NEW NAME. SAME PASSION.
SAME DRIVE TO EXECUTE EFFICIENTLY.
Recently, the SBG was rechristened ‘Minerals & Metals’, though for the people who make the SBG there has been no change in their passion, commitment, or drive to complete their projects in time with safety and quality as they have been doing all these years. Yes, the last couple of years were tougher, but they have proven even tougher going by their continued performance.
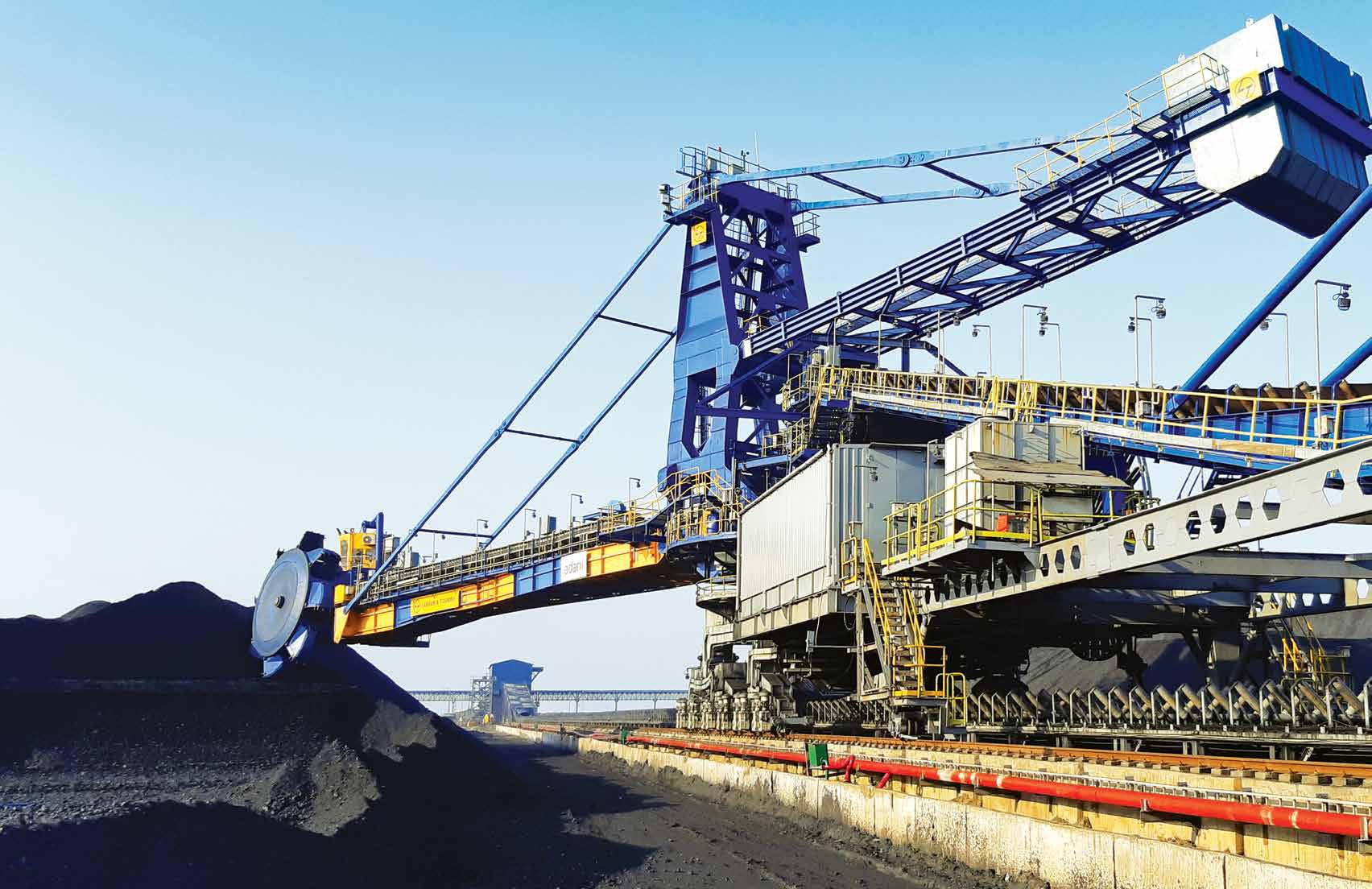
JSW DOLVI PROJECTS
THREE DELIVERED, ONE JUST A HAIR’S BREADTH AWAY FROM DELIVERY
Project Director Bhanu Pratap Singh heaves a huge sigh of relief as most of his projects for JSW Dolvi are either completed or just on the threshold of completion. “Of course, it has been tough going for the past couple of years,” he nods, “but it is remarkable how teams across our projects have stood firm, shoulder to shoulder, to face and overcome all the challenges that have been thrown in their paths.”
