M&M PROJECTS MINE MORE VALUE TO
DRIVE EFFICIENCY

BLAST FURNACE #5 FOR JVML BALLARI
The Blast Furnace #5 Project is part of the 18 MTPA expansion roadmap of JSW Vijayanagar Metallics Limited, Ballari, at their steel works facility.
L&T’s Minerals & Metals SBG is executing this arduous project that involves over 1 lakh cum of concreting works, 50,000+ MT of structural supply and erection works, and over 10,000 MT of equipment erection along with E&I Works. Aware that efficiency directly impacts project timelines, budgets, and overall quality, the team under the able leadership of Project Director, R Umasathiyan, has remained focused on completing the project on time and to profit.
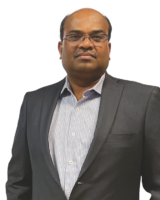
R Umasathiyan
Project Director
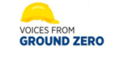

“Faced with uncertainties, we took a strategic decision to delay mobilizing critical resources, using the initial period to establish a greenfield fabrication yard, and, as the restrictions gradually eased, albeit with certain constraints, mobilization progressed. Most importantly, our decision alleviated complications associated with resource idling during the pandemic and saved costs in the process.”
Tough beginning, tough strategic decisions
Having begun against the backdrop of the pandemic in April 2021, the project team’s initial challenges were about mobilization. “Faced with uncertainties, we took a strategic decision to delay mobilizing critical resources, using the initial period to establish a greenfield fabrication yard,” shares Umasathiyan, “and, as the restrictions gradually eased, albeit with certain constraints, mobilization progressed. Most importantly, our decision alleviated complications associated with resource idling during the pandemic and saved costs in the process.” He looks pleased at their
wise call.
Driving efficiency in execution
“A project of this magnitude involving potentially up to 200,000 distinct items for erection, improving labour and equipment productivity required detailed planning and untiring efforts,” comments Sandeep Kaul, Project Manager (Mech), adding that there were inherent risks too associated with handling materials at heights reaching up to 103 m. “We embraced a module-based approach, with assemblies meticulously prepared at ground level that not only minimized the need for heavy equipment but also substantially mitigated the risks associated with working at heights.”
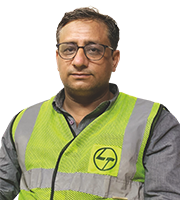
Sandeep Kaul
Project Manager (Mech)
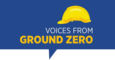

“A project of this magnitude involving potentially up to 200,000 distinct items for erection, improving labour and equipment productivity required detailed planning and untiring efforts. We embraced a modulebased approach, with assemblies meticulously prepared at ground level that not only minimized the need for heavy equipment but also substantially mitigated the risks associated with working at heights.”
While modularization significantly reduced the demand for heavy machinery and manpower, addressing the remaining requirements called for an innovative approach, skillfully implemented by the CMPC and P&M teams. “We introduced Strand Jacks, ingeniously mounted atop the structural building of the Stock House, to lift hoppers weighing between 60 to 70 tons into position that dramatically reduced our reliance on cranes with capacities of 300 tons or higher,” informs Santosh Patnaik, Project Manager (Stock House). Several other noteworthy modular lifts include the flare stack, stock house roof module and the cast house pipe rack.
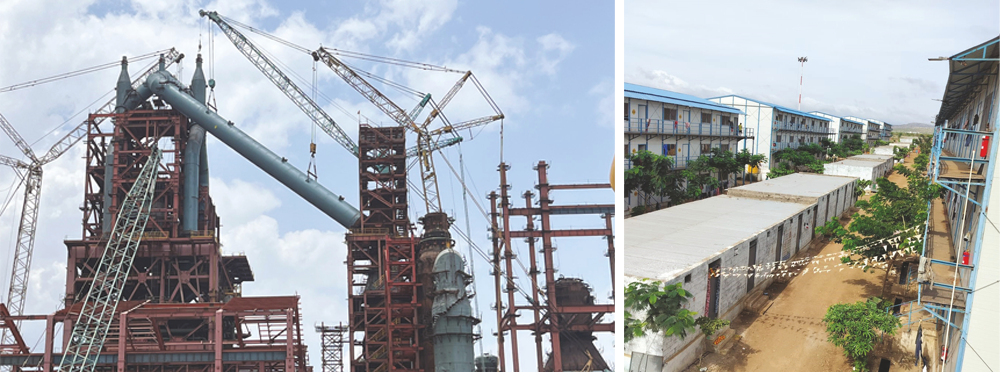
“In addition to our innovative approaches, we opted for steel shutters instead of the conventional methods to cast the ramp piers that significantly improved the efficiency of our concreting works, and cost savings,” remarks Sutanu Ganguly, Project Manager (Civil), with a satisfied expression.

