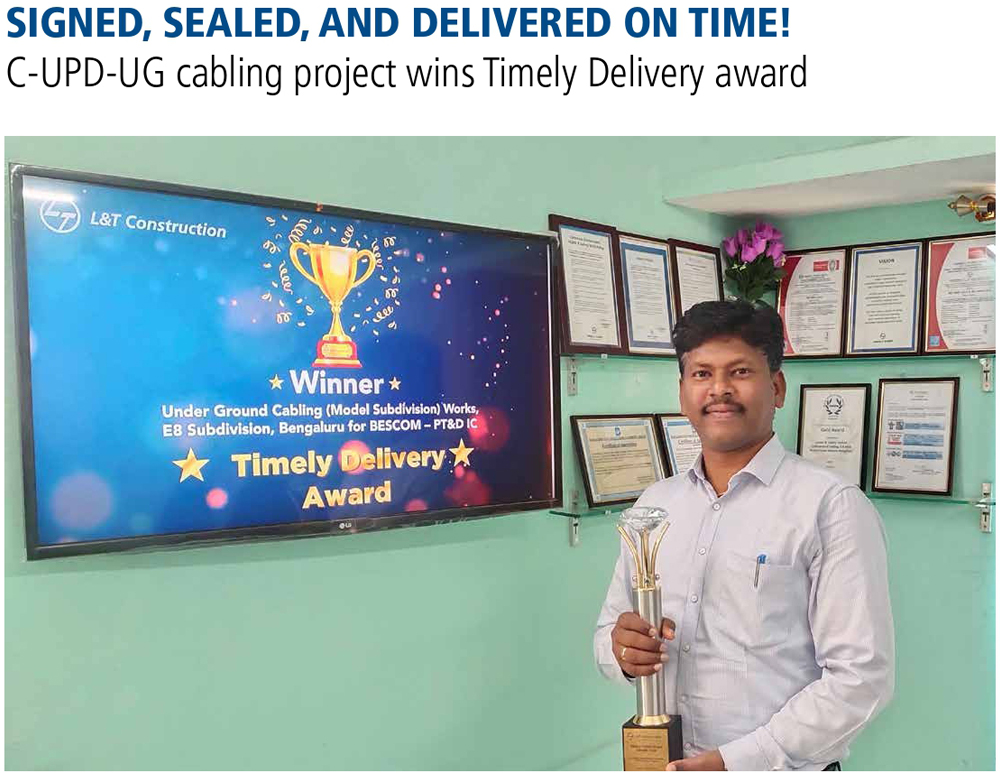
Work began on PT&D IC’s C-UPD-UG cabling project in Bengaluru for BESCOM (Bangalore Electricity Supply Company) right on cue on February 24th, 2018. The project involved underground cabling works under the Model subdivision scheme in the E8 subdivision of Shivaji Nagar division, East Circle, BMAZ North area on a total turnkey basis under rate contract for 2 years. Project Manager, K Dhandapani and his team delivered the project right on time on February 23rd, 2020, not a day earlier, not a day late. This outstanding achievement won the team the Timely Delivery Award for L&T Construction and although they have enough reason to celebrate, they agree that it was a hard-fought victory.
The Government of Karnataka and BESCOM envisions to convert Bengaluru’s entire overhead distribution network into an underground system to reduce T&D losses, power interruptions, ensure reliable quality power supply and avoid electrical accidents. To convert their vision into reality, 4 of the 54 subdivisions were chosen for a pilot project, out of which the E-8 subdivision was awarded to L&T. “After completing and delivering the project on time, we have been awarded six more similar projects by BESCOM in Bengaluru city for a total value in excess of INR 1,000 Crores,” says Dhandapani. Timely execution and delivery certainly have their rewards.
