RAILWAY PROJECTS TRACK PROGRESS, PROTECTING MARGINS
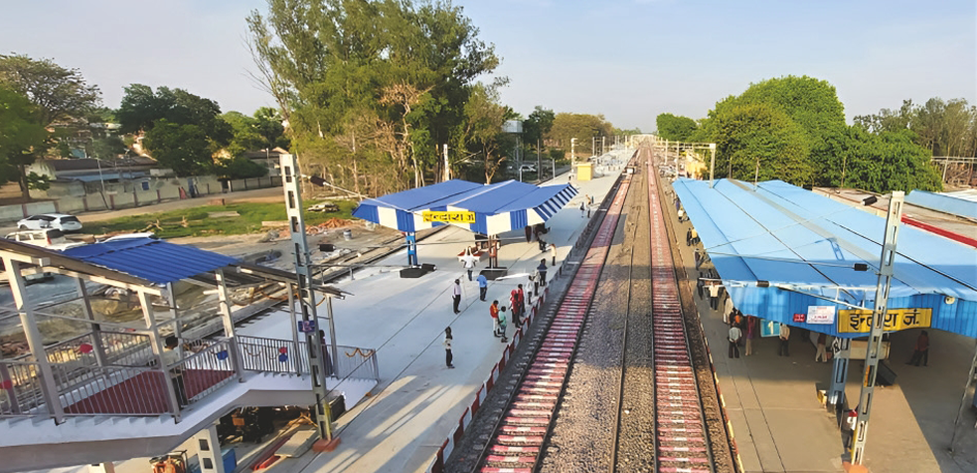
RVNL ARJ BTT PKG-2 DOUBLING PROJECT
The RVNL ARJ BTT Package – 2 Project aims to augment the capacity of the Indian Railways between the Aunrihar Junction, near Varanasi and the Bhatni Junction, near Gorakhpur. The team’s scope covers Pway, OHE, S&T works (160 tkm) including Ballast supply (4.2 lacs cum). Once completed and commissioned, the project will provide seamless connectivity between Varanasi and Gorakhpur, two major stations that will in turn trigger economic development of this stretch of Eastern Uttar Pradesh, bordering Bihar.
The team led by Project Manager, Sudheer Rayapureddy, is committed to deliver their project in time with a fair margin and with just one third of execution remaining, they are confident that they can deliver. “Having achieved 66% of financial progress, we have successfully kept our margins intact over a period of 23 months, addressing all the challenges of cost overruns by improving our efficiency,” he says with steely resolve.
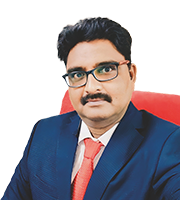
Sudheer Rayapureddy
Project Manager
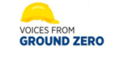

“Having achieved 66% of financial progress, we have successfully kept our margins intact over a period of 23 months, addressing all the challenges of cost overruns by improving our efficiency.”
His Planning Head, Ravi Mehrotra, Engineering Manager (ELEC), quickly supplements his PM’s statement sharing their progress achieved across various fronts. “In Ballast Supply, we have completed 3.75 lakhs out of the targeted 4.2 lakhs, we have commissioned 32 tkm out of 150 tkm, OHE commissioning has reached 40 tkm out of 160 tkm and we have completed S&T commissioning of 4 of the 12 stations in the contract.”
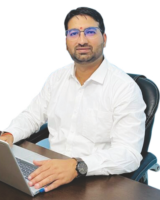
Ravi Mehrotra
Planning Head,
Engineering Manager (ELEC)
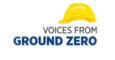

“In Ballast Supply, we have completed 3.75 lakhs out of the targeted 4.2 lakhs, we have commissioned 32 tkm out of 150 tkm, OHE commissioning has reached 40 tkm out of 160 tkm and we have completed S&T commissioning of 4 of the 12 stations in the contract.”
Doing the small things right for big rewards
By targeting high value items with short delivery timelines, the team has been able to maintain their cashflow, like for the supply of Ballast that constitutes almost 28% of the project value. In fact, the team has improved their margin in ballast supply by transporting it on railway rakes in long lead areas and by road in short lead areas, and reduced wastage by giving back-to-back orders to vendors, in line with their sales BOQ. “Ensuring timely approvals of Proposals/HPC approvals, POs and maintaining the cashflow of the Ballast, we have maintained our cashflow,”
Ravi smiles reassuringly. Timely and effective material planning has ensured smooth commissioning and 70% of the invoicing has been completed against material delivered till date.
“With efficient and strategic work planning with the execution team and site management, we have broken down the works into smaller patches, activities, and priority tasks, and have allocated them to different vendors to initiate the work in the available formation within the budgeted time and cost,” shares Senior Engineer (Civil), Vipin Kushwaha, referring to another smart MO.
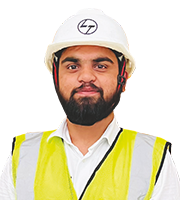
Vipin Kushwaha
Senior Engineer (Civil)
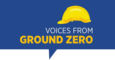

“With efficient and strategic work planning with the execution team and site management, we have broken down the works into smaller patches, activities, and priority tasks, and have allocated them to different vendors to initiate the work in the available formation within the budgeted time and cost.”