Sutanu Ganguly
Project Manager (Civil)
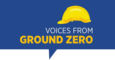

“In addition to our innovative approaches, we opted for steel shutters instead of the conventional methods to cast the ramp piers that significantly improved the efficiency of our concreting works, and cost savings.”
“Although the labour camp was designed to accommodate a workforce ranging from 5,000 to 7,000 individuals
(for BF5 & SMS4), a soaring attrition rate that peaked up to 145% in April 2023 was driving up mobilization costs. Maintaining the workmen habitat and transporting 6,000+ workmen within a stringent 1.5-hour time frame each morning presented formidable challenges. The possible solutions were either to increase the fleet of conveyance buses or reduce the 40-minute trip.
“After thorough research, we devised alternative routes and entry points and through persuasive and effective communication, successfully obtained approval from the client’s authorities to access entry gates via the shortest route by creating a separate gate for L&T personnel,” shares L A Anurag, Head IR, “that has optimized our transportation process, and reduced in the trip time to just 22 minutes.” Over a month, this time saving translates into an impressive 2,700+ extra man-days of work, achieved without incurring any additional cost. F&A Head, Ranganathan mentions that welfare programmes and cash incentives, reimbursed by the Client, are helping matters too.
Technology leading the way
At a juncture when labour is both expensive and scarce, mobilizing skilled manual welders has been a perennial problem and realizing that assembling critical technological structures like Blast Furnaces, Hot Blast Stoves, and Gas Cleaning Plants require a time-intensive process, spanning 20 to 25 days, with extensive welder involvement and subsequent high costs, the team has proactively explored the latest industry trends and technologies to mechanize welding. “By introducing a mechanized semi-automatic welding process utilizing FCAW (Flux Cored Arc Welding) and SAW (Submerged Arc Welding), we have revolutionized our workflow, reducing cycle time for a single assembly to just 7 to 9 days,” shares Umasathiyan, with a sense of purpose. The overall structure schedule has been reduced from 60 to 45 days and exposure to safety threats has decreased too.
“Fuel is money, the less you burn, the more you earn” smiles K Padmanaban Deputy General Manager (P&M), referring to the MOBA-FDMS system and fuel sensors implemented in equipment to continuously monitor and control diesel dispensing while adhering to the fuel norms for each piece of equipment. “While on one hand, this system prevents fuel pilferage, on the other, it holds the potential to save 2-3% of our regular fuel consumption.” All the identified equipment has been digitalized, with IoT devices providing real-time data.

K Padmanaban
Deputy General Manager (P&M)
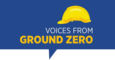

“The lab has realized a direct profit of approximately Rs. 50 lakhs by reducing our operational costs and enhancing efficiencies by minimizing downtime and delays.”
With a modest yet strategic investment of Rs. 10,000, the team has established an electronics lab at the construction site for in-house repairs on damaged electronic components and sensors, a task previously outsourced to OEMs at a significantly higher cost. “The lab has realized a direct profit of approximately Rs. 50 lakhs,” remarks Padmanaban,
“by reducing our operational costs and enhancing efficiencies by minimizing downtime and delays.”
With robust digitalization having strengthened their Management Information System (MIS), it is easier for Srinath C, Planning Manager, and his team to analyze equipment productivity and utilization. “It provides timely feedback for us to offer suggestions to the management regarding effective utilization patterns and to identify idle or underutilized equipment,” he points out.
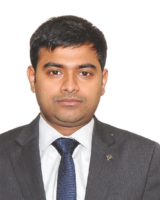
Srinath C
Planning Manager
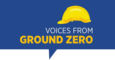

“To ensure transparency and accountability, each modification was communicated in advance and meticulously documented, and by formally documenting and submitting claims, we mitigated the risk of absorbing unforeseen additional costs or delays beyond our control that have helped enormously to sustain profitability and financial stability.”

