Strictly following EHS protocols
every step of the way
The Ad Dakhiliyah Water Transmission Project Phase II, a one-of-its-kind project for WET IC for the Oman Water and Wastewater Services Company, is to construct a water transmission pipeline (carbon steel pipes of up to 1,700 mm diameter, 145 km long & ductile iron pipes of up to 700 mm diameter, 28 km long), 10 Glass Fused Steel (GFS) tanks of up to 12,500 cum. capacity (total capacity of 90,000 cum.), 4 welded steel storage reservoirs each of 87.5 million litres capacity with dimensions of 93.4 m dia., 13.5 m shell height, & 33 m, the largest in Oman, with a total capacity of 350,000 cum., new pump stations and equalizing storage, integrating new reservoirs and pumping stations, and other associated civil, electrical, mechanical, SCADA, and instrumentation and external power supply work as necessary.
Lifting with care & precision
The construction of the 10 state-of-theart balancing reservoirs to store water in each pumping station was built with GFS, a premium next-generation technology designed for longterm performance with minimum maintenance. GFS has the strength of a steel plate, the corrosive resistance of glass and is excellent in harsh environments. EHS control measures were infused into the activity right from the planning stage, with method statements and risk assessments prepared by considering every major and minor task.
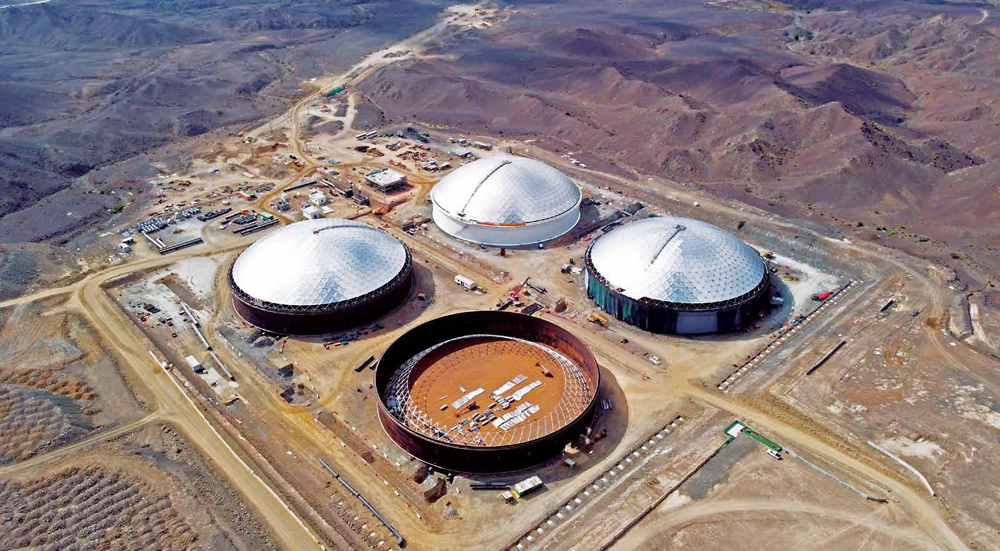
Steel tanks with Aluminium Dome Roof
The tank shells and aluminium dome roofs were first assembled at site and the top two tank shells assembled one above another on the foundation, with a jack system lifting the rings to a height of 1.3 m to make room for the third shell. The challenging lifts were carried out in 2 stages using 61 hydraulic telescopic jacks of 3.5-ton capacity and closely monitored to ensure even lifting. “Site-specific SOPs, risk assessment, and the lifting plan were prepared and approved by a competent person, and all lifting equipment and accessories were inspected daily,” informs EHS Manager Unnikrishnan. For stable lifting operations, the tank remained fixed to the jacks, and the jacks in turn secured to the concrete base.
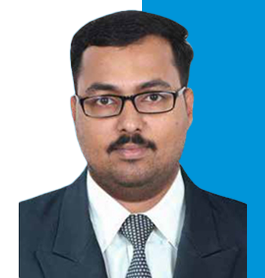
Site-specific SOPs, risk assessment, and the lifting plan were prepared and approved by a competent person, and all lifting equipment and accessories were inspected daily.