“Of course, it has been tough going for the past couple of years but it is remarkable how teams across our projects have stood firm, shoulder to shoulder, to face and overcome all the challenges that have been thrown in their paths.”
Bhanu Pratap Singh
Project Director,
JSW Dolvi Projects
3 MPTA COKE OVEN #2 PLANT: 100% COMPLETE
Having 4 batteries, this is India’s tallest stamp charging battery with a height of 6.25 m. A 2-phase project, the contractual completion dates were 30th September 2018 for Phase 1, which was met, and March 2022 for Phase 2, for which Project Manager Arup Kumar Ray is ready for his final push. “100% of our project is complete,” he smiles. “We have harnessed the benefits of technology to restructure our working methodology for better coordination, accountability, and governance between the various departments.” Challenges, however, were aplenty, like the monsoons frequently playing havoc with their execution plans as their site is in a coastal region. “Working in a congested space and constantly changing work dynamics required precise coordination and logistic planning,” informs Planning Manager Shastha Kiran Manai, whose well-laid plans were further upset by the pandemic. “Executing close to a functioning plant is not an ideal situation as it leads to issues of getting work clearances, supply chain problems, and others. It was also critical for us to ensure the safety and physical wellbeing of our people in the areas of operations.”
“We have harnessed the benefits of technology to restructure our working methodology for better coordination, accountability, and governance between the various departments.”
Arup Kumar Ray
Project Manager,
JSW Dolvi Projects
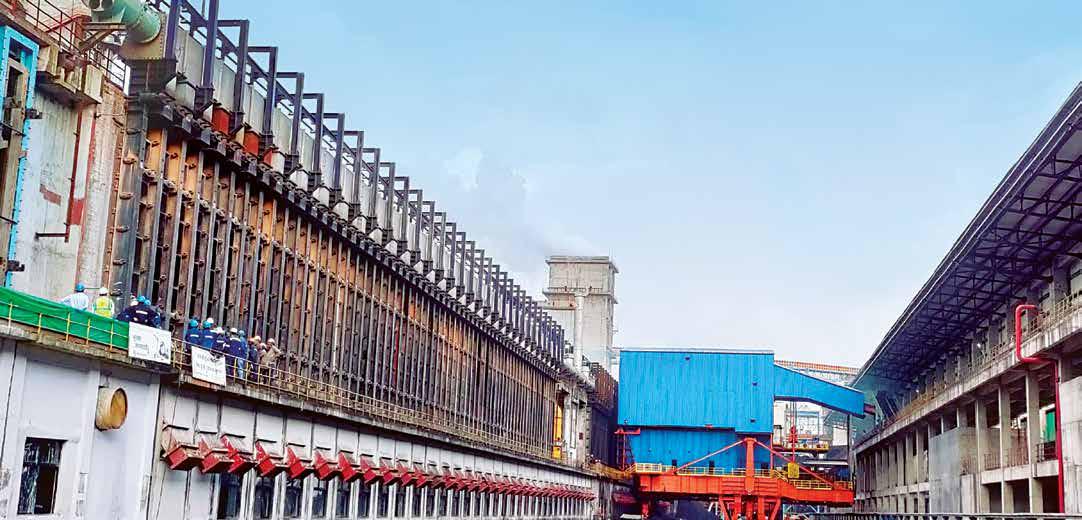
Coke Oven Battery, Phase 2
“Working in a congested space and constantly changing work dynamics required precise coordination and logistic planning. It was also critical for us to ensure the safety and physical well-being of our people in the areas of operations.”
