ONE B&F PROJECT ENTERS THE GUINNESS BOOK OF RECORDS; ANOTHER SET FOR A PODIUM FINISH
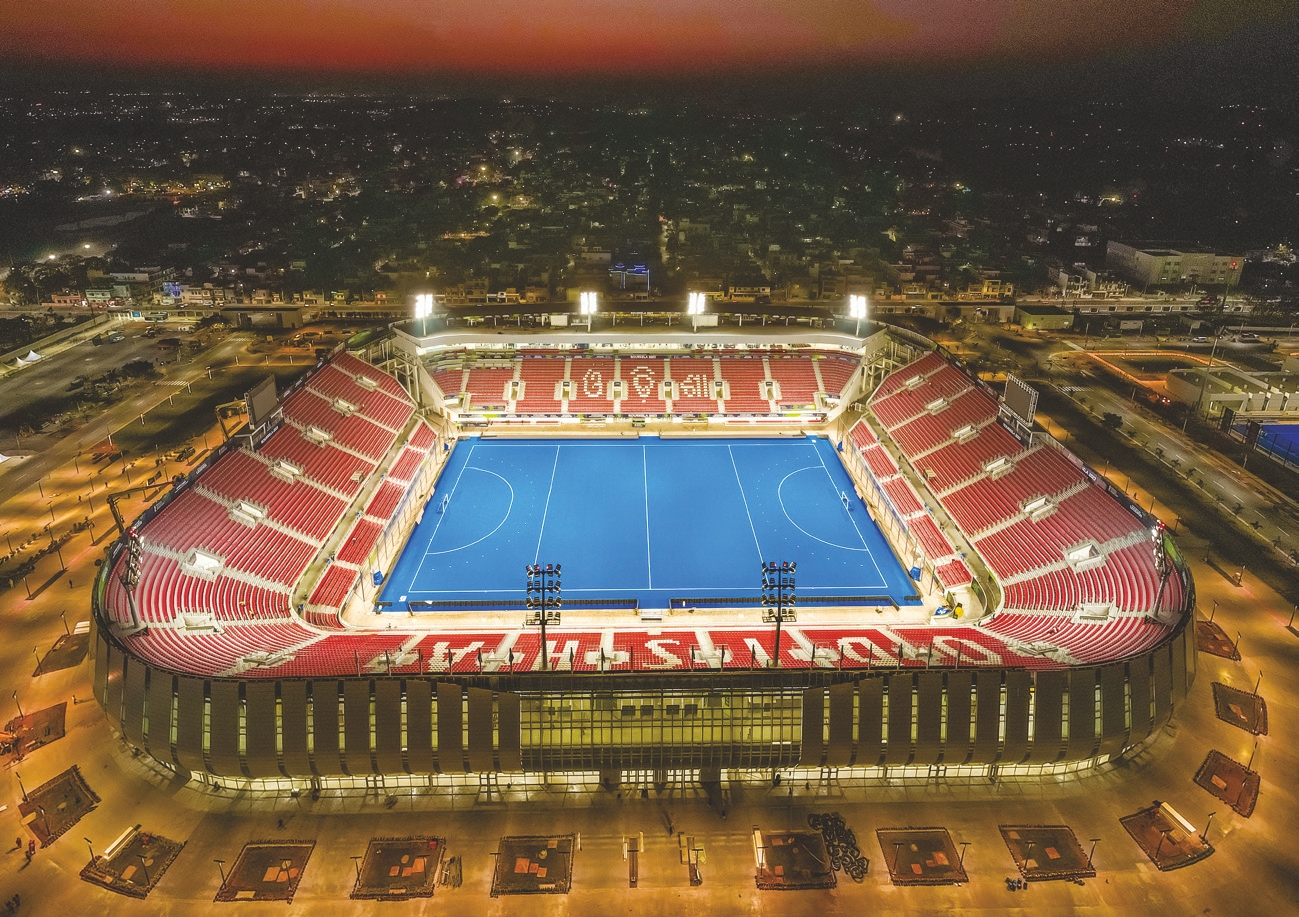
BIRSA MUNDA INTERNATIONAL HOCKEY STADIUM, ROURKELA
The dates for the International Hockey Federation (FIH) World Cup Hockey tournament scheduled to be held in Odisha, India, were announced and L&T was mandated to build an international hockey stadium in 15 months, in time for the opening match on January 13th, 2023. “If there was a project that had to be built to speed and scale, this was one,” enthuses Project Manager, K N Sabarish, recalling those hectic days. “Built from scratch, we delivered a stadium that has entered the Guinness Book of Records as the world’s largest seated hockey stadium with a total seating capacity of 20,011 and so designed that every one of those spectators can enjoy a clear and uninterrupted vision of the field of play.”The stadium was inaugurated by the Odisha Chief Minister, SJ Naveen Patnaik on January 5th, 2023.
