WET IC’s CP-09 Project bags three BSC Awards. All in one year!
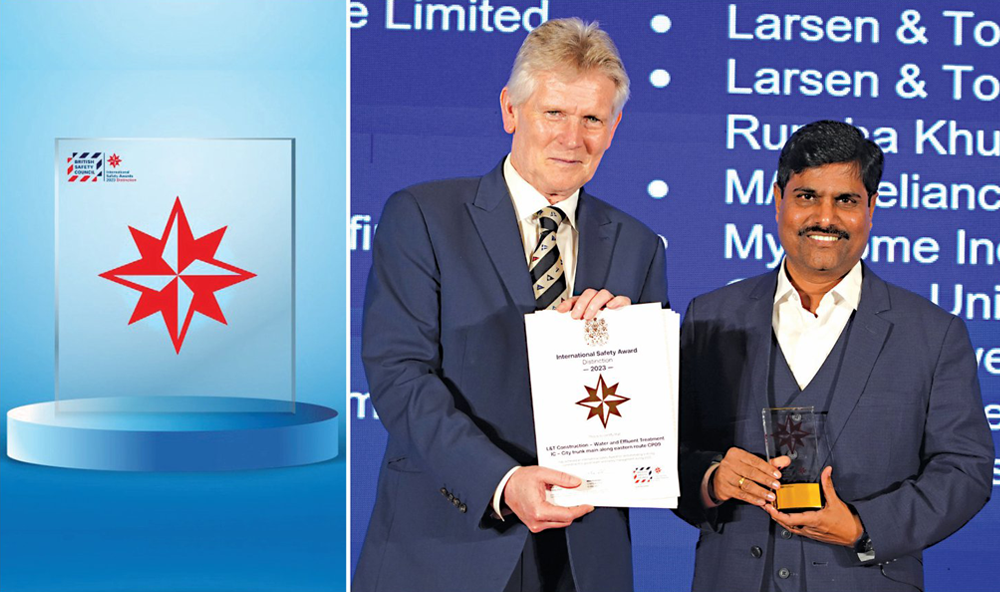
WET IC’s CP-09 Project aims to provide drinking water to about 42 lakh people of Bengaluru, including the residents of Bruhat Bengaluru Mahanagara Palike (BBMP). Funded by the Japan International Cooperation Agency (JICA), under the Bengaluru Water Supply and Sewerage Project (Phase 3-Stage V), the 775 MLD of water will augment the needs of 110 villages, added to the core of Bengaluru city in 2007, through water treatment, pumping facilities, and transmitting to terminal reservoirs in the city.
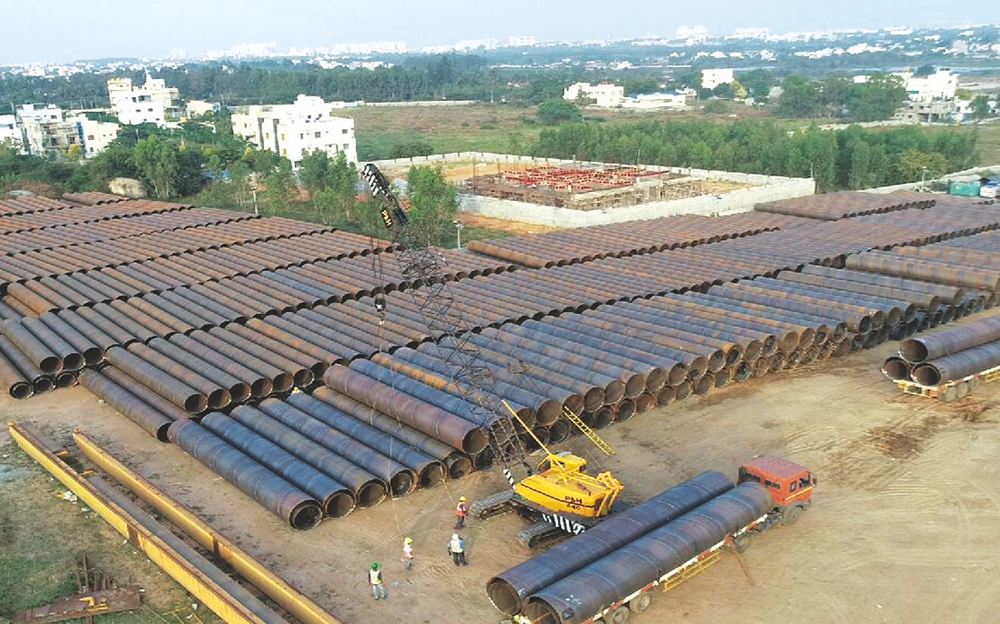
The CP-09 Project received the British Safety Council’s (BSC’s) International Safety Award (ISA) 2023 with ‘Distinction’. A select few high-scoring winners of this award are autoentered into three different categories, and the CP-09 Project won two of these: the Best in Sector Award (under ‘Local Government, Defence and Public Service’) and the India Regional Best in Zone Award (South).