Smart planning and small innovations making a big difference
Gokulan S (Project Manager Fabrication and SMS) faces a huge task of catering to a project involving 52K+ tons of steel structures within a stringent schedule of 24 months that translates into a supply rate of 2K+ tons per month.
60 acres of barren land has been converted into a full-fledged Fabrication and Modular Assembling Facility within
3 months. “Further, to obviate the need for a substantial fabrication yard area and the associated maintenance requirements, we decided to outsource 32% of the fabrication work to external vendors that reduced both the demand for P&M and overhead resources and optimized our overall project cost structure,” he states. By identifying vendors with robust supply capabilities close to the site, the team has minimized transportation costs too.
With consumables accounting for 2% of the total cost estimate for the Blast Furnace project, the team strategically allocated the scope for consumables to subcontractors, significantly increasing their accountability in usage apart from keeping overall project costs under control. To safeguard against the risk of fluctuations in steel prices for a 2-year long project, the team implemented a steel price escalation clause under which a fixed base price for steel was established at the outset of the contract with any future fluctuations to be borne by the client. “We therefore effectively transferred the risk of price escalation to the client, ensuring greater financial stability and predictability for our project,” grins Umasathiyan.
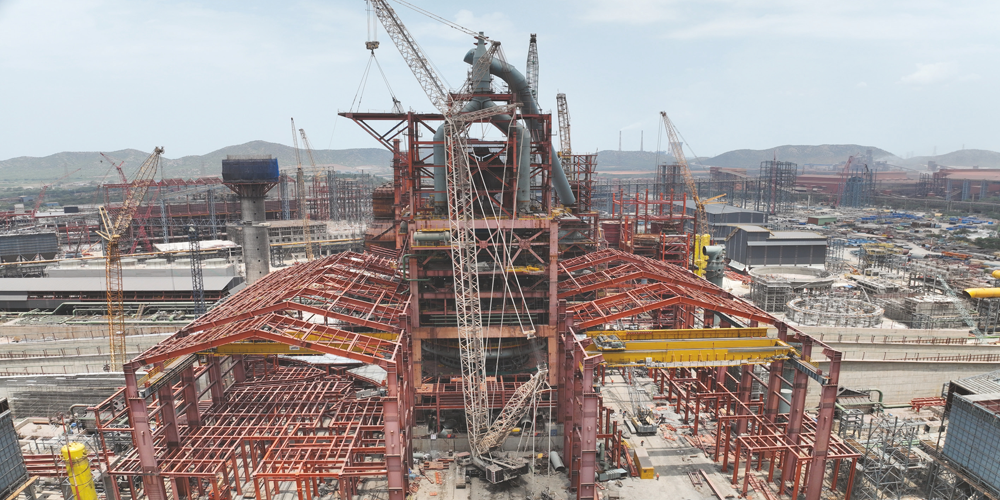
Adopting a prudent approach towards any change in scope, involving either modifications or additions, that normally came with substantial costs and erosion of profit margins, the team has only addressed those changes that were deemed necessary. “To ensure transparency and accountability, each modification was communicated in advance and meticulously documented,” mentions Srinath, “and by formally documenting and submitting claims, we mitigated the risk of absorbing unforeseen additional costs or delays beyond our control that have helped enormously to sustain profitability and financial stability.” By engaging experts previously associated with the JSW group and the Ballari location for decades, the team benefits from their longstanding association with the group and deep understanding of technical and commercial intricacies, to effectively address issues during contract finalization and execution.
“I am impressed by the way the Ballari project team has given contract and schedule management top priority for as the saying goes time is money,” enthuses Bhanu Pratap Singh, Head – Operations, Metals BU. “Even though the project schedule has been impacted by delays in customer inputs, they are tracking project and resources schedules to reduce cost overruns.” Delayed events have been duly submitted and extension of time successfully obtained, and such timely actions have helped the team improve their margins even before completion. A matter of great pride for Umasathiyan and the entire project team and motivation to deliver.
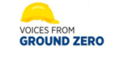

“I am impressed by the way the Ballari project team has given contract and schedule management top priority for as the saying goes time is money.”

Bhanu Pratap Singh
Head – Operations Metals BU
TATA KPO COKE OVEN PROJECT

Proactive measures for efficiency
According to Project Manager, Prasanta Tikadar, his and his team’s focus never wavers from delivering their project efficiently and within budget. “To enhance productivity, we have increased modularization during execution, moving from the conventional style of execution to a more mechanized and automated implementation, that has speeded up our progress,” he remarks purposefully.
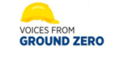

“To enhance productivity, we have increased modularization during execution, moving from the conventional style of execution to a more mechanized and automated implementation, that has speeded up our progress.”
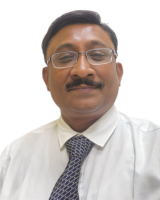
Prasanta Tikadar
Project Manager
Setting up a labour colony near the plant’s entry gate was a wise move that reduced daily travel time for the workforce and saved on monthly transportation costs. “By splitting work timings into two shifts: 7 am to 7 pm and 8 pm to 8 am, we have reduced the number of buses deployed for manpower movement,” points out Subhasish Sarkar, Planning Manager.
Refractory and Electrical & Instrumentation manpower adhere to a 7 am to 7 pm schedule, with staff rosters structured accordingly.
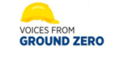

