M&M PROJECTS OVERCOME DISRUPTIONS TO TAKE CLIENT RELATIONSHIPS TO THE NEXT LEVEL
The project to construct the Blast Furnace #5 and Steel Melting Shop #4 for JVML Ballari Project began in April 2021 when the world was still reeling under the impact of the pandemic. Apart from that major challenge, Project Director
R. Umasathiyan and his team had to face other major issues including delayed receipt of drawings and non-availability of workmen. Refusing to be overawed, they put up a solid front, went about meeting the client’s requirements of establishing the required infrastructure like the labour camp, two large fabrication yards, site setup, a rolling yard and networking with vendors. Their quick decision making and swift action on ground have been prime reasons why JVML is singing their praises.
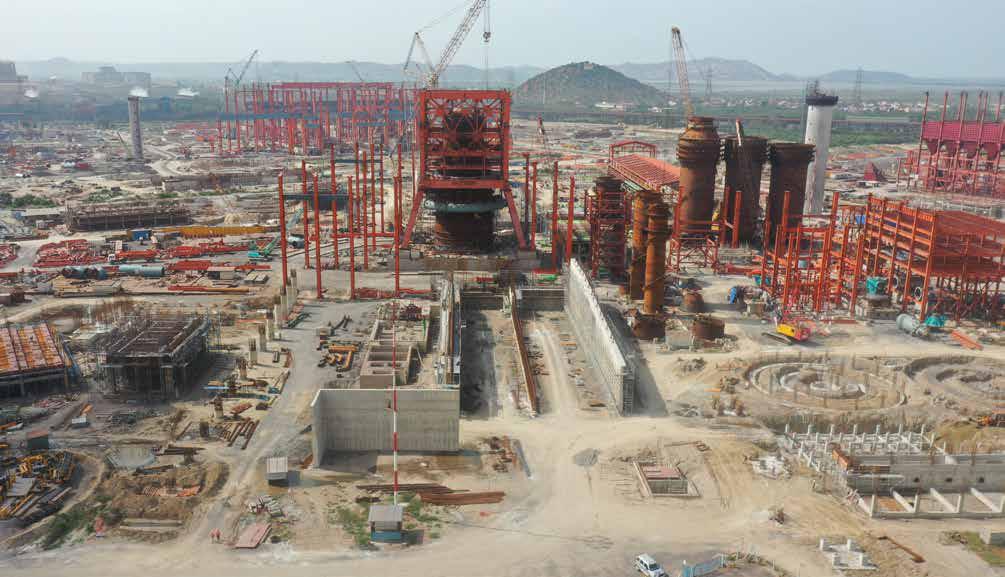
Quickly off the blocks
To meet the monthly demand of 5,000 MT of fabricated materials, the team begin by quickly developing a green field fabrication yard, with the support of the JVML project team. As the fabrication was ramping up, Umasathiyan’s next task was to handle the huge quantum of fabricated items. “We introduced a digital tool, EPC Proman, to monitor work progress, material management, dispatch, unloading and storage of material,” he says, revealing his faith in the benefits of digitalization. “Later, as the quantum of work increased with several new work fronts opening, and to eliminate the long route of data flow to the planning department, we digitally integrated scheduling and progress monitoring upfront to the central servers via the WRENCH platform.” The direct entry of data to the servers from the site officers eliminated delays and provided streaming data to review and monitor.
“We introduced a digital tool, EPC Proman, to monitor work progress, material management, dispatch, unloading and storage of material and we digitally integrated scheduling and progress monitoring upfront to the central servers via the WRENCH platform.”
R. Umasathiyan
Project Director
Arranging the required steel within a short time frame to feed the fabrication team was another challenge for which a crossfunctional project team comprising representatives from L&T, the procurement team and JSW was formed to discuss the supply chain issues on a weekly basis and take immediate action.
