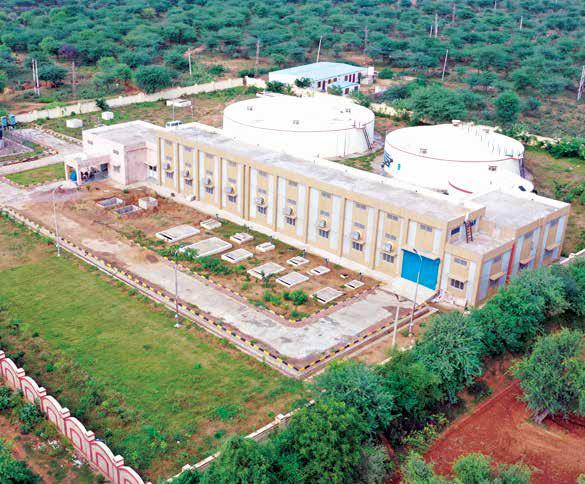
Cluster Distribution System, Nagaur
A tribute to Hemkant’s character is that he and his team took all these in their collective stride. “We have completed the project, fulfilled all our contractual obligations in time and have harvested all the contractual benefits like EOT/claims, etc. with timely documentation, meticulously maintaining data on price variations, GST impact claims, time extensions and the like.” He pauses a moment for effect. “We have completed execution as per our schedule with safety and quality without a single contractual penalty and with no lapses in contractual benefits.”
Involving last-mile water connections in homes, the team faced severe resistance from the local population, largely owing to the fears of the pandemic. “For implementation, we had issues as the water was not reaching some villages with more than 100 connections,” points out Quality In-charge Sudhir Kumar Patra. “To resolve it, we provided additional valves & zoning systems, incorporating them into the design to avoid rework later.” Both Sudhir and his colleague, EHS In-charge Robin Maprani, are delighted with their performances. While Sudhir’s Quality score sheet is clean with excellent customer feedback, Robin’s efforts have translated into the site clocking 2.3 million safe manhours without any fatalities or LTI, with a RoSPA Gold award to show for his efforts.
“We implemented ePragati to monitor project progress and prepare look ahead plans that helped us to deliver in time,” says Digital Officer Akshay J Shetty. “In addition, we used EDMS for design/ drawing submissions, the QIR app, Smart Glass for site reviews by the top management, and ViewEHS.”
While Hemkant is happy that the site has achieved a gross margin better than ACE, he flags off some of his other triumphs like building the highest capacity for an elevated storage reservoir of 1,300 KL with 22 m staging, laying a pipeline network of 1,619 km, creating pumping capacity of 1,623 cum./hour and 17.7 ML storage capacity in the reservoirs. Apart from a FICCI Award, a recognition of the team’s performance is a 10-year O&M contract on turnkey basis.
3X660 MW GHATAMPUR WATER CARRIER SYSTEM
PERFECT DELIVERY
The Water Carrier System for the 3×660 MW Ghatampur Thermal Power Plant is another project where the theme of ‘delay’ recurs. “We delivered the project on 22nd November 2021, as per contract; 100% invoicing is done and O&M works are already ongoing,” states a satisfied Project Manager, Vilas Shinde Ramji, though initially the going was tough with several external factors being spokes in the wheel for Vilas and his team. “We faced delays for clearance of fronts, to shift utilities like electric poles, water pipelines, etc. that fell into our scope. Clearances from the Forest Department to cut trees took all of six months; ROU clearances from NHAI, local third parties and other government organizations all took very long, and then there was the delay in mobilizing workmen due to the pandemic.”
“We delivered the project on 22nd November 2021, as per contract; 100% invoicing is done and O&M works are already ongoing.”
Vilas Shinde Ramji
Project Manager,
3×660 MW Ghathampur Thermal
Power Plant
Being a crowded area and right in the middle of the main route used to transport sand from the Yamuna and Betwa Rivers, open cut DI pipelaying was not possible. “Spotting an opportunity, we converted the DI pipelaying scope to trenchless methodology with a cost impact of some INR 24 crores,” smiles Quality In-charge Rajeev Vibhutty. “As per our contract, only 5 km of supply of unlaid pipe was payable against 100% BG. We persuaded the client and received payment for the entire 86 km supply of pipe without BG.” However, by going trenchless, the onus on the team was to ensure perfectly welded pipes at 5 m below ground level, for which the entire process from MS pipe inspection to hydrotesting was mapped and each joint DP tested.