Shastha Kiran Manai
Planning Manager,
JSW Dolvi Projects
Adopting the jacking method in the BPP area instead of crane/hydra to erect six ALS tanks reduced the danger of working at heights to a mere 5%, and the quality of joint welding was maintained. Resorting to modular erection for the scrubber inlet duct header saved the team time and improved quality. “We proactively engaged with the consultant and clients regarding changes in the structural design, modifications in the crosssections, and installations of permanent platforms as per the construction feasibility to save time, enhance safety, and ensure better maintenance in the future,” remarks Project Manager S Gokulan. A host of digital tools including the Conquer, Procube, Safety, SLIM & WISA apps improved efficiencies.
The first Coke push of Battery ‘D’ was delivered on 26th February 2021 and Battery ‘C’ on 15th September 2021, representing the team’s significant achievements.
“We proactively engaged with the consultant and clients regarding changes in the structural design, modifications in the cross-sections, and installations of permanent platforms as per the construction feasibility to save time, enhance safety, and ensure better maintenance in the future.”
S Gokulan
Project Manager,
JSW Dolvi Projects
BLAST FURNACE #2: DELIVERED TOO
Commenced in December 2017, the mandate was to supply and erect Blast Furnace #2 for JSW, the biggest blast furnace in India with an inner volume of 5,358 cum. The team has successfully delivered the project before the contractual handover date of March 2022. Referring to steps taken by his team to overcome issues, Project Manager A Dhanasekar says, “Faced with inadequate storage capacity, we adopted a lean method for site material management with most of the materials stored outside the plant premises and retrieved based on the schedule for installation, which helped us to sequence the materials better too, right from the engineering stage.” To manage plates of 3 m width and thickness ranging between 50 mm and 100 mm in rolling and fabricating the furnace/stove shells, a special rolling machine and CNC machine were installed; with a proper cutting plan, the productivity of the plate bending machine increased and wastage of plates decreased.
“Faced with inadequate storage capacity, we adopted a lean method for site material management with most of the materials stored outside the plant premises and retrieved based on the schedule for installation, which helped us to sequence the materials better too, right from the engineering stage.”
A Dhanasekar
Project Manager,
JSW Dolvi Projects
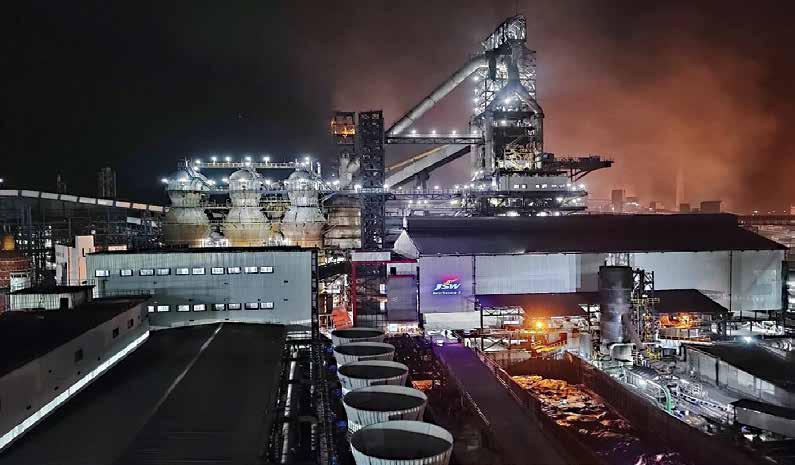
JSW Dolvi Blast Furnace
Efficient logistics management tightened serial operations of several follow-on trades, and converting those trades from serial to parallel operations helped accelerate progress. “One of the unique problems we faced was to identify specially shaped bricks for the dome portion of the furnace, which was critical for final handover and commissioning,” shares Project Manager Sandeep Kaul. A dedicated team got into the details and resolved the issue expeditiously to keep things rolling.
“One of the unique problems we faced was to identify specially shaped bricks for the dome portion of the furnace, which was critical for final handover and commissioning.”
Sandeep Kaul
Project Manager,
JSW Dolvi Projects
“We expedited a full-scale rollout of digital initiatives,” apprises Quality In-charge Simanchala Gouda, “for greater interdepartmental synergy for progress monitoring, material issuance, work permits, inventory management, and workmen induction to curb the spread of the virus and create and maintain a safer workplace.” While Simanchala mentions the appreciation letter from the client, JSW Steel Limited, for maintaining construction quality standards and adhering to ISO 9001:2015 standards, his colleague, EHS In-charge B D Vishwakarma, is delighted that the site has clocked 7.5 million safe manhours, which has also won the client’s appreciation.
