THE FIRST PARABOLIC ASPHALT HIGH-SPEED TEST TRACK BUILT WITH A UNIQUE 44-DEGREE CURVATURE!
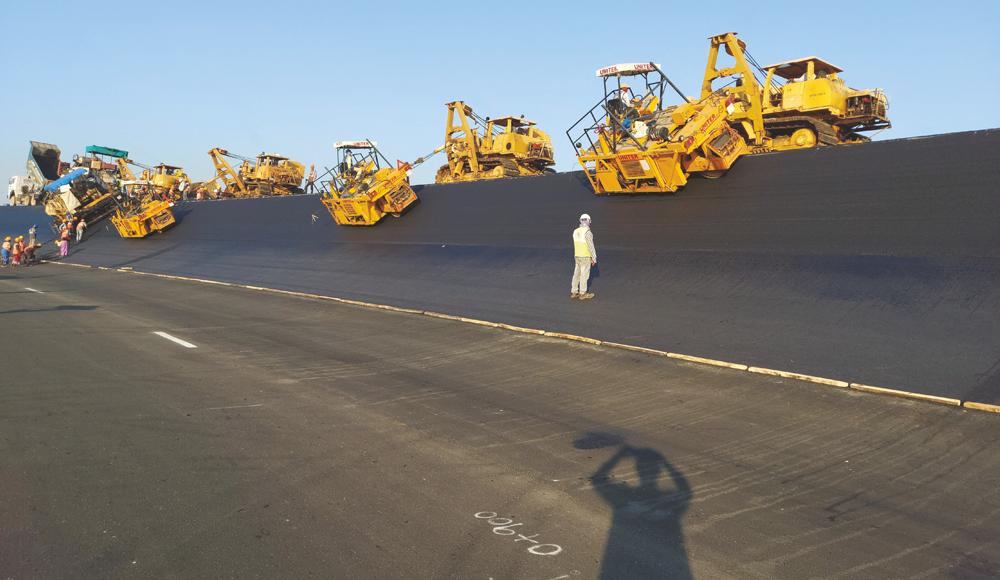
MAHINDRA SUV PROVING TRACK PROJECT
Built over 454 acres at Cheyyar SIPCOT Industrial Area, near Chennai, the spectacular Mahindra SUV Proving Track project offers a variety of environments to carry out vehicle and system tests efficiently and under any condition. There are 16 test tracks with a total length of 44.56 km custom-built for all speeds, every incline, simulating a variety of terrains with 58 specialized surfaces for scientific experimenting and testing of a range of automotive products. And it all started with a tract of barren land when the project kickstarted in May 2018.
Conforming to stringent surface tolerances using inhouse indigenous technology, satisfying international Safety and Quality Standards and exemplifying the spirit of ‘Make in India’, the B&F project team led by Project Manager, Raghuraman Sadagopan, has set a new benchmark for the automobile industry and for the client Mahindra & Mahindra (M&M) who are, needless to say, delighted that L&T has been able to deliver such a complex project on time in
October 2022.
“The challenges were one notch higher here with an extremely steep surface to be paved and compacted, with the top lane of the Parabolic Test Track designed for cruising speeds of 220 Kmph and surface tolerance of +/- 3 mm in both directions. This project was a triumph of teamwork where we raced against time, overcoming some unique challenges to deliver.”
Raghuraman Sadagopan
Project Manager
The project was awarded on the strength of L&T having previously built Asia’s largest 11.28 km long and 16 m wide high-speed track with 34-degree parabola for client, NATRiP Implementation Society, so the project team had a huge reputation to protect. “The challenges were one notch higher here with an extremely steep surface to be paved and compacted, with the top lane of the Parabolic Test Track designed for cruising speeds of 220 Kmph and surface tolerance of +/- 3 mm in both directions,” shares Raghuraman, etching the contours of the complexity of the project. His eyes fall momentarily on the Timely Delivery award prominently displayed on his desk and adds, “This project was a triumph of teamwork where we raced against time, overcoming some unique challenges to deliver.”
Superseding challenges with innovative solutions
With such a tough task, the team evolved means and methods to stay on top of things with phase and weekly planning sessions, maintaining manpower and machinery requirements, immediately tracking, addressing, and resolving issues. They developed and implemented the construction methodology for laying the high-speed parabolic curve, performance track which was critical in handing over the High-Speed test Track. Work started in earnest only after all the design data had been checked and confirmed by the client.