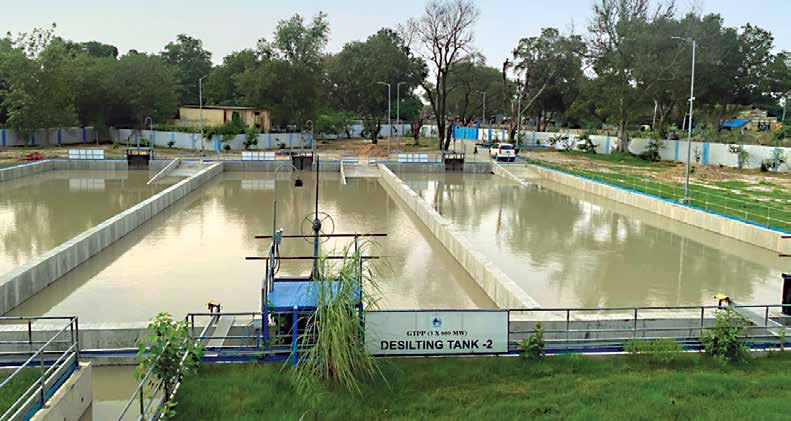
3×660 MW GTPP desilting tank-2
“10 pits were identified for working,” Rajeev explains the process, “and from each pit, 100 m of single pipeline shot was planned. We prepared a shoring method, WPS/PQR/WPQR, with at least four welders per pit. We conducted 63 welder tests, of which 42 qualified for total pits, and to ensure the quality of welding, we used 100% root DP tested welded joints and 10% of 41 joints were UT tested.” Hydrotesting the laid pipes was another huge task, for which dummy DI pipes were fabricated and welded with electrodes like Ni-55. Vilas chips in, “This innovative strategy helped us to bill the hydrotesting amount during the execution phase itself to create a positive cash flow.”
Executing 2 km of trenchless in the busy Ghatampur town was a challenge for EHS In-charge Ashif Eqbal. “Old, ‘live’ underground utilities were identified that had to be handled, and safety items like Local Exhaust Ventilation (LEV), motion scouts, hard barricading, blinkers, lux & sound meters, anemometers, gas detectors, and dewatering pumps ensured safety at site.”
“We have implemented BIM 3D, EIP Pragati, GIS Survey, P&M IOT & GPS, SafeArmZ and QIR at site,” declares a happy Digital Officer, Prakhar Singh.
Vilas is thrilled with the various awards the project has picked up, including the Timely Completion Award (December 2021), Best Emerging Site Award (2019) and Max Observations Award (2019), but what thrilled him most is the client’s appreciation for a project well delivered.
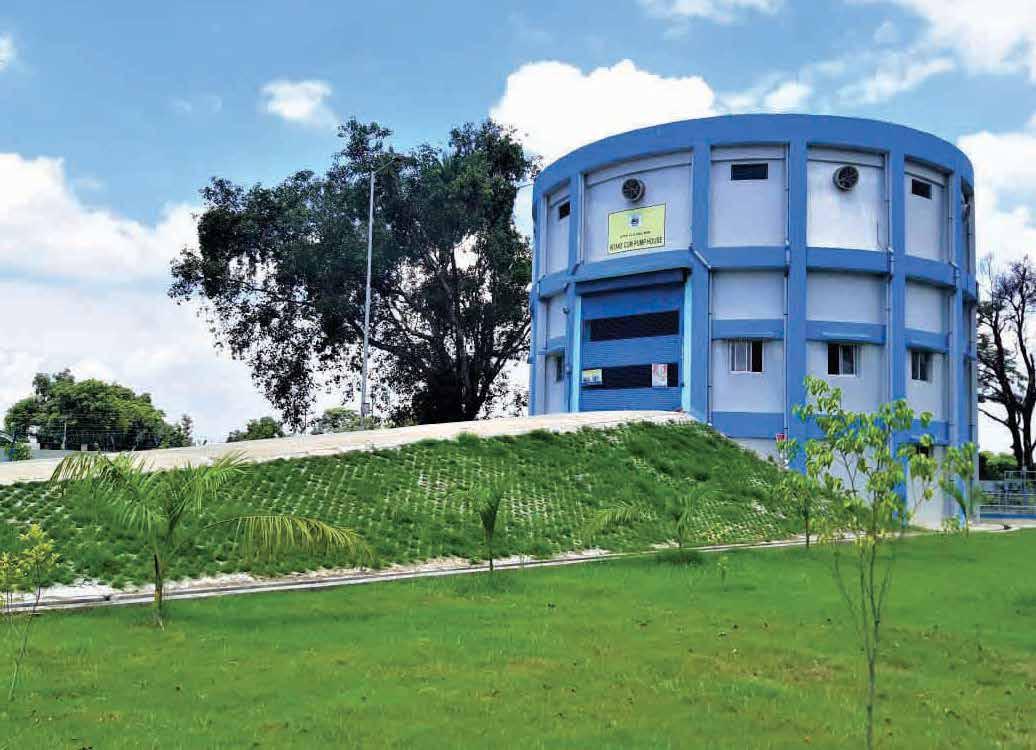
Intake cum pump house
BANSUJARA MICRO IRRIGATION SCHEME
TO IRRIGATE 75,000 HA OF LAND
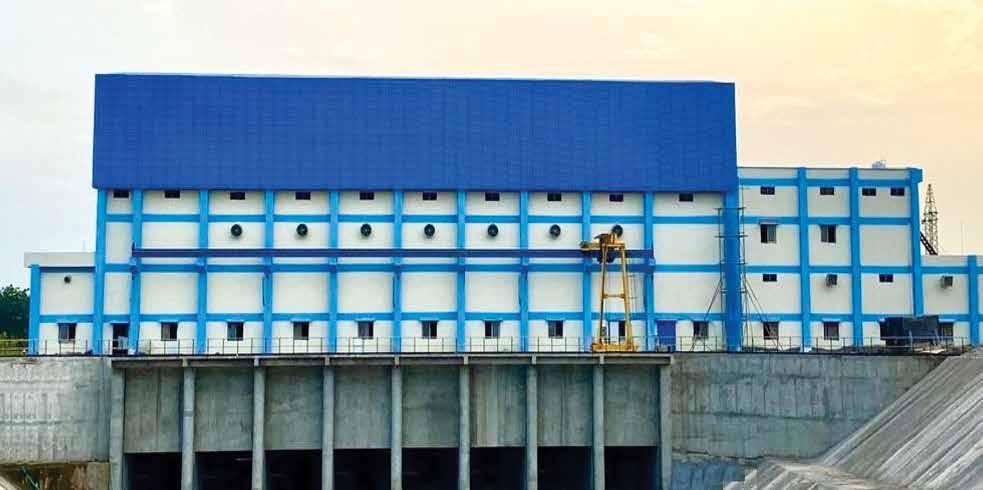
Bansujara Irrigation Scheme