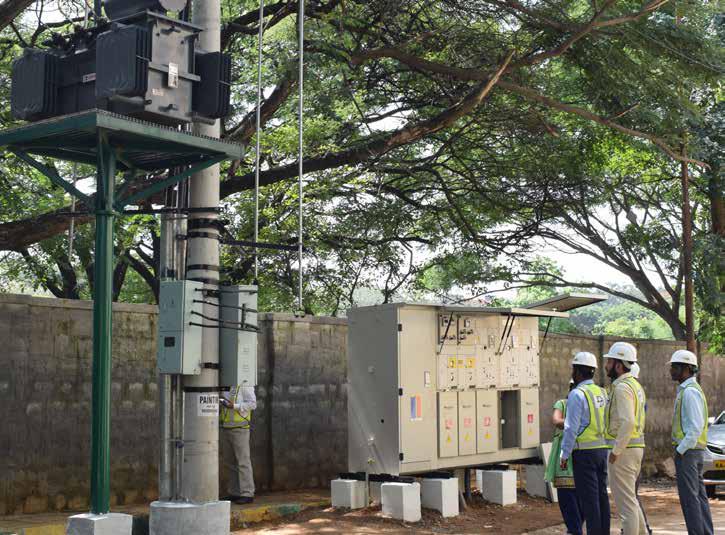
“How can there be projects without challenges?”
Dhandapani had to contend with several imponderables even as they started work. Since the project had been awarded on a rate contract basis, the total amount of work was only a guesstimate. Shivaji Nagar, like any place in Bengaluru, has high population density, narrow roads, and heavy traffic. “Several statutory approvals had to be taken prior to the commencement of work as we were going to execute in an urban location,” points out Planning Manager, Mrs. Swati M Rajapure, who played a dual role of Quality Head too. “Since high value materials scope was involved, it was essential to get the right materials at the right time.” In addition, since majority of their work was underground using the HDD method, the team had to deal with a lot of underground utilities like the GAIL pipeline, power cables, communication cables, traffic signal cables, water & sewage pipelines, all of which required close coordination.
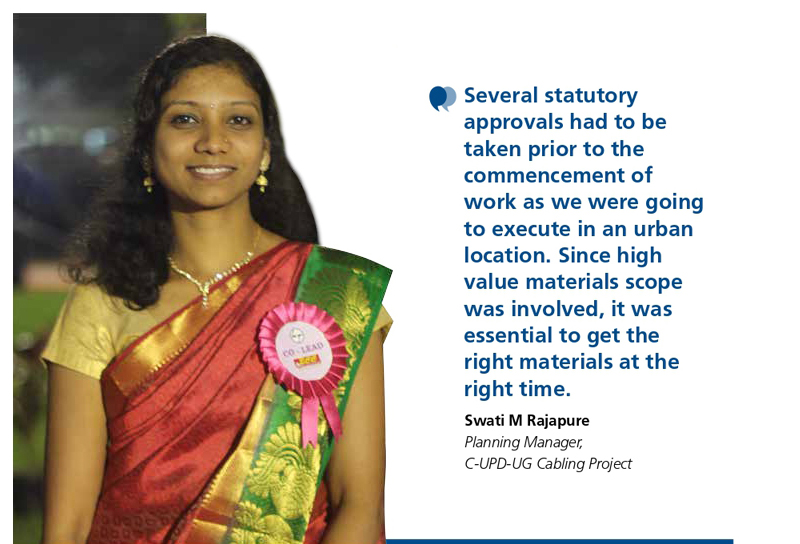
Dealing with government agencies is difficult in normal circumstances but having to obtain permissions from the Multi Agency Coordination Committee (MARCS) headed by BBMP involving several Government departments like BMP, BWSSB, BDA, BMRCL, KPTCL, BSNL, GAIL, HAL and the city police including traffic police and BESCOM was a tall order. “We deputed dedicated resources to vigorously follow up with all the departmental officials for permissions to commence road cutting,” says Dhandapani. As open trenches would disrupt traffic and endanger pedestrians, the LT UG scope had to be converted to LT ABC works to get started that interestingly reduced the scope by 23%. Overhead activities like installing DTCs, GOS, stringing LT AB cables and dismantling the existing 11kV line works all required everyday line clearances and hence execution was so planned so as not to be disrupted by shutdowns for better productivity and zero LTIs.