To accelerate progress, the team finalized the OHE drawings to initiate OHE foundation and mast erection work early, and meticulously micro planned each OHE activity including manpower and materials availability, before and during NI.
“When executing critical OHE work activities such as OHE wiring, bracket adjustments, OHE modifications and ATD adjustments, we take extra safety precautions like using a 25 kV discharge rods, anti-fall arresters, and full-body harness belts,” informs Engineer (ELEC), Mohammad Shahnawaz Alam. “I played a crucial role to develop the OHE mast reverse deflection measurement process, to accurately determine the grouted OHE mast reverse deflection at site,” he says, proud of his contribution and mentions an OHE Progress Master Sheet, to consolidate data on OHE work activities for the entire project to facilitate daily progress monitoring, aid sub-contractor and client billing, and provide a secure backup for comprehensive record-keeping.

“When executing critical OHE work activities such as OHE wiring, bracket adjustments, OHE modifications and ATD adjustments, we take extra safety precautions like using a 25 kV discharge rods, anti-fall arresters, and full-body harness belts.”
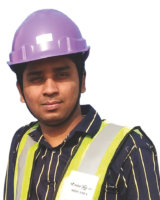
Mohammad Shahnawaz Alam
Engineer (ELEC)
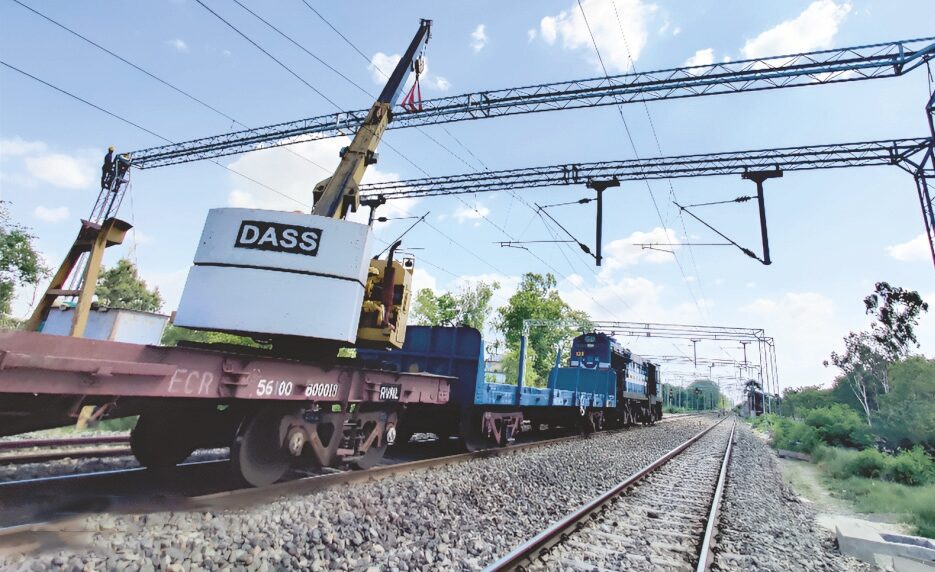
A huge safety concern is that the project runs parallel to the busy Indian Railway (IR) line and much of the OHE activities are being executed during specified power and traffic block periods, for limited periods of time granted by the IR authorities.
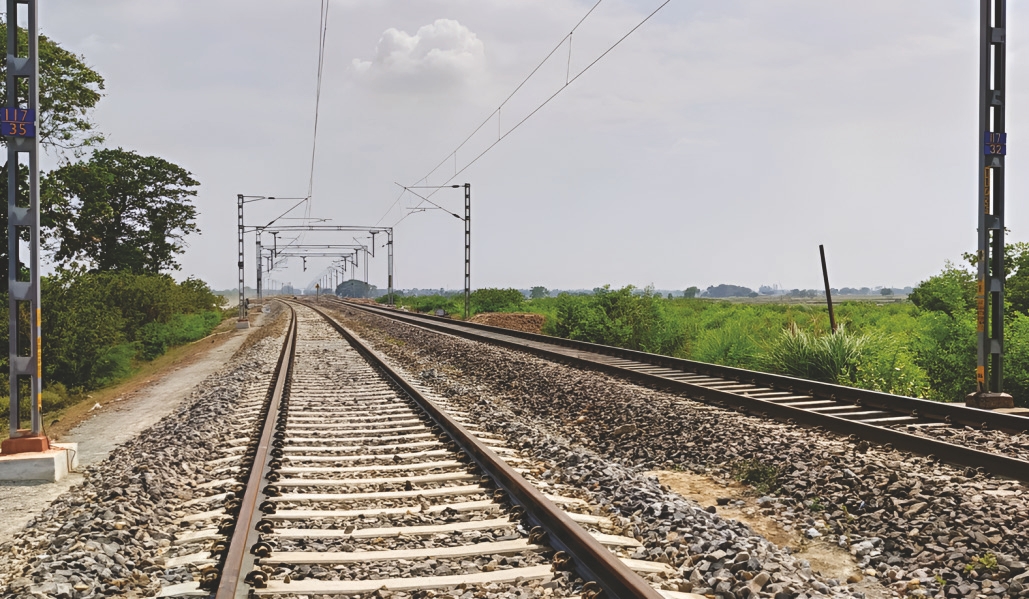
Building bridges with the customer
A key reason for the team’s impressive progress has been their strong relationship with the Client, RVNL. It did not start on the right foot though owing to RVNL’s inaccessibility and decision to descope a portion of the project even before mobilisation. “Gradually, we were able to build bridges with RVNL by creating proper channels of communication and documentation, taking them along our journey,” shares Assistant Manager (Civil), Aditya Chopra. Sudheer agrees, adding, “Not only for their constant support and cooperation but also for speedy resolution of our EOTs and claims.”