The task before Project Manager Pradip Kumar Parida and his team is to complete the Bansujara Micro Irrigation Scheme, which will transform the lives of farmers by irrigating 75,000 Ha of culturable command area through a pressurized pipeline system. Having started in July 2016, the project is on the threshold of completion. “We started with a handicap, because early in the game we realized that we only had 4–5 months a year for pipe laying, i.e. April to June and then October to mid-November, and we had to lay a pipeline of 9,000 kms – 8,500 km of HDPE and 500 km of MS – cross-country, which required a lot of careful planning,” he says. The MS pipe of 3.15 mm thick coil, used for 237 km, is difficult to fabricate and lay due to its low thickness, for which the team mobilized qualified welders for precise,
quality welding.
The team faced a particularly severe monsoon in 2018 that extended the cultivation time, which in turn reduced their time for construction. To catch up lost time, the workforce was doubled. “Our plan was to simultaneously work on multiple fronts with highly qualified welders,” shares Quality In-charge Prakasam Sekhar about their strategy. “We laid 865 km of pipes (843 km of HDPE and 22 km MS) in a single month in April 2018, which is the highest in the whole of WET IC till date,” he adds, visibly proud of his team’s achievement.
“We started with a handicap, because early in the game we realized that we only had 4–5 months a year for pipe laying, i.e. April to June and then October to mid-November, and we had to lay a pipeline of 9,000 kms – 8,500 km of HDPE and 500 km of MS – crosscountry, which required a lot of careful planning.”
Pradip Kumar Parida
Project Manager, Bansujara Micro Irrigation Scheme
Acts of vandalism, theft, and damage to components from the villagers disrupted progress, forcing the team to conduct awareness programmes to make the villagers understand the importance of the project. “Despite discrepancies due to the pandemic, we have completed the entire physical works and, at present, have already completed 68,469 Ha as on December 2021,” informs Pradip. “With the support of the farmers and the local administration, we plan to complete the project by February 2022,” concludes a determined Pradip.