“Winning three BSC Awards in a single year tops an impressive EHS performance,” shares an excited Project Manager, V. Balasubramanian. “And the fact that we have received appreciation from JICA, who are well known for their high safety standards, is truly the icing on the cake.”
Winning three BSC Awards in a single year tops an impressive EHS performance. And the fact that we have received appreciation from JICA, who are well known for their high safety standards, is truly the icing on the cake.
V. Balasubramanian
Project Manager
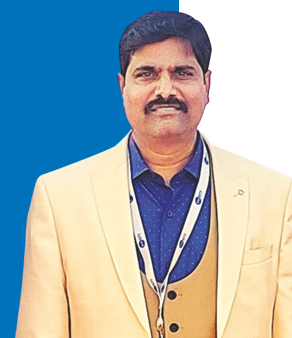
The perils of working in a bustling city
“The nature of work has been tough,” observes V. Guruprasth, EHS In-charge, grimly. “The entire 54 km of MS pipe must be laid in busy, narrow roads, with many underground utilities present. Sub-activities such as MS pipe fabrication, transportation, excavation, and the like are always challenging when executing inside a city.”
The entire 54 km of MS pipe must be laid in busy, narrow roads, with many underground utilities present. Subactivities such as MS pipe fabrication, transportation, excavation, and the like are always challenging when executing inside a city.
V. Guruprasth
Assistant Manager – EHS In-charge
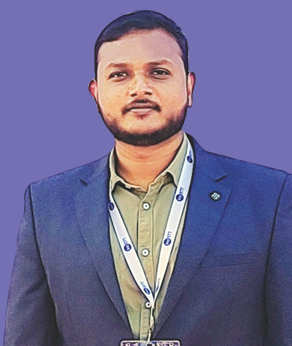
Having identified all possible hazards right at the planning stage, the team arranged for the required resources, permissions, and approvals before start of work. “We were thus able to start and close site activities on time, and safely implemented several engineering control measures to eliminate and reduce hazards,” notes Krishna Madhusudana Rao, Planning Manager.
The effective implementation of our control measures was duly documented, and coupled with our EHS track record from the beginning of the project, we won two of the auto-entry awards as well.
Krishna Madhusudana Rao
Planning Manager
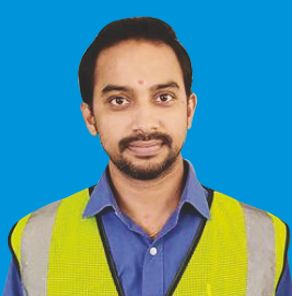
When presenting their case to the BSC for the International Safety Award, the EHS team focused on the hurdles of executing a project in the bustling Bengaluru city. “The effective implementation of our control measures was duly documented, and coupled with our EHS track record from the beginning of the project, we won two of the auto-entry awards as well,” grins Krishna.
Effective control measures for a safer site
Initiating automated MS pipe fabrication within the site premises using hydra cranes obviated the need to transport them and substantially reduced the hazard of material handling. “After shifting the fabricated MS pipes to the pipelaying trenches, we laid them directly from the transportation vehicle, reducing multiple handling of pipes, pipe stacking–related hazards on the road, and movement constraints,” elaborates Krishna.
The project team followed the soil inter-carting method for excavating from the pipeline alignment to the dumping yard, which reduced the soil overburden on trench edges, movement constraints, and traffic issues. “Only CMPC-approved shoring boxes were used in weld pits as an engineering control, and inside bevelling was done for higher-dia MS pipes (2,200 & 1,600 mm) to reduce the welder’s exposure to the hazard,” Guruprasth adds.
“We have implemented all confinedspace safety measures,” notes Rethish B. I., CEHSM. The trial pit and utility detection at the pipeline alignment were completed before excavation began, which avoided the damage of utilities as well as electrical & gas line–related fire hazards. “We used the trenchless technique for pipe-laying in areas with high-tension overhead powerline and busy road crossings.” Backfilling/encasing using crusher dust with water consolidation or concrete avoided soil settlement in main roads, ensuring safe vehicular movement.
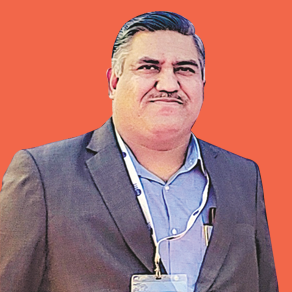
We have implemented all confined-space safety measures. We used the trenchless technique for pipe-laying in areas with high-tension overhead powerline and busy road crossings.
Rethish B. I.
CEHSM
The CP-09 project team has completed all 54 km of the MS pipe fabrication with various dia and 70% of the pipelaying work within city limits. Having already clocked 2 million safe manhours in October 2022, they are on track to safely deliver their promise.