MAINTAINING A TRADITION OF TOP-NOTCH EHS PERFORMANCE.
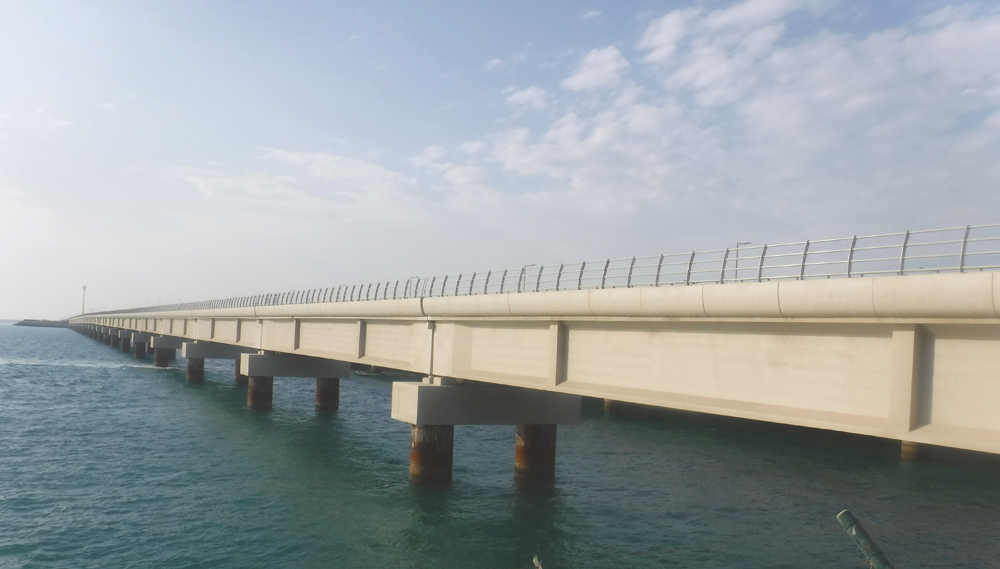
ETIHAD RAIL PROJECT
The L&T-Power China JV constructing the challenging Etihad Rail project has been recognized for their excellent EHS performance right from word ‘go’. Last year, the project bagged a BSC award followed by a RoSPA Gold at an international awards event and won the best EHS for M&M SBG so it was hardly surprising that they won L&T Construction’s Best Safety Award 2022 (International). Perhaps what must have warmed the hearts of the project leadership and team even more is the recognition from the CEO of Etihad Rail for fully complying to the Etihad Rail HSE Policy and being only the second contractor to be so recognized in the last 8 years of Etihad Rail’s history. “The project is very close to achieving 19 million safe manhours and the journey continues with the team enthusiastic and fully geared to handover the project without LTI as a benchmark,” enthuses an understandably proud, EHS Head – Jagdish Singh Chouhan.
“The project is very close to achieving 19 million safe manhours and the journey continues with the team enthusiastic and fully geared to handover the project without LTI as a benchmark.”
Jagdish Singh Chouhan
EHS Head
“The Etihad Rail Freight Facilities project has been a triumph of resilience and collaboration, overcoming the challenges posed by the pandemic to deliver a safe, efficient, and sustainable solution for goods transportation in the UAE,” remarks Project Director, Ahmed F Fahmy. “By successfully managing equipment sourcing, subcontractors, contracts, and major construction works, the project team has demonstrated their commitment to excellence in project management and their ability to work towards a common goal.” The project involves the construction of six freight facilities to support the Etihad Rail network, and provide a safer, greener, and more efficient mode of transportation for goods and commodities.
“By successfully managing equipment sourcing, subcontractors, contracts, and major construction works, the project team has demonstrated their commitment to excellence in project management and their ability to work towards a common goal.”
Ahmed F Fahmy
Project Director
Several mountains to climb
The pandemic and the resultant lockdowns, supply chain disruptions, lack of labor were the team’s initial hurdles that were expertly mitigated. Other challenges included managing the interface with mainline contractors, obtaining approvals from local authorities & multiple design consultants, and the distant location of the freight facilities across the UAE. “The construction team worked closely with all the parties involved, meeting customer expectations while balancing the various technical and logistical requirements of the project,” observes Ahmed. “Despite all these issues, we have completed the Etihad Rail Freight Facilities on time, with zero Harm and or LTI and within budget,” which he finds extremely satisfying after his previous decade-long association with Bechtel. The facilities are designed to be environmentally sustainable, reduce carbon emissions and support UAE’s commitment to sustainability.
