FEATURE-LADEN MTHL HAS ONE MORE CLAIM TO FAME – THE OSD
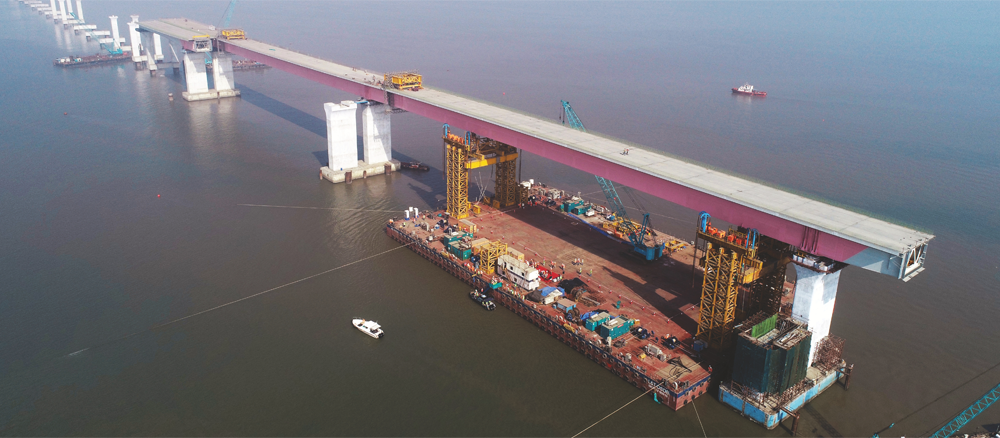
The OSD installation involved 3 million bolts, 24 kms of welding, 1,06,000 sqm of painting, bringing together 50,000 MT of structural steel, forming 38 spans with a total length of 4.666 kilometres.
The 21.8 km Mumbai Trans Harbour Link, India’s longest sea bridge, is close to establishing a vital link between the city of Mumbai and its satellite city, Navi Mumbai. Truly an engineering marvel, in addition to its various highpoints is yet another – its Orthotropic Steel Deck or OSD. “Although OSDs are being done for the first time in India, based on our domain strength, we strategically decided to do the entire OSD installation activities in the Arabian Sea totally in-house,” remarks R Anbalagan, Executive Vice President & Head – Heavy Civil SBG. K Senthilnathan, Executive Vice President & Head – Technical Services, took on the challenge to accomplish this technological feat.
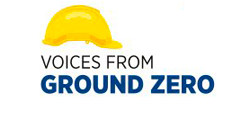

“Although OSDs are being done for the first time in India, based on our domain strength, we strategically decided to do the entire OSD installation activities in the Arabian Sea totally in-house.”
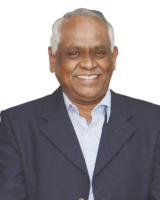
R Anbalagan
Executive Vice President &
Head – Heavy Civil SBG
Decoding the OSD: It is a steel deck superstructure (strengthened or stiffened both transversely and longitudinally) to carry vehicular load more efficiently on three planes and improve the load-carrying capacity of a bridge compared to a concrete superstructure for similar spans. The OSD has lesser self-weight than concrete or composite girders and is preferred for longer spans – 180 m, in the case of MTHL.
Arriving in segments, the OSD span is assembled, transported on Self-Propelled Multi-axle Trailers (SPMT) and loaded onto a barge using a customized skidding system. The lifting towers are then assembled on the deck of the barge and strand jacks commissioned on top of the lifting towers for each lift. The OSD span is lifted above the pier height just before reaching the final location for installation, and the barge moved slowly using mooring winches till the OSD span comes in line with an already erected one, lowered, aligned, and installed on the bearings atop the pier. QED, quite easily done, one might think, but V Kasiraja, Vice President & Head – P&M and Special Projects & Construction Methods and team will vouch that it certainly was not as easy as it sounds.
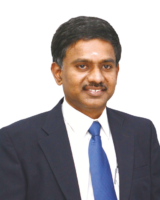
V Kasiraja
Vice President & Head – P&M and Special
Projects & Construction Methods
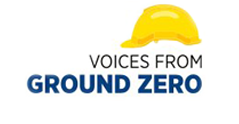

“We chose multiple strand jacks (16 numbers, each having a capacity of 300 MT) to lift the OSDs synchronously within a tolerance of ±5mm thanks to digital, tailor-made software controlled by a laptop with a mouse click.”
Tracking the birth and journey of the OSD
The first challenge for Vice President & Deputy Project Director, Sanjay Digambar Patil and team was to manage the logistics of procuring the components from across 7 countries, while still recovering from the impact of the pandemic. “We had to manage other complexities,” mentions P Vijay, General Manager & Head – OSD, MTHL-1, “like the dependency on tidal variations, disruptions due to the monsoons, and the complexities of working over critical utilities and pipelines located underwater.”
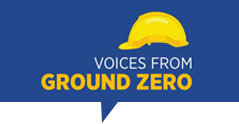

