HEAVY CIVIL PROJECTS MAKE SIGNIFICANT HEADWAY, DESPITE OPERATING IN CHALLENGING TERRAINS AND CONDITIONS
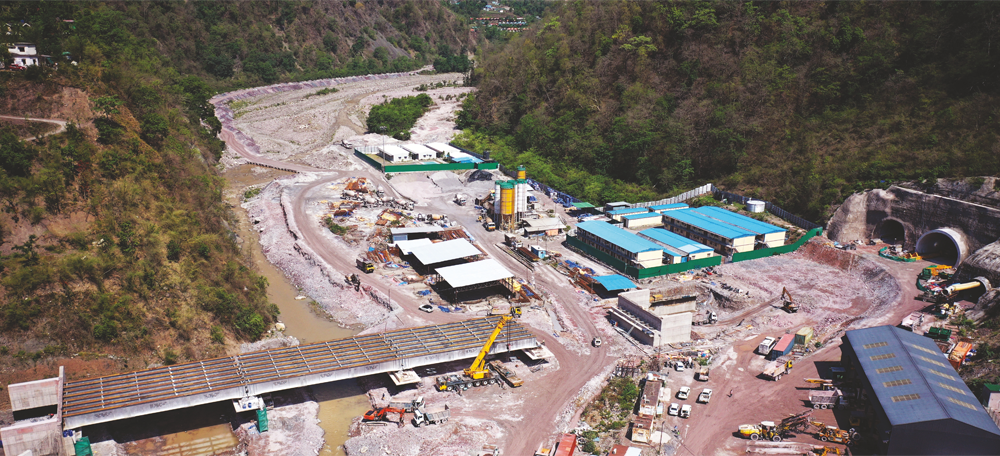
RISHIKESH-KARNAPRAYAG RAILWAY
TUNNEL (RVNL) PACKAGE-2
Ask Project Manager, Rajesh Chopra, and his team at the Rishikesh-Karanprayag BG Rail Line Project (Package 2) and they will vouch that executing in the Himalayas is no small matter and tunneling is even more challenging, considering the varying and tough geological conditions. The project involves the construction of tunnels, bridges, and formation works of a broad–gauge rail link between Rishikesh and Karnaprayag in Uttarakhand.
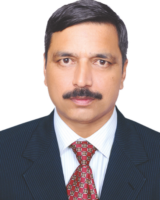
Rajesh Chopra
Project Manager
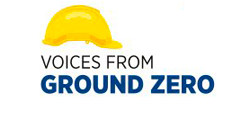

“We have completed 21.73 km of the total 26 km and the final lining works have begun across multiple fronts. We have set yet another benchmark by completing 20 km of NATM tunnelling in just 32.7 months from the first blast, against industry standards of 4 to 6 years. This is certainly the fastest 20 km tunnelling done in the country so far.”
The team started to dig into the Himalayas on August 26th, 2020, the first amongst the 10 packages of the RishikeshKaranprayag Railway Line, and Rajesh is happy with their progress of tunneling till date. “We have completed 21.73 km of the total 26 km and the final lining works have begun across multiple fronts,” proudly adding, “We have set yet another benchmark by completing 20 km of NATM tunnelling in just 32.7 months from the first blast, against industry standards of 4 to 6 years. This is certainly the fastest 20 km tunnelling done in the country so far,” he reiterates for good measure. The team has faced tough geological conditions like heavy water ingress of up to 7,200 litres/min and poor rock strata ranging from colluvium soil, phyllite, and the like.
“The tunnel excavation is being executed through 16 tunnel faces at six different locations, including four additional faces, with the diameters ranging from 5.2 m to 21.7 m,” apprises Senior Construction Manager (Civil), Param Jit Singh. “Of these, we have broken through in four faces in 2022, with a further eight expected this year,” he adds triumphantly.
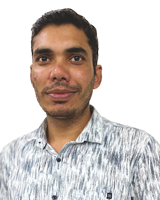
Param Jit Singh
Senior Construction Manager (Civil)
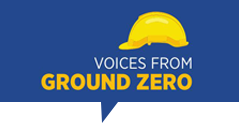

“The tunnel excavation is being executed through 16 tunnel faces at six different locations, including four additional faces, with the diameters ranging from 5.2 m to 21.7 m. Of these, we have broken through in four faces in 2022, with a further eight expected this year.”
The Client, RVNL, is equally thrilled with the team’s progress commending them for their efforts to mobilize the required resources, open multiple work fronts ahead of schedule, maintain progress and achieve 10.2 million safe man hours in the process.