Innovations push progress
Planning Manager Srinivas Pabolu is excited about the Semi-Automated Welding they have introduced at site. “It is an efficient methodology where the welding locus is Planar, and the machine movement path is simple,” he explains. “We initially utilized it for the modular doubling of the Blast Furnace Shells achieving significantly less cycle time for the bed level doubling.” The Hot Blast Stoves that were initially scheduled for 12 months was squeezed to 8 months as per the Client’s requirement that had initially looked too tall a mountain to climb. Not leaving any stone unturned, the team conducted meetings with expert blast furnace in-charges and understood that increasing welders would decrease cycletime, but expert welders were scarce. “To address this issue, the number of fabrication beds was increased and with the semi-automated welding methodology, we achieved a cycle-time that was significantly lesser that the manual welding cycle,” adds Srinivas.
“The Semi-Automated Welding is an efficient methodology where the welding locus is Planar, and the machine movement path is simple. We initially utilized it for the modular doubling of the Blast Furnace Shells to achieve significantly less cycle time for the bed level doubling.”
Srinivas Pabolu
VPlanning Manager
Managing the workmen
Owing to the remote location of the site, workmen accommodation had to be set up next to the fabrication yard to house 5,000 people during Stage 1 of development, scalable to accommodate up to 7,000 during Stage 2. To keep the pace of progress intact, Umasathiyan requires a strong workforce and when attrition started to outstrip mobilization, quick action was warranted to retain labour. “We reduced the workmen commuting time to site by establishing alternate entry and exit gates and introduced additional amenities at their camp to improve their quality of life especially for those who did not prefer to stay in after travelling from various distant parts of North India,” he shares. Other amenities they set up included a volleyball court, a football ground, an open-air theatre, proper bus parking and boarding points, canteens, and RO plants for drinking water. “We revamped the induction and screening process to reduce it from 6 days to just
2 days and set up a Medical Center too.”
The challenges remain but Umasathiyan, Srinivas and their charged project team are keen to overcome them and deliver the project to the client’s complete satisfaction.
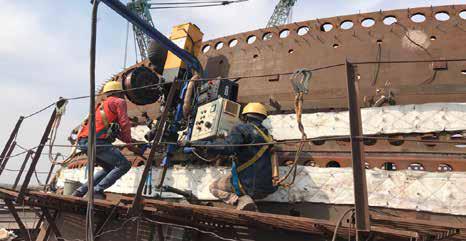
Semi-automatic welding process for shells
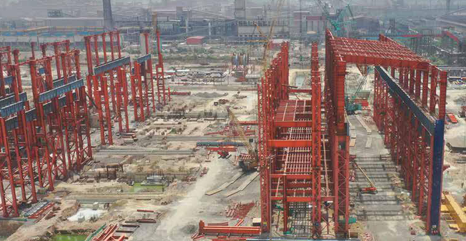
Steel Melt Shop at JVML Ballari
DELIVERING ON THE TRUST REPOSED BY TATA STEEL
M&M is presently executing two projects for Tata Steel: the 1.5 MTPA Coke Oven plant and the Steel Melt Shop both at Kalinga Nagar. In both cases, project teams have been punching above their weight to delight the client with their consistent, and often before-time, delivery.
Tata Steel Limited is augmenting the capacity of their integrated steel plant at Kalinga Nagar, Odisha from
3 MTPA to 8 MTPA under the Phase II Expansion project in which L&T has been mandated to construct the
1.5 MTPA Coke Oven plant. The scope includes refractory works, supply & erection of building & technological structures, equipment, piping, E&I, and commissioning assistance of the plant within 24 months. The major units of delivery being two blocks of Coke Oven batteries each with 62 ovens (6.25 m height),
by-product plant & utility, two Coke Dry Quenching (CDQ) units of 200 TPH capacity each and an associated raw material handling system.