“We had to manage other complexities like the dependency on tidal variations, disruptions due to the monsoons, and the complexities of working over critical utilities and pipelines located underwater.”
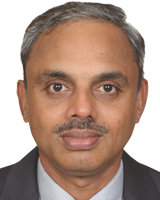
P Vijay
General Manager & Head – OSD, MTHL-1
While the steel spans were fabricated by the project’s consortium partner, M/s IHI Corporation, in factories across Japan, Vietnam, Taiwan, China, these were assembled in Mumbai involving the installation of 3 million bolts, 24 kms of welding, 1,06,000 sqm of painting, bringing together 50,000 MT of structural steel, forming 38 spans with a total length of 4.666 kilometres, accomplished in a limited 10-acre assembly yard, transformed into 7 assembly lines. Further, a facility was developed in an eco-sensitive zone by expanding and reinforcing an existing jetty to load the longest
(180 m) and heaviest (2650 MT) OSD spans without disturbing the surrounding mangroves and flamingo
breeding areas.
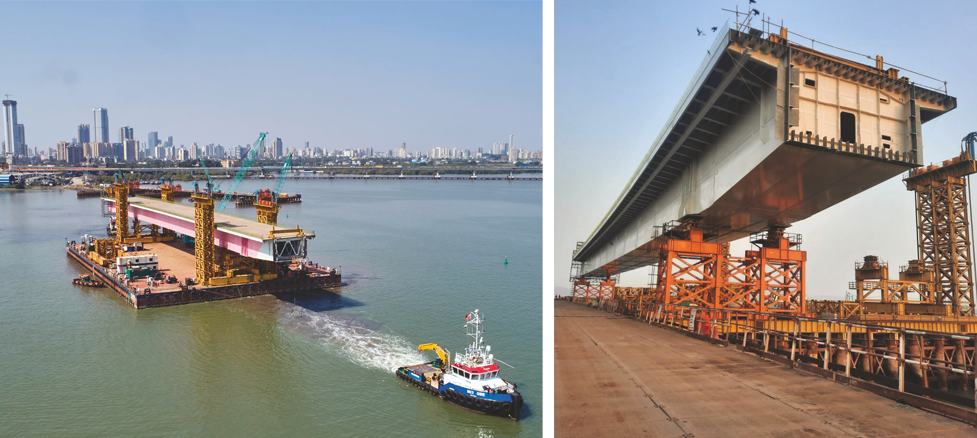
A modular flat-top ballastable barge measuring 110 m in length, 64 m in width, and 6 meters in depth, roughly equivalent to the size of a football ground, was designed and manufactured at L&T’s shipbuilding facility in Kattupalli, Chennai.
A modular flat-top ballastable barge measuring 110 m in length, 64 m in width, and 6 meters in depth, roughly equivalent to the size of a football ground, was designed and manufactured at L&T’s shipbuilding facility in Kattupalli, Chennai, while the Hydrocarbon offshore team took on the onus of manoeuvring and mooring operations to transport the spans. Additionally, L&T Construction’s Special Projects & Construction Methods team, attached to Divisional Corporate, collaborated in loading out skid car arrangement and final erection using multiple Strand Jacks in tandem. The OSD spans had to be synchronously lifted from all four corners and all the structural members, lifting towers and strand jacks were preassembled and load tested prior to first lift.
For P Vijay, another challenge was the limited access for the 3 spans of OSD -1 (320 m long), which crossed low-tide zones and one span of OSD-3 (85 M long) which crossed the highly critical utility pipelines transporting LPG & crude oil at Pirpau Jetty. “By adopting a unique Full Staging Method, we assembled these spans at the erection location itself,” he explains, “after which the entire superstructure, weighing up to 3200 MT, was shifted laterally across the viaducts.”
A couple of standout achievements of the team were assembling and aligning OSDs 1 & 3 by full staging methods using cranes and handling transverse skidding movement of a single 3200 MT OSD bridge from the left to right side pier caps at four locations using a tailor-made 2×80 MT push-and-pull jack skidding mechanism developed inhouse by the special projects and construction methods team.
Selecting the right tools & people
Jacks can be hydraulic or mechanical in operation and available in a range of capacities and designs, so Kasiraja’s task was to choose the right ones for their specific task. “We chose multiple strand jacks (16 numbers, each having a capacity of 300 MT) to lift the OSDs synchronously within a tolerance of ±5mm thanks to digital, tailor-made software controlled by a laptop with a mouse click,” he elaborates. The jacks were carefully and uniformly raised or lowered to avoid uneven loading. “We maintained and restricted a maximum of 80% of the hydraulic jack stroke length and lifting capacity, based on which calculations were made and specifications arrived at for procurement,” he adds.
All the lifting jacks, push-pull jacks (skidding) and strand jacks were tested at 125% of their rated capacity before being engaged and automatic horizontal strand jack re-coilers were designed, fabricated, and used for the OSD load out to avoid bailout strands into the seawater. Apart from rigorous checks, the strand jack lifting system was periodically maintained. The Strands were replaced with new ones after every 6 lifts to avoid slippage due to the highly corrosive marine environment ensure safe lifting.
160 MT (2x80MT) twin push-pull jacks with radio devices were developed, implemented, and successfully executed for 3200 MT & 2000 MT OSDs 1 & 3 for side shifting and mechanical locking system to facilitate the horizontal skidding push force was deployed for the first time. Approximately 150 hydraulic jacks were used at various locations while for the OSD lifting at the assembly yard and final alignment, the team used remote-controlled double-action hydraulic jacks with common manifolds to maintain perfect levels during lifting, lowering and final alignment.
The barge movement from the jetty to the location for erection was carefully planned based on tidal swells and all OSD span installations were completed before the onset of the 2023 monsoon.
All OSD activities were handled by specially trained strand jack/ lifting jack operators mentions S. Velu, Manager (Mechanical, Special Projects & Construction Methods). “We selected competent technicians and trained them at various stages to execute the job flawlessly with a team made up of people drawn from different cultures, nationalities, and demographics to overcome the challenges of time, tide, and wind to deliver.”
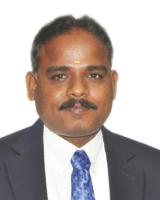
S. Velu
Manager (Mechanical, Special
Projects & Construction Methods)
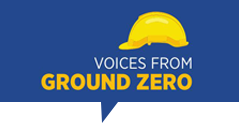