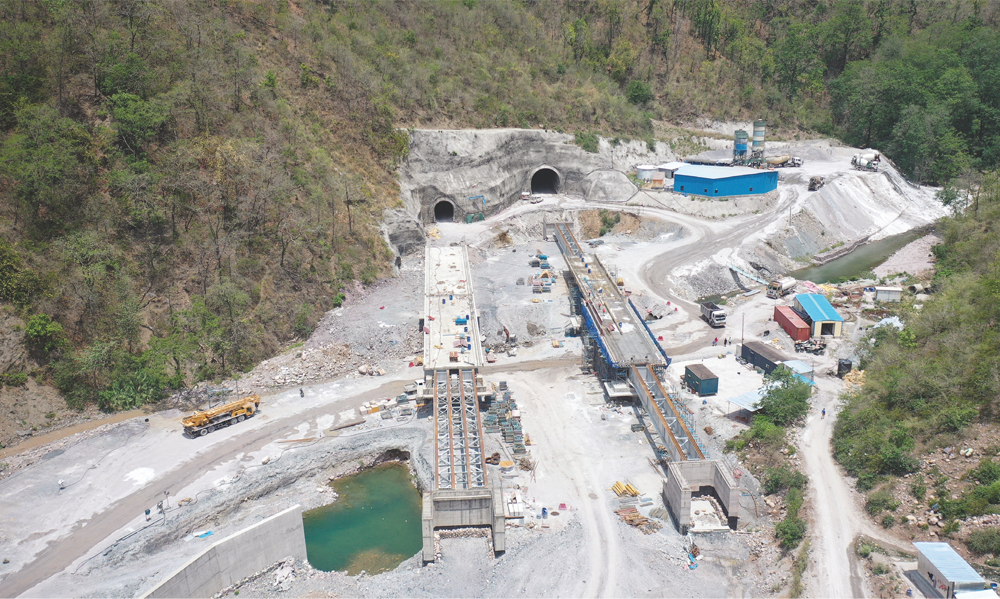
Succeeding in challenging conditions
Efficient contracts management: “We realized very early in the project that a robust contract and claims management system was required and adopted a proactive approach rather than the conventional ‘reactive’ approach to execute and manage the contract,” Contracts Manager, Srimaan Nannapaneni, points out insightfully, and reels off some of their best practices. Every GET and PGET is encouraged to go through the GCC, PCC and Works requirements of the contract in the first week of deployment at site before taking up their roles in the assigned departments. “We have empowered the entire execution team right from In-charges to the GETs with knowledge about scope management, which historically ‘make or break’ construction projects,” he adds. One such initiative is the ‘knowledge sharing Thursdays’ wherein all department in-charges and their delegates deliver sessions on their areas of expertise to the rest of the team.
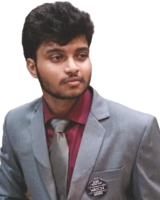
Srimaan Nannapaneni
Contracts Manager
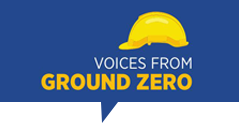

“We realized very early in the project that a robust contract and claims management system was required and adopted a proactive approach rather than the conventional ‘reactive’ approach to execute and manage the contract.”
“In addition to the direct variations, our prime focus has been on contract interpretation claims, the basis for which is made in close coordination with our Planning and Contracts teams,” mentions Construction Manager, Divyanshu Sharma. “In fact, we successfully lodged and realized several such claims by taking the client into confidence and following up end-to-end.”
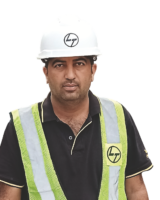
Divyanshu Sharma
Construction Manager
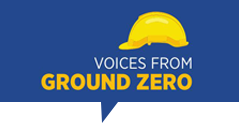

“In addition to the direct variations, our prime focus has been on ‘contract interpretation claims’ the basis for which is made in close coordination with our Planning and Contracts teams.”
All department heads are encouraged to avoid deliberate contract breaches and have a solid contemporaneous record (in standardized formats) throughout the execution phase to make strong grounds for claims and avoid unwarranted disputes with the customer. In addition, delays, hinderances and variations are updated real-time, periodically reviewed followed by timely notices to the customer to establish the team’s time and cost entitlements.
Efficient PM management: If there was one thing the pandemic taught P&M In-charge, Shankar Kumar, it was to ensure adequate P&M manpower, spares, in-house facility for repairs and OEM support. “We targeted skilled manpower with minimum 10 years’ experience to operate our best-inclass automatic jumbos and shotcrete machines and gave them simulation training with the help of the OEM apart from on-the-job training to ensure that the machines were in safe hands,” he remarks. Looking ahead, the team has kept additional operators on standby from March 2021 to mitigate the risk of a second pandemic wave.
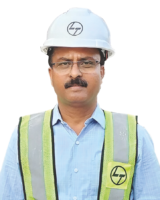
Shankar Kumar
P&M In-charge
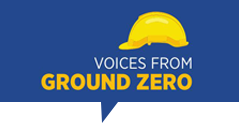

“We targeted skilled manpower with minimum 10 years’ experience to operate our best-in-class automatic jumbos and shotcrete machines and gave them simulation training with the help of the OEM apart from on-the-job training to ensure that the machines were in safe hands.”
Best-in-class workshops at Shivpuri (start) and Byasi (finish) ensure in-house facilities to upkeep the Rs. 160 Crore asset base (owned & hired) that have also increased the Mean Time Between Failures (MTBF) and reduced Mean Time To Repairs (MTTR). Vendors manage inventories at site to avoid disruption.