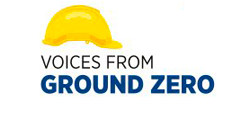

“If there was a project that had to be built to speed and scale, this was one. Built from scratch. we delivered a stadium that has entered the Guinness Book of Records as the world’s largest seated hockey stadium with a total seating capacity of 20,011 and so designed that every one of those spectators can enjoy a clear and uninterrupted vision of the field of play.”
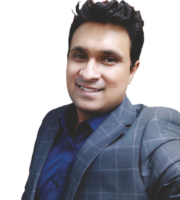
K N Sabarish
Project Manager
Located in Sundargarh district, regarded as the ‘cradle of hockey’, the Birsa Munda International Hockey Stadium is spread over 35 acres of land on the campus of the Biju Patnaik University of Technology in Rourkela. L&T’s scope included constructing the main stadium with a gallery, a hockey practice centre, the main field of play, practice field and other ancillary structures like an underground tank, a substation and pump room, external work, stain concrete along with road and landscape works and the renovation of two hockey fields at the Panposh Sports Hostel.
Many fouls to start with
The team’s trials began from word ‘go’, for the location earmarked for the stadium was where the hockey practice centre was originally situated. “Due to several overlapping issues, we had no option but to switch the location of the hockey practice centre with the main stadium that necessitated shifting the main stadium further south where the land profile was not uniform with level differences of up to 7 m,” laments Sabarish. He and his team lost three precious months due to this change in location.
“The shift in location impacted the soil-bearing capacity,” point outs Construction Manager Anirban Chakraborty, with a serious face, “because of which the isolated footings of the West Stand had to be redesigned and converted into a raft, forcing us to change the core design from a fully RCC into a steel structure to meet our deadline.” These changes also increased the quantities of concrete, reinforcement, shuttering and structural steel. “For instance, the quantity of concrete jumped from 6,500 cum to 40,000 cum, for which a captive batching plant had to be installed within the stadium site premises,” Anirban taps his forehead.
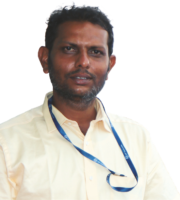
Anirban Chakraborty
Construction Manager
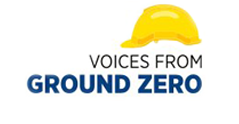

“The shift in location impacted the soilbearing capacity, because of which the isolated footings of the West Stand had to be redesigned and converted into a raft, forcing us to change the core design from a fully RCC into a steel structure to meet our deadline.”
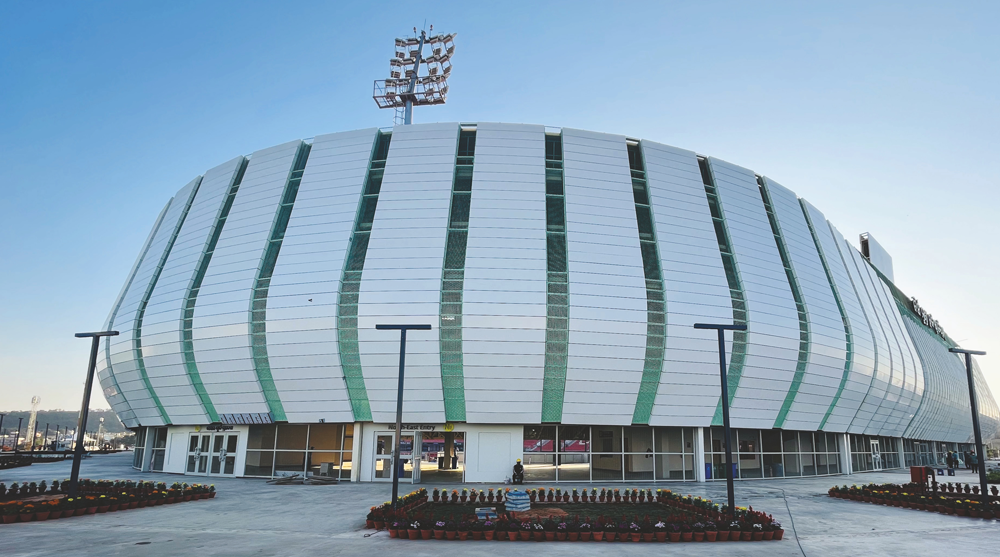
Apart from all civil structural and finishes, the team handled 4,000 MT of structural steel & deck sheeting, 17,500 sqm of façade & glazing works, placed 20,011 chairs, electricals, HVAC, fire protection and fire alarm systems, elevators, main and practice FOPs, external work with road and landscape.