“We expedited a full-scale rollout of digital initiatives for greater interdepartmental synergy for progress monitoring, material issuance, work permits, inventory management, and workmen induction to curb the spread of the virus and create and maintain a safer workplace.”
Simanchala Gouda
Quality In-charge,
JSW Dolvi Projects
Being a labour-intensive project site, the huge onus on Debasish Ghosh, Head – Accounts & Administration, and his team was to keep 9,500+ workmen safe and COVID-free. “Keeping them safe and healthy was critical for project progress, as was arranging for industrial oxygen at the height of the scarcity,” he remarks. “Fortunately, we succeeded on both fronts,” he smiles widely.
CONSTRUCTION AND ERECTION OF 2 × 190 TPH / 1 × 140 TPH
CDQ: 100% COMPLETE
Another project to build Coke Dry Quenching (CDQ) plants has been completed by Project Manager R Sivanesan and his team before the scheduled handover date of March 2022. Certain unforeseen circumstances, weather conditions, national lockdowns, reverse migration of labor, supply chain disruptions, and dwindling cash flows threatened to derail their progress. “By revisiting our schedule every week, we bridged the gap between material supply and erection works and handing over of the front for subsequent activities,” says Sivanesan. The team reduced the average collection period, managed adequate inventory to optimize working capital turnover, and subsequently reduced the working capital cycle. “We ensured timely payment to our vendors and subcontractors to pay their workers and keep their storefronts,” chips in Shastha, “and continuously emphasized the need for marginal costing.”
“By revisiting our schedule every week, we bridged the gap between material supply and erection works and handing over of the front for subsequent activities.”
R Sivanesan
Project Manager,
JSW Dolvi Projects
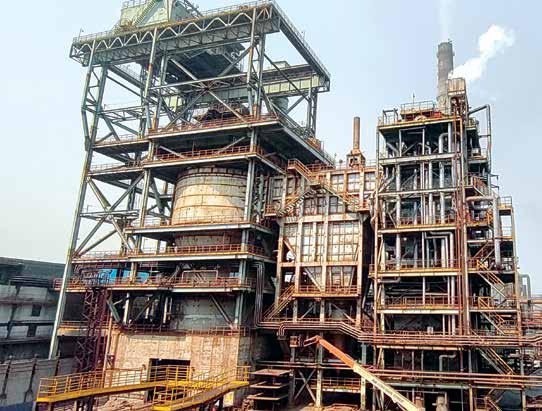
Coke Dry Quenching Plant, Dolvi
A lean and mean method for material procurement (bulk or consumables) and deploying plant and machinery ensured less crowding and more output. “Modular formwork for shuttering works proved beneficial to amplify the number of repetitions and reduced cost and construction time by almost 40%,” smiles Simanchala. “For structural works, we insisted on streamlining fabrication and erection processes, which smoothened material movement even in a constrained environment to overcome re-handling and storage issues.”
Sivanesan proudly shares that the CDQ-1 chamber of 24.5 m height and 11.05 m diameter was erected in 7 parts, and that too in just 96 days against the planned 120 days. The CDQ-2 was commissioned on 7th July 2021, CDQ-1 on 23rd December 2021, and CDQ-3 on 17th January 2022.
SUPPLY AND ERECTION WORK FOR SMS-II – DOLVI: ALMOST THERE
“We have just about 3% work left, which we are sure to complete before our contractual handover date of 30th July 2022,” says a confident T S Muraleedharan, Project Manager. “To overcome the issues of the pandemic, lack of space, supply chain issues, and labour attrition, we concentrated on labour re-mobilization, uninterrupted supply of consumables and materials, maintenance of buffer stock, and greater capacity utilization to carry us through.” Their core strategy was to monitor and control the critical activities to complete their targets in a phased manner. “We divided the project into Stream-1 (Converter-1 & Caster-2) and Stream-2 (Converter-2 & Caster-1) for handover,” informs Shastha, “and kickstarted production with 50% capacity, to keep our customer engaged.”
“To overcome the issues of the pandemic, lack of space, supply chain issues, and labour attrition, we concentrated on labour re-mobilization, uninterrupted supply of consumables and materials, maintenance of buffer stock, and greater capacity utilization to carry us through.”