Unnikrishnan
EHS Manager
After constructing the two tank shells, the assembly of the Aluminium Dome Roof (ADR) commenced, starting with handling, storage, shifting into the tank, and assembly of the components. “Material handling hazards were controlled through toolbox meetings and selecting certified lifting equipment as per the lifting plan,” adds Balasubramaniam Kamaraj, EHSO. Since the assembly included many components like hub, strut, strut cap and panels, a unique procedure was followed wherein each hub, strut, strut cap, and panel have their own written and colour codes to indicate the exact position (Dome Codes) for perfect fitment at site. During the toolbox talk, the site engineer was explained the importance of positioning the material in the correct position.
Working safely at height: During the erection of the ADR shoes, working at height was the major hazard. Shahid Ali, Safety Officer, explains that every manlift was inspected and approved by the P&M engineer, and if work was happening above 1.8 metres, all the workmen and operators in the manlift were attached to full body harnesses with short lanyard type to arrest a fall if anyone overreached from the manlift work platform. Apart from activityspecific training, workmen without height pass were not allowed inside the work area. When moving the manlift, materials were always secured to avoid movement or falling off.
“Work-at-height safety requirements were ensured through workmen EHS inductions, medical checkups, and skill pass procedures,” says Chandrasekar Kulkarni, Head – EHS, Water International BU. A robust access control system restricted all unauthorized entry, and no work was allowed without online safe execution card & permit to work. When working at height, it was mandatory to pass the height test.
Work-at-height safety requirements were ensured through workmen EHS inductions, medical check-ups, and skill pass procedures.
Chandrasekar Kulkarni
Head – EHS, Water International BU
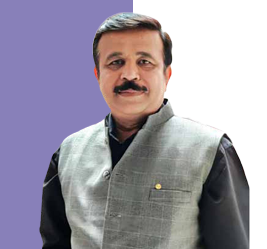
Battling windy conditions: Wind was the primary hazard when installing the aluminium panels as it increased the risk of working at height. Excessive wind could easily damage the panels and imperil the personnel working on the dome structure. Since the panels were not strong enough to support a person’s weight if not secured to the strut with all three corresponding clamp bars, only experienced workmen were allowed to work when the panels were not fully secured, equipped with a centre lifeline hook serving as an anchor point and a safety lifeline using a rope grab fall arrestor. An anti-slip walkway was also installed on the ADR panel to avoid slippages, anemometers monitored wind conditions, and activities were suspended in extremely windy conditions. “We conducted mock drills for the crew engaged for the roof panel erection to help them overcome the trauma of falls when suspended at a height,” points out Project Manager Daniel Abraham Thanaraj.
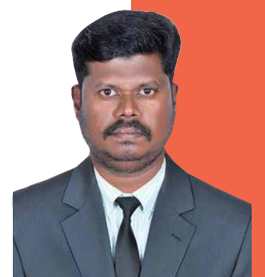
“We conducted mock drills for the crew engaged for the roof panel erection to help them overcome the trauma of falls when suspended at a height.”