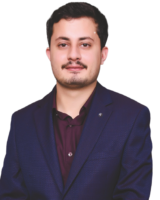
Aditya Chopra
Assistant Manager (Civil)
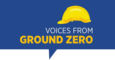

“Gradually, we were able to build bridges with RVNL by creating proper channels of communication and documentation, taking them along our journey.”
He will also agree that despite the going being tough with challenges on the work front from the Client’s side, parts of his project have already been commissioned, with work in full swing at all the available stretches. “Our objective is very clear,” Sudheer emphasizes. “To exhaust all the available work fronts, keep material and manpower ready in advance by planning meticulously for material planning is key, considering that our project involves Pway, OHE and S&T works, to maintain both financial and physical progress.
IRCON NFR RAILWAY
ELECTRIFICATION PROJECT
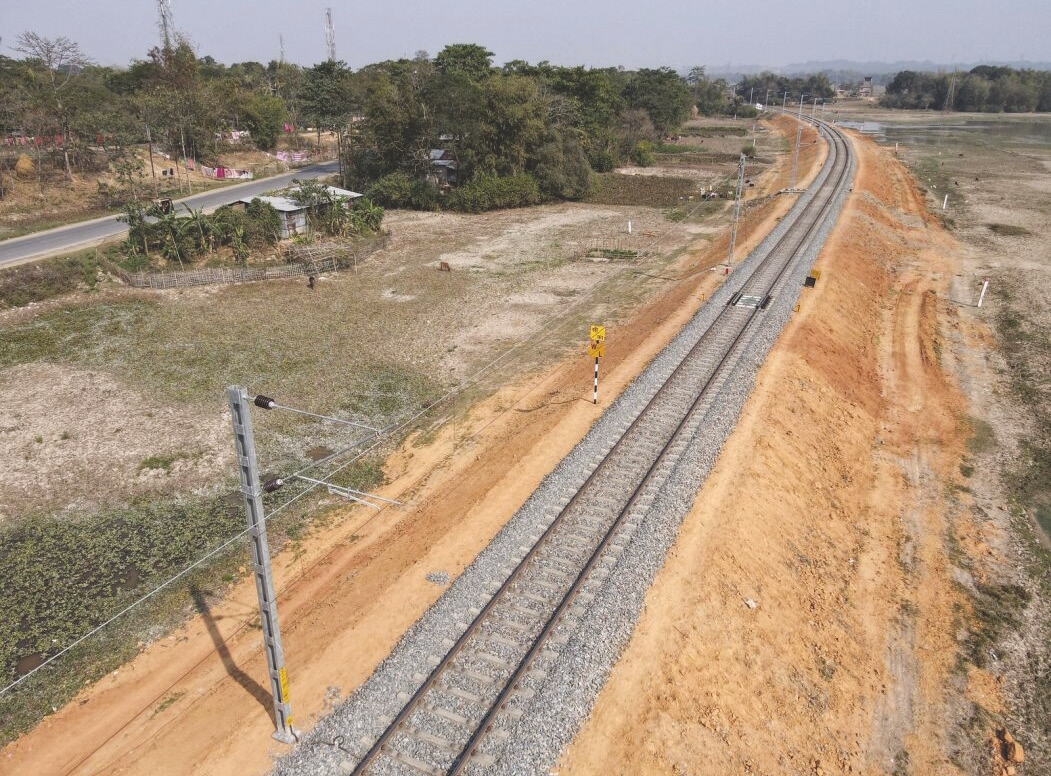
As part of the Indian Railways mission to achieve 100% electrification, the IRCON NFR Railway Electrification project team of the Railways SBG has been mandated to electrify 535 Rkm (678 TKM) from Silchar-Agartala-Sabroom, KathkhalBhairabi, and Arunachal-Jiribam in lower Assam and Tripura, touching the Bangladesh border, with some portion of works in Manipur and Mizoram. India’s northeast always evokes images of unforgiving terrains,
difficult-to-access locations, heavy rainfall, floods and young Project Manager, Debashis Manasranjan Aich, has had to face challenges by the trainloads.
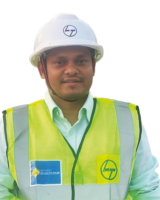
Debashis Manasranjan Aich
Project Manager
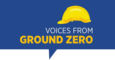

“I appreciate my team’s timely invoicing, timely procurement of high value materials like copper, steel, cables, and such like with cashflow management being the silver lining to improve working capital.”