“We selected competent technicians and trained them at various stages to execute the job flawlessly with a team made up of people drawn from different cultures, nationalities, and demographics to overcome the challenges of time, tide, and wind to deliver.”
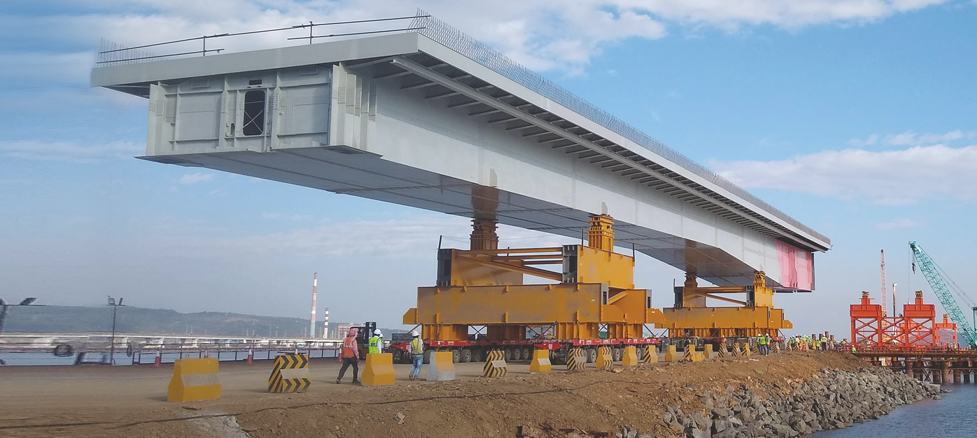
“We were aware of most of the challenges with true to remarks K Senthilnathan. “We, however, held firm, and thanks to some excellent coordinated efforts from different wings of L&T, all the 38 OSDs are in place.”
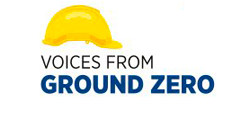

“We were aware of most of the challenges with true to form many unforeseen ones cropped up as we progressed, we, however, held firm and thanks to some excellent coordinated efforts from different wings of L&T, all the 38 OSDs are in place.”
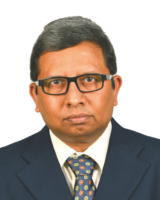
K Senthilnathan
Executive Vice President &
Head – Technical Services
As the Project team prepares for the inauguration, they are a delighted bunch having literally moved the earth to erect these huge Orthotropic Steel Decks.