TWO L&T GEOSTRUCTURE PROJECTS MAKING A SOLID IMPACT IN MARINE ENVIRONMENTS
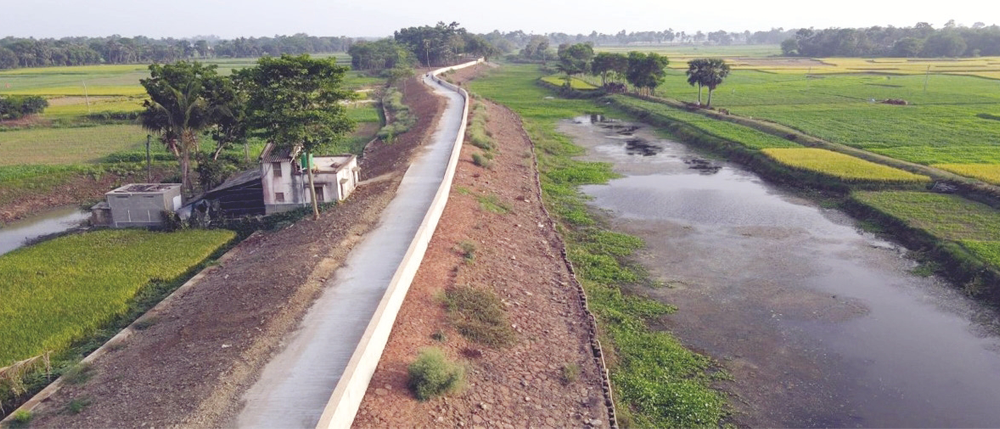
THE FLOOD MANAGEMENT PROJECT PACKAGE II, WEST BENGAL
Major Scope of Work | UoM | Scope Qty. |
---|---|---|
Sheet Pile Installation | MT | 3,545 |
Concreting - M20 | Cum | 24,362 |
Concreting - M25 | Cum | 23,080 |
Reinforcement | MT | 1,698 |
Wooden Bullah Driving (6 m -175 mm Ø) | Nos | 33,660 |
Anti-Skid Bag Pitching | Nos | 3,10,000 |
Boulder Pitching | Cum | 10,343 |
Earthwork in Excavation & Filling | Cum | 1,95,245 |
For years, flooding has been a major problem in West Bengal’s Hooghly and Howrah districts, in and around the lower Damodar sub-basin, disrupting lives and damaging crops. The area that faces the brunt is spread over 1.8 lakh hectares (1,887 sq. km), covering two municipalities and 20 administrative development blocks. Data collected over the last six decades reveals that about 4.6 lakh people are affected by floods annually and 335 sq. km (0.335 lakh hectares) of cropped area inundated. In 2021 alone, 1,79,321 hectares out of a total 10,82,285 hectares of paddy seeds were damaged and 2,20,957 hectares of agricultural land submerged. Over 22 lakh people were affected and 2,301 people needed to be evacuated to safer places.
To address this continuing menace, the West Bengal government is undertaking various measures and the proposed project involves an integrated flood management plan. The comprehensive plan of the State Irrigation & Waterways Department involves the construction of flood walls, river embankment armouring, de-silting the Mundeshwari river, and 41 other canals. The cost of the project is split three ways: the State Government contributing 30% with The World Bank and The Asian Infrastructure Investment Bank pitching in with 35% each.
In their maiden association with the West Bengal government, L&T GeoStructure has been mandated to develop ‘Flood protection measures on the left embankment of the upper Rampur Khal with flood walls and sheet piles, including old existing embankments to strengthen the countryside, and bank protection work on the river side in the districts of Howrah and Hooghly Package-II.’
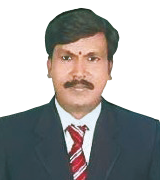
Vinod Bapurao Thakare
Project Manager
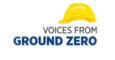

“Consecutively, both our client and the quality department approved our out-of-the-box suggestion to dredge the bed of the Damodar and Mundeshwari Rivers for earth and mix it with good earth at a 50:50 ratio to fulfil our requirements.”