“Many of our locations in the alignment are in remote, hilly terrains with unstable ground conditions that pose huge logistic challenges to move men, material, machinery and equipment,” begins Debashis, “and the heavy annual rainfall that Assam and Tripura receives only add to our problems.” Rains can damage infrastructure, increase maintenance costs and delays but perhaps the bigger problem is that it wipes away months of activity leaving the team only a small window from October to end-March for construction. To top all these is the difficulty to find skilled workmen in the region, necessitating a training programme to develop a local workforce, and doing everything possible to retain the migratory workmen.
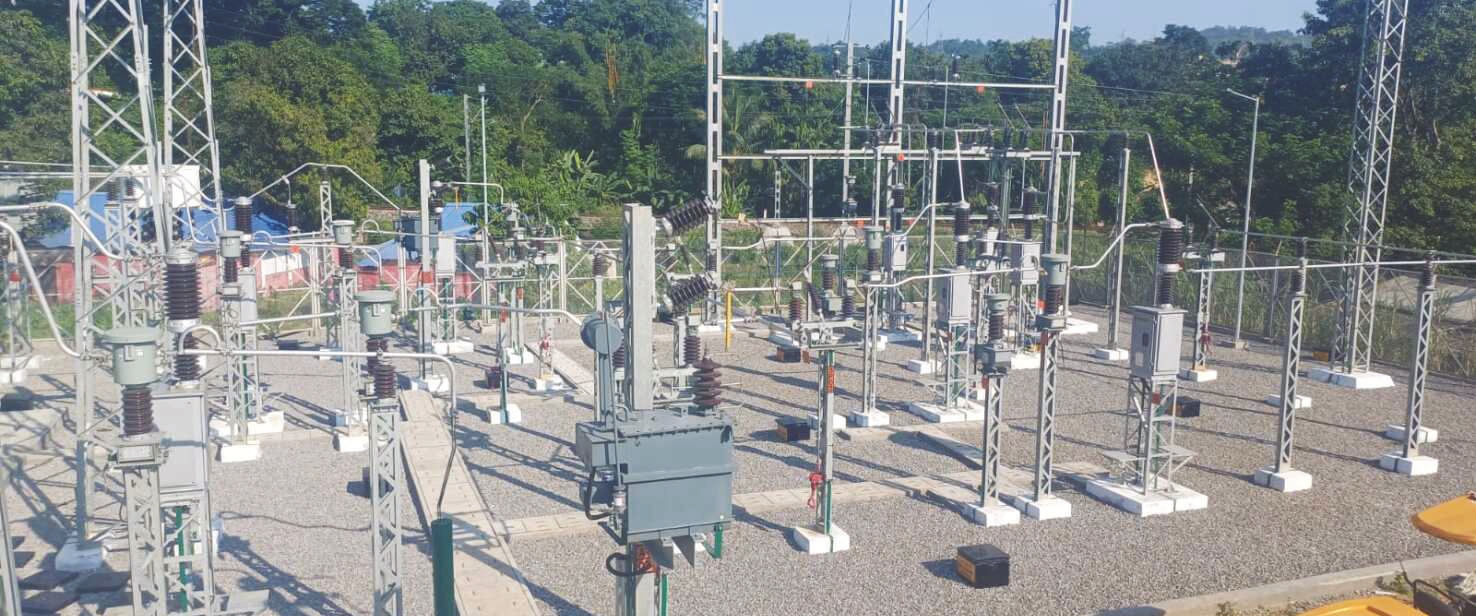
However, despite this welter of challenges, the team has held together, and performed, coordinating among themselves and continuously learning from our mistakes. “We network with our other ongoing projects in the northeast to mobilize resources and keep all our stakeholders and the Client involved that fosters trust and aligns everyone towards a common goal,” remarks Civil Head – Suvajit Gupta, Senior Construction Manager (Civil).
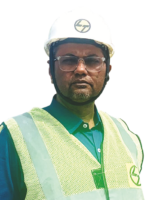
Suvajit Gupta
Civil Head
Senior Construction Manager (Civil)
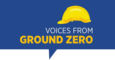

“We network with our other ongoing projects in the northeast to mobilize resources and keep all our stakeholders and the Client involved that fosters trust and aligns everyone towards a common goal.”
By adhering to responsible practices, cultivating a positive team culture and continuously planning resources, the team has achieved much: having completed 75% of the OHE foundation works, around 200 TKM OHE pre-wiring & post wiring activities, 14 stations, signalling modification works, completed & tested one TSS, seven SP/SSP works, completed four TSS and eight SP/SSP civil works, all within 10 months of working sessions. “This has given our customer the confidence that we will be able to complete this entire project in this financial year itself,” says Debashis, with an air of quiet confidence. “I appreciate my team’s timely invoicing, timely procurement of high value materials like copper, steel, cables, and such like with cashflow management being the silver lining to improve working capital,”
he says and adds with a chuckle, “My earlier learning from different EPC projects has helped me to brainstorm and invoice low hanging items.”
Precise planning: For an EPC project with various types of works from design to final delivery, the customer seeks a well-crafted project plan that forms the bedrock of efficient execution. “By meticulously outlining the project’s scope, objectives, milestones, and timelines, we have established a clear roadmap for the entire exercise, incorporating detailed work breakdown structures (WBS) that helps to segment tasks, identify dependencies, and prioritize critical activities,” says Planning Head- Anirban Chatterjee, Assistant Manager (ELEC) shrewdly.