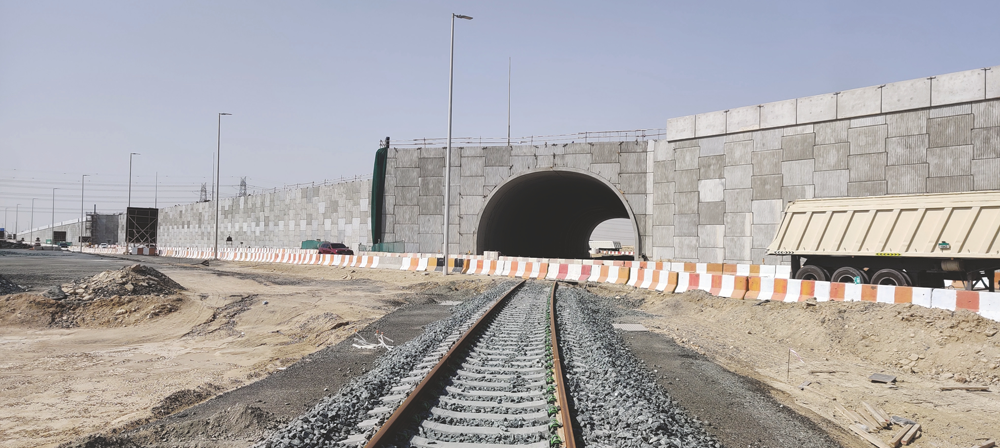
Sourcing equipment from 14 different countries was what kept Project Control Head, Barath Kumar, sleepless in UAE. That called for extensive coordination and communication with suppliers to ensure that all equipment arrived on time and within budget. “With careful planning and risk management, we successfully sourced all of the necessary equipment and materials within the deadlines,” he says with a relieved smile. “Through effective leadership and clear communication, we also managed a complex network of 250 contractors to ensure that their work met the expectations of our project management consultants – Egis and Jacobs.”
“Through effective leadership and clear communication, we also managed a complex network of 250 contractors to ensure that their work met the expectations of our project management consultants – Egis and Jacobs.”
Barath Kumar
Project Control Head
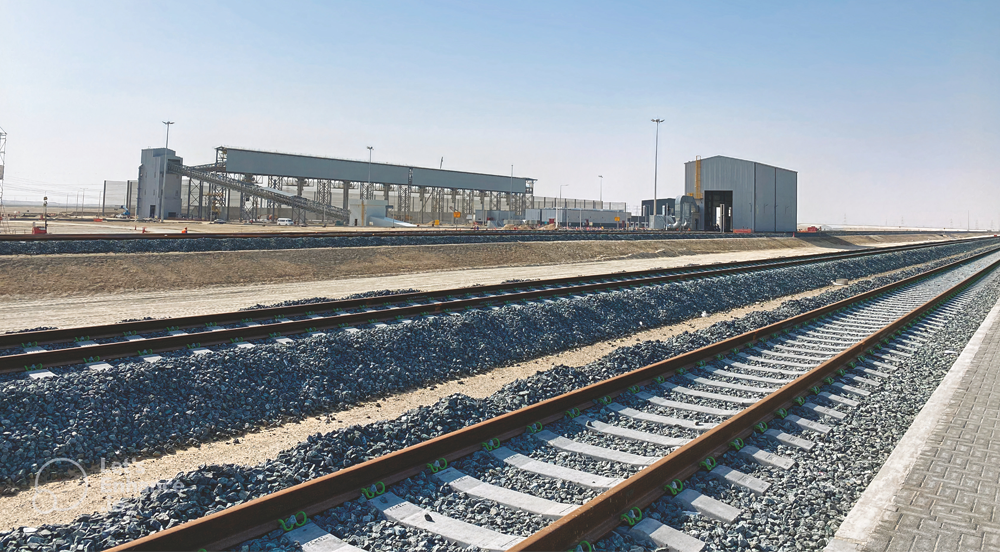
Handling 3.3 million cum of earthworks in the desert and hilly terrains for track & road works, a material handling conveying system, concrete silos, underground rail unloading stations, 40 km of track works, a hardstand for container handling and existing utilities protection and diversion is no laughing matter as the team discovered. “Constructing the 1 km marine bridge in Khalifa Port Abu Dhabi and a 1.4 km Rail over bridge (OBR) on E611 Highway in Dubai to connect Abu Dhabi were extremely tough,” sighs Barath. With innovative construction methods like two 11 m tall & 100 m long precast arch culverts for railroad crossing and modular fabrication, transportation & erection of bulky & heavy steel hoppers inside RCC silos, the team overcame months of initial delays to complete construction within the allotted
time frame.
