THE EXPANSION OF A BUSTLING AIRPORT CALLS FOR ULTRA-SAFE EXECUTION!
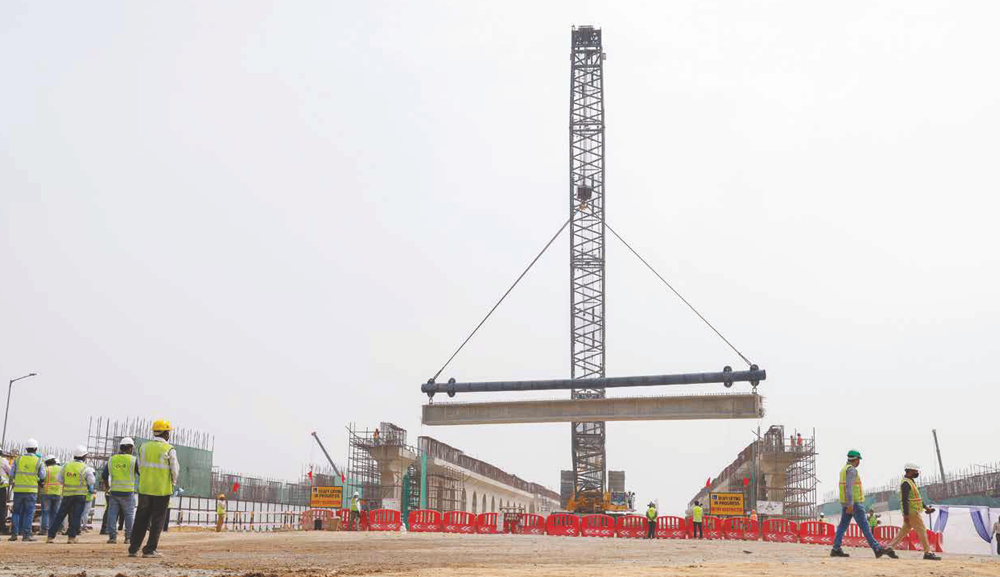
DELHI INTERNATIONAL AIRPORT LIMITED (DIAL)
PHASE 3A PROJECT
New Delhi’s Indira Gandhi International Airport (IGIA) is India’s busiest airport for VVIP, passenger, and cargo traffic, currently the 7th busiest in the world handling nearly 70 million passengers per annum (MPPA), and the under-construction expansion programme will increase its capacity to 100 MPPA. The Phase 3A development project awarded to L&T’s team from TI IC involves detailed design & engineering of the terminal and airside.
A bird’s-eye view of the expansion work
Reconstruction of the Domestic Apron: The existing domestic apron facilitates only remote bussing operations and does not allow for contact stands. On the existing footprint, a new T1 apron is being constructed with 82 Code C and MARS stands and the new T1 terminal. A minimum of 33 apron stands should remain operational during the construction phase.
Runway and Taxiway Works: A new 4th runway will be added to the existing Runway 09-27, which is being refurbished. The system of taxiways will be enhanced with new parallel taxiways to Runways 09-27 and 10-28 along the apron including link taxiways between the runway & parallel taxiways and two isolation bays. Again, a minimum of 3 runways should be operational, with phased closing planned.
Eastern Cross Taxiway (ECT): An iconic 2.5 km long ECT system, first-of-its-kind for India, is being constructed to facilitate traffic flow between the northern and southern airfield facilities, expedite landings and take-offs, reduce taxiing time, and save fuel. To maintain the gradient suitable for taxiing of aircraft over the ECT, a bridge is being constructed on the Central Spine Road and an underpass within the Radisson Road extent.
Landside Works: This includes improvements to accessing T1 Arrival and Departure lounges, widening the Northern Access Road to 2×5 lane configuration, widening the Central Spine Road to 2×6 lane configuration, constructing a new Parallel Access Road of 2×2 lane configuration, and improving the Radisson Road after the Toll Plaza – all to be completed while keeping major road arteries to T3 and T1 intact, thereby inducing multiple stages.