T S Muraleedharan
Project Manager, JSW Dolvi Projects
Their plan was further divided into monthly, weekly, and daily targets, which were regularly tracked with Procube. The QR code system used for the supply of steel structures made material tracing easy. Simanchala stresses on the mantra of ‘doing it right the first time’. “We encourage our workmen and subcontracting partners to work with quality consciousness and acknowledge their efforts with rewards and gifts. Our quality assurance system has been widely appreciated by our costumer, owing to lower welding defective rates of less than 1%,” he beams. “We logged in 23,097 EHS observations online through the Safety App and resolved all of them,” shares EHS In-charge Satish Chandra Yadav.
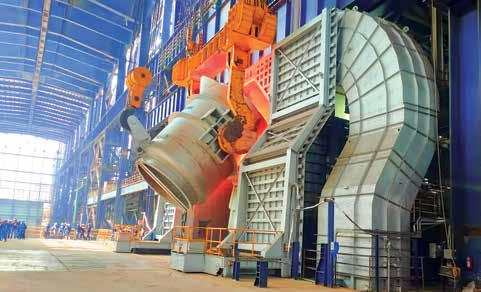
SMS-2 350 Ton Converter-1
The two Project Managers at site, Muraleedharan and Jagdish Shenoy, are proud that India’s first 350 MT capacity converter has been erected with a crawler mounted crane, and the country’s first 550 MT capacity EOT was erected in modular form. “We are proud that Stream-1 was commissioned on 16th October 2021. The Slab Caster-1 part of Stream-2 was commissioned on 6th March 2022, and the mechanical work for Converter-2 is expected to be complete by end-March 2022,” Jagdish signs off with a smile.
“We are proud that Stream-1 was commissioned on 16th October 2021. The Slab Caster-1 part of Stream-2 was commissioned on 6th March 2022, and the mechanical work for Converter-2 is expected to be complete by end-March 2022.”
Jagdish Shenoy
Project Manager, JSW Dolvi Projects
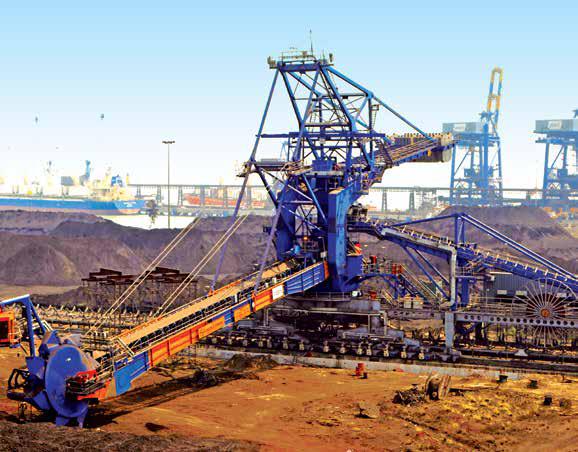
Stacker Reclaimer-8 at Dhamra
DHAMRA PORT PROJECT
100% DELIVERED
The mandate before Project Manager Sunit Das and his project team was the design, engineering, manufacturing, transportation, erection, testing, and commissioning of five Bucket Wheel Stacker Reclaimers for the Dhamra Port Company Limited (DPCL), Dhamra, Odisha, with the add-on job of design, engineering, manufacturing, transportation, erection, testing, and commissioning of BWSR-9 & BWR3 Stockyard machines shifted from Mundra to Dhamra. The project kicked off on 16th September 2016 and was delivered on 31st December 2021, albeit an extended date.
“We took the changes in our stride by negotiating hard with the client on each occasion and got the LOI amended with proper cost increments so that our profitability is maintained as per ACE.”
Sunit Das
Project Manager,
Dhamra Port Project
The team had their fair share of challenges. Connectivity was a major logistics issue to shift material, especially ODC material, considering the remoteness of the Dhamra Port. To overcome this impediment, the team liaised with the local police for escort vehicles to ensure smooth transport. Several cyclones blew their way: Titli, Fani, Amphan, and Yaas, though it was the Bulbul Cyclone that wreaked most damage. Planning Manager Vijayendra Brijmohan Sharma moans that one of their machines (the SR-4A) under construction toppled over. “The machine had to be totally dismantled, all parts inspected, damaged parts replaced, and then re-erected. A proper insurance claim was lodged and is under settlement with insurance departments,” he informs.