318 MLD WASTE WATER TREATMENT PLANT
AT CORONATION PILLAR
INAUGURATED ON 5TH MARCH 2022
“We have delivered India’s largest waste water treatment plant,” declares an understandably proud Ashutosh Kumar Awasthi, Project Manager of the 318 MLD (70 MGD) Wastewater Treatment Plant with 10 years’ Operation & Maintenance on DBO basis at the Coronation Pillar, New Delhi. The Sewage Treatment Plant was formally inaugurated on 5th March 2022 by the Hon’ble Minister of Health, Industries, Power, Public Works Department, Home and Urban Development Shri Satyendar Jain in the august presence of the MLA of the Adarsh Nagar Constituency, Shri Pawan Kumar Sharma, Chairman of Delhi Jal Board, and other dignitaries.
Although on top of the world, Ashutosh and his team would readily agree that it has been a hard-fought victory. Contractually awarded on 12th October 2016, the original completion date was 11th April 2019, but due to several delays, the revised date is 28th February 2022. “97.5% of our work is done and the project has been commissioned,” says Ashutosh. “It is on a trial run for 6 months with some road, drain and horticultural works in progress.”
“We have delivered India’s largest waste water treatment plant 97.5% of our work is done and the project has been commissioned. It is on a trial run for 6 months with some road, drain and horticultural works in progress. ”
Ashutosh Kumar Awasthi
Project Manager, 318 MLD Waste Water Treatment Plant
Being a joint venture with M/s Passavant Energy & Environment GmbH had its own set of challenges due to working culture differences, interdependences for decision making, deployment of resources, adopting L&T’s systems, safety procedures and IR management, and more. While that was an