“As the prefabricated structure was proposed as an additional item in place of the plinth, the approval process took considerable time,” remarks Dhandapani, “so, we focused on the feeders that did not involve these activities and since the transformer mounting arrangement was with a prefabricated structure, we executed with less manpower but better productivity,” he smiles. Right of Way was another roadblock for which the team held several meetings with different stakeholders to clear the way to move ahead.
On the fast track
As soon as the DWA was received, the team got cracking and the next six months went into planning, engineering, and procurement, starting with a detailed survey to finalize quantities. An unforeseen hitch was the assembly elections and the election code of conduct due to which no construction was possible for six months. “We, however, utilized this period to micro level plan and finalize activities for each feeder,” shares Swati, apart from proactively obtaining permissions from various third parties such as the PWD, NHAI, Railways and the like.
Once the elections were over, construction began in earnest that lasted for 18 months, including a monsoon during which the team adopted various methodologies and initiatives to reduce the involvement of labour, bring uniformity and quality to the work, save time, reduce cost, and push progress. “During the survey, the scope of bulk items like RMU and HT UG Cable increased by 6% and 21% respectively that required special permissions from BESCOM,” reveals Section In-charge, Amit Bhat.
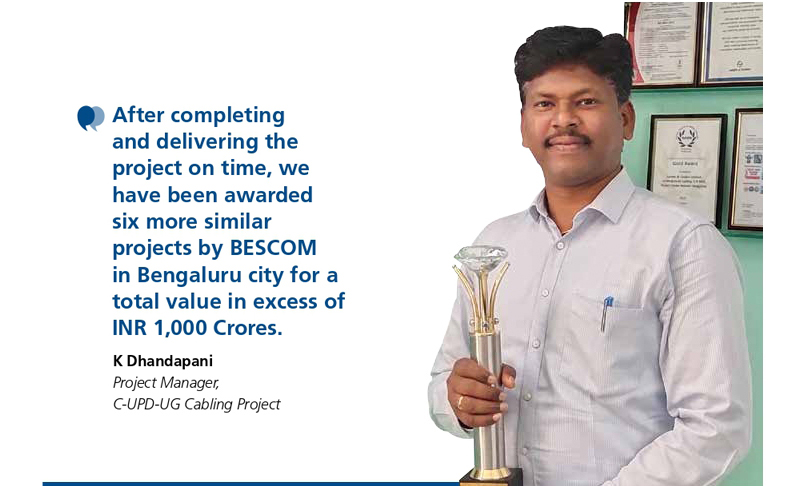
Dhandapani flags off a couple of other innovative steps to improve their productivity and save time. “Considering the involvement of more manpower and civil masonry works in the awarded scope of DTC plinth type foundation, we proposed a specially designed prefabricated structure platform to mount the transformer that worked very well for us,” he says. Workmen were trained on mock-ups in the store yard before engaging them at site and RMU foundations were implemented with pre-casting concrete.