“The machine had to be totally dismantled, all parts inspected, damaged parts replaced, and then re-erected. A proper insurance claim was lodged and is under settlement with insurance departments.”
Vijayendra Brijmohan Sharma
Planning Manager,
Dhamra Port Project
A major headache for Sunit was the frequent changes in the contract. “Midstream, our initial order for five machines was reduced to 4, and in the add-on job, the client changed the machine nomenclature twice,” he says. “We took the changes in our stride by negotiating hard with the client on each occasion and got the LOI amended with proper cost increments so that our profitability is maintained as per ACE,” he says, determination in his set features. Changing the nomenclature of the machines from Reclaimer to Stacker called for additional structures to be shifted from their Mundra port and retro fitted at Dhamra. “The equipment parts were dismantled and cut at the Mundra port and successfully re-fitted and erected at Dhamra,” says a pleased Quality In-charge N Kalaiselvan. “This called for precision work with very little margin for error. The machines were commissioned smoothly,” he smiles.
“We have commissioned four highcapacity ‘C’ frame Stacker Reclaimers, BWSR – 5, 6, 7 & 8, only for the second time by L&T after the Vizag MHS project,” says a proud Sunit. “All work done, and final payment settled with the client. Final bill has been raised and the payment is expected in the last quarter of 2021–22,” he sums up.
BOKARO PROJECT
ONLY FAC IS BALANCE
The Slab Caster project for the Bokaro Plant was awarded on 2nd July 2015, with 13th April 2022, as an agreed date of delivery. Project Manager Paramhans Singh can sit back in satisfaction, for his team has completed the execution 100%; the Preliminary Acceptance Certificate, Commissioning Certificate, and Performance Guarantee Test are over, with only the Final Acceptance Certificate remaining. “Being a brown field project, it was tough taking fronts from the client,” he remarks, “but our success in that regard has been primarily the reason why we have delivered the project in time.”
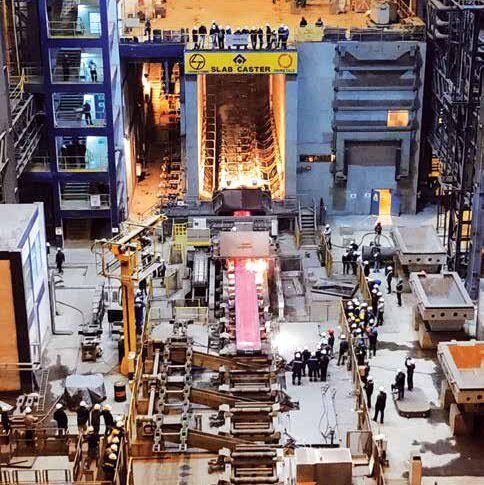
“Being a brown field project, it was tough taking fronts from the client but our success on that front has been primarily the reason why we have delivered the project in time.”
Paramhans Singh
Project Manager, Bokaro Project
Planning Manager Srinivas Pabolu’s philosophy was to identify and mobilize the required resources to accelerate progress. “I strongly believe that having all the required resources will push the project to completion even before the planned timelines,” he says emphatically. “Especially thanks to digital tools, the captured data is readily available for better analysis and interpretation. Additionally, we monitored the progress and workmen and P&M productivity real-time, which enabled faster decision making.” To sum up, he shares, with a beaming smile, “Commissioning the Bokaro caster project after years of hard work and struggle will always be cherished by me.”
“I strongly believe that having all the required resources will push the project to completion even before the planned timelines. Especially thanks to digital tools, the captured data is readily available for better analysis and interpretation.”
Srinivas Pabolu
Planning Manager, Bokaro Project
CHP & AHP, TANDA
THE FINAL LEAP
Project Manager Matta Satyanarayan quickly reels off some significant achievements of the teams at his Coal Handling Plant (CHP) and Ash Handling Plant (AHP) projects. “At the CHP, we have safely constructed three Wagon Tipplers to quality and handed over the CHP systems to the client well ahead of the plant COD,” he sounds pleased, having completed 99.1% of the project. At the AHP project, where only about 2.7% is pending, Matta says, “We have completed the balance installation and commissioning of the entire Ash Handling Systems within 92 days of final front release by the client and have handed over the AHP systems well ahead of plant COD.”