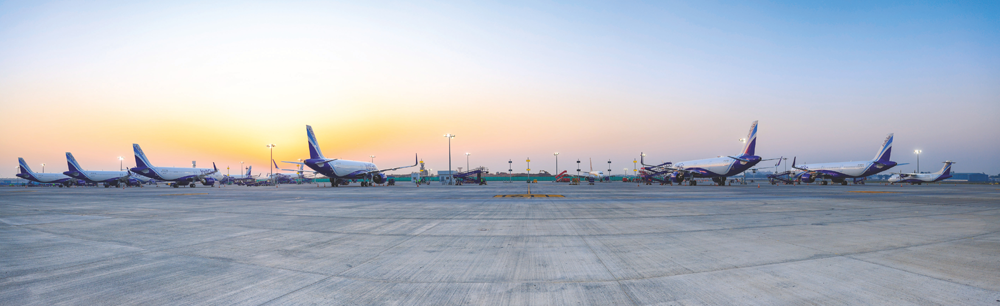
“We are expected to sequence all these various activities with minimal inconvenience to an operational airport and without impairing its capacity,” remarks K V Praveen, Executive Vice President & Head – Delhi International Airport. “Other challenges are frequent VVIP movements and working inside the airside area and terminal buildings while adhering to security and access restrictions to move personnel and construction equipment.” A tall ask, but the team has taken it as a challenge and have won L&T Construction’s Safety Award 2022 in the process.
“We are expected to sequence all these various activities with minimal inconvenience to an operational airport and without impairing its capacity. Other challenges are frequent VVIP movements and working inside the airside area and terminal buildings while adhering to security and access restrictions to move personnel and construction equipment.”
K V Praveen
Head – Delhi International Airport
Piloting through a web of challenges
Unchartered underground utilities, pollution, and proximity to a ‘live’ airport were some of the early challenges for Project Director, Rajesh Kumar Jha, his EHS Head, Chandra Sekhara Rao, and team.
Being a brownfield project, with a web of underground utilities connected directly or indirectly to airport operations, the team carefully worked out a rerouting plan in coordination with various stakeholders and then commenced the critical task of excavation. “We conducted a Ground Penetration Radar (GPR) report of the entire work zone to map all the existing live utilities,” reveals Ranjith Kumar R, Head – Construction & Project Control, “and then superimposed the coordinates of the utilities on a Google Earth map for their real-time identification during excavation.” This ensured least disturbance to the airport’s operations, lesser damage of utilities, and reduced costs.
“We conducted a Ground Penetration Radar (GPR) report of the entire work zone to map all the existing live utilities, and then superimposed the coordinates of the utilities on a Google Earth map for their real-time identification during excavation.”
Ranjith Kumar R
Construction & Project Contro
Constructing in a city that already has an extremely poor Air Quality Index (AQI) called for some strong measures as Deputy General Manager (Civil), Surojit Chatterjee, explains. “Our dust mitigation plan, as per DPCC guidelines and client requirements, were incorporated into method statements and 4 real-time monitoring stations & 2 cloud monitoring stations were installed to measure the ambient air quality levels of PM10 and PM2.5, with weekly revie CPCB/DPCC station’s data.” Other initiatives to control dust were the use of fog canons and rain guns, applying Zyco Bond chemical on access roads, covering stockpiles, and elevated water sprinklers.
“Our dust mitigation plan, as per DPCC guidelines and client requirements, were incorporated into method statements and 4 real-time monitoring stations & 2 cloud monitoring stations were installed to measure the ambient air quality levels of PM10 and PM2.5, with weekly reviews against the nearest CPCB/DPCC station’s data.”