For Assistant Manager (Planning), Chandradeep Etha, the dramatic and sudden increase in project scope from
Rs. 114 Crores to Rs. 285 Crores led to huge variations in quantities of non-tendered items. “We had to quickly mobilize additional manpower and resources,” he remarks with the urgency he had to act. The adverse weather significantly impacted construction schedules and site conditions. “We took everything in our stride to deliver thanks to our timely mobilization of materials and manpower and micro scheduling of work with meticulous and rigorous daily tracking,” highlights Construction Manager (Civil), Dipanjan Ghosh.
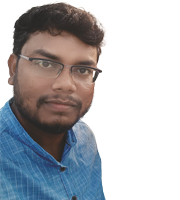
Dipanjan Ghosh
Construction Manager (Civil)
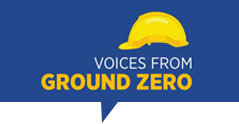

“We took everything in our stride to deliver thanks to our timely mobilization of materials and manpower and micro scheduling of work with meticulous and rigorous daily tracking.”
Executing to speed & scale
To execute a project of this scale and magnitude within such pressing deadlines, Sabarish’s choice and adoption of technology, materials and machines had to be spot on, apart from coordinating the entire spectrum of project management, across the areas of planning, mobilization, procurement, workforce management, EHS, Quality, subcontract management, and more.
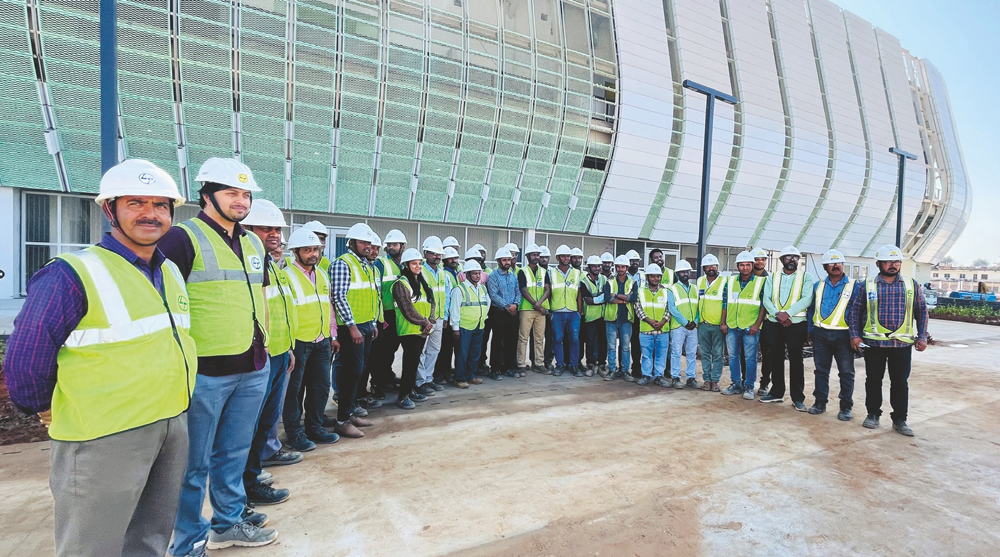
M/s Collage Design did the Design Engineering while EDRC vetted the structural stability and designed to fast-track construction with readily available sections in the market. The team fabricated 4,000 MT of structural steel, including 51,000 elements and over 1.20 lakh bolts at a specialized structural steel vendor’s factory at Bhilai, and transported these to Rourkela in phases for erection to progress, congruent with the sequence.