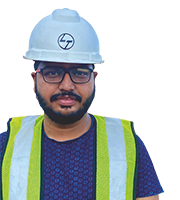
Anirban Chatterjee
Planning Head, Assistant Manager (ELEC)
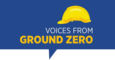

“By meticulously outlining the project’s scope, objectives, milestones, and timelines, we have established a clear roadmap for the entire exercise, incorporating detailed work breakdown structures (WBS) that helps to segment tasks, identify dependencies, and prioritize critical activities.”
The team’s decision to change the designated PSI locations has saved them a major chunk of earth filling quantity and subsequently cost saving in the area development works.
Careful resource mobilization & procurement: Focused on timely and well-coordinated resources, the team put up temporary infrastructure to kickstart activities and coordinated with suppliers to ensure ready availability of essential material and equipment at site, to avoid disruptions. The only way to reach material to site is by road that is unpredictable owing to landslides and other disturbances forcing them to evolve a robust procurement strategy to streamline acquisition of resources. A centralized procurement system has enhanced transparency, easing the process to track orders, approvals, and invoices.
Engineer (Civil) Malay Das’s effort to address the perennial problem of mobilizing skilled labour is note-worthy, developing and training local workers and deploying subcontractors in various civil departments. “Almost immediately, our execution works went into higher gear and most of our works in Assam is very close to completion,” he says with josh.
No compromise on safety & quality: EHS practices have been embedded into project culture to ensure the well-being of workers and prevent potential accidents. “Our stringent safety protocols and regular audits identify hazards, foster a secure work environment and ensure that all adhere to our safety regulations,” stresses EHS In-charge, Sushen Rath. Regular inspections, testing, and adherence to industry best practices minimize defects and rework, ensuring the longevity of the electrification infrastructure.
Keeping spirits up: Recognizing that clear role definition and allocation of responsibilities mitigate confusion and redundancy, the team leadership has opened and maintained effective communication channels to keep the workforce engaged and informed. “Continuous training enhances skillsets and cultivates a culture of improvement, enabling the workforce to contribute more effectively to project objectives,” mentions Debashis. “Seamless communication between the project teams, stakeholders, and contractors fosters alignment and with regular meetings, progress updates, instant resolution of issues, and goal synchronization, we are pushing forward.”
Finally, by proactively identifying potential risks and formulating contingency plans, the team has been successfully coping with unforeseen challenges, while regular risk assessments and updates ensure adaptability and prevent disruptions.
For Debashis, teamwork is the potion that is driving his project forward, “and, of course, the collaboration between the various stakeholders, selection of the right people at the right place for the right job,” he effectively sums up.