Surojit Chatterjee
Deputy General Manager (Civil)
Head – P&M, P G Aravinda Ghosh’s issue was to operate a hot mix plant at the premises of the IGIA without polluting the air. “We ensured smooth operation of the plant despite GRAP Stage II & III impositions of stringent dust control measures and installed two ambient monitoring stacks for the first time in our BU (at bitumen tank & plant) to measure emissions in real time,” he informs. Both the stacks were synchronized with DPCC servers for monitoring & record purposes. Using PNG instead of convention fuel like furnace oil and activating charcoal stakes at bitumen storage tanks to avoid blue smoke emission also helped to keep air quality levels within permissible limits.
“We ensured smooth operation of the plant despite GRAP Stage II & III impositions of stringent dust control measures and installed two ambient monitoring stacks for the first time in our BU (at bitumen tank & plant) to measure emissions in
real time.”
P G Aravinda Ghosh
Head – P&M
Traffic management when constructing in an operational airport was critical, for which a dedicated traffic management team was entrusted with carrying out the erection of girders for the ECT Spine Bridge, which involved shifting 29 m long and 90 MT heavy PSC girders, and a whopping 590 girders were erected without any incident. “We had multiple reviews of design, work methodology, and risk assessment with the EDRC, CMPC, client, and execution teams, with thorough third-party tests of all equipment, and deployed trained and competent rigging gangs after strict assessments and workshops,” shares Deputy General Manager (Civil), Sreejith G. The entire activity was as per a comprehensive EHS management plan developed in consultation with the client, city traffic inspector, and associated stakeholders, adds Assistant Manager (EHS), Sudarsan R.
“We had multiple reviews of design, work methodology, and risk assessment with the EDRC, CMPC, client, and execution teams, with thorough third-party tests of all equipment, and deployed trained and competent rigging gangs after strict assessments and workshops.”
Sreejith G
Deputy General Manager (Civil)
With all the execution taking place in the manoeuvring area of aircraft at India’s busiest airport, the team had to ensure that they caused no hindrance to the movement of aircraft, ground service equipment, and other heavy equipment. “We stringently implemented our action plan to efficiently manage FODs and safe taxiway crossings by deploying escort vehicles and adhering to the airport operation norms under the guidance of the civil aviation regulations (CAR compliance),” points out Project Manager, Sanjib Kumar Chakraborthy.
“We stringently implemented our action plan to efficiently manage FODs and safe taxiway crossings by deploying escort vehicles and adhering to the airport operation norms under the guidance of the civil aviation regulations (CAR compliance).”
Sanjib Kumar Chakraborthy
Project Manager
Working as close as 45 m to the operational area, coupled with low visibility on foggy days and high wind thrusts in the airside, added to the degree of difficulty. All workmen and employees were given mandatory airside safety training and airside stakeholder meetings for interface and coordination. ‘’Training by airside safety experts ensured that every project member was aware of the risks involved and equipped to execute work safely,’’ shares Pankaj Kumar, Assistant Manager (EHS).
The EHS mantra for success
Clocking nearly 41 million safe manhours is no mean feat in such a highly sensitive environment, which reflects the preparedness of Chandra and his team. “We believe that safety is everyone’s responsibility, and here at DIAL, everybody contributed persistently with the same spirit and enthusiasm throughout the tenure,” he remarks. “The collaboration and synergy among the departments and proactive approach are key to the successful implementation of safety culture across work locations.” Behaviour-based safety training helped to boost workmen morale and subsequent productivity, while industry-class workmen welfare and accommodation helped to retain them during tough pandemic times and made them feel safe and secure. EHS was always first in the agenda of every meeting and business affairs, including progress reports to the client, monthly progress review meetings (PRMs), and meetings with subcontractors, among others.
“We believe that safety is everyone’s responsibility, and here at DIAL, everybody contributed persistently with the same spirit and enthusiasm throughout the tenure. The collaboration andsynergy among the departments and proactive approach are key to the successful implementation of safety culture across work locations.”