“Efficient inventory management has been our top priority. We continuously monitor consumables, construction materials, and long-lead items with a special emphasis on bulk procurement to secure the best material prices.”
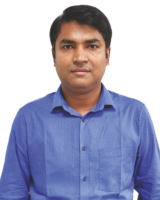
Subhasish Sarkar
Planning Manager
SOME OF THE TEAM’S MAJOR DELIVERABLES:

While smart equipment utilization is enhancing their efficiency, it is also fraught with impediments. The project has a stringent age criterion to deploy resources – less than 5 years – and the team has been finding it tough to find agencies in the market with the wherewithal to deliver as per specs. Secondly, the pandemic had disrupted the supply chain from China, with further delays caused due to inspections and obtaining clearances. “We maximized the use of plant & machinery and ran day-and-night operations by hiring a majority of the equipment,” informs Shijumon
N P, P&M In-charge. “Payments to agencies are based on actual usage, maintenance, and other operating costs that has ensured cost-effective resource management.”
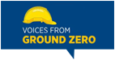

“We maximized the use of plant & machinery and ran day-and-night operations by hiring a majority of the equipment. Payments to agencies are based on actual usage, maintenance, and other operating costs that has ensured cost-effective resource management.”

Shijumon N P
P&M In-charge
Focused on productivity and inventory management
Every rupee saved adds to the profit line and Prasanta and team keep a hawk’s eye on controlling costs, diligently monitoring productivity. With monthly assessments of workmen and P&M productivity, the team is ready to make prompt corrective actions if required, and fine-tune gang compositions to complete activities within budgeted costs.
“Efficient inventory management has been our top priority,” says Subhasish. “We continuously monitor consumables, construction materials, and long-lead items with a special emphasis on bulk procurement to secure the best material prices.”