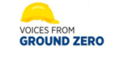

“The structural steel elements were digitally tracked for seamless erection, using heavy cranes varying from 80 to 150 tonnes, boom lifts with varying jibs of 80 ft to 150 ft and a couple of F-15 first-generation cranes to transport material from one end of the site to the other.”
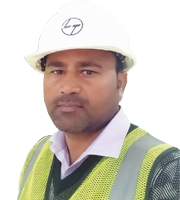
G M Khan
Construction Manager (MECH)
“The structural steel elements were digitally tracked for seamless erection, using heavy cranes varying from
80 to 150 tonnes, boom lifts with varying jibs of 80 ft to 150 ft and a couple of F-15 first-generation cranes to transport material from one end of the site to the other, informs G M Khan, Construction Manager (MECH). Assistant Construction Manager (Civil), Ujjwal Bairagi adds that to save time, the team adopted precast technology like precast drains, trenches and trench covers. “To construct the west stand, we innovated by doing staircases of eight flights with deck sheets instead of conventional formwork, allowing us to concrete the entire staircase at one go, guided by our CMPC department.”
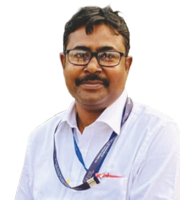
Ujjwal Bairagi
Assistant Construction Manager (Civil)
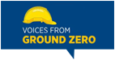

“To construct the west stand, we innovated by doing staircases of eight flights with deck sheets instead of conventional formwork, allowing us to concrete the entire staircase at one go, guided by our CMPC department.”
“We executed the MEP activities parallelly both internally and externally with different machineries to save time,” Construction Manager (ELEC), Manikandan Subramanian shares, “and used scissor lifts and boom lifts instead of scaffoldings when working at heights that apart from saving time, improved our productivity.” The team implemented a pulley rope system to expedite the cable laying from the HT substation to the LT substation and although contractually, they were to use about 3,660 cum of fly ash brick masonry, they used AAC Blocks instead to optimise time after procuring the client’s green signal.
In pursuit of their goal to complete the project on time, the team received valuable support and insights from senior colleagues such as Krishna Nand (DGM, Civil), and Govindan Kothanda Raman (Senior Construction Manager – Civil) whose unwavering dedication and collaborative spirit contributed significantly to the project’s success. Krishna precisely identified bottlenecks in finishing works and provided various alternatives while Govindan harnessed all around support to fast track the completion of the external works.
The stadium’s superstructure, the four stands, are made entirely of structural steel covered with an aluminium composite panelling having an expanded mesh to allow for natural light to pass through into the concourse area and aid air circulation too. The gallery area is designed for the spectators to watch matches without any obstruction and all the four stands can be accessed through multiple entrances, vomitory staircases and exit points for free and smooth movement. The West Stand, a VIP stand, is replete with players’ change rooms, offices, commentators’ boxes, the media centre, a separate media tribune, a CM Box, DSYS rooms, FIH/HI offices, and press conference rooms.
A few imported elements include the Astroturf pitches from Germany and the sauna system from Spain. The stadium has hot and cold plunge pools, steam and sauna rooms, a well-equipped gym, kitchens, pantries, and differently abled friendly toilet facilities while the practice centre has players’ change rooms, steam and sauna facilities, a hydrotherapy room, a well-equipped gym and first aid rooms. A total of 1500 migrant workers from across the country were involved in building this state-of-the-art arena.
The real test for the team was when a FIH delegation including the Acting President, Seif Ahmed, Chief Executive Officer, Thierry Weil, and a delegation from Hockey India comprising Committee of Administrators, Dr SY Quraishi and Zafar Iqbal, visited the site on September 7th, 2022, to inaugurate the Practice Centre (Recovery Building). That all went well strengthened the team’s resolve that their goal was nigh.