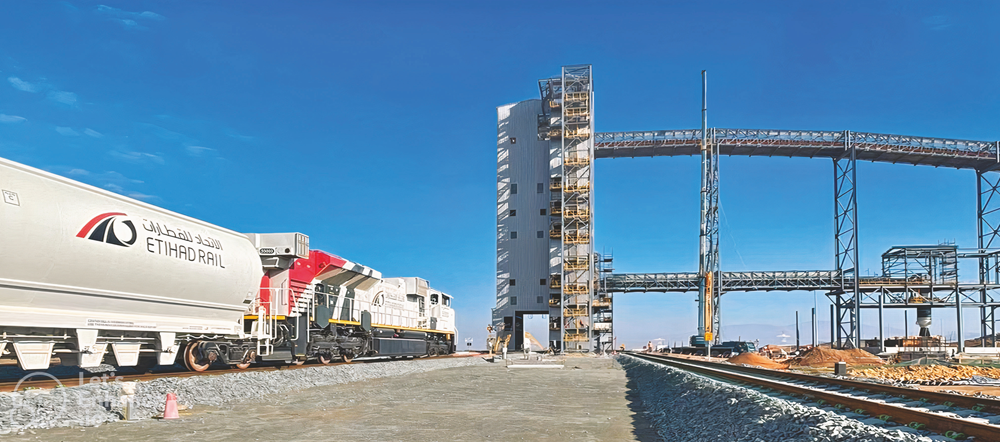
Constructing the Aggregate Dry Port freight facility
Heavy mechanical lifting & erecting 50 m tall silos and RLS hoppers weighing up to 174 T were carefully planned, along with EDRC, and executed by engaging a specialist lifting agency, supervised, and monitored by the site team. Working inside the silos to fabricate the conical sections involved work at height, addressed by fabricating the sections on the ground, then lifted and erected in place. The quantum of hot works inside the silos was marginally reduced with the same methodology, significantly reducing ill health effects on the working team.
Constructing the E611 (Emirates Road) bridge & road works at the DIC (Dubai Industrial City) freight facility
Since the project was located close to the existing E-611 highway, the team had to obtain Permits / NOCs from 7 different authorities with a Temporary Traffic Management (TTM) road constructed to divert the highway traffic. A lot of excavation work involving underground utilities was done by hand to protect the utilities and controlling dust in a windy environment was another big task. For Jagdish and team, the Safety demands were high as the team had to protect the overhead lines when moving machinery, shifting the 10T arches from the precast yard through live road to E611 for Tunnel – UTR (Ultimate Track Route) & CTR (Current Track Route), installing permanent concrete barriers on the vertical termination of the MSE wall that involved working at height near open edges with limited anchorage points. No LTI is an indication that Jagdish and his team did a perfect job.
Constructing the Ghuwaifat freight facility
Ready availability of material & equipment was always an issue as the project is in the western region of Abu Dhabi, 350 km away from the city of Abu Dhabi. 40km/hour winds and frequent sandstorms often buffeted the site causing frequent suspension of work. “Since there were no well-established camps available in the entire region, workers had to travel 100 km from Ruwais to Ghweifat and back in poor visibility, which was very risky, not to mention fatigue so we developed a suitable camp to Etihad Rail standards,” says Site EHS Manager, Benoy Cleettus. While look head plans for each activity addressed procurement; the workforce was protected with dust proof safety goggles.