Digitalization for seamless execution
For Prasanta, digital tools are helping him big time in his quest for efficiency. “Recognizing that refractory work is critical for timely progress in subsequent activities such as equipment, piping, and E&I, particularly in Batteries 3A and 3B, we have implemented digital materials management involving the receipt, unloading, and storage of various types of bricks and mortar in different storage locations, to ensure that layer-wise matching bricks are fed to the site as needed,” he shares. QR codes track each packet of bricks, and GPS tracking ensures precise delivery. For record-keeping and reconciliation, EPC Proman is employed for material entry and issuance.
One of the team’s standout achievements has been the uninterrupted brick lining without delays in feeding matching bricks – a testament to their meticulous planning and execution. “Considering the huge volume of bricks and complexity, our digitalized mode of material management has come in handy,” notes Shijumon. “The refractory work involves handling 35 lakh bricks, including 783 types of indigenous & FOB brick shapes for each battery and we use QR code and GPS to track and identify bricks easily.”
Preparing for rainy days
The rains are a potent threat to pipe shot blasting and painting, a critical part of the project scope necessitating them to evolve monsoon plans. “Considering the volume of job, which translates into 13 lakh inch-m, it was imperative to find alternate measures to continue work uninterrupted,” says Subhasish, “for which we have hired two temporary sheds that have proved invaluable for the piping erection work to continue even during the rains,” he adds with a satisfied grin.
Modular erection speeds up progress
Apart from modular erection, another notable achievement of the team has been the installation of Primary Gas Cooler Modules in the By-Product Plant, that has earned appreciation from Mr. Amar Bountra, Chief – Projects & Construction, Coke Plant, Tata Steel.
Manufactured by L&T’s EWL, Kanchipuram, these modules boast the following features:
- The highest single lift, weighing an impressive 134 MT
- The first in India for a by-product plant
- Erected by a 500 T crawler crane
- Cooling tubes, flaring, water box, etc. are fixed at the workshop to reduce erection time at the brownfield site
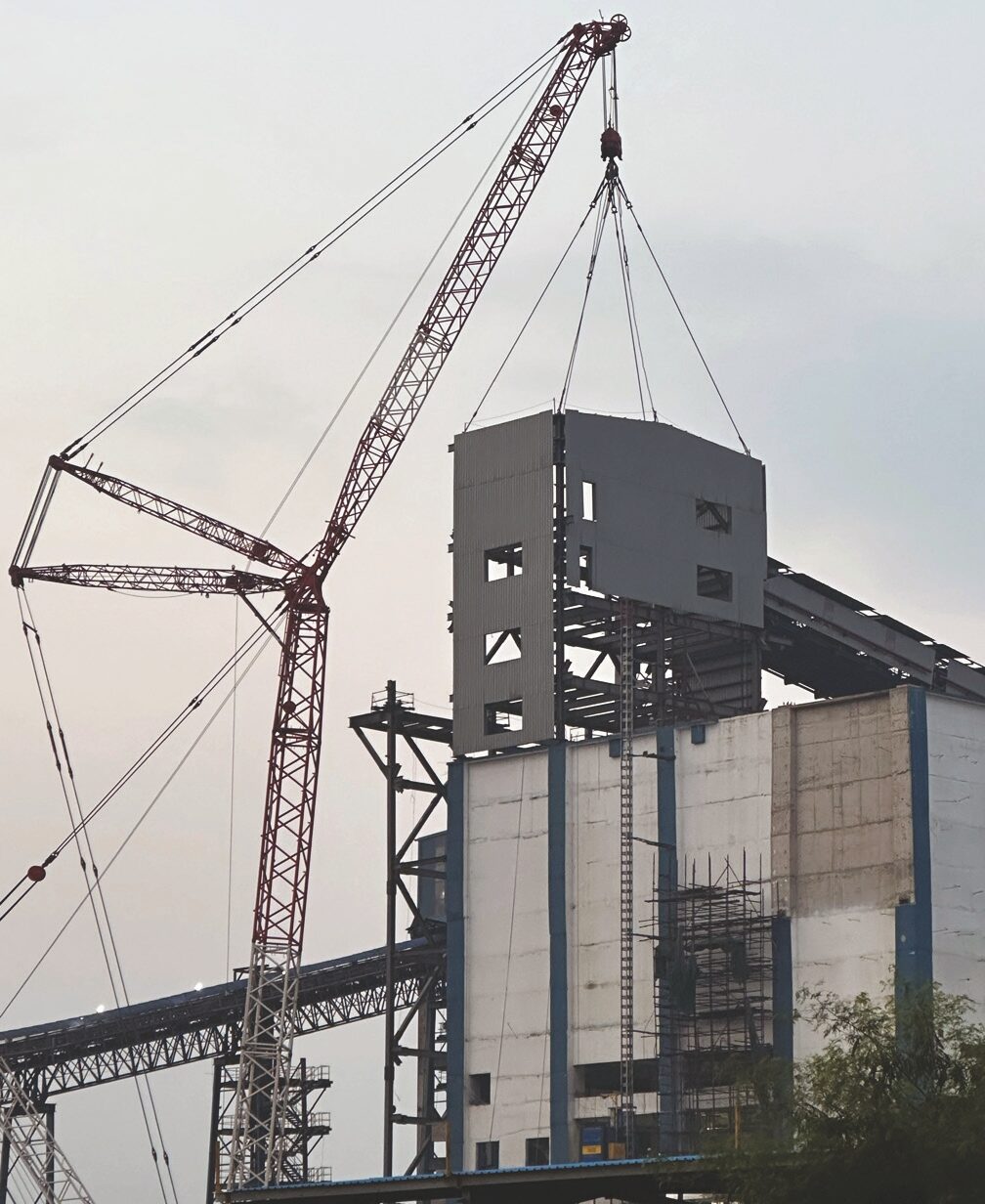
The pipe rack structures were erected along with the pipes, with the conveyor structures erected after completing the sheeting, tech structure, and equipment (idler frame, short post, roller, etc.).
“Our shift from conventional methods to embrace mechanization and automation has reduced the need for extensive on-site labour while increasing productivity,” remarks Prasanta. With the power of meticulous planning, digitalization, and innovation, he is confident that his team will continue to achieve remarkable efficiency and set new standards for excellence in progress.
VL’S 3 MTPA ALUMINA REFINERY PLANT PROJECT
This project can be best described as a start-stop-go-stopfinally go one. Back in 2008, L&T was awarded the civil and mechanical works to expand a 3 MTPA Alumina refinery plant at Lanjigarh, Odisha. Two years on, in August 2010, the project was halted due to environmental clearances and the plant, originally conceived, and designed by the Guiyang Aluminium Magnesium Design and Research Institute, China (GAMI), lay unfinished. In 2017, L&T was asked to assess and subsequently awarded the mandate to complete the balance works as per GAMI’s basic inputs including detail engineering. True to form, the project stalled again in 2018. Later, based on another feasibility assessment conducted by M/s, Worly Parson, the Client, Vedanta Limited (VL), started re-engineering with the help of M/s, TATA Consulting in 2020 and L&T’s Minerals & Metals SBG was re-awarded the project to complete the balance civil and mechanical works as per the drawings and equipment provided by VL.
The challenges of executing in the back of beyond
A measure of the remoteness of the project site, tucked away in the Kalahandi district in south Odisha, is that the nearest railway station, Muniguda, is 24 km, the nearest town, Bhawaniputra, 65 km and the nearest airport at Visakhapatnam 320 km away as a result, a couple of major challenges facing Project Manager, Sanjay Saha and team, have been to mobilize and retain labour and transport material & equipment to site.
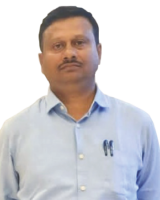
Sanjay Saha
Project Manager
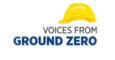