MUMBAI METRO 10B & 10C PROJECTS
The 33.5 km Aqua Line 3 of the Mumbai Metro aka Colaba-Bandra-SEEPZ Line currently under construction, when completed will be Mumbai’s first underground metro line with 27 underground stations and one at-grade station. It will run from Navy Nagar in Mumbai’s far south to Aarey Depot in the city’s north-centre, and include connections to other metro lines, the monorail, suburban rail, inter-city rail, and the Mumbai Airport. It is expected to decongest the roads and reduce the load on the Western Railway running between Churchgate and Bandra.
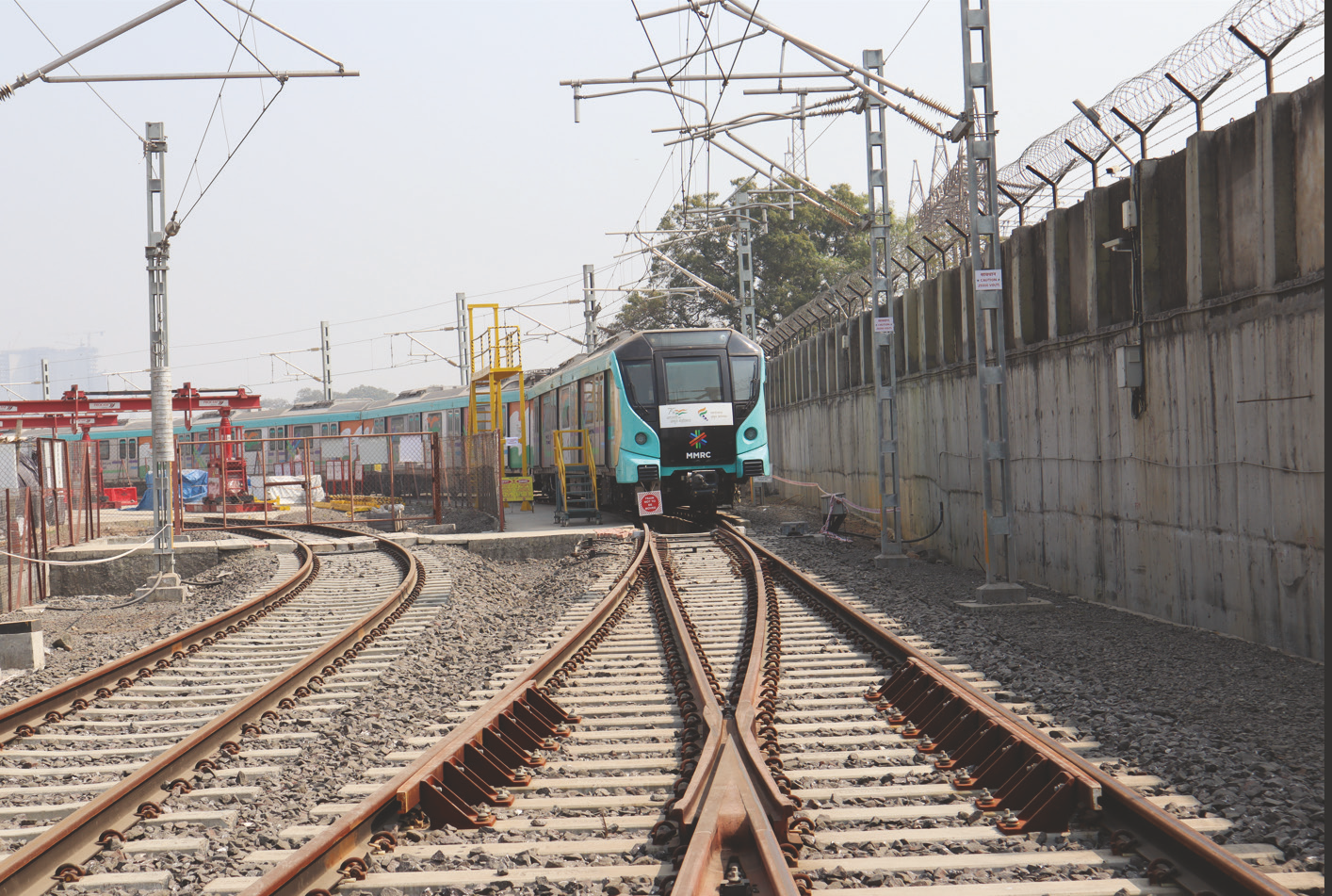
The Railways SBG is executing the 10B & 10C projects and the mandate for Brij Mohan Sharma, Cluster Manager (West), and leading the project and his team is to install the LVT (Low Vibration Track) for the complete line and finish the project to quality, and contracted timelines maintaining, and if possible, improving their profit margins.
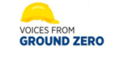

“We will be using LVT (High Attenuation) technology for the first time in India, that will not only improve the ride quality but also protect the 100+ years old heritage structures and buildings on the surface from vibrations.”
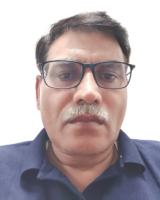
Brij Mohan Sharma
Cluster Manager (West)
Adopting new technology and making it work
“We will be using LVT (High Attenuation) technology for the first time in India, that will not only improve the ride quality but also protect the 100+ years old heritage structures and buildings on the surface from vibrations,” informs Brij, smiling as he shares the saga about procuring the LVT blocks from Sonneville, Switzerland.
Although initially as per the bidding considerations, the LVT concrete blocks were a part of the imports, after the contract was awarded and post long discussions & deliberations with Sonneville, the team took a conscious decision to manufacture the blocks in India. A state-of the-art factory was set up at Wadala, and as Planning Manager, Rohit Mali, Construction Manager (Civil) highlights, “Our decision to manufacture the LVT booted blocks saved the project a lot of money, and since the pandemic hit the world soon after, our decision proved to be an absolute boon.”
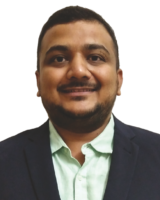
Rohit Mali
Planning Manager,
Construction Manager (Civil)
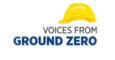

“Our decision to manufacture the LVT booted blocks resulted in significant cost savings, and since the pandemic hit the world soon after, our decision proved to Rohit Mali b an absolute boon.”
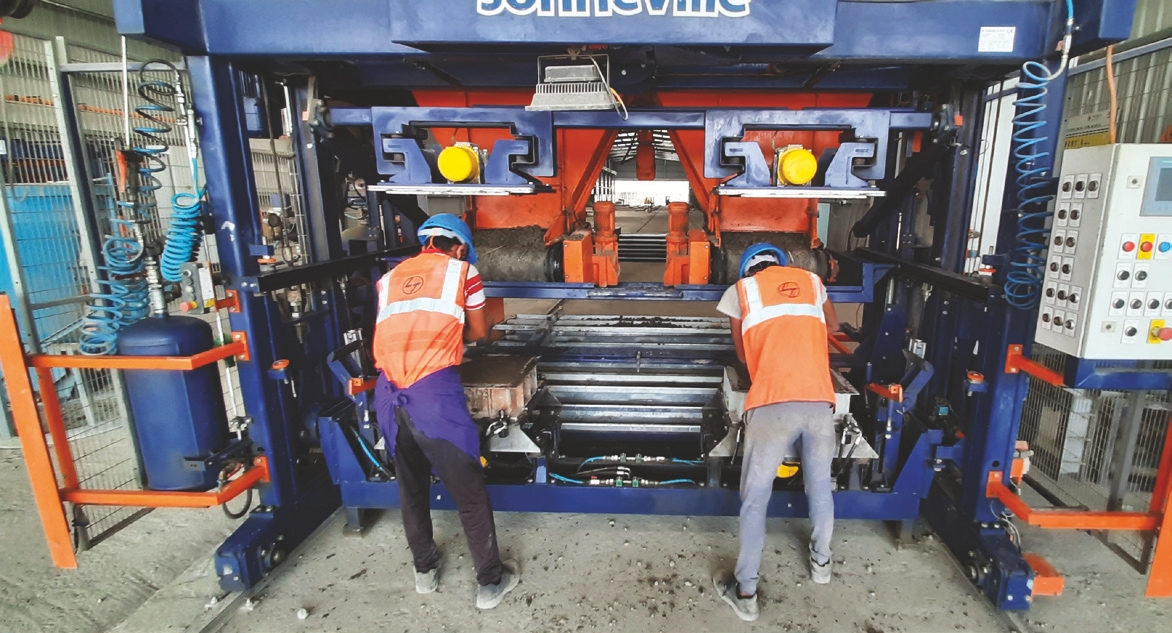
Technology provider, Sonneville’s benchmark was to manufacture 400 LVT sleepers per day with two machines. “We improved our efficiency to manufacture 600 sleepers per day using our CSTI-trained manpower,” shares a pleased Factory Manager, Amit Shukla, Senior Construction Manager (MECH), “to complete the targeted production ahead of time, saving on IDC in the process.”