“Since there were no well-established camps available in the entire region, workers had to travel 100 km from Ruwais to Ghweifat and back in poor visibility, which was very risky, not to mention fatigue so we developed a suitable camp to Etihad Rail standards.”
Benoy Cleettus
Site EHS Manager
Constructing the marine bridge at Khalifa Port Offshore freight facility
“This is an activity that would have tested the best of project managers,” Barath says with a tight smile. Access to the marine work front required obtaining time-consuming approvals from AD ports. Marine vessel mobilization was tricky considering the environment, as was delivery of concrete and transporting the T Girders to the launching area for which the team used purpose built launching gantries for installation and movement. Limited access hindered the construction of the bridge deck expansion joint and installation of drainage pipes under the girders. “For edge protection we installed the bridge barriers and the MSE wall, layer by layer,” informs Jagdish, “and our coordination with AD Ports was vital to obtain a spate of approvals to access the jetty, bridge areas, for demolition and removal of debris.”
Beating the heat & keeping it green
The team’s TWL (Thermal Work Limit) system proved successful to beat the extremely hot and humid conditions, with zero recorded heat related illnesses till date. “Considering the environmental sustainability, we developed a strategy to minimize the impact of construction waste while maximizing waste reuse and recycling in line with the Project CEMP requirements,” informs Geetha H Umapathi, Project Environment Lead, who drives sustainability at the project. An initiative to cure water reuse minimized waste and maximized resource conservation and local trees were relocated in consultation with the local environmental authorities.
“Considering the environmental sustainability, we developed a strategy to minimize the impact of construction waste while maximizing waste reuse and recycling in line with the Project CEMP requirements at the project.”
Geetha H Umapathi
Project Environment Lead
Keeping EHS top of mind
“I applied the benchmark practices most suitable for our multinational workforce based on my international experience that worked well,” smiles Jagdish, “especially engaging the workers with small but effective behaviour-based initiatives.” The Engineers, Jacobs, were tough nuts to crack with their stringent HSE compliance system, regular HSE Inspections and observations for close out but Jagdish and team were able to hold their own.
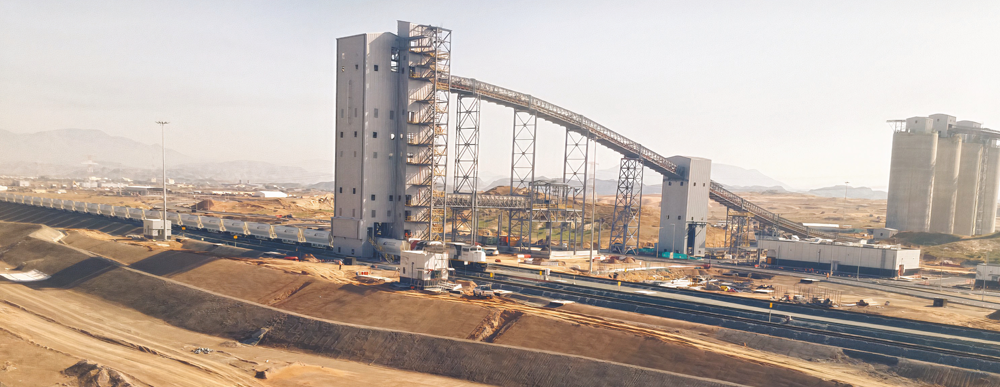
Each site had their own HSE Leads/Managers, and the EHS team was 50+-strong managing a project that was spread from the border of Saudi Arabia right across to the Omani border. “A Project HSE Manager covered one site a day thus 6 sites in a week to inspect and give site support,” says Jagdish.