“Despite the many stumbling blocks, we have completed 88% of the physical work with 12 major units out of 16, already handed over to the customer for startup of precommissioning activities.”
The project’s chequered history has added a new dimension to its complexity. “While we are expanding the alumina refinery, partial expansion work had already been completed in 2008-10 with the then engineering partner, GAMI,” points out Sanjay. “Now, to execute the project referring to the inputs and drawings of a new technology partner, Worly (formerly known as M/s, WorlyParson) and detail engineering by TCE, onto an already constructed building is very difficult,” he grimaces, “with the result we are strengthening the structure foundation and pump foundation, by retrofitting works at the digestion and settler & washer units, due to an increase of the size of the equipment and pump. Apart from that, many other dismantling works including foundation, structural building, equipment, and piping with new erections are being done at site.”
“It is essential to take permissions for shutdowns before starting the expansion project of an already operational refinery, that adversely affect progress,” laments Mechanical Head, Muthuraj C, Sr. Construction Manager (MECH), “and, at times, even forcing us to change our execution plans.” Another difficulty is supply and estimating the scope of pipes, fittings & steel that are lying scattered around in an old plant.
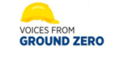

“As of August 2023, in the piping work, we have reached 21 lakhs IM within 24 months from starting of the piping works and are creating records by exceeding 1.5 lakh IM continuously over a period of five months with a maximum of 2.05 lakhs achieved in November 2022.”
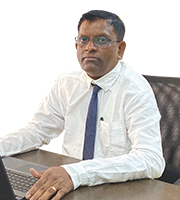
Muthuraj C
Senior Construction Manager (MECH) and Mechanical Head
As for labour, the project team has already mobilized more than 18,000 workmen to site, but people are leaving the place within a month or two, to comparatively better locations. It has also been observed that train routes are cancelled on many occasions, due to disconnections to the main rail head.
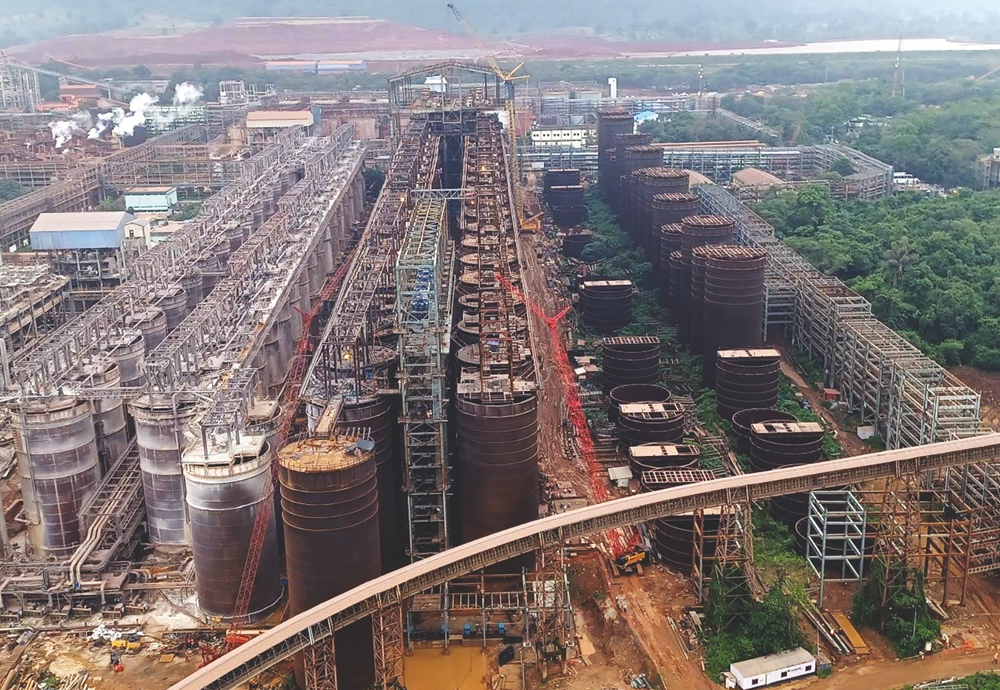
Progress in the face of big odds
“Despite the many stumbling blocks, we have completed 88% of the physical work with 12 major units out of 16, already handed over to the customer for startup of pre-commissioning activities,” states Sanjay, with a sense of achievement.