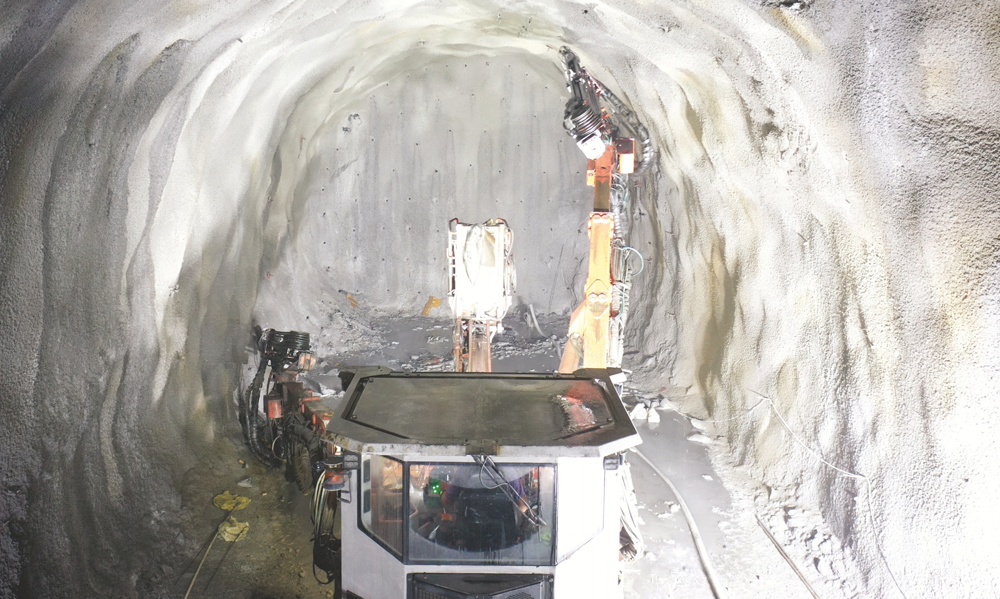
“Being first of their kind machines and a contractual requirement, we established service level agreements with key OEMs to ensure that their engineers are camped at site to train our staff for troubleshooting and guidance on maintenance practices,” informs Shankar and their effort paid off handsomely, especially during the pandemic, maintaining 95% availability. “Our first major triumph was completing 4 km of tunneling in 11 months and being appreciated by the client for our achievement,” he shares with a wide smile.
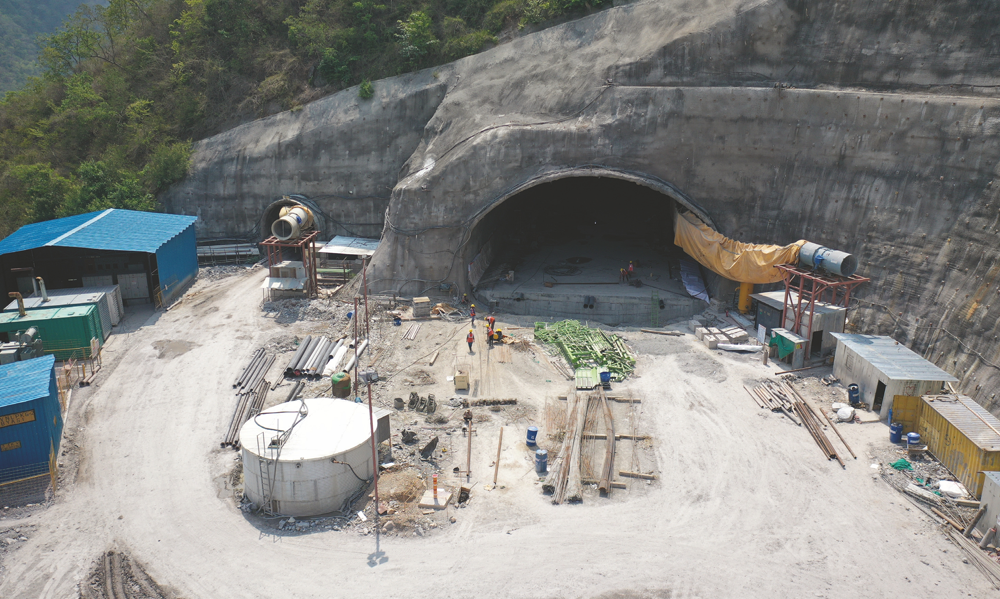
Site innovations
In-house fabricated dumper tailgate: that has reduced muck spilling, considerably improved hauling capacity and by evenly distributing the load, it has reduced the damage to the tyres and improves balance.
Mist sprayer fabricated in-house at the Byasi workshop: has suppressed dust by 75%, improved visibility, and reduced downtime.
Implementation of Out Riggers to Haggloader 7HR B: The site was getting mucked up as the conveyor did not have the height to entirely fill up the dumper and hence the out-riggers, that have substantially improved the cycle time of implementing the rigger.