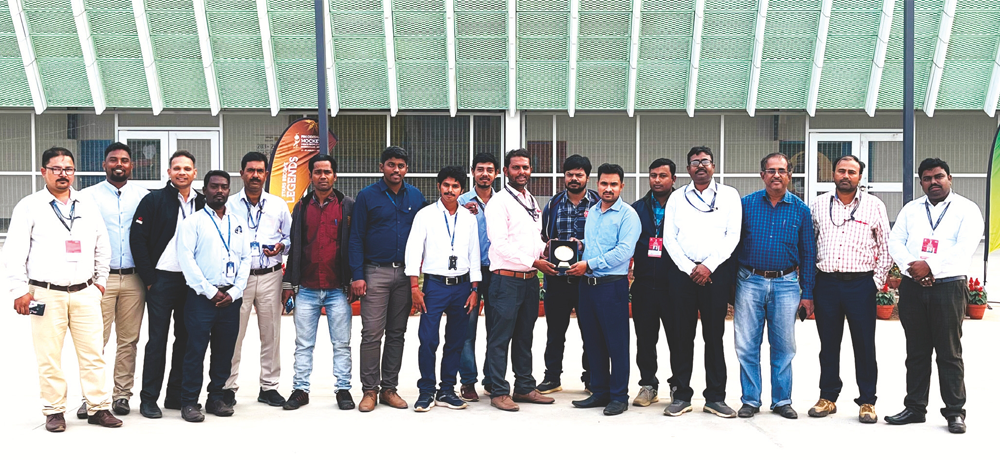
“Our success is thanks to our careful planning and corrective and necessary steps taken whenever necessary,” sums up a delighted Sabarish. “There was proper allocation of work following the work breakdown structure, and the key stakeholders and shareholders were regularly apprised of progress so that all the parties associated with the project
co-owned process. We would also like to extend our gratitude to the entire top management for their unwavering support to achieve this feat.” One could have almost heard his sigh of relief when the India-Spain match began.
PRESTIGE FINSBURY PARK
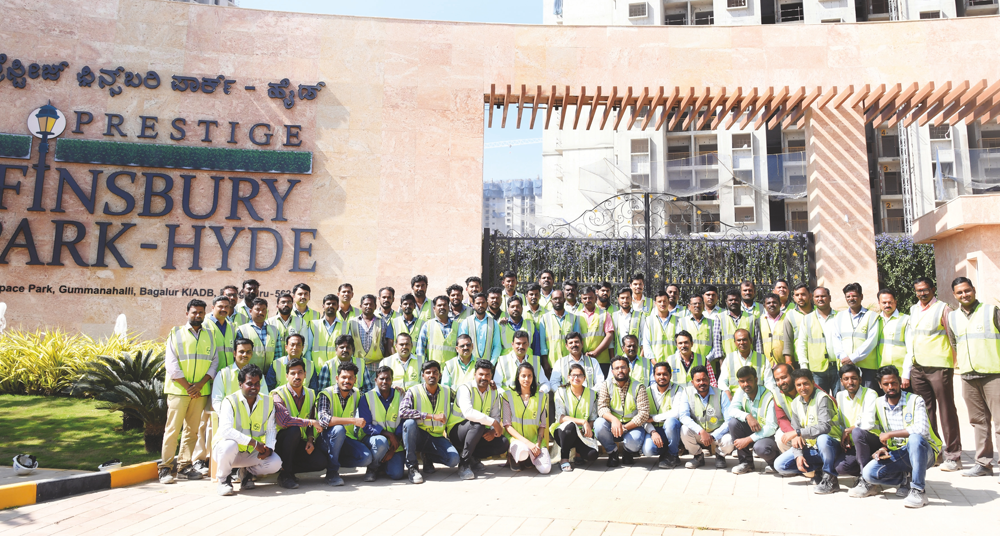
Prestige Finsbury Park, a large township destination of 25 acres situated adjacent to the Aerotropolis within the IT/Aerospace and hardware park being developed by KIADB, spectacularly re-defines the skyline, standing tall as a fitting tribute to the team behind that is putting finishing touches to it, capping a stirring saga that began on 25th Feb 2020, survived the pandemic, and navigated tough waters with a solution-oriented approach.
Prestige Finsbury Park has two independently located developments: Hyde & Regent. The Hyde, spread over 15 acres, features 2092 aesthetically designed one and two-bedrooms homes set in twelve 21-storey towers while the 10-acre Regent boasts of 958 equally aesthetically designed three-bedroom homes set in six 20-storey towers. Both developments have their own identity, approvals, amenities, and facilities.
Steering through challenges: A solution-oriented approach
“In a project site, time is money for delays can have a cascading impact on the entire timeline.” opines G Suresh, Project Director, “and so we meticulously balanced the allocation of resources, manpower, and materials to meet strict deadlines without compromising on quality, very often evolving out of the box solutions.”