on-going battle, the site had to contend with a series of inordinate delays, due to several factors beyond their control. “Land handover was delayed, although we went ahead, surveyed and investigated the soil,” says Ashutosh. ROW was extremely delayed, the client took very long to appoint the project consultant, and the construction ban by the Delhi Pollution Control Committee and the farmers’ agitation further disrupted progress. Since the site was filled with loose fly ash, the team had to do ground improvement using the Dry Vibro stone column technique, and a high subsoil water table necessitated constant dewatering. “We faced some severe weather conditions and then there was the pandemic,” sums up Ashutosh, with a tight smile.
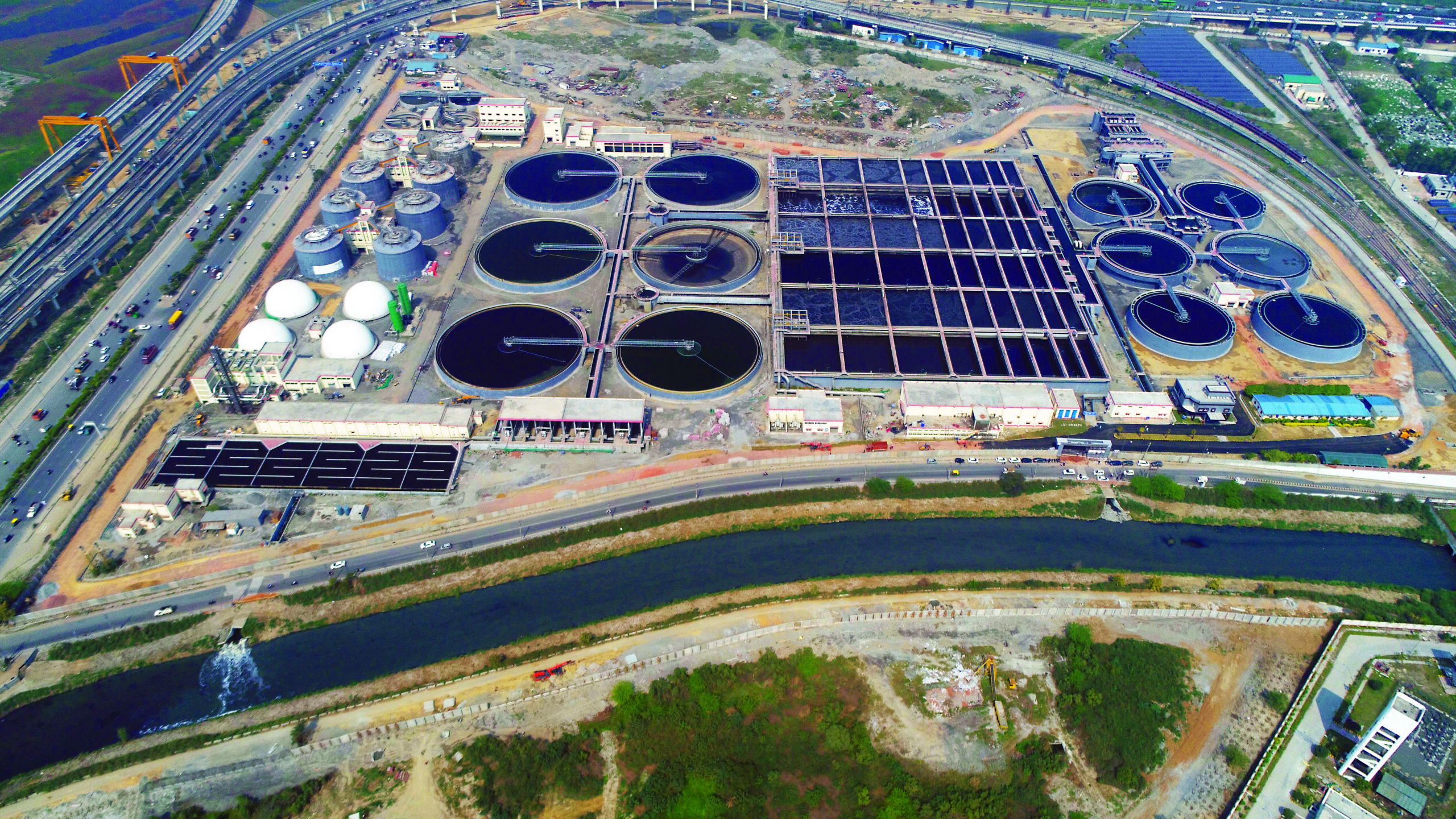
Coronation Pillar STP
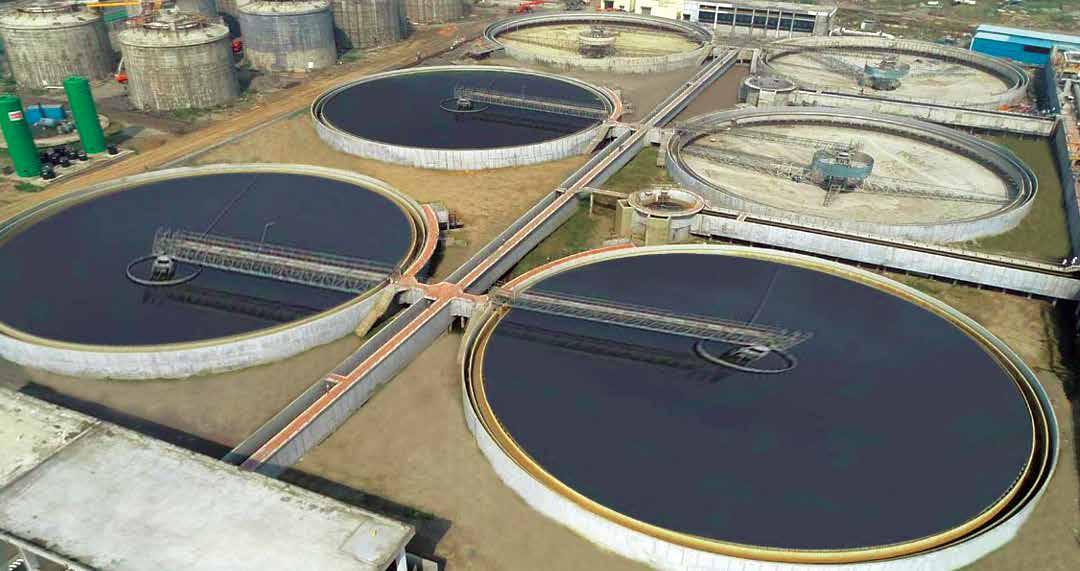
“For better control and to track resources, we divided the entire plant layout into 3 zones and deployed Senior Construction Managers for each zone reporting to the Project Manager,” explains Quality In-charge Aman Kumar. “We strategically placed tower cranes between the clarifiers and bioreactor tank to optimally use the access area, saving cost on P&M rental charges and fabricated 3.6 m high shuttering to construct the RCC walls of the bioreactor tank, which reduced cycle time and speeded up construction.”
With the object to protect the water bodies, the plant, based on A2O technology to treat municipal wastewater generated in New Delhi, is equipped with state-of-the-art biological nutrient removal facilities and designed to treat wastewater up to Biochemical Oxygen Demand (BOD) and Total Suspended Solids (TSS) levels of less than 10 mg/l, which is in line with the latest NGT guidelines.