“This is one of India’s best AHP plants in terms of timelines and performance, and the plant has been continuously in operation for more than 14 months after final commissioning and COD.”
Matta Satyanarayan
Project Manager,
CHP & AHP, Tanda
At the CHP project, things did not start well as the work fronts for the Wagon Tippler area was released by the client after a delay of 366 days from the original L2 schedule. “The excavation and dewatering works were challenging as the area was located very close to an existing earthen raw water reservoir for the Stage I plant, with the result that the soil was very silty with a high water table of approximately 6 m at the construction area,” laments Planning Manager Atanu Saha. A special deep de-watering method was adopted in consultation with EDRC, and each Wagon Tippler was constructed in a phased manner to overcome the challenges. “To achieve our contractual completion targets, various other resources were deployed in line with the budget to improve productivity and offset the delay from the client’s end,” Atanu adds.
“To achieve our contractual completion targets, various other resources were deployed in line with the budget to improve productivity and offset the delay from the client’s end. ”
Atanu Saha
Planning Manager,
CHP & AHP, Tanda
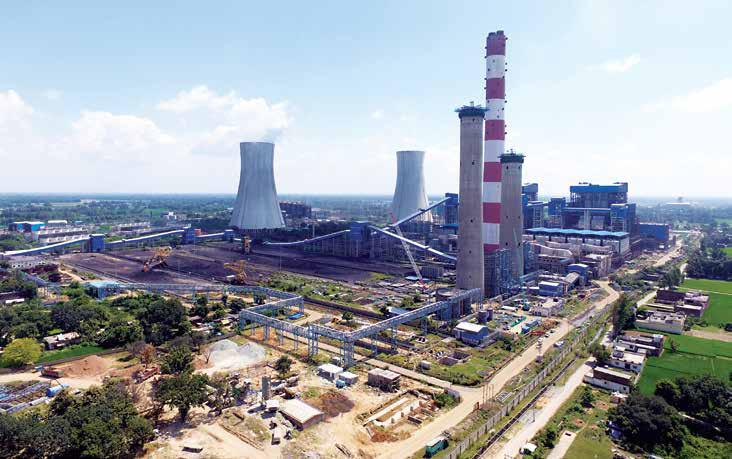
CHP and AHP at Tanda
The story was much the same at the AHP project as the release of the clear fronts was delayed by 611 days, and since the targets for COD of Unit #5 (660 MW) were set by the Ministry of Power, Government of India, for September 2019, there was no question of the team not readying the plant for load synchronization as per schedule. “Working round the clock, we achieved the overall system readiness within 92 days of the final front release,” shares a visibly proud Mechanical In-charge Kaushik Mitra, “and the COD of Unit #5 was achieved as per target, which delighted the client, acknowledged by a Certificate of Appreciation.”
“Working round the clock, we achieved the overall system readiness within 92 days of the final front release and the COD of Unit #5 was achieved as per target, which delighted the client.”
Kaushik Mitra
Mechanical In-charge,
CHP & AHP, Tanda
Matta adds, “This is one of India’s best AHP plants in terms of timelines and performance, and the plant has been continuously in operation for more than 14 months after final commissioning and COD.” Strategy wise, the team modularized the erection of structures with maximum equipment and electrical installations. Micro-planning and the agility to change as situations demanded have been other reasons for their success.
“Minor punch points are being taken care of with skeleton resources,” shares Matta. “In the CHP package, a few civil fronts related to drains, etc. are under release by the client, and the work is expected to be completed within the agreed revised schedule. PG Tests are complete, and evaluations are under progress too. Defect Liability Periods of handed-over systems are at the completion stages, and the Operational Acceptance Certificate is expected to be released by the client shortly as per contractual conditions.”