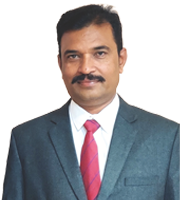
G Suresh
Project Director
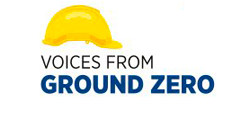

“In a project site, time is money for delays can have a cascading impact on the entire timeline, and so we meticulously balanced the allocation of resources, manpower, and materials to meet strict deadlines without compromising on quality, very often evolving out of the box solutions.”
The pandemic proved to be the sternest of tests, throwing the entire project off track. The team kicked off with just
27 workmen but soon mobilized 500 more in 3 months through careful planning, rigorous follow ups with vendors and boosting the morale of the workmen.
Another challenge was the second iteration of the initial setting of the aluminium shutters. Although the first iteration of the towers was delayed due to the labour shortage during the pandemic, the client was confident that the team could deliver without any time extension. Deciding to do the initial setting on the floor print to save time, they deployed
3 agencies for the exercise at the floor level of each tower and completed the initial setting of 9 towers in 126 days.
By implementing Lean Construction practices, extensively utilizing the last planner system, promised percentage completion and big room meetings, the team successfully aligned the sub-contractors with the project team, and built trust by resolving issues within a week’s time. Agencies and sub-contractors were pre-qualified and screened for skill level identification, all the workmen were screened to evaluate their skill category and a dedicated team was deployed for post pour levels and clearances.
“The construction of an STP 15 m below ground level at Hyde and Regent close to the main tower of 21 floors was tricky,” says Senior Construction Manager (Civil) and Planning Head, M.G. Vijayakumar, “but we adopted a proactive and organized approach by ensuring allocation of dedicated resources, including labour, equipment, and materials to complete the task within 5 months, before the monsoon.” He elaborates that bulk material requirements were addressed well in advance, procured on time, and delivered to the required spot to minimize wastages. Concrete and rebar tools further reduced excess wastage.
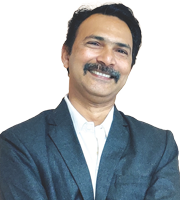
M.G. Vijayakumar
Senior Construction Manager
(Civil) and Planning Head
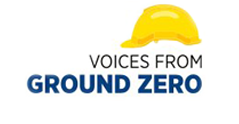

“The construction of an STP 15 m below ground level at Hyde and Regent close to the main tower of 21 floors was tricky, but we adopted a proactive and organized approach by ensuring allocation of dedicated resources, including labour, equipment, and materials to complete the task within 5 months, before the monsoon.”
Overcoming challenges only fuelled the team’s resolve to get to the finish line. A 2.5 km long retaining wall was constructed just 1.5 km away from the property line with 8 m excavation to avoid shoring after approaching and receiving permission from the neighbours for Right of Use (RoU) of land for a short period of time. By deploying the workforce in both directions and working on one bay of slab of the retaining wall at a time, they completed the
task in time.
Completing all the finishing activities 4 months from structure completion was a tall ask as the scope of work included Gypsum, tiling works and handrailing. Soldering on, the team effectively collaborated with the nominated agencies to complete the work sequentially preventing delays. “Our approach was always proactive,” reminds Suresh, “identifying bottlenecks, addressing short falls, and keeping the client in the loop throughout.”
Finishing Head, C.P. Prasanna Kumar, continues the story. “We engaged Front line Supervisors to take care of
activities like water proofing, Gypsum and so on, deployed a vendor for each tower for the tiling works that increased our productivity and reduced tile wastages and thus completed 270 flats of Gypsum and 250 flats of tiling work
each month.”
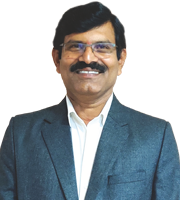
C.P. Prasanna Kumar
Finishing Head
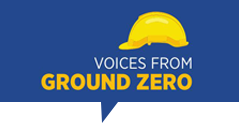

“We engaged Front line Supervisors to take care of activities like water proofing, Gypsum and so on, deployed a vendor for each tower for the tiling works that increased our productivity and reduced tile wastages and thus completed 270 flats of Gypsum and 250 flats of tiling work each month.”