“We started activity by preparing the subgrade with GCS technology on the Trimble base,” mentions Assistant Construction Manager (Civil), Jhulan Chakraborty. “GCS technology is purely GPS base technology that gives a smoother finish and greater accuracy. For subgrade work, we deployed two modified excavators, connected to a GPS base station to monitor the grading and leveling of the parabola surface without any deviations.” The parabolic curves on both sides of the oval circuit form a super elevation of 44.6 degrees with the transition curves stretching 0° to 44° in 170 m and 44° to 0° in 170 m making it one of the world’s highest inclinations.
“We started activity by preparing the subgrade with GCS technology on the Trimble base. GCS technology is purely GPS base technology that gives a smoother finish and greater accuracy. For subgrade work, we deployed two modified excavators, connected to a GPS base station to monitor the grading and leveling of the parabola surface without any deviations.”
Jhulan Chakraborty
Assistant Construction Manager (Civil)
“The test track was a proving ground for our engineers too,” shares Raghuraman for paving and compacting a steep slope was extremely tough. “To overcome these challenges and achieve several other demanding specifications, we carried out several studies and design mix trials at site to arrive at an optimum mix.”
With the help of the in-house Construction Methods & Planning Cell and P&M teams, a customized digital paver, the Segmented Steel Drum Roller & Pneumatic Tyre Roller, were developed. A customized system held the paver and rollers, banked at 44 degrees, to achieve the desired results.
As per contract, the team were to excavate 20,000 cum hard rock in the prescribed timeline. However, during execution, the team encountered 60,000 cum of it on braking the surface to accelerate the durability tracks that were critical to the project. Additional resources and crashing subsequent special surfaces saved the day. Anticipating the risk of parabola asphalt paving during the tendering stage, the contract team collaborated with the site execution team to redesign the mini parabola with a 33” slope in the performance track, to accommodate the parabola portion.
The team learned, unlearned, and developed inhouse technologies for the specialized flexible steel drum roller, pneumatic tyre roller and curved parabola paver which are digitally controlled machinery to ensure compaction of asphalt in the parabola of 0* to 44* angles that varies every meter in the transition portion. Effective use of frontier technologies helped to ensure workmen safety, improve productivity, optimally organize activities and avoid manual errors and reworks in making the parabola profile.
“We introduced advance technology in the form of a non-nuclear asphalt density gauge that tests the density of asphalt in real time saving hugely on time and cost,” shares Manager (QA/QC), M James Iruthayaraja.
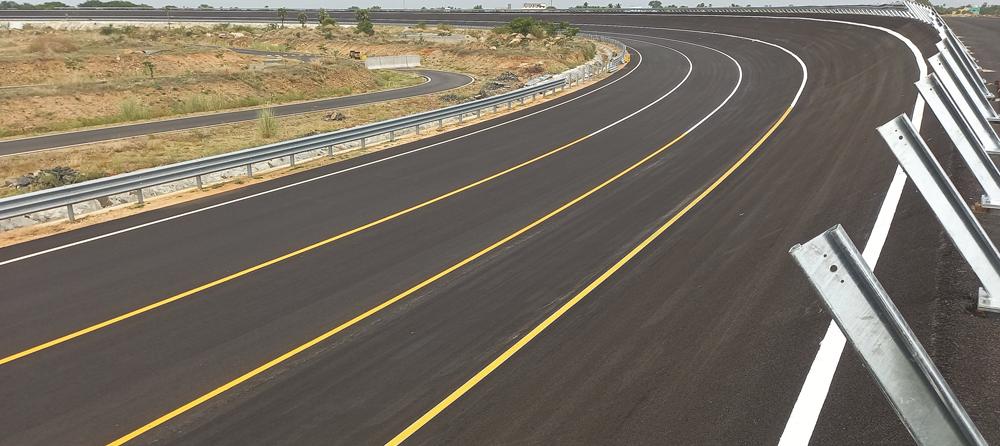
Lean Construction leading the way
To maintain stringent timelines, the team used Lean Construction tools that helped delivery systems and processes by minimizing wastes, increasing productivity, health, and safety.