“It is energy efficient,” reminds Aman, “and has India’s tallest sludge digesters equipped with sequential gas mixing, a German technology that ensures better mixing and higher biogas production.” It also boasts of India’s largest tertiary disc filtration to remove particulate matter from the treated sewage and meet the quality parameter requirements.
By way of automation, the team upgraded the concrete pouring methodology by replacing concrete pumps with Boom Placers and adopted slipform technology instead of conventional shuttering to construct the 18 m digester walls, saving overall construction time. “We poured 78,000 cum. of concrete and consumed 9,800 MT of steel to construct 57 structures and 8 digesters of 20 m dia. & 20.5 m height by Slipform method,” adds Ashutosh, mentioning that 50% of the liquid stream was commissioned in March 2021 and completed on 31st December 2021.
BALASORE WATER SUPPLY SCHEME
SUCCESSFULLY RISING TO EVERY CHALLENGE
“We have completed 99% of our work, with the balance pending due to ROW issues that will be completed within a month of getting the client’s clearance,” announces Project Manager K Karthikeyan, “but despite several challenges, our gross margin is still above ACE,” he says with a smile and a thumbs up.
The first challenge for the project team was that open excavation was not possible to construct the intake well on the banks of the Subarnarekha due to the quantum of water involved and the sentiments of the villagers. Therefore, they opted for the well sink method. “After constructing the intake well, the next challenge was how to draw the water from the river,” says Quality In-charge Abhigyan Dey. “We finalized a Jack pushing method to take the water into the well by pushing a 750 mm dia MS pipe as the intake channel, which played a critical role in our success.”
“We have completed 99% of our work, with the balance pending due to ROW issues that will be completed within a month of getting the client’s clearance but despite several challenges, our gross margin is still above ACE.”
K Karthikeyan
Project Manager,
Balasore Water Supply Scheme
“Initially our project was designed to supply water by constructing PSP to cover the identified villages, but after laying much of the pipeline, the client insisted that we provide individual household tap connections for all the villagers.” Karthikeyan’s face is grim. “Introducing the new scope without disturbing the core design was not easy in terms of material procurement, execution and cost, but we laid extra lengths of pipe through the streets and gullies of every village and successfully completed and commissioned on time.”
Micro-planning, constant reviews, and training engineers to execute multidisciplinary activities were key to their success. Digital Officer Sujit Das mentions the effective use of ViewEHS & QIP apps at site, while EHS In-charge Sujit Kumar Panda is glad that the site has thus far achieved 5 million safe manhours. “We have introduced RollerShifters to move pipes, which has significantly reduced damage to pipes when shifting, and have constructed a full area of PCC bedding at ground level to carry heavy HDT scaffolding for ESR,” mentions Abhigyan, by way of their
out-of-the-box thinking.
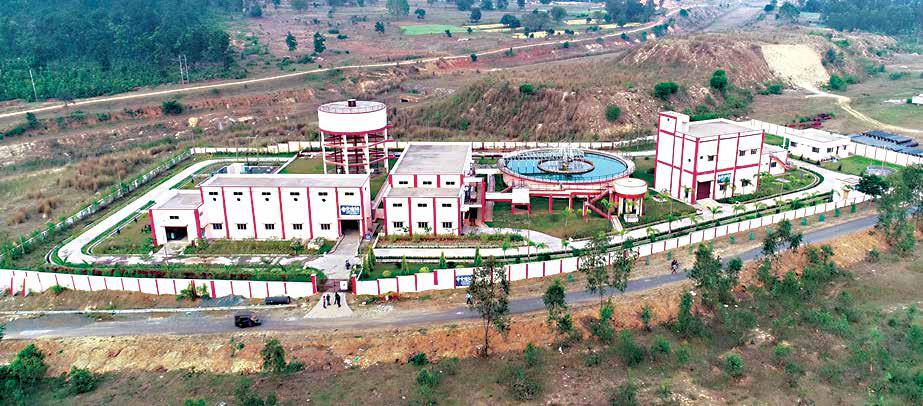
Balasore, Bhadrak Scheme
NANDAWADAGI LIFT IRRIGATION SCHEME
FULFILLING HOPES
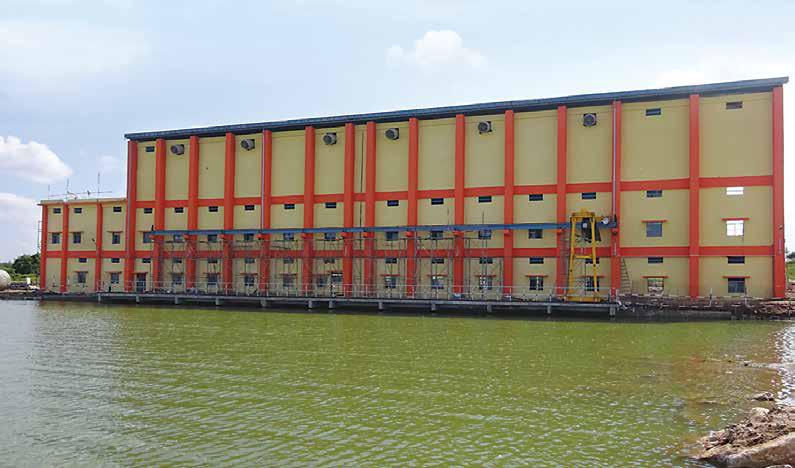
Pump house for Nandawadagi Lift Irrigation project, Karanataka