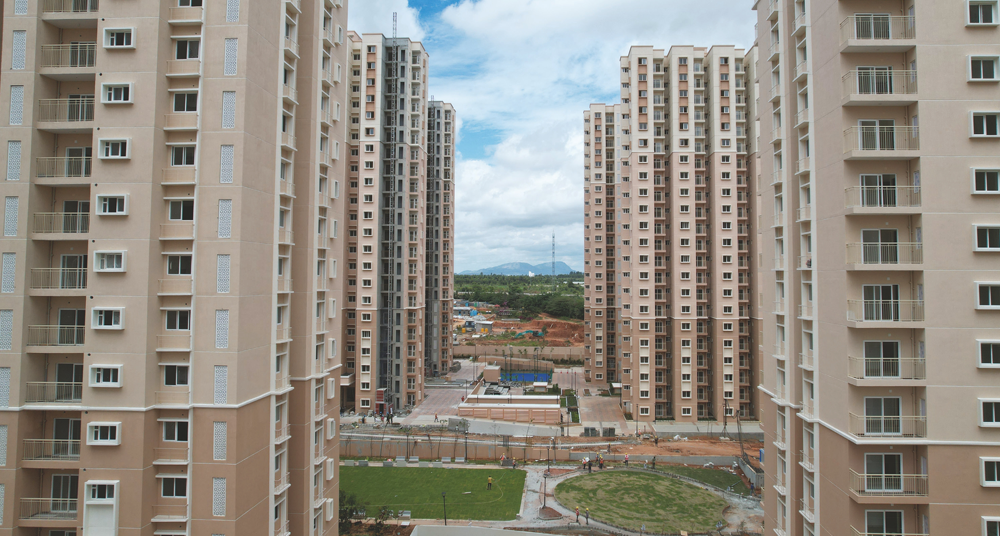
The priority for Quality Head, G A Raghavendra, is for the team to uphold the highest standards of Quality at every phase of the project. “We have implemented a comprehensive Quality Management System tailored to the unique requirements of our project that guides our quality planning, control, and assurance efforts.” He cites the 2.4 kms long retaining wall casted with monolithic starter with all vertical joints and trapezoidal grooves for watertight basements, as an example of their sterling efforts. Apart from this, they ensured that necessary surface preparation was completed on external surfaces before removing the external brackets.
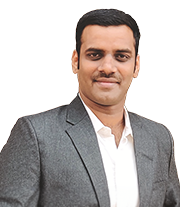
G A Raghavendra
Quality Head
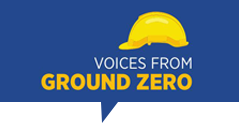