“We decided to use pull planning, a technique used as part of the Last Planner System, to develop a coordinated plan for the parabolic execution phase resulting in a higher level of integration, coordination, and efficiency,” shares Planning Manager, Sriram S. “This was a team-wide commitment,” he beams.
“We decided to use pull planning, a technique used as part of the Last Planner System, to develop a coordinated plan for the parabolic execution phase resulting in a higher level of integration, coordination, and efficiency.”
Sriram S
Planning Manager
Planning to the last detail was key to project success. Throughout the execution phase, Heads of all major disciplines met every week to assess upcoming deadlines and develop detailed deliverables for the approaching milestones. Eventually, the team became so efficient that 120-minute weekly check-ins were reduced to just 40 minutes. Asphalt laying in lane four was scaled down from 2 days paving to a day through a collaborative team approach.
The track features many purpose-built sections that can be used to test out the various parameters of vehicles.
- A dynamic platform of 1.5 km asphalt with 140 m radius is for studying the response of a vehicle in various dynamic situations, to assess the influence of a component or a subsystem on the overall vehicle ride, handling, and performance.
- Braking tracks to perform braking tests on various surfaces for homologation. These surfaces have several friction coefficients µ range 0.15 – 0.9 with various surfaces like basalt, ceramic, high friction asphalt, polished concrete, ABS tests, high speed brake tests, tire performance evaluation, and more.
- Accelerated fatigue track has a variety of surfaces from low to high severity, designed to accelerate ageing of a vehicle’s structure and components. There are 28 different profiles like Belgium Pave, potholes, Long Wave, Twist Track, Washboard Road, Cobble Stone, Corrugated & Herring Bone, etc. that enable manufacturers to decide their own course of durability. Another Accelerated Fatigue Track of 4.5 km with special PQC Surfaces is for testing trucks, SUVs, cars.
- Belgium Pave track constructed using hardest granite stone having high compressive strength.
- Potholes are a 300 m long and 4 m wide concrete stretch with a pattern of depths varying from 10 mm to 190 mm.
- Long Wave Pitching consists of 200 m long and 3.5 m wide concrete pavements with uniform patterns 200 m long, 3.5 m wide, 7.5 m pitch & height of waves 100 mm.
- High Frequency is a 100 m long and 3.5 m wide concrete pavement with variable dimension slots with MS angle of size (65x45x6 mm) fixed.
- Twist Surface constructed with M 40 PP fiber of prismoids shape.
- Cobble Stone for Car / Truck 600 M X 4 m Stones placed in unique patterns and inserted to a depth of 30-33% of its height.
- Herring Bone Pitching consists of 100 m long and 3.5 m wide M 40 pp fiber concrete pavement with uniform pattern: 200 m long, 3.5 m wide, 7.5 m pitch of wave, 50 mm height of waves.
- Oval shaped concrete track for tractor performance and autonomous driving test.
- Water Test facilities: Water wade & saltwater wade, rain simulation and water splash to simulate different tropical conditions.
Tracks to be added:
- Performance track of 4 km asphalt with parabolic angle 33 degrees is being constructed with +/- 3 mm surface tolerance for testing straight-line performance, cornering/handling.
- 4 X 4 adventure track to testing off-road capability, design build with 16+ adventure events.
- Oval shaped concrete track for tractor performance and autonomous driving test.
- General highway track of 8 km with abstruse surfaces like Manhole Surface, Wavy Surface, Railway Crossing Surface, Dynamic Tilt Surface, Ground Clearance Surface, ABS Check Surface, Misuse Surface. Asphalt patches, rough surface.