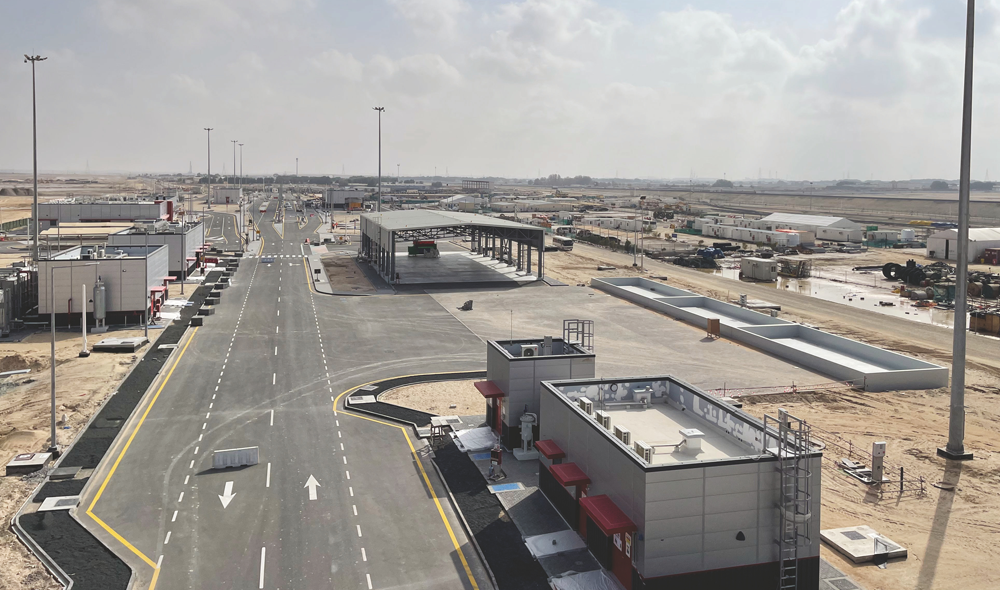
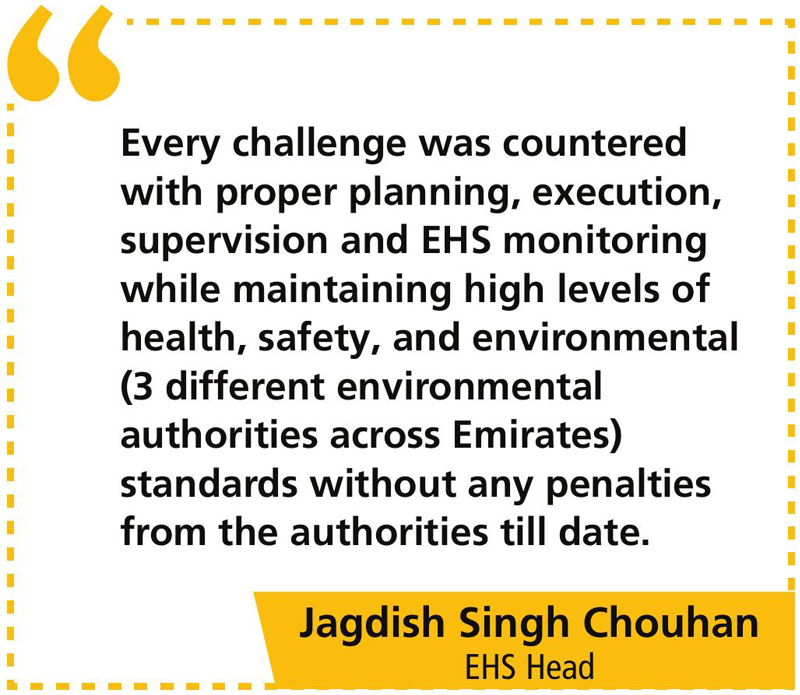
The Hazard Hunt competition engaged workers and staff with EHS, apart from monthly HSE incentives for workers, and EHS Readiness Reviews prior to starting a new work or with a new subcontractor. Lead & lag indicators were discussed at weekly coordination meetings with all sites.
“Digitalization was our ally,” smiles Jagdish, for all reporting was digital, all reports to the client and observations from them uploaded on the EPFM platform with closeout on the digital platform known as PROLOG (engineer controlled). FIRI was used to report any incident to the L&T HQ while SOSC reported to the L&T HQ using the digital platform (Telegram).
“Every challenge was countered with proper planning, execution, supervision and EHS monitoring while maintaining high levels (OSHAD, OSHA, Etihad Rail and Jacobs) of health, safety, and environmental (3 different environmental authorities across Emirates) standards without any penalties from the authorities till date,” concludes Jagdish rousingly, confident that he and his team have set an EHS benchmark for other sites across the organization to follow.