Digital fuel monitoring system: To overcome the challenges of shortage of diesel from IOCL, fuel pilferage due to the site’s remote location & round-the-clock operations and the need to track daily consumption of 15 KL, the team implemented underground tank fuel sensors with IoT, static dispensers & fuel bowsers with IoT and RFID readers, use asset tagging, RFID tags and fuel sensors. The accruing advantages include monitoring the entire fuel chain, reducing pilferage and increasing fuel mileage. The team has installed an Aether GPS monitoring system to further control pilferage and monitor idling. An underground decantation system has addressed the issue of fuel shortage from IOCL.
“We have an extremely aggressive timeline to deliver our project,” sums up Rajesh, “and hence we have had to manage several independent activities at site parallelly to crash the duration and meet the project schedule like starting the concrete lining works along with tunnel excavation. Thus far, we have managed all the multiple activities well in a planned way to meet scheduled progress.” Here’s wishing the team the very best!
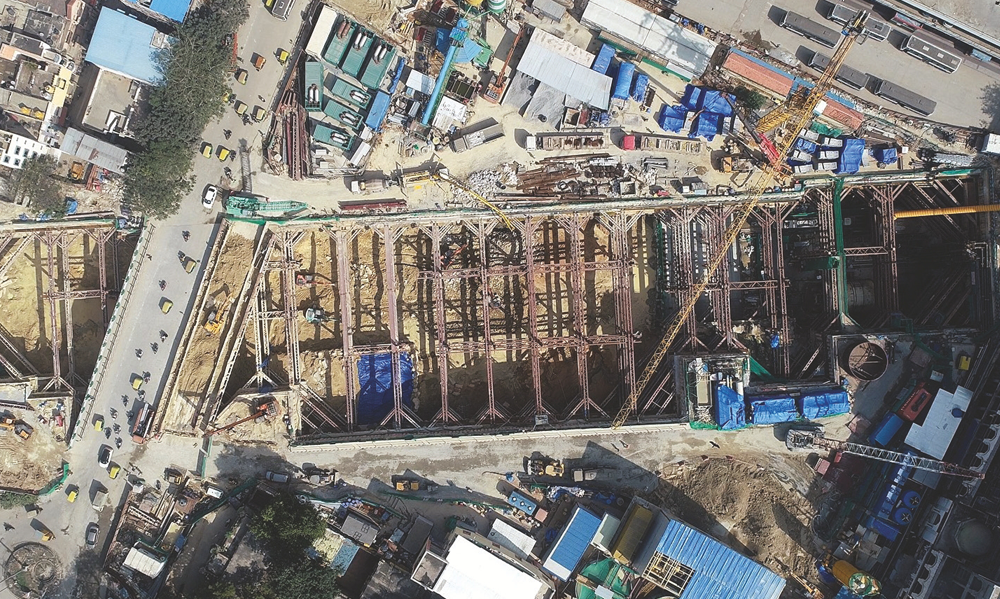
BANGALORE METRO RT-02
The story about the Bangalore Metro project is one of facing and overcoming underground challenges that have come in various shapes and forms for the RT-02 & RT-03 project teams. Kickstarted on March 8th, 2019, the RT-02 project involves the design and construction of three underground stations at Shivajinagar, M.G. Road and Rashtriya Military School (RMS) along with Entry-Exits, construction of a 2.2 km long underground twin tunnel along with four cross passages. Executing in the heart of the city throws up its own unique challenges like traffic congestion, keeping age-old buildings safe, handling public grievances and, to top them all, tunnelling into one of the most difficult terrains due to Bengaluru’s varying geological condition. Taking all these in their stride, Project Manager, Vivek Maruti Pai, and his team, can take pride in having completed 87% of the project and are gearing themselves for the final ‘push’ to conclusion.
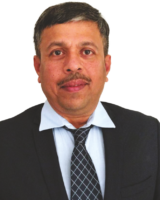
Vivek Maruti Pai
Project Manager
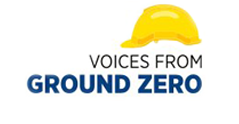

“As our project’s success depended on how well we navigated the TBM through various geological surprises and under densely populated buildings without any accidents, we realized that understanding the geological conditions first could significantly mitigate risk.”
It’s all about efficiency in tunnelling
Tunnelling conditions are classified into three: full face rock, full face soil and mixed face (soil and rock). “As our project’s success depended on how well we navigated the TBM through various geological surprises and under densely populated buildings without any accidents, we realized that understanding the geological conditions first could significantly mitigate risk,” shares Vivek, insightfully.
Therefore, their first step was to carry out confirmatory boreholes for Geotechnical Investigation (GTI) at 26 locations as per contractual requirements. Further, the site team collaborated with the National Institute of Rock Mechanics (NIRM), Bengaluru, to carry out Tomography Survey, an advance Geophysical survey, to determine geological conditions along the stretch from Shivajinagar to RMS stations. When faced with space constraints to drill exploratory holes (required for Tomography), an alternate Geophysical method i.e., GPR (Ground Penetrating Radar) survey and Multi-Channel Analysis of Seismic Waves (MASW) were conducted by collaborating with the Indian Institute of Science (IISC), Bengaluru.