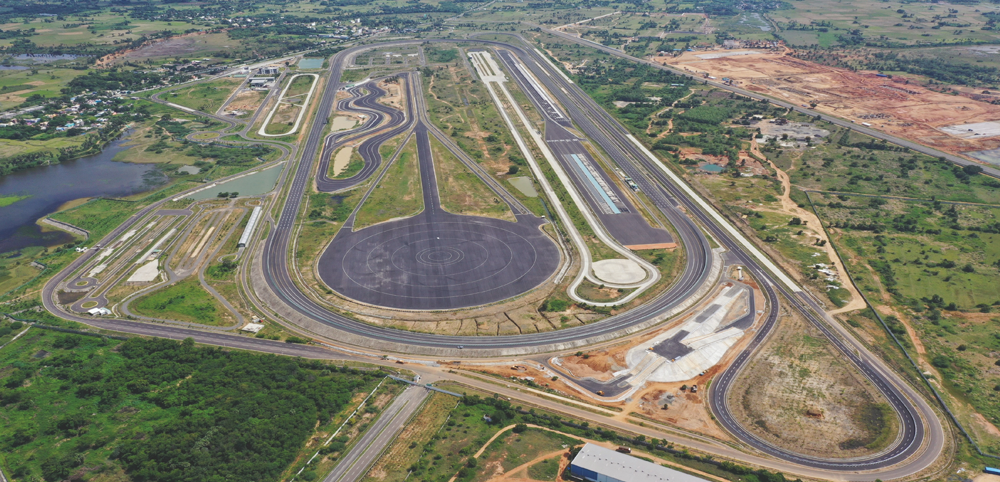
On the right track through digital solutions
“The entire track profile was redeveloped in Autocad and the equipment movement was simulated at all the curve profiles to determine the holding methodology,” points out Ashok Kumar Pappala, Construction Manager (Civil), CMPC for B&F HRC-SBG. Flagging off the vital contribution of Madhu Anand (Head CMPC, B&F- HRC), Ashok remarks, “Without digital support it would have been extremely difficult to manually ascertain the vehicle inclination and the holding length & hydraulic jack pressure to be maintained.”
Digital technologies enabled better collaboration, greater control of the value chain, and a shift toward more datadriven decision making. A Grade Control System (GCS) on excavators was implemented for slope trimming in the parabolic portion, precisely positioned 3D teeth of the bucket to perform complex tasks with precision and simplify finishing slopes with accurate 3D positioning. Even site inspections were conducted in the digital mode saving time for documentation and approvals.
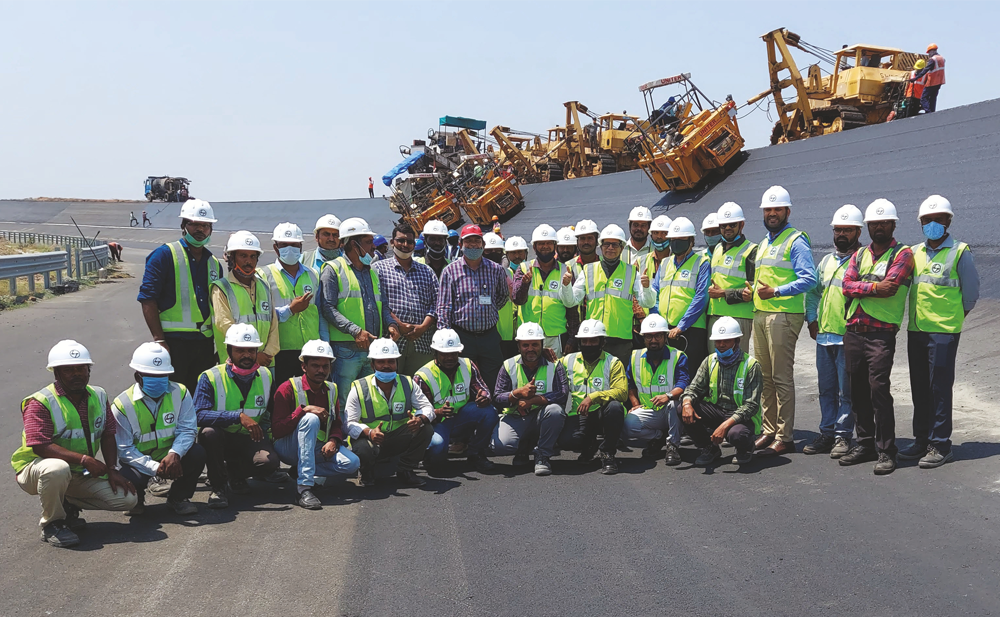
“The entire track profile was redeveloped in Autocad and the equipment movement was simulated at all the curve profiles to determine the holding methodology. Without digital support it would have been extremely difficult to manually ascertain the vehicle inclination and the holding length & hydraulic jack pressure to be maintained.”
Ashok Kumar Pappala
Construction Manager (Civil)
“We drove policy into practice, creating digital workflows, compiling lessons learned, auditing, tracking and keeping track of key performance indicators,” shares Manager (QA/QC), M James Iruthayaraja.