Daniel Abraham Thanaraj
Project Manager
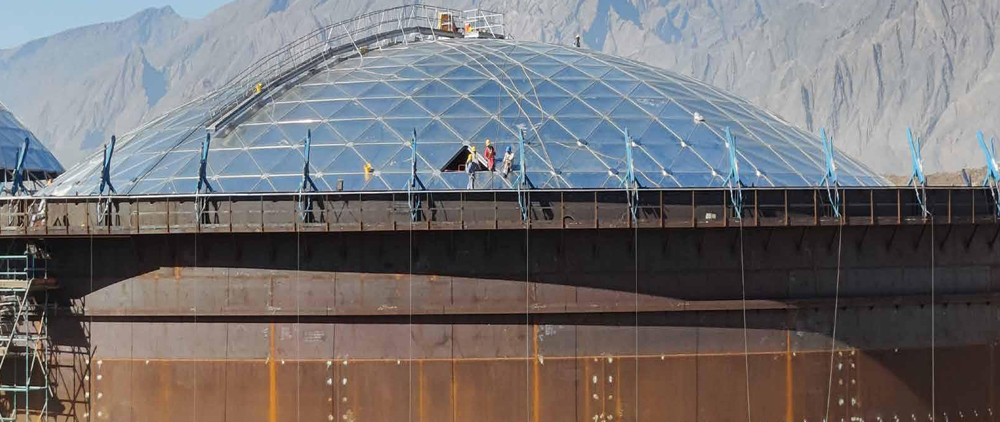
Aluminium Dome Roof erection
The steel tanks were lifted by the jacking method involving several lifting trestles with hydraulic climbing jacks and a common high-pressure pump. After the top second shell course was assembled at a base elevation of 400 mm, the bottom annular plates were hoisted by a mobile crane. Then, the top shell course plates were erected, welded, and raised by jacking. As the upper sub-assembly rested on the jacks, the immediate lower shell plates were assembled over the steel spacer blocks. Lifting and positioning the plates was a critical activity, for which a detailed lifting plan was prepared and all the crew members specially trained. The crane, lifting tools, and tackles were selected as per the lifting plan and executed by a competent team trained and certified in lifting activity.
Lifting and fixing the ADR was another challenging activity. The number and distribution of lifting hoists are detailed in the assembly and lifting plan drawings. Totally 60 pieces of lifting equipment were distributed around the top of the tension rings. The total weight of each aluminium dome assembly was 83 tonnes, with a surface area of 8600 m2. Before the lift, the actual lifting process was discussed at a toolbox meeting along with safe operating procedures, associated hazards, and its control measures by the lifting supervisor and EHS in-charge. The entire lifting process was controlled and executed mechanically, with a certified supervisor controlling the lifting control box and other staff following his instructions, which was successfully completed in an hour’s time.