A Chandra Sekhara Rao
Head – EHS
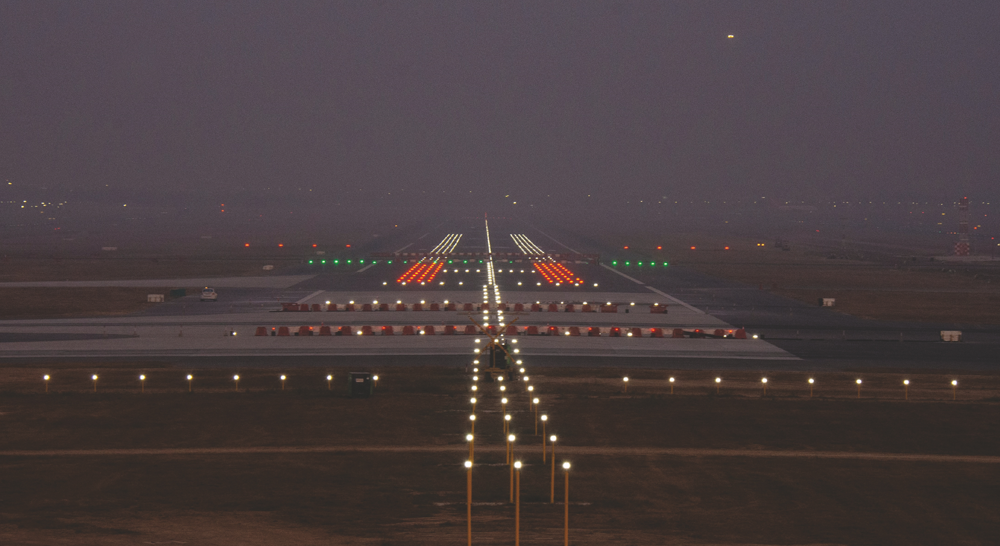
Rajesh was crystal clear in all his communications and decisions that safety & quality could not be compromised at any point, under any circumstance. “Ours is a top-bottom driven system, and the TFL and project management teams were focused to execute the job adhering to our commitments,” he observes, “with proactive planning, training, and complete involvement of each personnel.” Every member actively participated to identify hazards & risks and implemented SOPs to achieve the EHS goal of Mission Zero Harm following a ‘Safety First’ mantra.
“Ours is a top-bottom driven system, and the TFL and project management teams were focused to execute the job adhering to our commitments with proactive planning, training, and complete involvement of each personnel.”
Rajesh K Jha
Project Director
Safety measures were reviewed with all stakeholders at pre-job EHS risk assessment workshops to develop hazard identification and risk assessments, safe work methods for every activity, and control measures implemented through 3,000+ training sessions and over 92,000 training manhours. A Project EHS Committee with representatives from all sections, chaired by Rajesh with Chandra as Secretary, discussed, promoted, reviewed, and tracked EHS in consultation with stakeholders on any external or internal issues. “We have sincerely worked on root causes of violations and acted on specific inputs to initiate training programmes as per the specific needs,” shares Assistant Manager (EHS), Yerawar Shivanand S. “The DIAL operational and EHS teams worked together to create awareness and enhance skills and behavioural aspects to meet our objectives.”
Head – Planning, Somen Chakraborty, mentions a pocket EHS Handbook to create awareness on brownfield airport projects. “Robotic flagmen eliminated workforce engagement on ‘live’ roads; we had ceiling-mounted fire extinguishers, ‘fire balls’ to reduce human intervention and maintenance, introduced a gas manifold system, and adopted the ‘5S’ culture; our ‘Don’t Walk By’ initiative helped create a positive EHS culture among the workforce.”
“Robotic flagmen eliminated workforce engagement on ‘live’ roads; we had ceiling-mounted fire extinguishers, ‘fire balls’ to reduce human intervention and maintenance, introduced a gas manifold system, and adopted the ‘5S’ culture; our ‘Don’t Walk By’ initiative helped create a positive EHS culture among the workforce.”