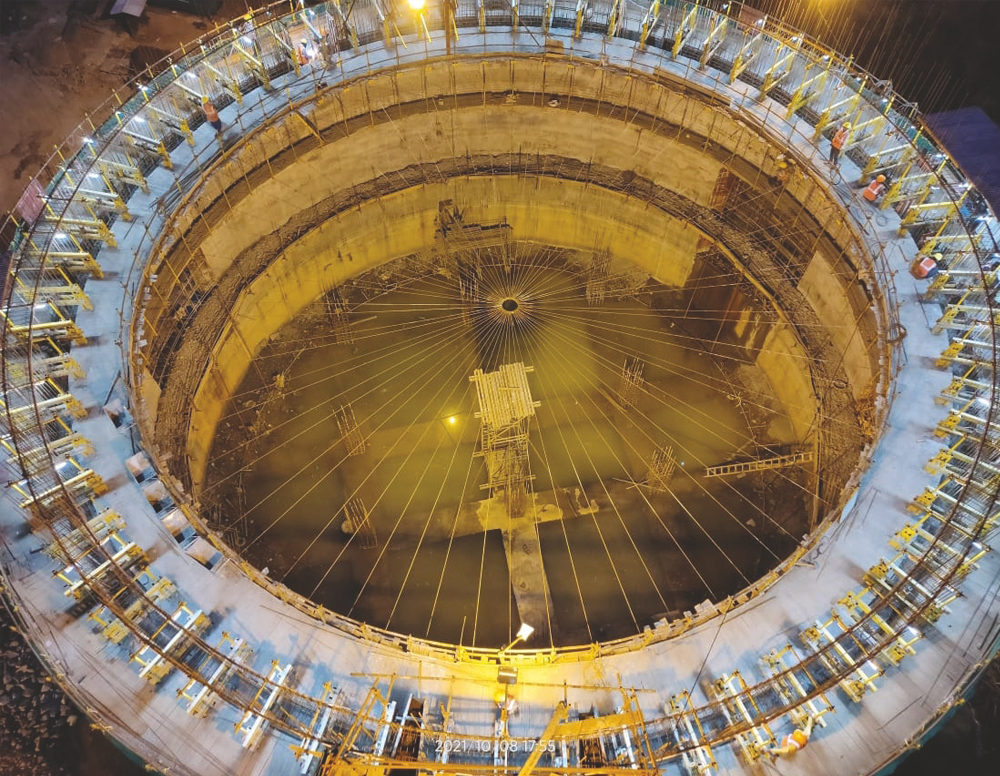
“As of August 2023, in the piping work, we have reached 21 lakhs IM within 24 months from starting of the piping works and are creating records by exceeding 1.5 lakh IM continuously over a period of five months with a maximum of
2.05 lakhs achieved in November 2022,” says a visibly delighted Muthuraj. The team has done 4 lakh IM piping hydrotests in June 2023 and completed UT (PAUT) for 113 tanks by February 2023.