Lofty objectives; tough challenges
Awarded on February 10th, 2020, this two-year project is Project Manager, Vinod Bapurao Thakare, and team’s opportunity to execute a project that will infinitely improve the lives of people living on the banks of the Damodar River. Challenges were awaiting Vinod and his team even before they set the ball rolling in the form of the pandemic. Later, as life limped back to normalcy, the team attempting to build flood protection systems were themselves repeatedly hit by nature’s fury: two cyclones, Amphan in May 2020 & YAAS in May 2021 and three bouts of heavy flooding in 2021. The government’s restriction on the supply of laterite boulders adversely affected the project as also encroachments, access issues, post flood restoration challenges, and more. The list is long, but the team has stood resolutely, staying committed to deliver a project that will certainly transform lives.
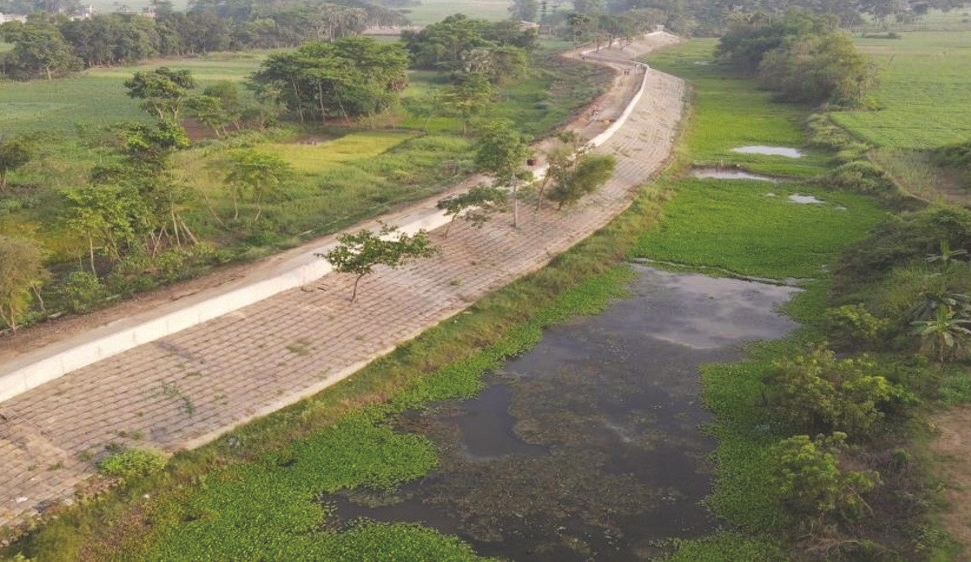
Pushing progress by piloting through a web of challenges
Access issues: “We had just about half of the site, 54% to be exact, when he started construction activities,” Vinod points Consecutively, both our client and the quality department approved our out-of-the-box suggestion to dredge the bed of the Damodar and Mundeshwari Rivers for earth and mix it with good earth Vinod Bapurao Thakare at a 50:50 ratio to fulfil our requirements. Project Manager out, “with most of the land encroached by migrants and having various other permanent obstructions.” When they arrived at the site, the first issue they had to address was to build proper motorable access. Lack of proper access also meant that it was difficult for construction equipment like excavators, tractors, and other machinery to reach the site. “Initially, we decided to widen the existing 2 m wide embankment bund but due to the existence of highly cultivated, rich agricultural land, we were unable to get the earth easily to do this job,” he shares. “Instead, we reduced the embankment height to 0.5 – 1.0 m to get the required width of the road to accommodate excavators and other construction material at site that speeded up progress.”
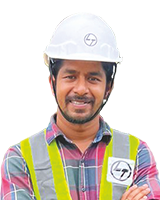
Dibakar Podder
Assistant Manager (Civil)
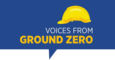

“At times, the situation turned worse with the locals ready to fight with us, but we had to keep calm in such situations, console them and focus on our targets.”
Another thorn in their flesh was the issue of encroachments. “Our embankment passes through several villages and, although the Government had remunerated the locals to relocate, many faced payment-related discrimination from the tenants,” shares Dibakar Podder, Assistant Manager (Civil). “At times, the situation turned worse with the locals ready to fight with us, but we had to keep calm in such situations, console them and focus on our targets,” he says grimly.