“We have implemented a comprehensive Quality Management System tailored to the unique requirements of our project that guides our quality planning, control, and assurance efforts.”
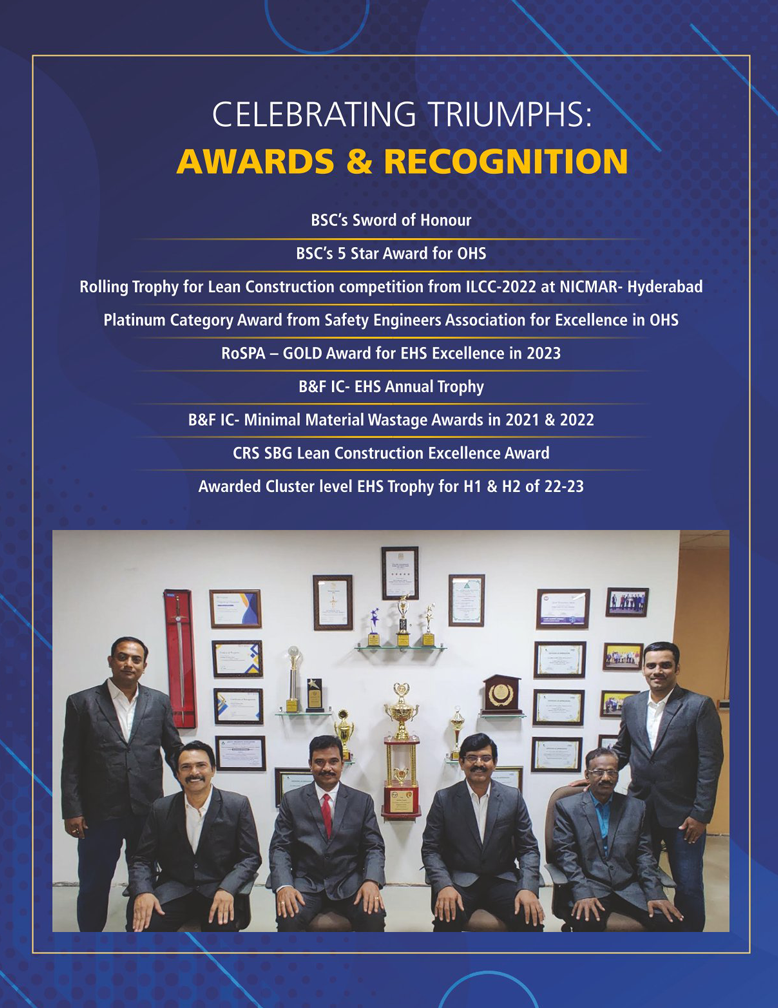
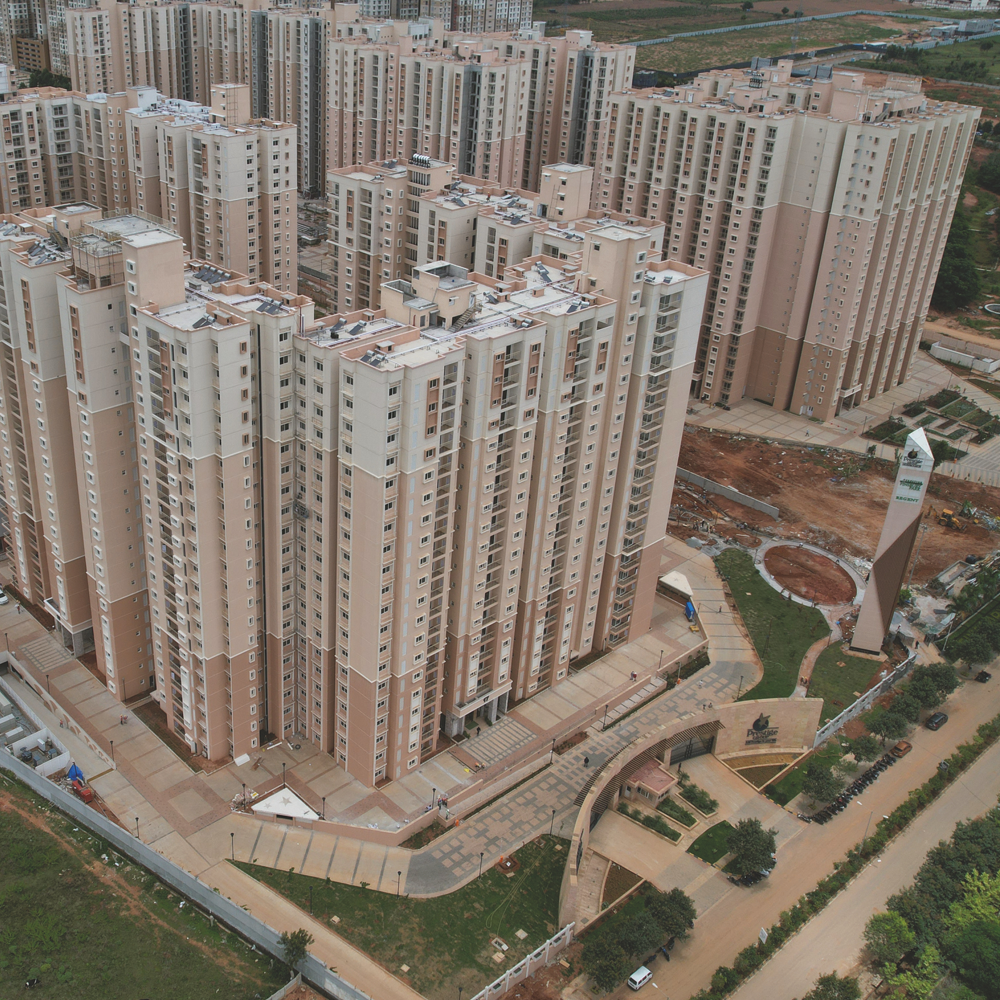
Cruising to the finish line with an enviable strike rate
“Our strike rate of completing 2.38 flats in a day is inclusive of flats, basements, and external development works.
(3050 flats /1281 days = 2.38 flats),” says G. Suresh with a bright smile “We are in the last leg and will be completing the project 7 months ahead of the RERA deadline,” he adds with visible excitement.
At the end of the day, collaborative spirit, unwavering commitment, and relentless pursuit of excellence of both these B&F teams have defined their success.