DRIVING QUALITY IN THE SAHARA DESERT
PT&D’s Algeria project bags Quality Award
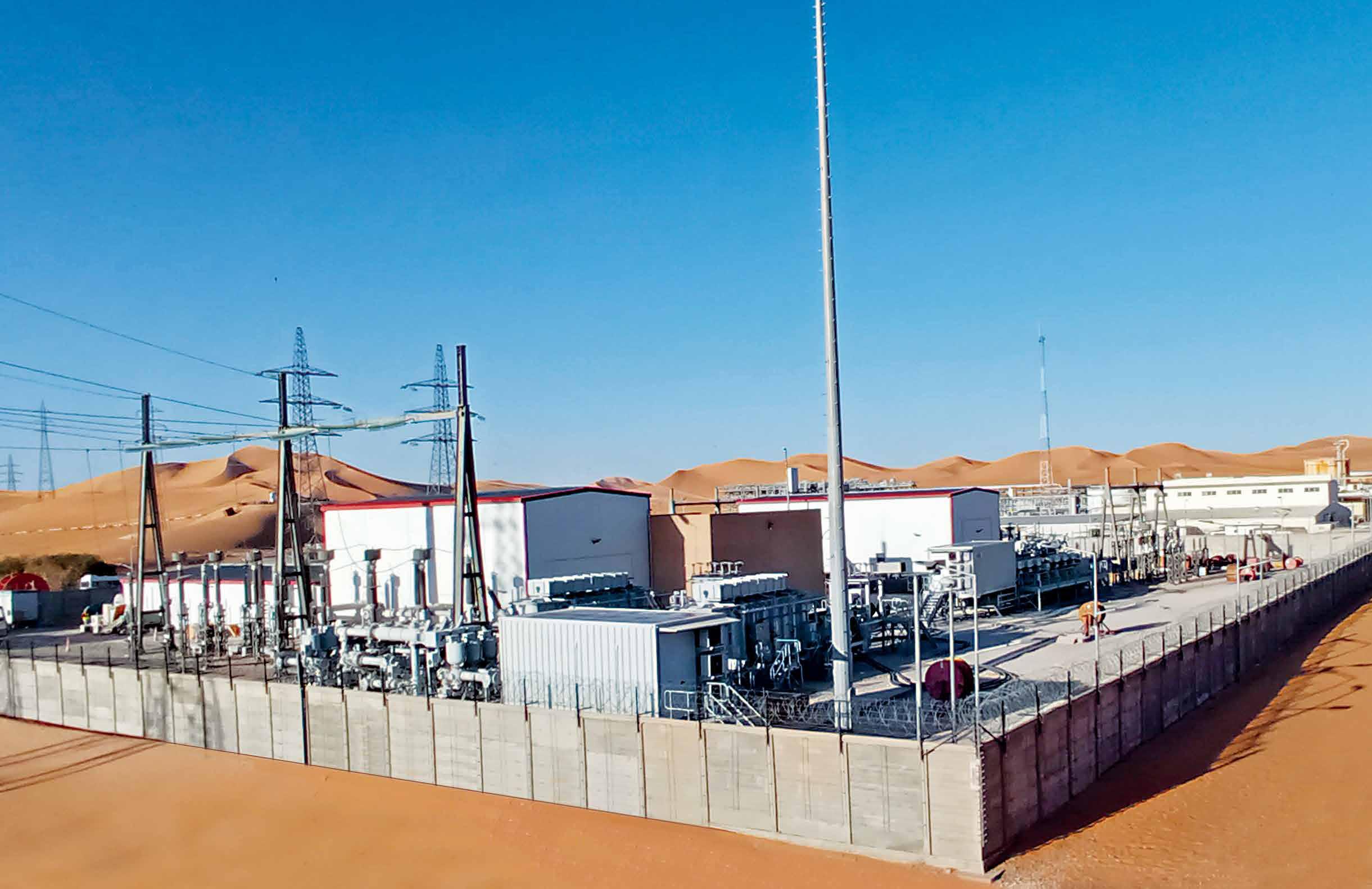
Algeria or the People’s Democratic Republic of Algeria is situated in North Africa’s Maghreb region. In terms of land area, it is the largest country in Africa and the 10th largest in the world. The country is a semi-presidential republic, with its capital city of Algiers, located in the far north on the Mediterranean coast. The 44 million Algerians are Arab-Berber, speak Algerian Arabic, practice Islam, and use the official languages of Arabic & Berber although French serves as an administrative and educational medium. Possessing the highest Human Development Index among the African countries, Alegria is also one of Africa’s biggest economies, based prominently on energy exports. With a semi-arid geography, the south of Algeria is dominated by the world’s largest desert – the Sahara Desert.