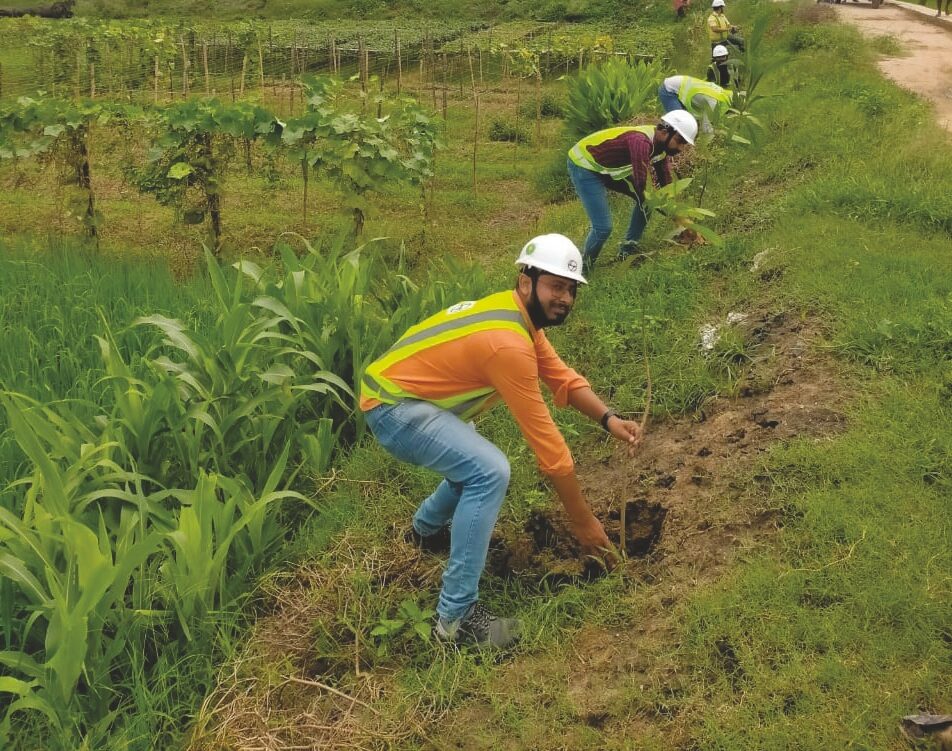
Logistics headaches: Insufficient space made logistical movement extremely difficult to overcome which, the team set up a yard 8 km from the site, that was easily accessible for heavy machinery and where the sheet piles and other construction material could be conveniently unloaded. “After the sheet pile was cut, painted, and inspected by a client representative, we dispatched it through tractor trolleys to the site,” informs Krishnendu Santra, Assistant Foreman (Marine). Similarly, the team set up a batching plant near the central yard, though transporting concrete on Transit Mixtures was not an easy task. Hence, after reaching a certain location, the concrete was transferred onto small SLM/Ajax of 2-4 cum capacity, that could easily deliver the concrete at the desired location at site.
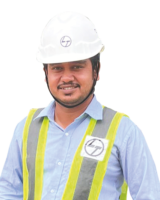
Krishnendu Santra
Assistant Foreman (Marine)
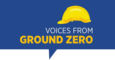

“After the sheet pile was cut, painted, and inspected by a client representative, we dispatched it through tractor trolleys to the site.”
In search of good earth: One of the biggest challenges before Vinod and team was to find about 150,000 cum. of earth to strengthen the embankment as per the designed drawing. With no one willing to offer earth from their highly valued agricultural land, the team approached the Gram Panchayat members about taking earth from the canal beds. “Consecutively, both our client and the quality department approved our out-of-the-box suggestion to dredge the bed of the Damodar and Mundeshwari Rivers for earth and mix it with good earth at a 50:50 ratio to fulfil our requirements,” shares Vinod. While it was not an easy proposition, the team took it upon themselves and solved their problem.