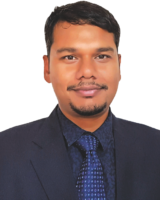
Amit Shukla
Factory Manager,
Senior Construction Manager (MECH)
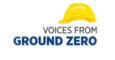

“We improved our efficiency to manufacture 600 sleepers per day using our CSTI-trained manpower to complete the targeted production ahead of time, saving on IDC in the process.”
The LVT slab technology is without steel rebars in the track bed. Initially, however, the client was not ready to adopt the technology without steel and forced the team to go with steel for around 300 m. “However, after deliberations with our design team and third-party certifications, we successful moved ahead without steel mesh or rebars in the track slab, which led to substantial cost reduction,” shares a satisfied-looking Mohammad Asif, Senior Engineer (Civil).
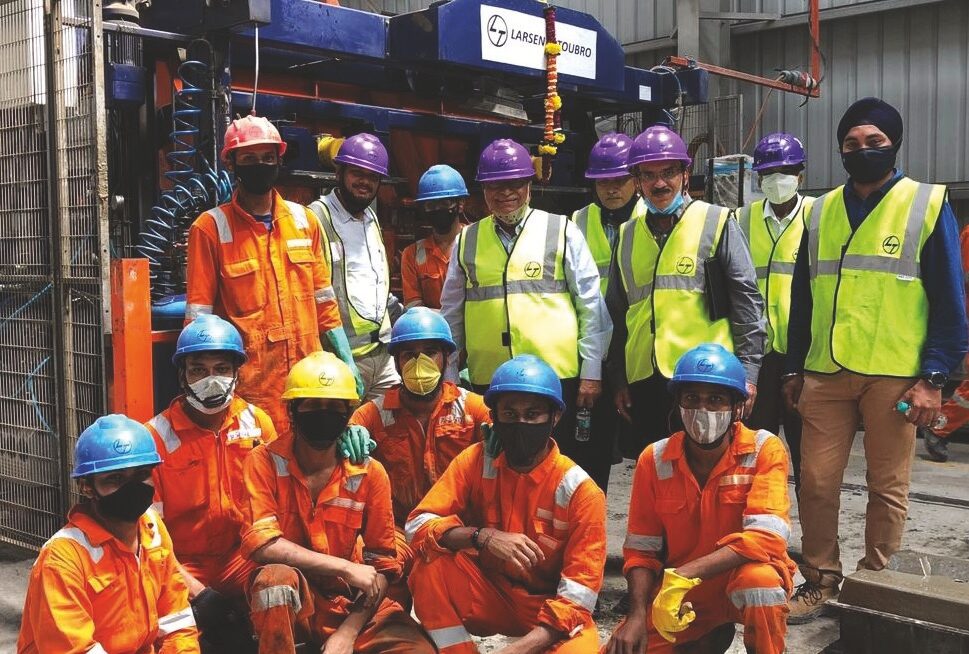
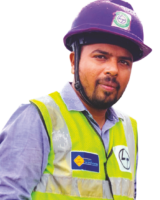
Mohammad Asif
Senior Engineer (Civil)
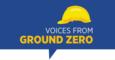

“However, after deliberations with our design team and third-party certifications, we successful moved ahead without steel mesh or rebars in the track slab, which led to substantial cost reduction.”
Solving the Aarey Depot issue
Right after the contract was awarded in November 2019, the Maharashtra Government cancelled the Aarey Depot which was part of the contract. Having already placed orders on major suppliers for track material, the team took a strategic decision not to cancel their POs till the validity dates. In hindsight, this proved to be a wise call for in June 2022 when Maharashtra Government restored the Aarey Depot, the team successfully convinced the Client to compensate them in the form of PV for supplies till date, whereas they were able to procure at old rates: a significant step towards increasing the project’s EBDITA.