PT&D’s project to Rehabilitate & Upgrade the electricity grid of Alegria’s Hassi Berkine Basin is a large span job that stretches right across the Sahara Desert involving revamping the existing 220kV power network in a ‘live’ environment across 19 locations, comprising 8 main substations and 11 Central Processing facilities. “Even moving from one work location to another was a huge task,” remarks Project Control Manager, Shelbbyn Michael Raj, seriously. “We were prohibited to move out of the Base Camp without armed guards and hence precise planning was required to sequence our tasks.”
Apart from executing in an alien land in extremely inhospitable ground & climatic conditions, the team had to face and overcome a plethora of other on-ground challenges, making the taste of success of being recognized as the project with the best Quality standards across L&T Construction even sweeter for Project Director Venkatesan Karuppaiah, BU Quality Head Seetarama Bangar Raju, Shelbbyn Michael Raj, Project Engineering Manager Venkateswarlu Aitha, Manager QA/QC Anto Gnanaraj, Asst. Manager QA/QC Satish Kumar Singh, and the team of hardy desert warriors.
“Our first task therefore was to decide and firm up our approach starting with the premise that we were not going to compromise our contractual time of 24 months that included 7 months for engineering.”
Venkatesan Karuppaiah
Project Director,
PT&D Algeria Project
“Our job is very similar to hotline stringing,” points out Venkatesan, “but the critical thing is to ensure continuous power supply at all the voltage levels to power the oil & gas processing facilities in the region.” Most of the composite works like energization of the 220kV mobile station and laying 81 km of 30kV underground cables inside the hydrocarbon facility is over and the team is now gunning to finish the core infrastructure before Q3 of 2022.
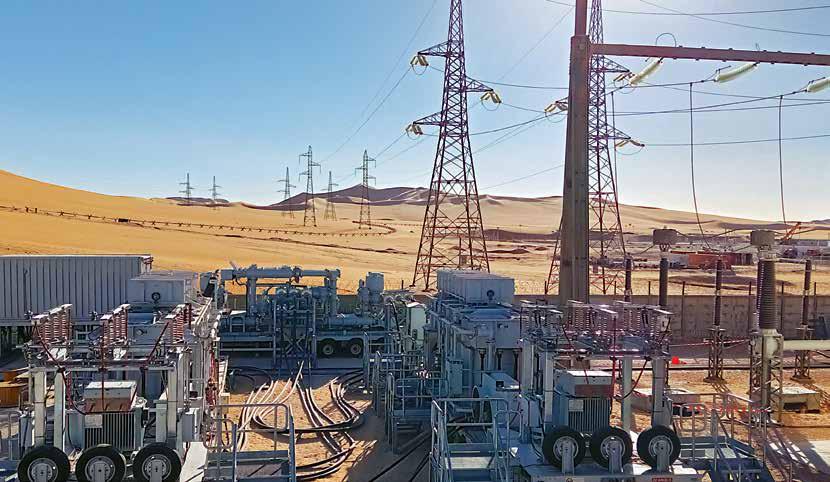
MLN – 220/60kV GIS Mobile Station
Collection of old, as-built information and ensuring its accuracy
Procuring data is challenging in the best of times. Here, the team had to source as-built data from a 23-year-old substation without shutting it or the feeders down as that would have resulted in revenue loss to the customer. With conventional methods, this exercise could have easily taken anywhere close to 4 months with only about 90% accuracy of the data. Further, the team could have ill afforded the resultant delays to engineering schedules, time & cost overruns, and disruptions to their procurement plans. “Our first task therefore was to decide and firm up our approach starting with the premise that we were not going to compromise our contractual time of 24 months that included 7 months for engineering,” Venkatesan sets the context. “By creating an integrated existing as-built data bank, we had a single source of truth and one point solution for IPD (Integrated Project Delivery).”