Initiatives to drive progress: The team has installed MOVAX, a special attachment, to the Excavator (PC-210) equipment to drive the sheet pile and Bullah faster. By using temporary electric board connections throughout the 18 Km stretch for area lighting and other construction activities, they have reduced emissions and thereby the carbon footprint.
Recognition: Despite the multiple challenges, the team has been aggressively pushing progress and Vinod is particularly pleased with the recognition they have won. “We won the ‘Quality Appreciation Certificate’ from the Chief Engineer & Project Director, I&WD, West Bengal Govt. for adopting best quality practices at site,” he shares proudly, “and received a special mention for our quality from the L&T Management
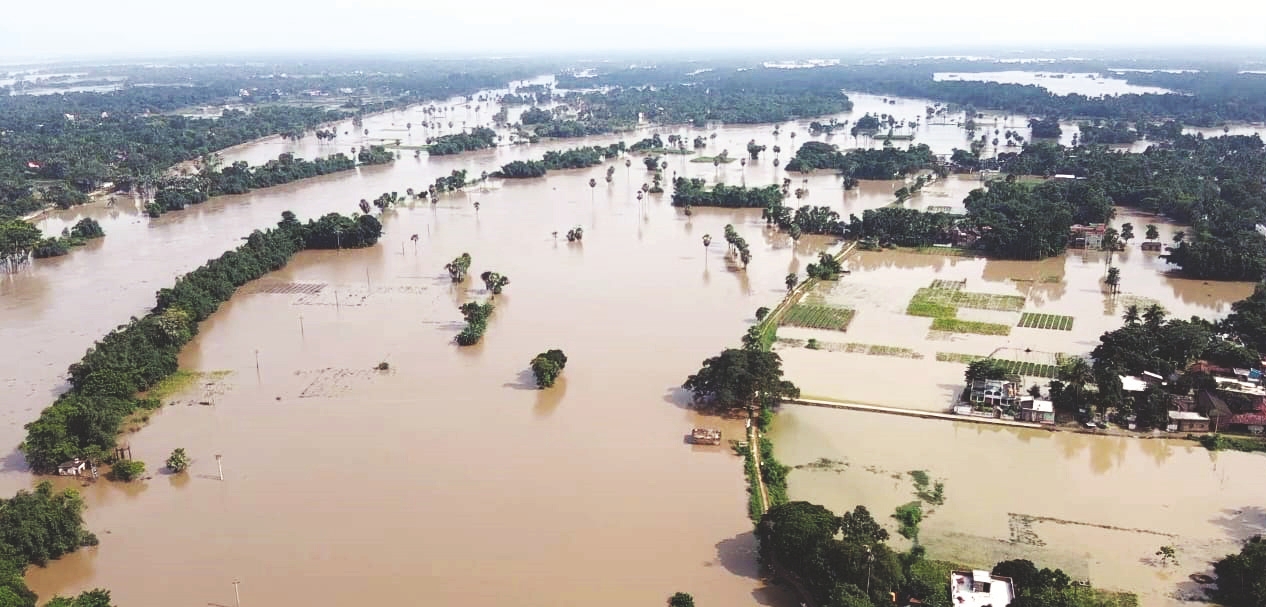
The team to the rescue: The project team turned out be to the people’s saviours in the neighbouring villages from flooding when the Damodar and Mundeshwari Rivers were in spate. More than 1100 workers were deployed to safeguard the bunds by placing filled polybags at the breaching locations and thereafter, effectively maintained pre- and postflood measures. Their efforts won them a certificate of appreciation from the client in 2021.