Somen Chakraborty
Head – Planning
Digitalization driving EHS efficiency
Digitalization helped to significantly control project risk levels to implement and review EHS systems through various EHS digital modules and mobile applications, with a unique VR model that merits special mention. “Developed and reviewed by senior management for its extensive use at brownfield airport projects, the VR module has helped us for Quality training, simulating a real-time experience of an operational airport and its safe measures in an easy and well-defined manner, to prevent idling of resources and drastically reduce airside safety deviations,” remarks Rajesh. The SHEILD and IB4U apps are the lead drivers for EHS inspections, observations, and tracking of EHS records, while GPS technology facilitates live location tracking, speed monitoring, and tracking the status of operations to further reduce airside deviations.
Chandra is delighted with the UNIQUO app that they developed with a vendor to trace relevant test certificates and keep track of inspected tools and tackles. “UNIQUO alerts us about certifications expiring in the next 30 days, and we can request for TPI certification in advance to avoid delays in equipment commissioning,” he informs. The inspection records are accessible to every individual associated with the activity, and the certificate can be produced instantly.
With the engagement of various stakeholders critical to execute a brownfield job, it was important to maintain information flow for quick redressal of grievances, for which the team set up a Central Control Room (CCR) that
helps with
- 24-hour live monitoring through 21 PTZ cameras and 200+ CCTV cameras,
- single-point contact for any emergency (medical, security, utilities, etc.),
- minimal emergency response time, and
- dedicated response teams.
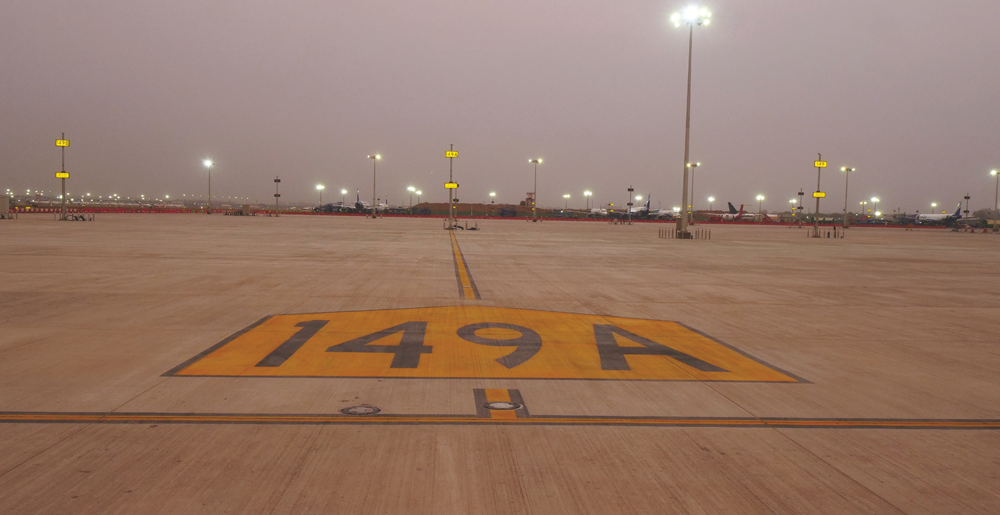
Driving sustainability at DIAL
Sustainability was high on the team’s agenda with their work procedures and methodologies aligned accordingly, and key personnel were trained to effectively implement and track ESG parameters. “We have reduced waste and energy consumption wherever possible and protected the natural environment like flora and fauna around the site premises,” comments Joint General Manager, Shreebanta Kumar Das.
A 700 KLD sewage treatment plant recycles wastewater, washroom taps are fitted with sensors, and a dedicated maintenance team checks for water leakage in all areas. Around 500 LED lights illuminate the site, and solar light masts provide lighting for work at night. Waste material is recycled as much as possible to reduce the amount of solid waste. ‘’C&D waste (milling material & dismantled PQC) is crushed and reused for sub-grade works,’’ claims Manoj Das, DGM – QMCC. The tested concrete cubes are used as pavement blocks, and kerb stones for temporary diversions and gardening purposes.