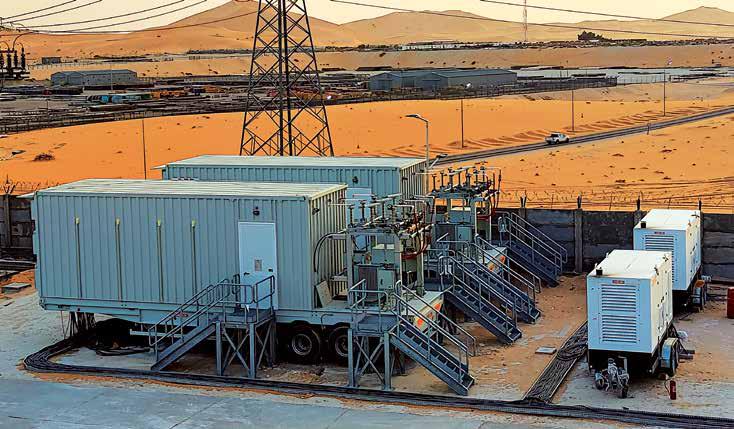
30kV GIS Mobile trailers at ORD
Using a combination of digital tools including LiDAR, REVIT, NAVISWORKS, 3DS Max, and others, the team completed the entire exercise in 6 weeks flat with 100% accuracy of the data collected, which has ensured the quality of the documentation from the start. “We have adopted the highest standards of Oil and Gas projects and the best engineering practices and strategies,” chips in BU Quality Head Seetarama Bangar Raju.
Adopting the digital mode reduced cycle time thanks to online client reviews & approvals, improved productivity by avoiding multiple revisions, ensured accuracy of the bill of materials for the LOT items as the data was extracted directly from the 3D layouts, and saved costs, with no need for multiple site visits.
“We have adopted the highest standards of Oil and Gas projects and the best engineering practices and strategies. ”
Seetarama Bangar Raju
BU Quality Head,
PT&D Algeria Project
“Yes, it called for some close coordination between the various stakeholders – SONATRACH, SONELGAZ, GRTE, and the CPF authorities,” nods Shelbbyn Michael Raj, “but our planning was spot-on.” The good relations forged in the process with all the stakeholders have stood the team in good stead even during the critical rehabilitation works.
“Yes, it called for some close coordination between the various stakeholders – SONATRACH, SONELGAZ, GRTE, and the CPF authorities – but our planning was spot-on.”
Shelbbyn Michael Raj
Project Control Manager,
PT&D Algeria Project
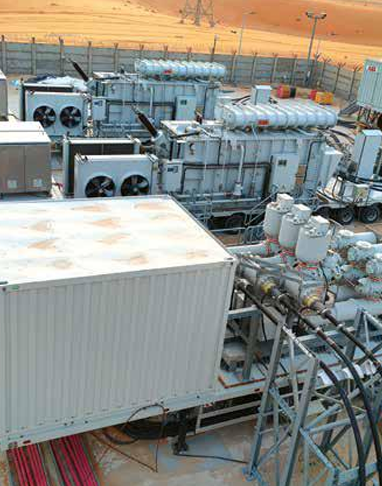
ORD – 220/30kV GIS Mobile Station
To demolish or not, to construct
The team was mandated to demolish the existing 30kV AIS building and construct the foundations for a new one, which, although seeming straightforward on paper, was not quite so. The demolition of any existing heavy structure in the Hassi Berkine area requires a mandatory approval from the CTC, the local statutory body in Algeria, that normally takes 6–9 months. “Structurally, the old building was interconnected with other buildings that were fully functioning and so we had to ensure their structural integrity,” mentions Venkatesan. To address both these issues, the team proposed a prefabricated building next to the existing 30kV AIS building. This proved to be a masterstroke as not only was the onerous task of procuring permissions avoided, but the team also saved 135 days in construction time and other related costs in site overheads.