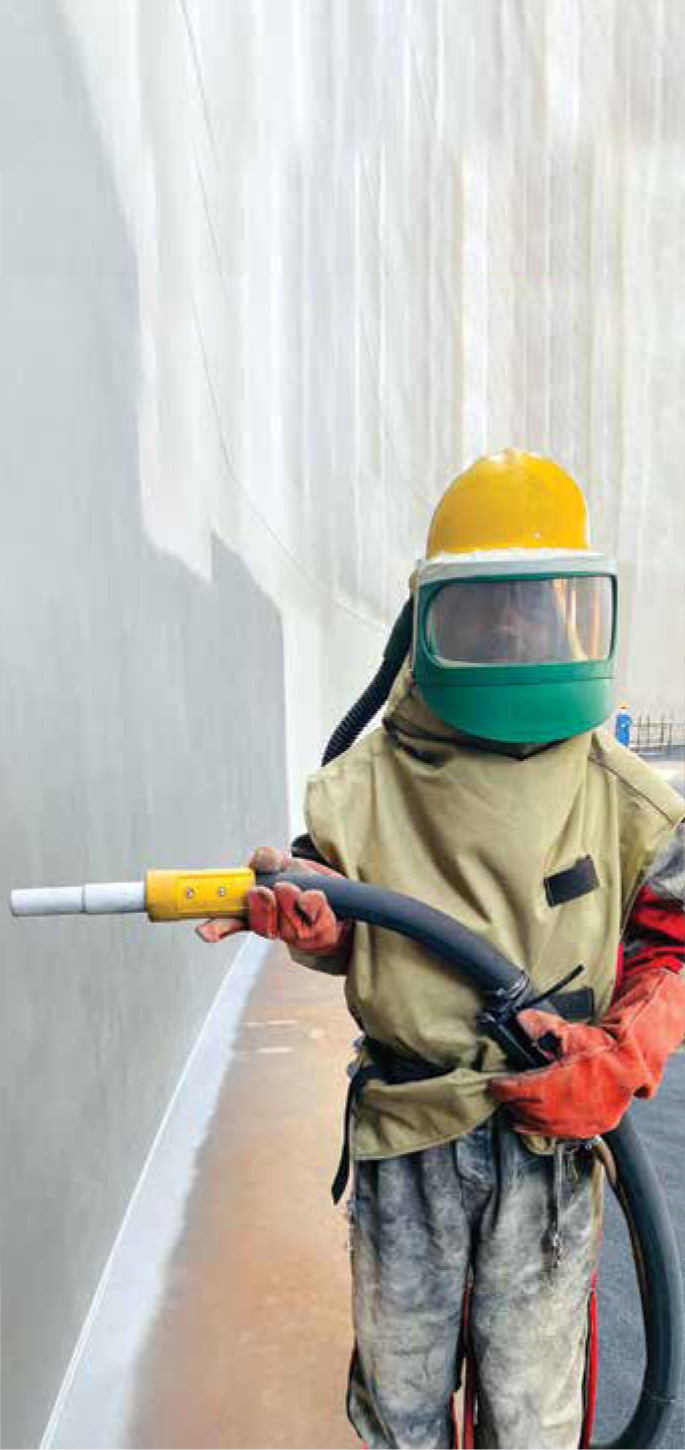
Grit blasting
Keeping safe from electric shocks, welding dust, & fumes
Electrical safety was the prime focus of the EHS team during welding the bottom annular plates and shell plates. A fulltime electrician ensured the electrical connections, cable routing, and other electrical-related activities. RCCBs of
30 mA sensitivity, earthing, industrial distribution boards, and properly sized cables were monitored, welding machines were inspected before each activity, and daily electrical safety inspections were conducted using ViewEHS.
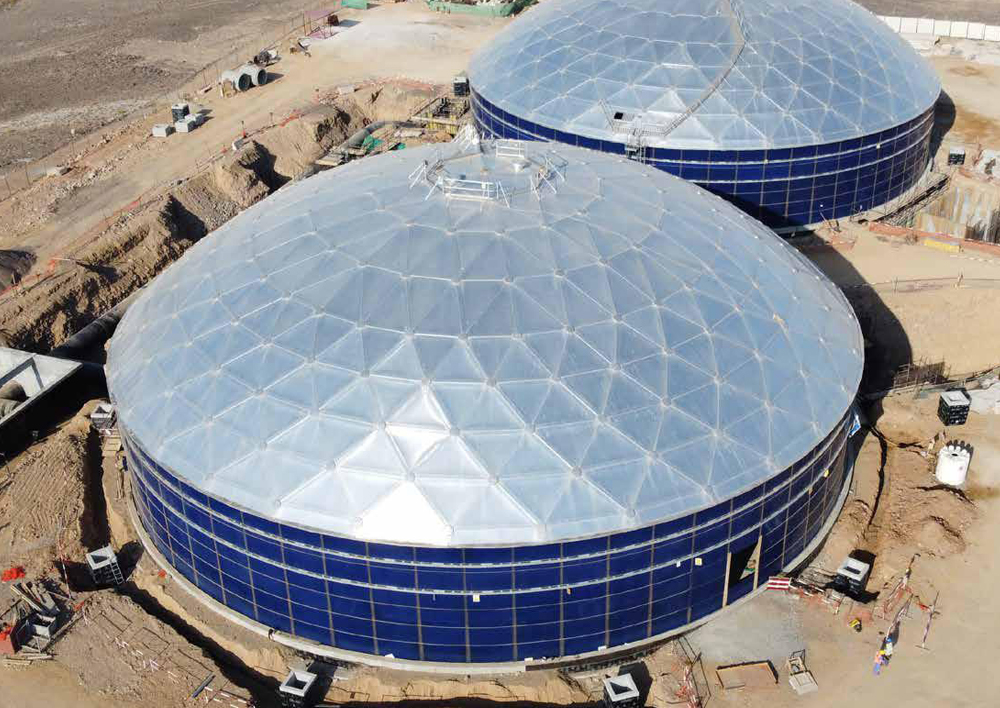
GFS tank with Aluminium Dome Roof
The vertical seams of the lower shell were fitted and welded first by either Shielded Metal Arc Welding (SMAW) or Flux Cored Arc Welding (FCAW) and mechanised Submerged Arc Welding (SAW) for horizontal seams. The welding arrangement mounted on rails was constantly monitored by a supervisor. Mukesh Singh, Deputy Project Director, is glad that the mechanized welding process avoided human intervention and reduced the risk of electrocution and exposure to the welding fumes. Suitable welding PPEs like welding helmets, welding aprons, coverall for arms and legs, leather gloves, and face masks ensured the safety of the workers.