“We drove policy into practice, creating digital workflows, compiling lessons learned, auditing, tracking and keeping track of key performance indicators.”
M James Iruthayaraja
Manager (QA/QC)
“We created a collaborative environment for everyone to blend, identify and solve problems together that saved money, time, reduced waste and redundancy,” remarks Sriram. “In fact, the pull planning promoted the concept of
‘we’ instead of ‘me.’ ”
Awards & recognition
In addition to winning the internal Timely Delivery Award, the project has won the ACI Excellence in Concrete Construction at the ICACI Excellence in Concrete Construction Awards: 2022 and the First Place in India’s Chapter of ACI Excellence in Concrete Construction Awards in the Concrete Flatwork category. Another feather was the First Place (Global Level) at The ACI Excellence in Concrete Construction Awards 2022 for flat concrete, held in the US.
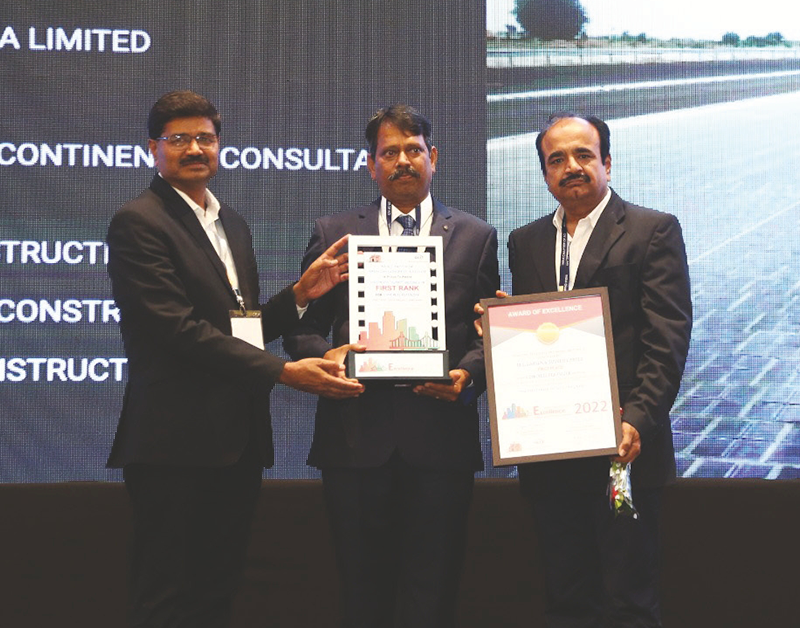
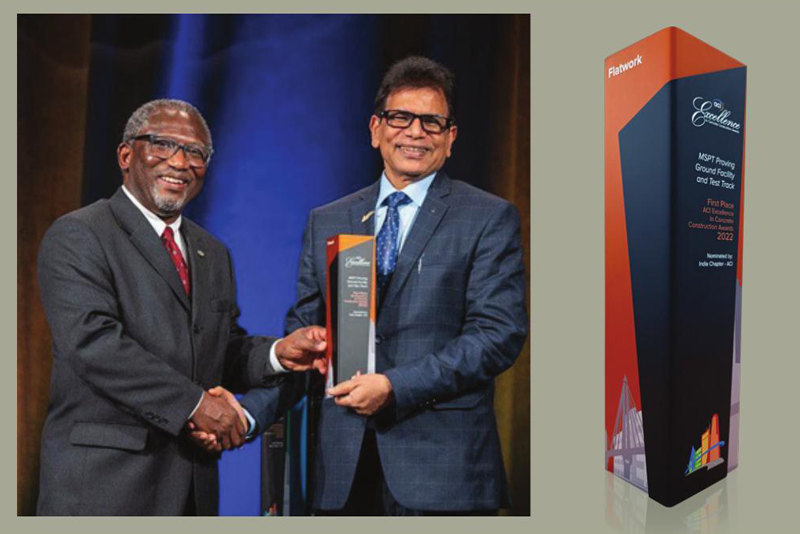
Raghuraman Sadagopan sums up with a smile “We have now earned the distinction of becoming India’s first construction organization with the capability to build a parabolic test track and what’s more, it has been constructed entirely with inhouse talent, expertise and equipment.”