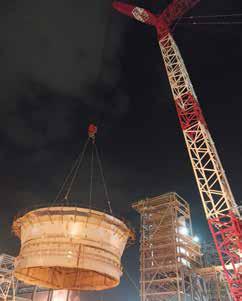
Modular erection of CQD chamber shell
As per the contract, the supply of major structural items/ equipment for the two CDQ units were in Tata Steel’s scope for which they issued free issue materials along with the work fronts at start of the contract. “By mobilizing from word go, we started structural erection work on 21st January 2022 i.e. within 70 days from start of contract on November 11th 2021,” informs a determined Prasanta Tikadar, Project Manager. “We completed major erection in the module and around 550 MT (light weight & tall structures) was erected within 2 months. During a site visit, higher officials of Tata Steel expressed their admiration for such significant progress in such a short span of time,” he says with a beaming victory smile.
“By mobilizing from word go, we started structural erection work on 21st January 2022 i.e. within 70 days from start of contract. We completed major erection in the module and around 550 MT (light weight & tall structures) was erected within
2 months. During a site visit, higher officials of Tata Steel expressed their admiration for such significant progress in such a short span of time.”
Prasanta Tikadar
Project Manager
Good work brings more and considering the rapid progress in execution, Tata Steel offered L&T to execute another critical structure (TOPR – 3B battery) after another agency had failed.
“We completed the structural erection works within the stipulated time and handed it over to a delighted customer who is all praise for our efforts for timely completion of a job which is in the critical path of the entire Coke Oven project.” Prasanta is visibly proud of his team’s delivery.
Delivery on the back of automation & digitalization
Refractory Works: Considering the huge volume of bricks & complexity, the team digitalized materials management for seamless execution. “The entire process from receipt of 17.5 lakhs of 783 different types of brick and mortar, unloading and storage in different locations and feeding the matching bricks layer wise to site as per requirement was digitized,” informs Planning Manager Subhasish Sarkar. The entire refractory installation work of one battery was planned to be completed in 250 days and the entire materials availability and progress is being monitoring on a 3D platform. For easy tracking and identification, each packet of bricks are QR coded and GPS tracked as per site requirement. “For record & reconciliation, we use EPC Proman for entry and issue of materials,” adds Subhasish.
“The entire process from receipt of 17.5 lakhs of 783 different types of brick and mortar, unloading and storage in different locations and feeding the matching bricks layer wise to site as per requirement was digitized.”
Subhasish Sarkar
Planning Manager
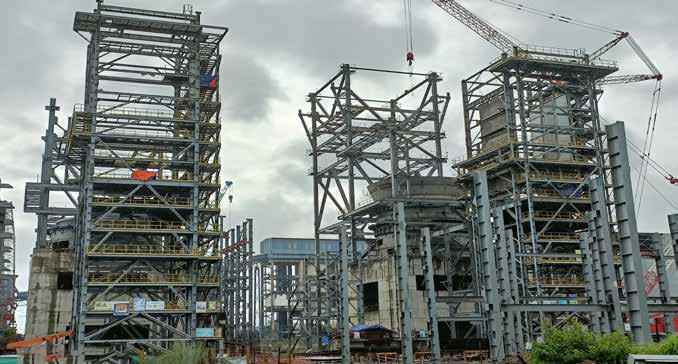
CDQ 2 & 3
To enhance productivity and speed up progress, the team plans to move from a conventional execution style to more mechanization & automations with minimum workmen strength. Here are a few of them:
- Refractory 4D modelling: 3D Model developed in REVIT & Navisworks software and 4D progress monitoring in Synchro-Pro software to monitor planned v/s actual progress each brick layer wise.
- By-product Plant Model: 3D Model developed in REVIT & Navisworks software to visualize the entire plant/facility to ease execution planning.
- Modular erection specially for heavy & critical structural lifts like tanks, structures, conveyors, heavy weight equipment like scrubbers, primary gas cooling units resulting in huge savings of labour & time, improved quality of job and reduced safety hazards.