The Nandawadagi Lift Irrigation Scheme is a significant water life-line scheme to provide irrigation facilities to drought-prone areas of Karnataka’s Raichur district by lifting 6 TMC of water from the Narayanpur Dam of the Krishna River to irrigate 57,000 Ha of land. “One of our significant milestone achievements was the partial commissioning of the project, and it was an absolute joy to see the happiness on the faces of the farmers when the water was pumped out for the first time,” says an emotional Project Manager, Chinni Subbarayudu. Scheduled to close by April 2019, the project was delayed due to land acquisition issues, and Chinni and his project team have completed the project in January 2022 with only punch points remaining.
“Looks are often deceiving,” says Chinni with a serious face, “for though the project looked relatively easy to start with, we faced a lot of headwinds owing to a host of reasons: ROW issues involving both direct and indirect stakeholders, remoteness of the site where all facilities had to be established from scratch, lack of local support, difficulty to obtain timely administrative and statutory approvals, the pandemic, delay in mobilizing material due to restrictions on movement and, finally, workmen mobilization post the lifting of the restrictions.” That is a fairly long list, but the team has risen to all challenges and succeeded due to a combination of analytical skills, a proactive approach, close planning and monitoring the project schedule and issues, efficient people management, maintaining excellent relationship with the customer and timely follow-ups for approvals, especially of drawings, designs and rates.
Some innovative strategies the team adopted to enhance efficiencies included shifting the location of the Jackwell and 110/6.6 kV switchyard from a hard-rock location to one with mixed soil, excavating an intake canal with intermittent coffer dams to control seepage and increase excavation productivity, laying a service road cross-country along the MS pipeline with excavated earth from the trenches to save on Murram requirement, and convincing the client for epoxy painting of the pipeline and Guniting on site to save cost and time.
“One of our significant milestone achievements was the partial commissioning of the project, and it was an absolute joy to see the happiness on the faces of the farmers when the water was pumped out for the first time.”
Chinni Subbarayudu
Project Manager,
Nandawadagi Lift Irrigation Scheme
“Our plan was to increase the ratio of sub-contracting, but considering the requirements for heavy P&M for MS pipe laying and ROW issues, we had to strategize to take P&M into our scope to retain the sub-contractors,” points out Quality In-charge S Gopal. Further, splitting the same work between multiple sub-contractors in different stretches of the pipeline helped the team execute at multiple fronts. Another initiative was to lay 12 m pipes instead of normal 6 m ones with heavy capacity cranes (75 MT) to improve productivity, meet the high asking rate and reduce the labour requirement for more joints. All the MS pipe and electro-mechanical equipment procurements were completed well ahead of time, escaping the inflation of raw material prices.
“Almost 1,130 trailer trips were safely made to shift the MS pipes cross-country on earthen roads without any untoward incident,” informs EHS In-charge Aashish Meher. “Our work was executed in line with the approved SOPs & work methodologies, and we conducted training sessions to identify probable hazards with effective mitigation plans. We won the CII-SR EHS Excellence Award in 2019 with 4-star rating for Commitment of EHS practices and have clocked 1.23 million safe manhours at site thus far,” he adds proudly.
“Presently, only commissioning in the client’s presence is remaining, apart from a few checklists that are being attended to, after which we will hand over the scheme to O&M,” concludes Chinni, adding, “and the completion certificate will also be availed from the client, KBJNL.”