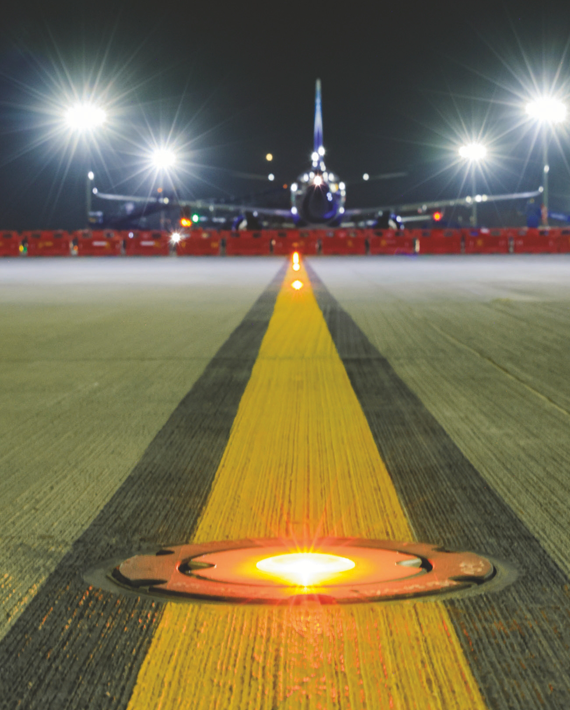
Efforts well rewarded
The project team’s efforts have won them several accolades, both nationally and in the international arena. “We secured the Safety Award across L&T Construction all thanks to our cumulative efforts!” Chandra exclaims with evident pride, adding that he felt on top of the world when receiving the award from SNS. “We won the Sarvashrestra Suraksha Puraskar Award (Gold), the highest safety award in the country, from the National Safety Council of India in the ‘Construction’ category, and have been recognised and honoured from reputed international organisations like the RoSPA Gold and the British Safety Council award (Distinction grade) for the past three consecutive years, CIDC Achievement Award for EHS Implementation, and SEA Awards (Gold) for Innovation in Occupational Safety & Health, which are all more feathers to our cap.”
Other important safety recognitions include the Chairman’s Commendation and Achievement Award for Health, Safety, and Environment Performance from the Construction Industry Development Council (CIDC) in 2021; Gold Award for Innovation in Occupational Safety & Health, Silver Award for Establishing Excellent Occupational Safety & Health, and Bronze Award for Individual Contribution in Occupationa Safety & Health, all from the Safety Engineers Association of India; and Winner – LIFE Awards among TI IC projects in consecutive years 2020 and 2021.
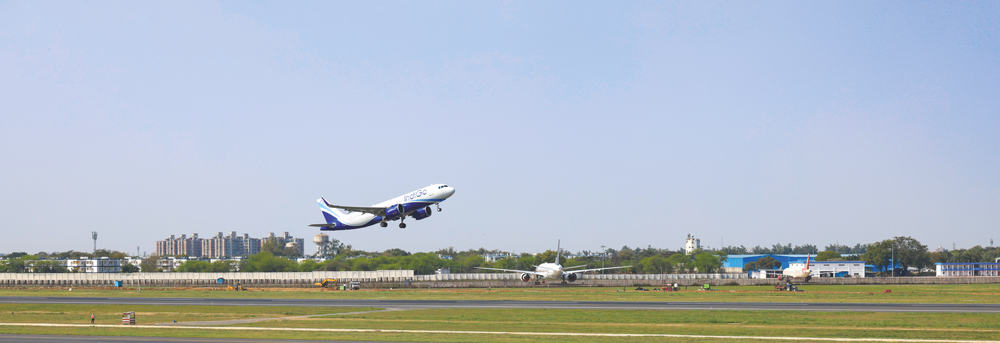
“Topping them all is the Safety Award 2022 that we received from SNS Sir,” sums up Rajesh. “Our top management drives the EHS implementation by demonstrating it through their actions; every meeting starts with a review of the EHS performance, and they participate in EHS walk-downs and promotional events, inspire the workforce with motivational awards, and more.” No wonder the DIAL Phase 3A Project has been a RUNAWAY Safety success!