“The alternate Geophysical approach helped us enormously,” says Vinayak Gaonkar, Senior Construction Manager (MECH), “to identify the weak geological pockets that required stabilizing before carrying out the necessary grouting works, saving us from major incidents like sink holes, damages to buildings, and giving us better control on volume loss measurements as the geological parameters were accurate. The extensive geological data also helped us to plan cutter disc requirements since they were imported from CRCHI, China.”
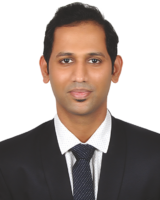
Vinayak Gaonkar
Senior Construction Manager (MECH)
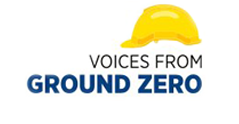

“The alternate Geophysical approach helped us enormously to identify the weak geological pockets that required stabilizing before carrying out the necessary grouting works, saving us from major incidents like sink holes, and damages to buildings, and giving us better control on volume loss measurements as the geological parameters were accurate.”
Three formations predominantly encountered:
- Fresh to completely weathered with tight joints (massive in nature) rock mass
- Uniaxial compressive strength varies from 50 to 200 Mpa
- Moderately to highly weathered, highly jointed, moderate to closely spaced open joints rock mass with spheroidal weathering in nature
- Fine grain soils (silty-clay or fine sandy-silt)
A full face of rock or soft ground or mixed face conditions were predicted for the tunnel drives with groundwater level as low as 3 m below the surface.
With most of the tunnelling being carried out in mixed face conditions with boulder formations, chances of damages to the cutter discs were high that necessitated frequent cutter head interventions in Hyperbaric mode under pressure of
2 Bar that threatened to slow down progress. “We carried out 736 hyperbaric Cutter Head interventions involving the replacement of 2000+ cutter discs, and, at times, hot work was carried out during hyperbaric interventions, the first of their kind in India.” informs Ram Krishna Shrivastava, Senior Manager, TBM. “During hot works, the samson air supply lines were modified and sophisticated equipment like plasma cutting, gouging, MIG welding machines were used to address the situation.” he illustrates.
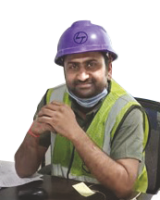
Ram Krishna Shrivastava
Senior Manager, TBM
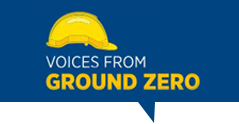

“We carried out 736 hyperbaric Cutter head interventions involving the replacement of 2000+ cutter discs, and, at times, hot work was carried out during hyperbaric interventions, the first of their kind in India.”
Managing the cross passages
“As per BMRCL’s approved key date, we were supposed to complete the cross passages within six months after completing the tunnel,” mentions Vivek, “but we changed the construction sequence and undertook the construction of the cross passages along with the tunnelling by making a ramp. We completed all four cross passages progressively within 3 months of the last TBM breakthrough,” he says with a look of triumph, helping the team to achieve the final key date of tunnelling well within the stipulated time.
Apart from tunnelling, constructing the three underground stations had their own set of challenges due to limited working space, delay in handing over the land by the customer, high density of traffic and public grievances to address which the team undertook several time and cost control measures.
Driving a COVID advantage: Road diversions and traffic decking works had to be carried out along Cubbon Road, Hosur Road and Meenakshi Kovil Road to construct the Entry-Exit structures in the M.G. Road, RMS and Shivajinagar stations. “Normally, subway works are taken up only after the station box is completed that often result in delays,” points out Vinayak. “As per our construction methodology, the traffic decking along Cubbon Road was planned in 6 stages, to be completed in 12 months.” Similarly, traffic decking at Hosur Road was planned over 6 months and at Meenakshi Road over 4, with additional road diversions. As the density of traffic fell during the lockdowns, the team was permitted by the Commissioner of Police to partially block these roads. Despite acute shortage of workmen, they prioritized traffic decking works, realizing their long-term implication. “We completed the road decking works on Cubbon Road and Hosur Road within 3 months and Meenakshi Kovil Road in a month and a half without having to construct alternate diversion roads that saved us cost and time,” asserts Vivek.
station box was handed over on August 8th, 2022, just 11 days before the contractual completion date. The entire land for the station box construction was handed over in a piece meal basis with the first tranche of 20%. “By changing the construction sequence, we were able to reach the roof slab level before the adjacent land was handed over to us,” says Vinayak. “This was a learning curve for the entire team to plan construction activities better and take corrective action to reduce cycle time during further construction.” The team’s proactive measures saved the project 10 months in the construction of the RMS station.