SIR PROJECT, DHOLERA
ON THE HOME STRETCH
The project to design and construct roads and services in the activation area of the Dholera Special Investment Region (SIR), Dholera (Gujarat), kicked off in March 2016 with an agreed delivery date of 30th June 2022. Project Manager Jyotsna Gautham’s confidence to meet her deadline stems from the fact that she and her team have only another 4% left to complete. “We have completed 400 km of pipeline activities, 136 km of information and communication ducts, 4,000 km of PLB ducts, and 136 km of power ducts along with 9 ESRs of 19.5 ML capacity,” she reels off her achievements.
However, Jyotsna will be the first to admit that it has been an arduous journey managing a site that is spread across 22 sq. km. “Designing itself took more than a year due to the intricate underground utilities network, but BIM modeling saved us a lot of rework and time, thanks to it detecting clashes,” she says with relief. Remoteness of the location – “we had to even put up dedicated mobile towers for us,” she interjects – adverse climatic conditions like dust storms in the summer, massive flooding during the monsoons, and the clayey soil that hinders movement all disrupted progress. Microplanning and flood management using huge dewatering sets and constructing bunds, working in parts & multiple shifts during the working period, and constructing temporary approaches were some of the team’s mitigation measures.
“We have completed 400 km of pipeline activities, 136 km of information and communication ducts, 4,000 km of PLB ducts, and 136 km of power ducts along with 9 ESRs of 19.5 ML capacity.”
Jyotsna Gautham
Project Manager, SIR project, Dholera
“We used a hybrid modality to construct 272 km of ducts for ICT and power cables using precasting and self-compacting concrete, outsourcing precast segments, installing plants for dry precasting, establishing a wet cast precasting yard, moving shutters, and conventional cast in-situ to fasttrack the works,” informs Quality In-charge Mohan Shaha. To sequence the underground utilities, the team interfaced with the road work teams. Primavera was implemented to track and monitor planned works, along with the Integrated Strip Chart.
“In addition to BIM, we use Bentley’s ProjectWise software for Enterprise Document Management for all engineering and construction submissions/correspondences,” mentions Digital Officer Ms. Uppala Supraja, “Google Forms for DPR reporting, ePragati, ViewEHS, the QIR app, P&M Insight app, Smart Glasses for virtual reviews, and more.”
By way of automation, the team implemented spot welding and cage bending machines for reinforcement cages. Self-compacting concrete used in collaboration with M/s Fuji Silvertech resulted in best-in-class precast segments of RCC ducts for the ICT network. By introducing 50% Ground Granulated Blast Furnace Slag instead of 100% cement, the team has reduced cost and saved carbon footprint. Stretch films and curing compounds have significantly reduced water consumption for curing. Little wonder, then, that the project has won the Green Cover award.
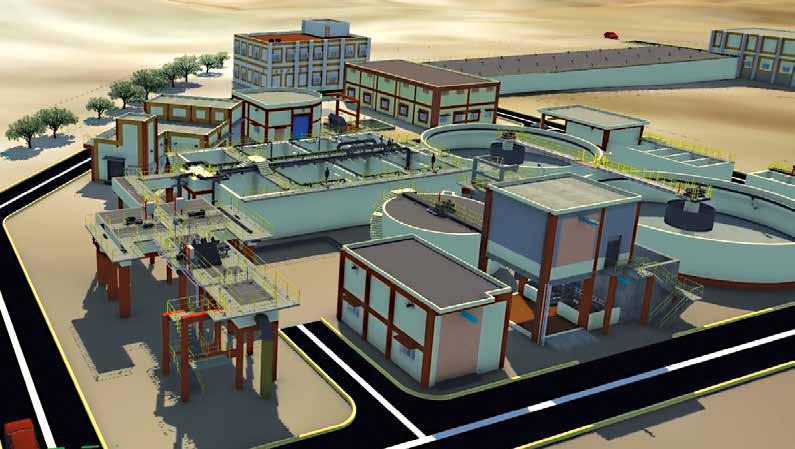
Dholera STP
“We have achieved 7 million safe manhours with nil LTI,” remarks EHS In-charge Himanshu Mukherjee, who is also delighted with the CII Award for Safety, the British Safety Council award and the annual EHS rolling trophy that the project has won thus far.
So, what worked for the project thus far? “Dividing the 22 sq. km project into multiple zones, delegating ownerships for each zone, preparing punch lists, conducting joint walkthroughs with clients & daily interface meetings, focusing on testing, and commissioning of the networks to hand over to customers seem to have worked for us,” smiles Jyotsna.
Every project faces unique challenges; the difference is in the mindset and teamwork required to convert them into opportunities for growth. All these WET IC projects have scored handsomely on those counts, and here is wishing them all the very best for their final push to completion.