A cup lock scaffolding arrangement was used for the shell assembly, which was inspected by third-party-certified scaffolding inspectors and tagged. All workers had to pass the skill, height, and medical tests, and all the appointed welders were qualified in accordance with the ASME Section IX and API 650.
Blasting with care
Abrasive blasting creates harmful dust; hence, the team selected copper slag as the abrasive material, which is suitable for open blast cleaning. While its low silica content reduced health hazards, its sharp, hard particles give an excellent surface profile. During the manual abrasive blasting of the internal and external tank walls, several precautions were taken to control hazards to ALARP levels:
- Prior to grit blasting, the surface was de-greased, cleaned, and washed to remove oil, grease, soluble chlorides/salts, etc. and dried properly
- Proper earthing was provided for the blasting equipment; conductive hoses were used to prevent buildup of static electricity
- Deadman handles were fixed to blast hoses as close as possible and controlled by hand pressure only; whip checks were connected at the hose connections and joints
- Care was taken to supply the blasting operator’s hood with clean, fresh air fed through an air filter
The automatic blasting machine was used for the bottom plates, completely avoiding manual intervention. This machine has closed-loop air pressure and a blast media flow that avoids dust generation and saves workers from blasting dusts. Again, only experienced, and trained personnel were engaged. When grit blasting the external walls, the whole tank was covered with nets to contain the spread of dust, while the used copper slags were collected and disposed of through an approved waste disposing agency in Oman.
Digital interventions to drive EHS
“ViewEHS helped the site team immensely in their sustained effort to keep EHS performance at a high level,” enthuses K S Sudheesh Kumar, Head – EHS, WET IC, “what with all the permit systems and inspection & observation programmes digitized on the app. EHS data is visually captured on attractive and interactive Power BI dashboards, and the analysis threw up valuable insights for the team to take pragmatic decisions and track SOP compliance across sites,” he explains, adding that the EHS Observation Image Analysis dashboard underpins the EHS observation programme, enabling the team to drill down UA/UB/ UC factors to analyse compliance and non-compliance images of a particular observation.
ViewEHS helped the site team immensely in their sustained effort to keep EHS performance at a high level what with all the permit systems and inspection & observation programmes digitized on the app. EHS data is visually captured on attractive and interactive Power BI dashboards, and the analysis threw up valuable insights for the team to take pragmatic decisions and track SOP compliance across sites.
K S Sudheesh Kumar
Head – EHS, WET IC
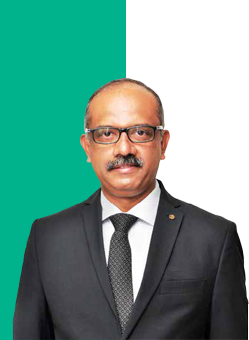
All workmen at site underwent EHS inductions, medical check-ups, and skill pass procedures. A robust access control system restricted all unauthorized entry, and no work was allowed without online safe execution card & permit to work. When working at height, it was mandatory to pass the height test.
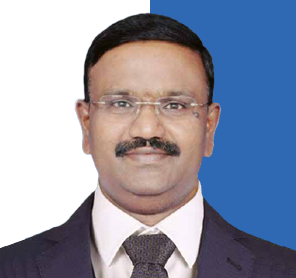
Safety is never an accident but the result of
planned and concerted effort.
K Parasuraman
Project Director
“Safety is never an accident but the result of planned and concerted effort,” signs off Project Director K Parasuraman. The project team at the Ad Dakhiliyah Water Transmission Project have proved that with their impeccable EHS record.