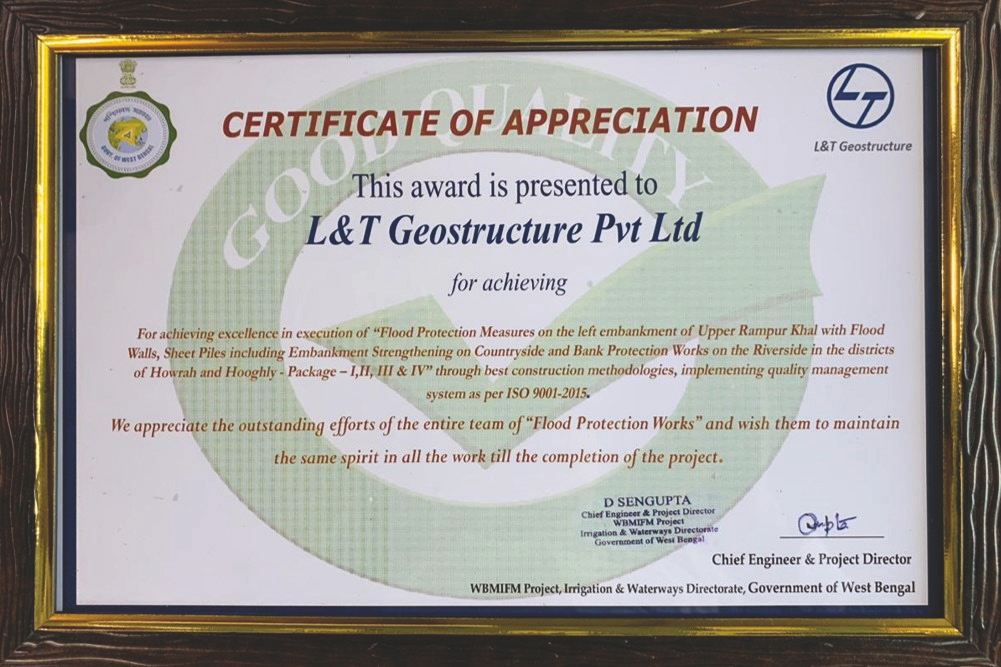
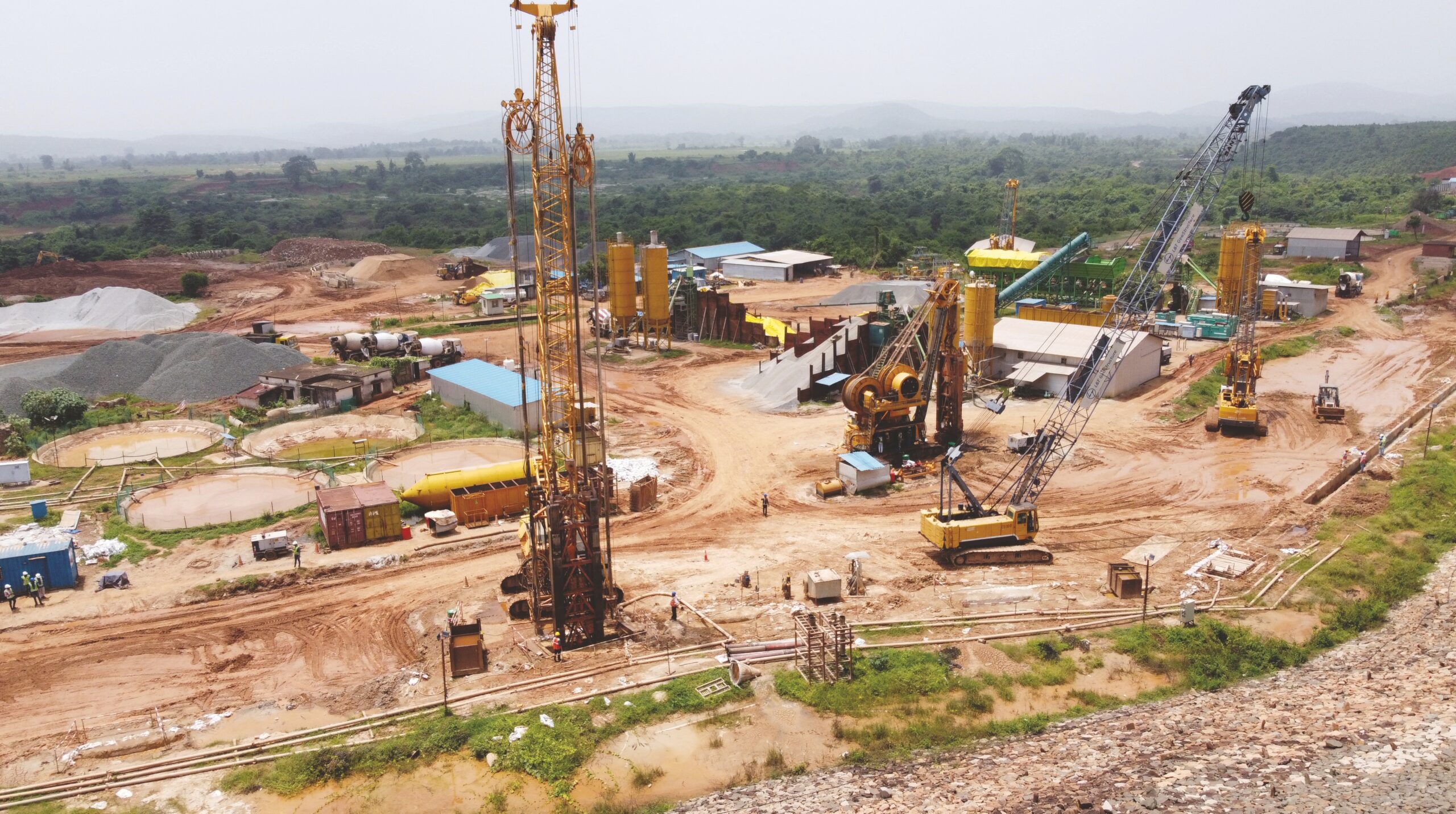
KANUPUR CUT-OFF WALL PROJECT
The Kanupur Cut-off wall project, being executed by L&T GeoStructure in Odisha’s Keonjhar district, involves building a 993 m cut-off wall to shore up a dam being constructed for irrigation purposes. Kicked off in late September 2021, the project team under the leadership of Project Manager, Praveen Pratap Singh, has completed 91% of the project and are pushing hard to complete and deliver.
Their progress has, however, been arduous having to trench through weathered and hard rock. Before starting trenching works, the team had carried out TAM Grouting works, through a specialized agency, for the entire stretch of the panel layout to stabilize the pebbles, cobbles, boulders and the trench to deploy heavy machinery.
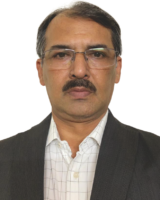
Praveen Pratap Singh
Project Manager
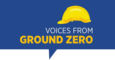

“As such panels were being done in 3 bites, we often encountered fresh rock at different levels in each bite, thus resorted to GTI that helped the Client agree to different termination depths for different bites on the same panel. Indirectly it also helped to reduce the breakdown of the cutter gearbox.”
Facing tough teething troubles
“We began working with 2 trench cutters, namely BC-32 and BC-30, to trench the cut-off wall but initially made very little headway doing only about 5.6 m in a month,” Praveen shakes his head and the reasons for their slow progress were multi-fold: huge and abrupt variations in the soil profile, an extremely