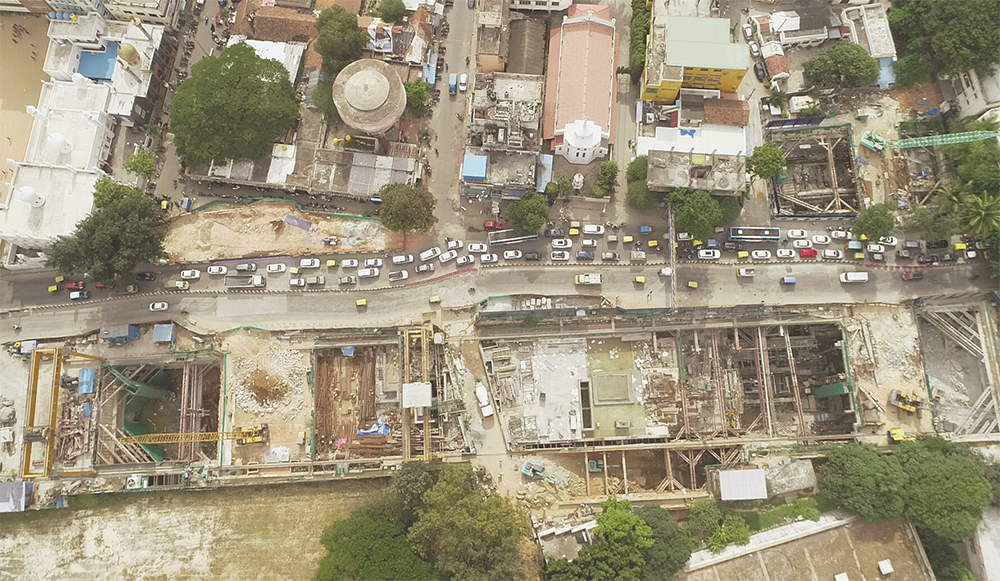
Driving continuous improvement
Reuse of Temporary Structural Steel (Strut and Waler): Temporary structural steel members are used to support soil retaining structures (piles) during open excavation in the stations and Entry-Exits and dismantled stage wise during construction. Dismantling in stations is linked to their requirement in the Entry-Exits for which the team followed a schedule to reuse the structural steel without going for additional procurement, saving approximately 2,500 MT of structural steel in procurement and fabrication (25% of overall structural steel consumption). “Bangalore Metro RT-02 was the first job site in Heavy Civil IC to implement the E-Tap digital initiative that enables QR based tracking of temporary structural steel,” adds Vinayak, proudly. Since drawings, MTC and other quality documents are loaded on the portal against fabricated steel member, E-Tap helps to track steel for reuse w.r.t drawings.
Using Crushed Rock Fines (CRF) and TBM sand instead of M-Sand to produce CLSM concrete (Controlled Low Strength Materials) for backfilling works that is 20% cheaper: The team used the TBM sand obtained during the tunnelling operation based on availability and replaced CRF materials by 50% during a certain period (when good tunnel sand was available) to produce CLSM concrete resulting in substantial cost savings.
The team laid a dedicated 66 kV line from C-Station of KPTCL to tap 12 MW of power for TBM operation that involved laying 1.25 km of cables along heavily congested roads, after procuring all the regulatory approvals from BESCOM and KPTCL, which is time-consuming. Through this smart move the site saved substantially.
BANGALORE METRO RT-03
Awarded in March 2019, the Bangalore Metro RT-03 contract involves the design and construction of underground structures (tunnels and stations) of approximately 2.884 km from Shivajinagar Station (excluding) to Retrieval Shaft (excluding) (Chainage 13938.328 m to 16822.521 m) including allied works and 2 UG Metro stations at Cantonment and Pottery Town.
TBMs drive the tunnelling effort forward
“Apart from executing in one of the toughest and most unpredictable geologies, we contend daily with a densely populated city and an extremely busy railway line that sees 76 train crossings every day,” remarks Project Manager, Lakshmi Prasad Vesangi, “but despite these challenges, we achieved the longest mining length of 27 m in a day and 273 m in a month, both significant benchmarks in Bangalore Metro’s mining history.”
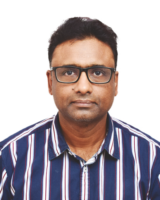
Lakshmi Prasad Vesangi
Project Manager
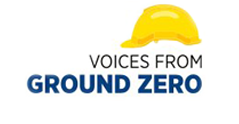

“Apart from executing in one of the toughest and most unpredictable geologies, we contend daily with a densely populated city and an extremely busy railway line that sees 76 train crossings every day, but despite these challenges, we achieved the longest mining length of 27 m in a day and 273 m in a month, both significant benchmarks in Bangalore Metro’s mining history.”
Contributing in no small measure to their success has been the performance of the two TBMs, ‘Urja’ and “Vindhya’ that cumulatively dug 4.866 km over three drives:
- Drive 1: Cantonment to Shivajinagar (864 m)
- Drive 2: Cantonment to Pottery Town Station (900 m) &
- Drive 3: Pottery Town to Shadi Mahal Retrieval Shaft (688 m)
A hint of their demanding task is reflected in the fact that for their entire stretch of mining, the mixed geological conditions required 222 cutter head interventions (open & closed) for each TBM. “It was really tough going,” remarks Planning Head, A M Santhosha, “but, as a team, we stuck to our task overcoming obstacles, learning and developing new skills, and implementing creative methodologies to add value to our effort.”