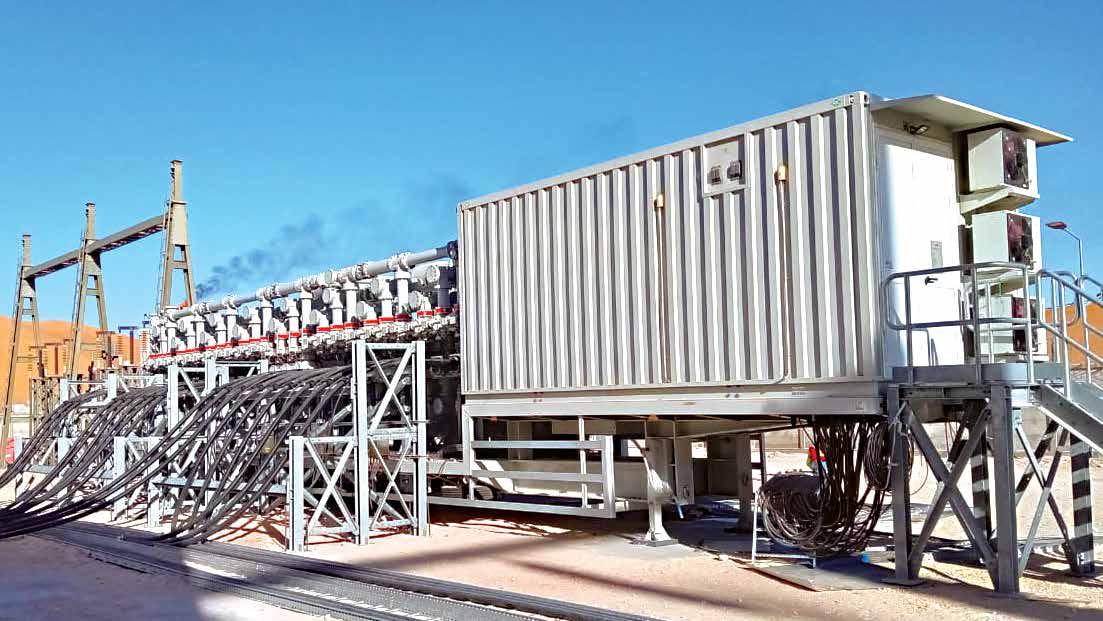
MLN – 60kV GIS Mobile Trailer
Executing in a ‘live’ environment without interrupting power supply
As power supply to the existing oil processing facilities could not be interrupted at any cost, the team had to continue executing in a ‘live’ environment, for which they prepared appropriate rehabilitation procedures and execution sequences.
“After analysing all the risks, we proposed precast foundations (interlocked tiles) for the temporary equipment that are suitable to install in a ‘live’ 220kV equipment area, which has both saved us execution time and improved our quality of execution.”
Venkateswarlu Aitha
Project Engineering Manager,
PT&D Algeria Project
As Venkateswarlu Aitha, the Project Engineering In-charge at the site, elaborates, “At the ORD location, the execution sequence has been redefined to avoid one cycle of shutdown activities, saving us 55 days of construction time and attendant overheads.”
The ’live’ environment also posed a challenge to cast new, temporary foundations for outdoor 220kV cable terminations in the existing 220kV live switchyard to tap the power supply to connect with the temporary 220kV mobile station. “After analysing all the risks, we proposed precast foundations (interlocked tiles) for the temporary equipment that are suitable to install in a ‘live’ 220kV equipment area,” Venkateswarlu Aitha explains, “which has both saved us execution time and improved our quality of execution.”
Who can forget the pandemic?
Topping all other challenges were those that were thrown up by the pandemic. FATs via MS Teams replaced physical inspections due to the restrictions involving the OEMs and clients. The team ensured that every quality check and all other routine and type tests were conducted online, without fail.
EHV cable termination activities are usually carried out by either the OEM or OEM-certified jointers, but in this scenario where OEMs were unable to depute their personnel, the team sourced technically qualified locals to close in on such critical activities with sufficient orientation.
A delighted customer is half the battle won
Venkatesan and his team can take pride in the regular accolades they receive from the customer, SONATRACH, for their progress and quality. The project was ISO 9001:2015 certified by Bureau Veritas and was implemented following ISO 9001:2015 QMS practices right from the start, with Quality Managers Anto Gnanaraj and Sathish Kumar Singh taking charge along with the quality inspectors to maintain Zero Defects. They have implanted quality & workmanship requirements right down to the workmen level. “We orient our employees and workmen during induction and before the start of any new activity, and Pep Talks are an effective tool to ensure that quality is implemented at the grassroot level,” elaborates Anto. Internal audits & product quality checks are conducted meticulously and regularly to capture issues before they happen, while management reviews help to align towards the right direction and procure resources at the right time. As a result of this strict implementation, the project has received ZERO customer complaints & ZERO product defects.
“We orient our employees and workmen during induction and before the start of any new activity, and Pep Talks are an effective tool to ensure that quality is implemented at the grassroot level.”
Anto Gnanaraj
Quality Manager,
PT&D Algeria Project
On the safety front, the project has bagged a RoSPA ‘Silver’, and the client’s accolades for achieving one million safe manhours in December 2021 are propelling the team to keep raising the bar, complete and hand over this challenging project, always maintaining their exemplary quality standards.