hard rock layer of Granitic Gneiss, delay in finalizing the termination depth due to the varying rock profile and lack of maintenance of the equipment that was unsuitable to work in the rock strata they had encountered. It was up to the team to dig themselves out of this hole.
30 GTI boreholes, spaced approximately 40 m apart, were KANUPUR CUT-OFF WALL PROJECT made to map the soil and rock profile. As per the contract, the criterion to terminate the panel was 1 m in fresh rock with RQD > 75%. Shop drawings were prepared accordingly and approved by the client. The termination depth of panels executed between any 2 GTI holes is determined by interpolating the rock levels indicated on the GTI holes on either side. Due to the highly undulating rock strata, the team often encountered fresh rock above the interpolated fresh rock level and were thus forced to drill more than the required 1 m to reach the termination level as per the Client’s insistence to follow the submitted drawings.
Making little headway, the team after discussions with the HQ design team decided to carry out additional rock profiling boreholes spaced 10 – 20 m apart depending on the variation observed in the already executed boreholes to arrive at a more realistic rock level. This was re-proposed to and approved by the Client. “Doing so many additional boreholes would have been extremely time consuming and hence we went for the GTI open panel borehole method that reduced excessive workload on machinery, saved time and cost too,” remarks an evidently pleased Naik Musaddiq, Senior Engineer & Geologist.