On the structural erection front, Assistant Construction Manager (MECH), Seetakanta Pande, shares, “Several critical structures such as Digestion Tanks #3 and #4, coarse seed filtration, hydro-cyclone and more have been completed.” The erection of these structures is critical, he elaborates owing to space and height restrictions, often requiring discussions with customer basis which they need to, at times, amend their rate of structural works.
The team has made significant headway in equipment erection having already erected 20 (943 MT) heaters for Digestion T-4 within two months in September & October 2022. “Similarly, we have erected 9 heaters (410 MT) for Digestion T3 in a month in November 2022,” flags off Assistant Construction Manager (MECH), Narayan Debnath, adding that they erected 4 digester vessels (120 MT) in Digestion the same month. They have also completed erecting shells for the Ball Mills 6 & 7 including the feed & discharge end cover & trunnion (478MT) of train within a couple of months.
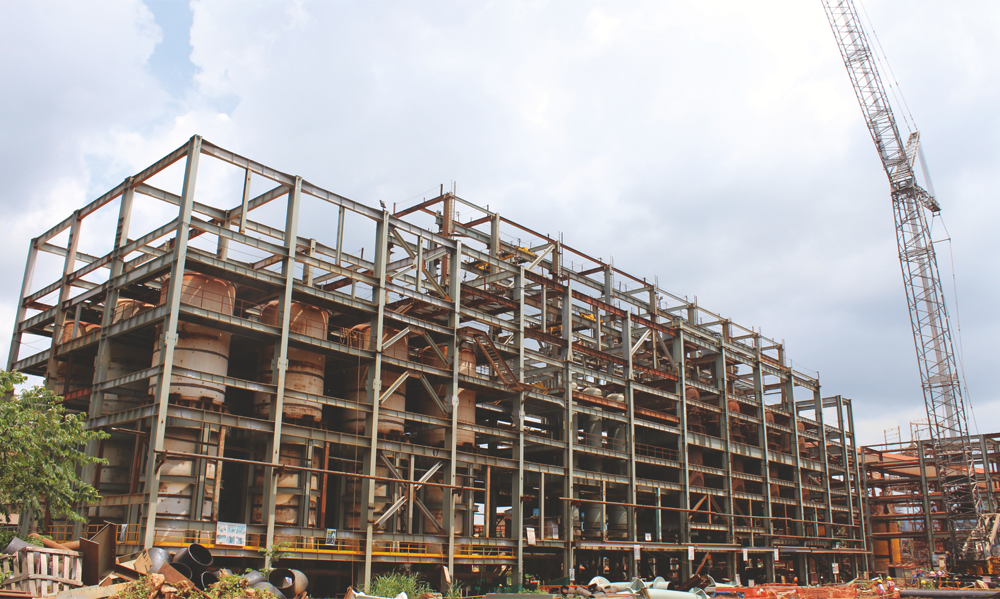
“As of August 2023, we have completed 69,732 cum of concreting hitting an average of about 2,500 cum per month,” says a pleased Sr. Construction Manager (Civil), Sushanta Kumar Panda and “the PPT colling tower was completed in a record time of 12 months,” his wide smile says it all. In Silos 2 & 3, 14 m slabs have been completed. “These were extremely complex involving circular/ ring beams with reinforcement dia. of 32 mm, rebar anchoring & heavy stagging work construction of Vertex Cone “^”, that starts from an elevation of 8 m to 32 m, inside the 40 m silos” remarks by Basant Kumar Panigrahi, Senior Engineer, highlighting the level of difficulty.
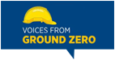

“As of August 2023, we have completed 69,732 cum of concreting hitting an average of about 2,500 cum per month and, the PPT colling tower was completed in a record time of 12 months.”
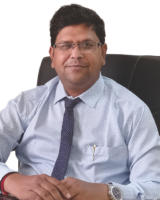
Sushanta Kumar Panda
Sr. Construction Manager (Civil)
As for finishing work: the false ceiling work of 3,260 sqm has been completed in three months for SS7, SS5, SS 3.1 & SS 3.2 & SS4 and the aluminium window works with toughened glass has been fixed in all substations, highlights Prodipta Chandra, Construction Manager (Civil).
Modularization & mechanization keeping them ahead
“By adopting the PAUT method for 113 tanks, we have eliminated a huge quantity of scaffolding works, saving us time and cost,” points out Barkat Hussain, Manager QA-QC.
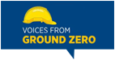

“By adopting the PAUT method for 113 tanks, we have eliminated a huge quantity of scaffolding works, saving us time and cost.”
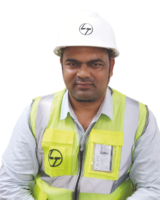
Barkat Hussain
Manager QA-QC.
Assistant Construction Manager (Civil), Vinit Kumar shares that by deploying the diamond wire saw cutting method for dismantling concrete especially in their brownfield project, the team has eliminated several risks normally associated with such work and saved time too. Other steps include implementing an ‘electric chain pulley block’ for rigging and an automatic bolting machine for fitting bolts.
Despite challenges, site team has performed the job with extreme satisfaction of the Customer and Mr. Navin Agarwal, Vice Chaiman of M/s, Vedanta Limited, visited site and appreciated the work of the entire site team.
The saga may have begun a decade and half ago, but despite several challenges, Sanjay and his team of hardy warriors are close to put finishing touches to this tough project, far away from civilization. Here is wishing them the best!