- EPC PROMAN: Piping work planning involves a lot of interfaces, identifying lines with specifications, processes that SPOOLMAN makes easier & faster with the isometric view it affords. Material is tracked with MATCONTRK for different dia/types of pipes & pipe fittings.
- Orbit pipe cutting & welding machines reduce time for pipe fabrication, especially for the higher dia. pipes.
Addressing the issues of procurement & workmen
The team soon realized that delivery depended on the supply of building structures for timely generation of fronts for subsequent activities like equipment, piping & E&I. “Accordingly we finalized as many as 5-6 fabrication vendors at different locations to speed up fabrication of the building structures,” shares Pradeep Kumar Das, Assistant Construction Manager – Structural Fabrication, “with special emphasis on procurement of raw steel, and delivery at fabrication shops as per priority items. Within 3 months from the start of the project, we had procured 46% of the raw steel, and started delivering the fabricated building structures.”
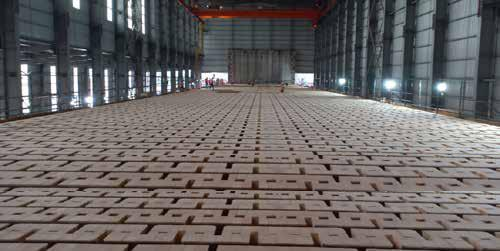
Refractory top layer – Corbel Zone (Battery 3A)
“As we mobilized early, we started structural erection work at various critical units like CDQ Chamber, Boiler Structure, that boosted our client’s confidence in us,” says Saroj Kumar Maity, Construction
Manager – Structural. Saroj is a happy man for their action also insulated the project from the highly volatile steel market and disruptions caused by various global geopolitical issues.
“As we mobilized early, we started structural erection work at various critical units like CDQ Chamber, Boiler Structure, that boosted our client’s confidence in us.”
Saroj Kumar Maity
Construction Manager – Structural
“To counter the higher price trends, we tightened our planning and started to order minimum quantities of raw steel closely monitoring site requirements / completion of critical units,” adds Subhasish. “In some cases, we even directed the vendor to defer supplies and delayed placing fresh orders to minimize the impact of material cost.” The orders for pipes were delayed a trifle, only minimum quantities of pipe fittings were ordered considering immediate front readiness of pipelines. “Altogether, we made substantial operating cost savings in this unavoidable global market scenario,” sums up Prasanta.
Realizing how critical workmen are for project progress, the location finalization, construction of the workmen colony and associate infrastructure were taken up on top priority despite persisting local issues. At the same time, local agencies were engaged to identify and mobilize competent workmen. When finalizing the sub-contractors, special attention was given to bring workmen groups in the right combination & skill levels. With all the basic amenities in place, timely wages payment, etc., workforce attrition was significantly controlled.
“Overall, the initial resource mobilization was completed at least a month ahead to start the execution at site by meticulous planning, monitoring, and coordination with the customer, internal departments & the BU team,” points out Prasanta. “Our customer appreciated our efforts for prompt mobilization at site with required manpower, plant and machineries.”
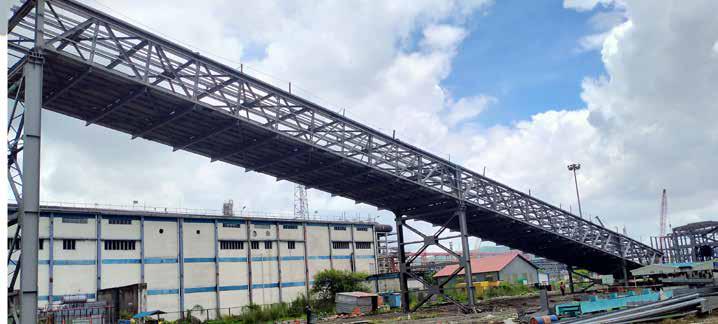
C 207 – 208 Conveyor (COB area)
ONE MORE FOR TATA STEEL
M&M is helping Tata Steel to augment their ‘Steel Melt Shop’ from its existing capacity of 3 MTPA to 8 MTPA with the scope of work involving supply & erection of building & technological structures, equipment, piping, E&I and commissioning of the plant. The project that kicked off on 24th January 2022 must be delivered in 28 months.