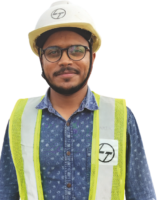
Naik Musaddiq
Senior Engineer & Geologist
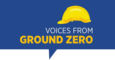

“Doing so many additional boreholes would have been extremely time consuming and hence we went for the GTI open panel borehole method that reduced excessive workload on machinery, saved time and cost too.”
There were more challenges awaiting the team. Without support, the drill casing was breaking due to the vibrations. The solution lay in fabricating a frame of MS pipes and plate that worked as a guide that reduced drilling time from
6 shifts to just 1 shift. “Whenever we encountered fresh rock at shallower levels than expected, we moved the cutter to a nearby panel to carry out GTI in the panel the same day to finalize the revised fresh rock level,” adds Naik.
For Praveen, another point of contention with the Client was to finalize the fresh rock levels for the larger panels.
“As such panels were being done in 3 bites, we often encountered fresh rock at different levels in each bite, thus resorted to GTI that helped the Client agree to different termination depths for different bites on the same panel,” he explains. “Indirectly it also helped to reduce the breakdown of the cutter gearbox,” his relief is evident.
In addition to the confirmatory boreholes, the team obtained the Client’s permission to carry out drilling in open panels wherever they hit fresh rock above the expected level by interpolating data obtained from the confirmatory boreholes.
“The GTI proved to be extremely cost effective and took less time than the actual trenching works,” mentions Naik.
Frequent breakdowns and poor maintenance of equipment was weighing the team down too. “A proper monthly maintenance schedule was put in place and spares planned and procured in advance accordingly,” informs Kappala Srikanth Vamsy, Assistant Manager (Execution). “Since we found the BC-30 cutter without a Bi-tronic system unsuitable for our work often having verticality issues, we replaced it with a BC-40 which became free only in August 22.”
In addition to regular maintenance that reduced idle time and idling of resources, spares are physically verified at the end of every month along with the list to ensure that critical spares are always available at site to avoid any major breakdowns as the lead time for the critical spares from Bauer could vary from 30-40 days.
Some other measures to keep productivity & progress in high gear
A working platform for free movement: During the 3-4 months of annual heavy rainfall, movement of men and machinery becomes difficult in wet, slushy underfoot conditions to combat which, the team created a working platform of Geocell and Geotextile, a ploy they had successfully deployed earlier at the HSR site.
Decreasing the length of the larger panels: When preparing the time cycle for each individual panel, the team observed a pattern that the instances of the panels in a particular stretch taking more time to trench with frequent breakdown of equipment in weathered rock and fresh rock matched with the GTI data where the strength of the rock was very high. After discussions with the Client, the length of the larger panels which are greater than 6 m was reduced to 2.80 m that improved productivity of the trench cutters.
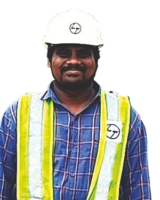
Kappala Srikanth Vamsy
Assistant Manager (Execution)
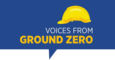

“A proper monthly maintenance schedule was put in place and spares planned and procured in advance accordingly. Since we found the BC-30 cutter without a Bi-tronic system unsuitable for our work often having verticality issues, we replaced it with a BC-40 which became free only in August 22.”
Stop & start technique: Pressure increases with an increase in temperature. Since the team was facing constant issues with the trench cutter system, they approached M/s Bauer for a solution and were informed that the system was designed to operate in rock having strengths of 100MPA whereas the rock they were encountering had strengths
of 100 to 200MPA. Repairs were also proving too costly for the team. Observing the working of the trench cutter, they noticed that when the temperature rose above 98°C, a warning red light in his cabin warned the operator to intermittently stop trenching to cool the gear oil. “This was a good takeaway for us as our trench cutter was more than 15 years and costly to maintain,” remarks Saroj Paul, Assistant Manager – Execution. “We immediately decided to cool the gear box oil by intermittently stopping the trench cutter for 10 minutes every hour with the result our gear boxes start to work for more than 1,500 hours. In fact, four of them even reached 2,000 hours,” he says pleased with their effort.