Drag-through is a common practice in TBM mobilization within stations. “We completed the process in 15 days
(a first of its kind achievement) by avoiding interference with concurrent activities and relaunched the TBM via the station area with the participation of all stakeholders, involving equipment for speedy completion,” says Senior Engineer, Gandupalli Diwakar.
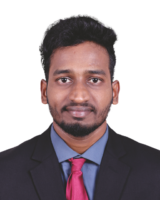
Gandupalli Diwakar
Senior Engineer
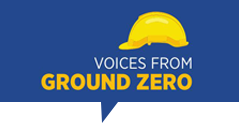

“We completed the process in 15 days (a first of its kind achievement) by avoiding interference with concurrent activities and relaunched the TMB via the station area with the participation of all stakeholders, involving equipment for speedy completion.”
Station building: The Cantonment station was a prominent station to be constructed in the densely populated Cantonment area where the team identified rock strata in the geological conditions that required controlled blasting. “The rock strata present in the station box area consisted of joints which dissipated the explosive energy in between the rock layers curtailing the productivity of blasting,” says Assistant Construction Manager (Mines), Santosh Kumar, with a serious face. “Based on our findings, we decided to go ahead with deck charging in which blasting was executed in two different media of rock layers.”
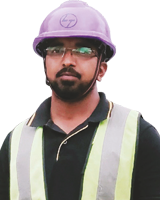
Santosh Kumar
Assistant Construction Manager (Mines)
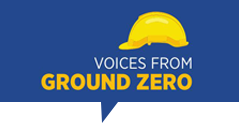

“The rock strata present in the station box area consisted of joints which dissipated the explosive energy in between the rock layers curtailing the productivity of blasting. Based on our findings, we decided to go ahead with deck charging in which blasting was executed in two different media of rock layers.”
By itself a risky affair, blasting, albeit controlled, in an area hemmed in with buildings, public roads, and age-old religious structures call for a high degree of control over AOP (Air Over Pressure) and PPV vibrations. “We overcame these challenges by covering the trunk line detonator with sandbags to prevent the glass of windows and doors from breaking,” A M Santhosha explains, “and to control the excess use of concrete, we drilled two vertical 20 to 22 m holes, adjacent to each other instead of rope cutting.”
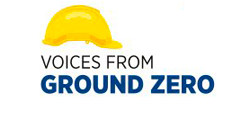

“It was really tough going but, as a team, we stuck to our task overcoming obstacles, learning and developing new skills, and implementing creative methodologies to add value to our effort.”
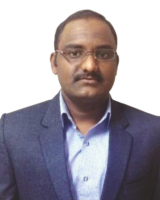
A M Santhosha
Planning Head
For the piling activity to begin at the Pottery Town station, environmental clearances and utility diversions proved major hinderances; the high-water table levels encountered during excavation and piling, another. “Heavy seepage turned the retrieved muck into slush hindering our efforts to lay the PCC and waterproofing,” points out Engineer Manish Kumar, “but we managed the situation by carrying out parallel activities.”
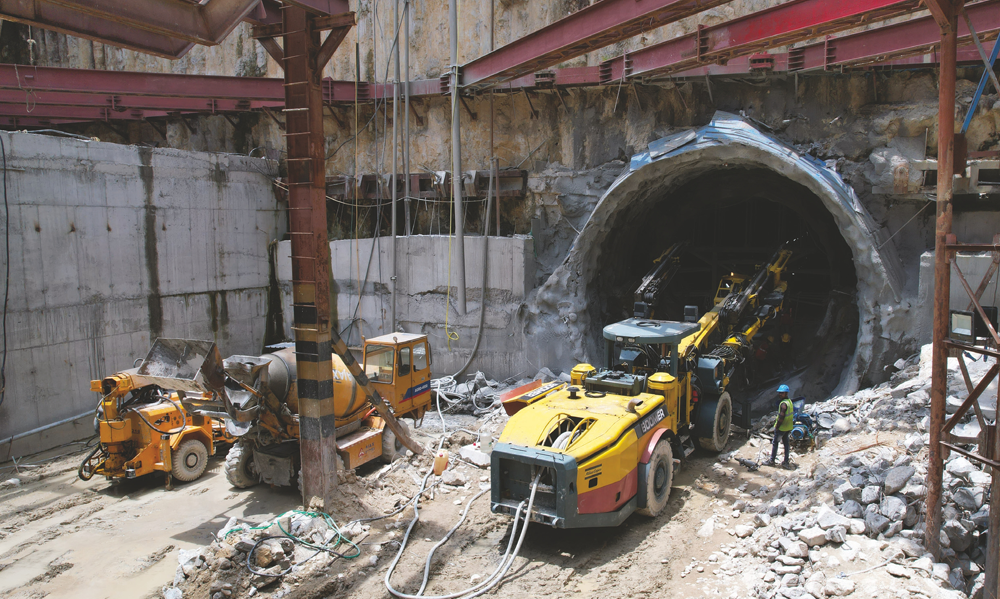
Handling reinforcements with the help of SSC: Reinforcement cutting and bending play vital roles in construction and in this case, the cutting and bending reinforcements were provided by SSC (Steel Service Centre) that significantly reduced the dependence on the workmen for cut and bend activities, saving cost of workmen and wastage. It also accrued indirect savings as a dedicated setup at site was not required and that resulted in better organization of the limited workplace made available at construction sites by the client.