Apart from the challenges of executing inside an operational plant, timely resource mobilization was key in a highly volatile global scenario. “We had three months for mobilization as per the contractual schedule but with meticulous planning and drawing on our strong relationships with vendors from earlier projects, we mobilized the site one month ahead of the schedule that delighted the client,” says an equally delighted R Sivanesan, Project Manager.
“We had three months for mobilization as per the contractual schedule but with meticulous planning and drawing on our strong relationships with vendors from earlier projects, we mobilized the site one month ahead of the schedule that delighted the client.”
R Sivanesan
Project Manager
“When the steel prices were at their peak, we struck a fine balance between site requirement and cost of procurement,” shares an astute R Prabakaran, Planning Manager. “With some micro planning, we postponed some supplies without affecting site progress and schedule and after minutely studying the BOQ issued by the customer for pipes & pipe fittings, ordered bare minimum quantities to facilitate the site erection and make huge savings in the bargain.”
“When the steel prices were at their peak, we struck a fine balance between site requirement and cost of procurement. With some micro planning, we postponed some supplies without affecting site progress.”
R Prabakaran
Planning Manager
WISA, Safety app and WRENCH are being implemented at site. “In fact, we have done away with manual DPRs, and all drawing approvals & communications are through WRENCH,” points out Shubhranshu Mohapatra, who is spearheading the digital initiatives. “Progress monitoring is through chatbots since the beginning of the project; all supply items are QR coded and we even bar code client supplied material to identify and retrieve them easily.” He is happy that the client is extremely appreciative of the team’s digital efforts. On the automation front, the focus is to reduce dependency on manpower as the customer is keen to reduce human footprint inside the site to avert any potential safety hazard due to operating units and, increase modularization. “Avenues like Bevel cutting of pipes, orbital duct welding and electric chain blocks have been identified,” informs Jiten Dutta, Senior Construction Manager.
“Progress monitoring is through Chatbots since the beginning of the project; all supply items are QR coded and we even bar code client supplied material to identify and retrieve them easily.”
Shubhranshu Mohapatra
Digital initiatives
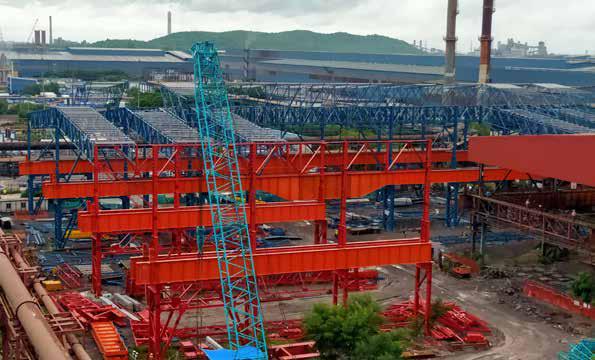
PQR Bay area at SMS expansion project, Kalinga Nagar
Site administration is key to keep the morale of the employees & workmen high while labour attrition has been controlled by redressing their genuine grievances. “We received an appreciation mail from our SBGH for the timely processing of subcontractor bills and 100% workmen payment before the 7th of the succeeding month,” says a proud Satish Patnaik, Site Accounts & Admin Head, which he adds also won the customer’s appreciation.
No stone is left unturned at all these three M&M sites to overcome every disruption and push progress to delight their customers.
“We received an appreciation mail from our SBGH for the timely processing of subcontractor bills and 100% workmen payment before the 7th of the succeeding month.”
Satish Patnaik
Site Accounts & Admin Head