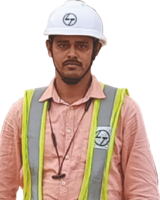
Saroj Paul
Assistant Manager – Execution
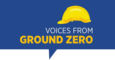

“We decided to cool the gear box oil by intermittently stopping the trench cutter for 10 minutes every hour with the result our gear boxes start to work for more than 1,500 hours. In fact, four of them even reached 2,000 hours.”
On the EHS front, Assistant Manager – EHS, Yuvaraj Ravi is focused on engineering control measures like additional locking arrangements for the radial conveyor movement during cyclones or heavy winds at the M-01 batching plant and an electrostatic discharging pit installed near the High-Speed Diesel (HSD) storage facility that effectively discharges any accumulated static charges in the fuel bulker during fuel transfer from the tanker to the storage facility.
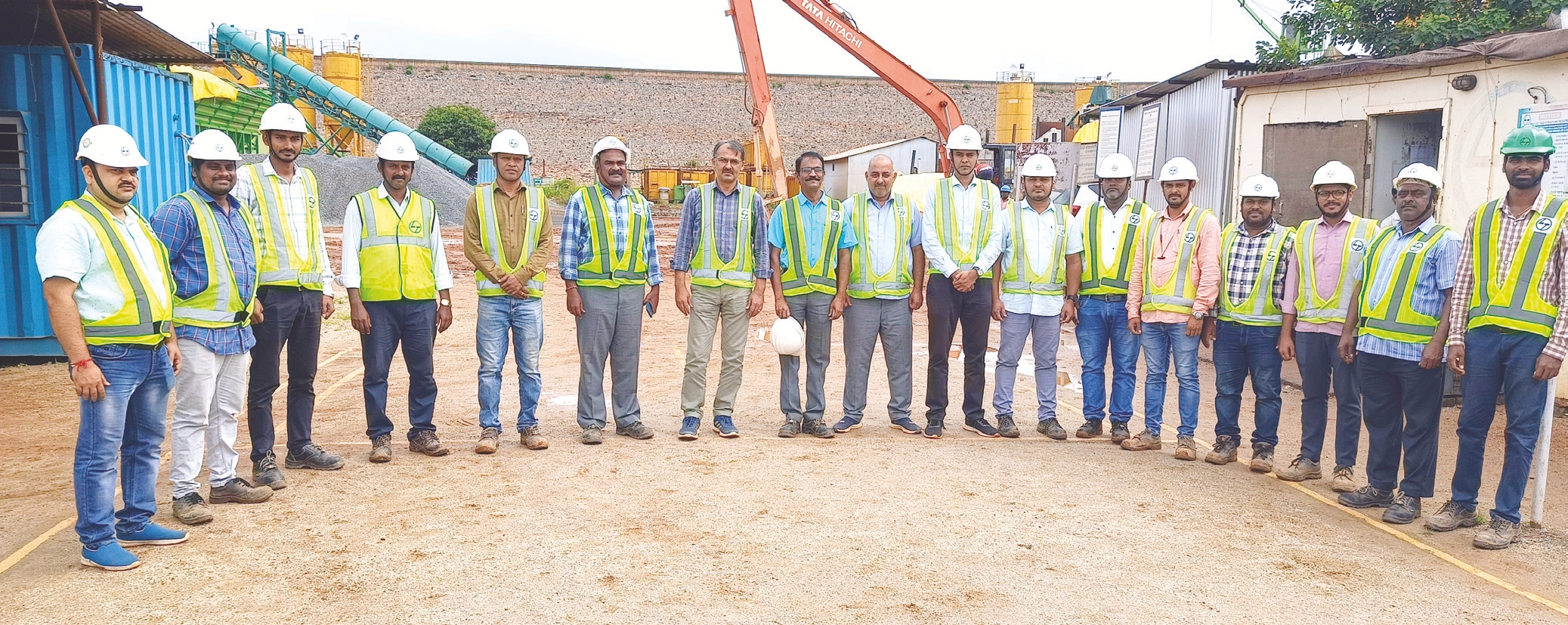
With most of his underground concerns resolved, Praveen and his team are on the high road to completing and delivering their project by October 2023 with just over 96 m of the cut off wall remaining to be built. And with a good margin too.