Efficient precast team: The Precast team’s vital contribution for both the RT-03 & RT-02 projects to keep the four TBMs operating simultaneously cannot be ignored. “Selecting steam curing instead of normal curing and hourly monitoring of each activity and progress helped to improve cycle time and increase production to almost double the cycle time with a record achievement of 19 Rings in a day with only 9 sets of moulds,” says Senior Engineer, Ranjeet Kashyap. The challenge of production complexity vs the capacity of stacking for the continuous production of rings for both projects in the limited stacking area was tackled by opting for double tier stacking.
Smart procurement: Efficient procurement shortened the lead time between a purchase request (PR) and a purchase order (PO) and the involvement of all stakeholders guaranteed prompt material delivery to the site with minimal disruption. “We introduced new vendors after negotiating competitive rates to prevent monopolies and, more importantly, reduce cost,” smiles A M Santhosha. The team’s vendor relationship management helped maintain good affinity with both internal stakeholders and vendors and is a big contributory factor to their sustained success.
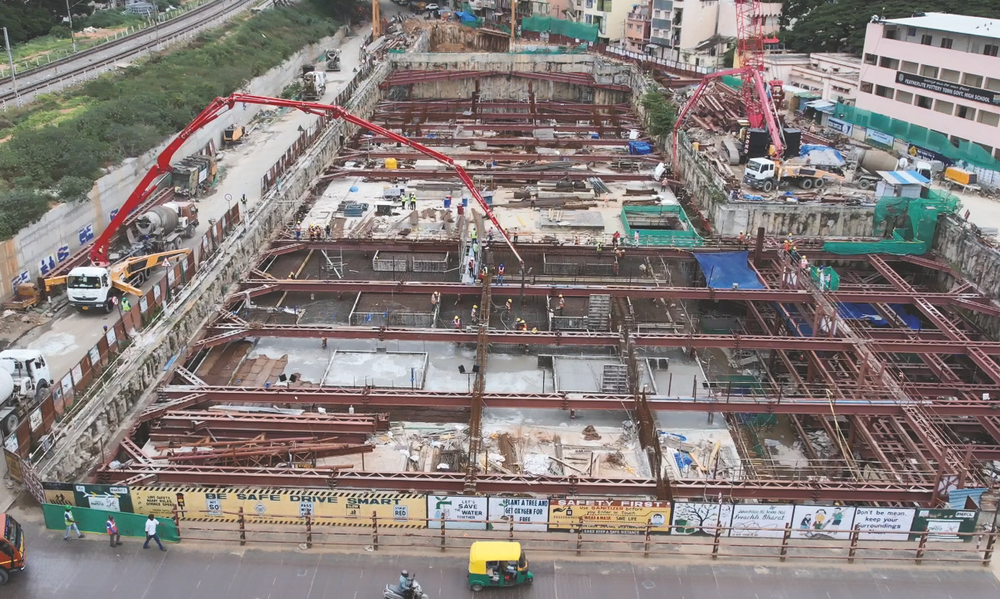
Driving Quality & Digitalization
Several quality initiatives have resulted in cost saving for the project. As both the TBMs were slurry driven, the disposal of slurry was a big concern. By using the clay obtained from the TBM face strata instead of making a new whole solution of slurry, they reduced the consumption of bentonite by 1300MT that has saved the team lakhs. Further, by reducing the slurry density in the STP, and the quantity of the slurry being disposed, also saved cost. Vesangi is proud that the entire 4.88 km tunnel stretch was completed with zero non-compliance on the backfill grout, maintaining all parameters without any deviations from the contractual requirements.
Another feather in his team’s cap was being recognized as the ‘Best Digital’ site for their implementation of IoT, ConEase, Procube, segment tracking that have enhanced productivity. An interesting ploy was to monitor production of concrete through discrete stimulation that even reduced wastage.
Performing on women power: “Our female colleagues have played an important part in the project’s success,” shares Vesangi, with a smile. “Working on-site, Junior Surveyor, Anuradha Shaw has established benchmarks to motivate others by understanding the minutiae at site level, monitoring, and scheduling work in line with the construction sequence, monitoring activities at a micro level of detailing, understanding the feasibility and estimating the cost of the project.” An environment of equity with equality has gone a long way to enhance diversity with women enjoying equal responsibility.
To round off their sterling performance, by deciding to use recycled sewage water in place of fresh water for all construction activities like road cleaning, wheel washing, TBM slurry / grout preparation, etc. at site, the team has shown their awareness of doing things to sustain the planet.
Well done, Lakshmi Prasad Vesangi and team! Here’s wishing you a quick and successful completion!