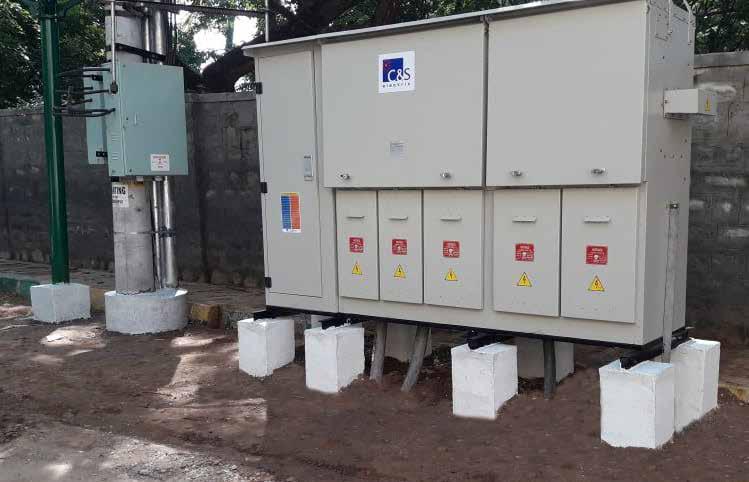
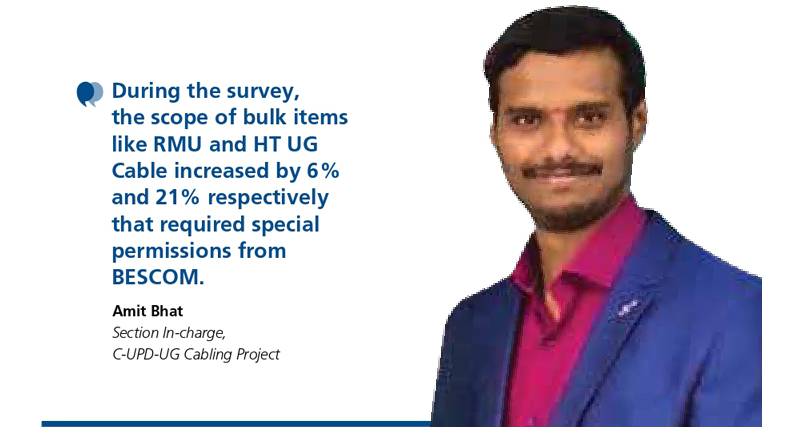
Precise project management, monitoring, control
“Our project monitoring and control were spot on with daily progress updates and regular reviews with the Cluster and Segment that resolved issues and speeded up progress,” informs Sahukar Mohan Rao, another Section In-charge. Prompt sourcing of material was critical to their success. “All the required 3M resources of Men, Material and Machine were mobilized at the right time for optimum utilization because of our rigorous follow up with our client and vendors,” he adds.
On the peoples’ front, every team member was empowered to take decisions to achieve a common objective. “Training, delegation, rewards, constructive feedback and motivational events and sessions kept the team engaged and, on their toes,” smiles Dhandapani.
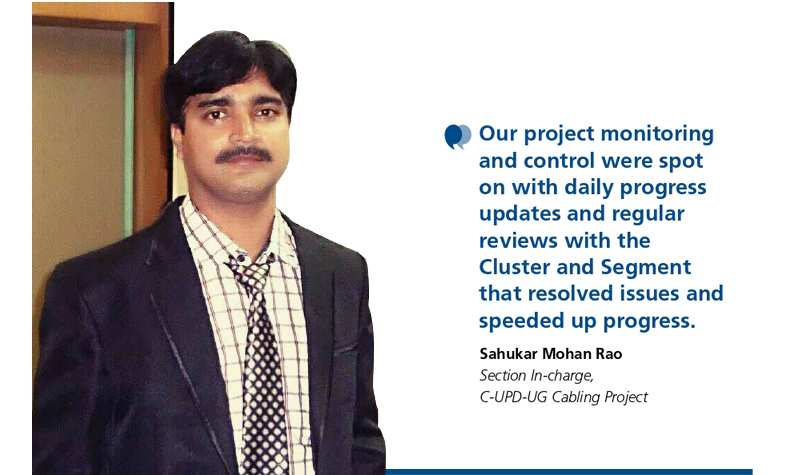

Digitalization leads the way
Swati reels off a slew of digital solutions that the team adopted. “We had Empower to monitor project progress and materials in real time and the Quality App to ensure product quality and work methodologies,” she shares. A digital display board showed DPRs, a fleet card system was used for fuel purchase and CCTV cameras provided surveillance at the store yard. Workmen were screened through WISA while VR modules came in handy for their training. EHS Head, Biman Roy adds how useful the Safety App was to maintain safe operating procedures, proud of the RoSPA Gold the site won.
“In essence, it was the triumph of wonderful teamwork,” concludes Dhandapani, clearly thrilled with his team’s achievement.