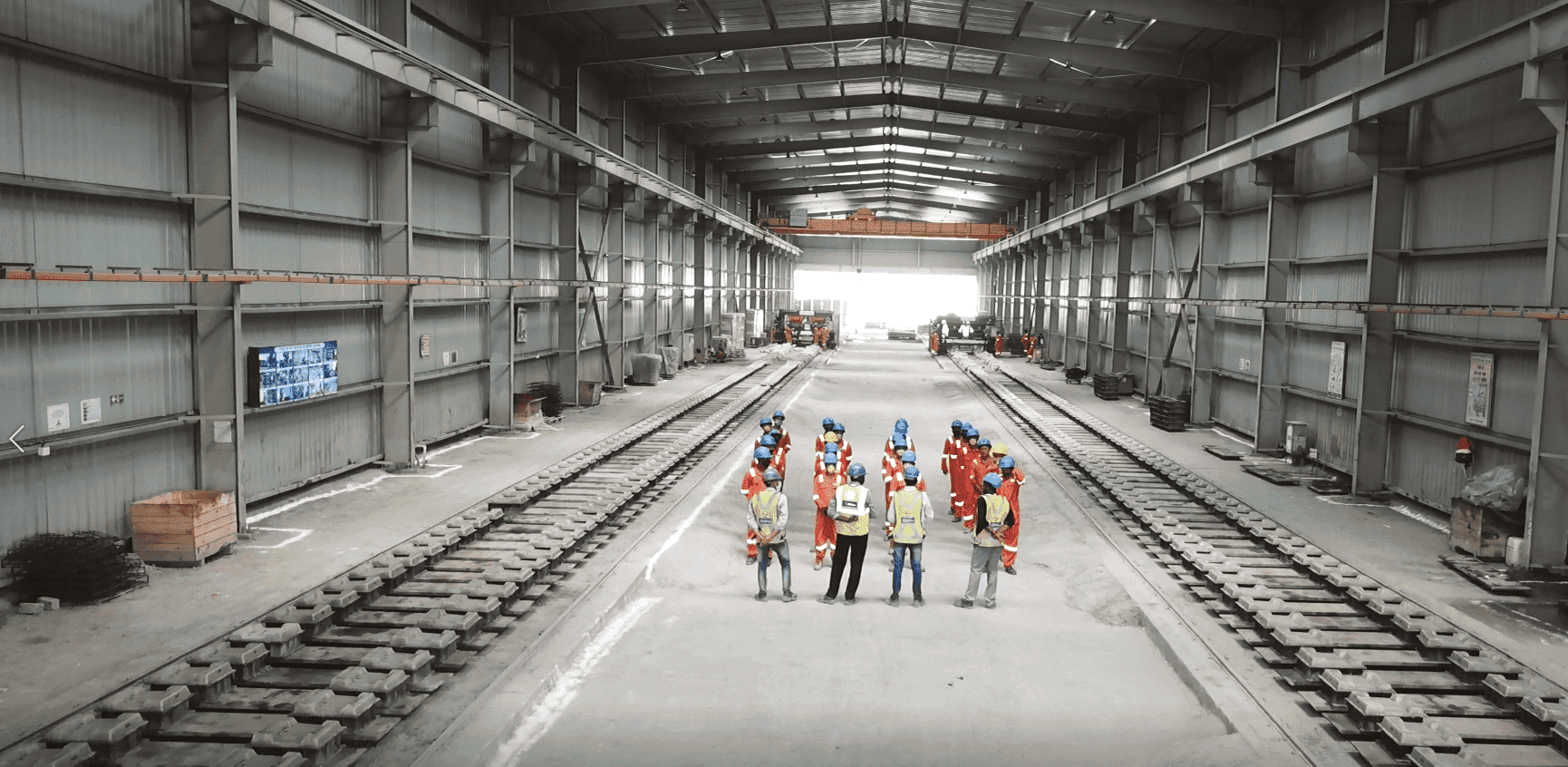
Managing a difficult client
The Mumbai Metro Line-03 is divided into two packages: 10B & 10C. “The client considered these as two separate projects whereas we were operating them as one to share common facilities and expenses,” highlights Brij. “The client kept demanding for separate project offices and staff for both projects, but we stood firm on our decision of having a single project office, explaining that it was better suited to address issues under a single umbrella.” After much discussion and deliberations, the client conceded, and the team was able to improve their margins, albeit slightly, over ACE.
Maintaining operational efficiency
Normally, track installation is through subcontractors and initially, the team was unaware of the productivity they could expect from the new LVT technology, and hence adopted a mode of installation with the P&M in the subcontractor’s scope. After streamlining the installation process, they decided to change tracks and bring P&M within their scope, leaving only labour in the subcontractor’s. The wisdom of their decision soon became apparent. “With the first model, the cost per tkm (with P&M) was on higher side; however, with the adoption of the second model, the cost of installation (without P&M) came down substantially,” points out a pleased Amit.
The ballast for any railway project is sourced and stacked in heaps at site, measured, tested, and taken for execution. “We convinced the client to put the ballast directly on to the formation on the track bed as our payment was in track meters hence saving cost of storing and rehandling the ballast,” grins Rohit.
“Apart from sweating our assets to improve operational efficiency, we have set stringent benchmarks of diesel usage for hired assets,” mentions Brij. If the company’s norm of fuel for forklift is 3.0 LPH, they have set a norm of 1.5 LPH, to save on fuel. “Every bit matters if the aim is to keep improving our bottom line,” he sums up with a determined set to his features.