MANSOURAH–MASSARAH GOLD PROJECT
GUNNING FOR A SEPTEMBER 2022 HANDOVER
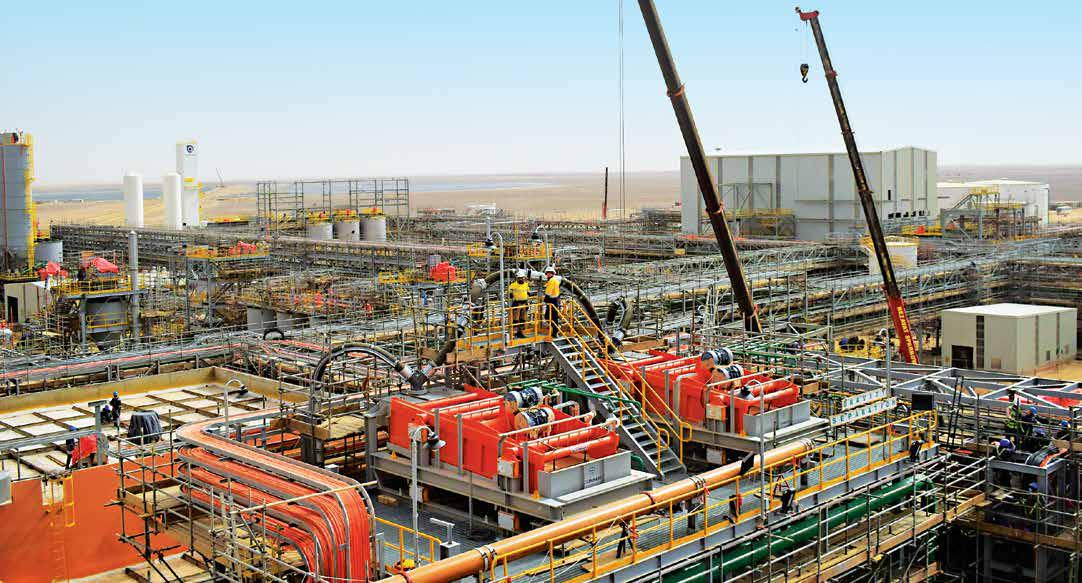
Bird’s-eye view of the Gold Process Plant
Construction Director Pranava Kumar Vatsa seems to have things under control as he shares the extent of completion of the different aspects of this huge and challenging project: “We have completed 85% of the project, with 95% of civil and structural works, 90% of mechanical works, 82% of piping, 77% of electrical, 56% of instrumentation, and 30% of automation. The construction of the substations is over, mechanical completion has started, and No Load trails have begun sequentially as per the Process Flow Diagram starting with the crushing system.”
“We have completed 85% of the project, with 95% of civil and structural works, 90% of mechanical works, 82% of piping, 77% of electrical, 56% of instrumentation, and 30% of automation.”
Pranava Kumar Vatsa
Construction Director,
Mansourah–Massarah Gold Project
Situated in the back of beyond, deep inside the uninhabited Arabian desert, the team had initially no access to electricity, water, or mobile connectivity. “We actually built a telecommunication infrastructure to avail of the internet and make voice calls,” smiles Planning Manager Mahesh Kommuru. Though isolated, the multiple waves of the pandemic disrupted progress, but as Mahesh adds, “A robust leadership and a committed workforce, with effective COVID and customer management, helped us to overcome the challenges.”
“A robust leadership and a committed workforce, with effective COVID and customer management, helped us to overcome the challenges.”
Mahesh Kommuru
Planning Manager,
Mansourah–Massarah Gold Project
Digitalization is playing a key role in driving the project forward. “We use Primavera for project monitoring, linking progress with resources,” points out Digital Officer Nawaz Haider. “The entire plant engineering has been completed on the AVEVA E3D platform and shared across the site for seamless model reviews. BIM 4D Modelling helps us to review physical progress, we use the WRENCH system for all the engineering documents and the Aconex System for all documentation.” For piping, the EXINT software has been implemented not only for fabrication but also for site installation to track piping spools from manufacturing to installation, and the entire workforce is monitored through the locally purchased system (DLIHR).
“We use Primavera for project monitoring, linking progress with resources. The entire plant engineering has been completed on the AVEVA E3D platform and shared across the site for seamless model reviews. BIM 4D Modelling helps us to review physical progress, we use the WRENCH system for all the engineering documents and the Aconex System for all documentation.”
Nawaz Haider
Digital Officer,
Mansourah–Massarah Gold Project
The issue of procurement has been addressed by engaging local vendors from KSA and using and promoting in-house L&T products and facilities like apron feeders and pipe spooling yard. “We introduced the concept of a Package Manager with end-to-end responsibility from order finalization to equipment delivery to site, commissioning and handover,” explains Mahesh. Equipment packages like water systems and pre-fab substations have been modularized.
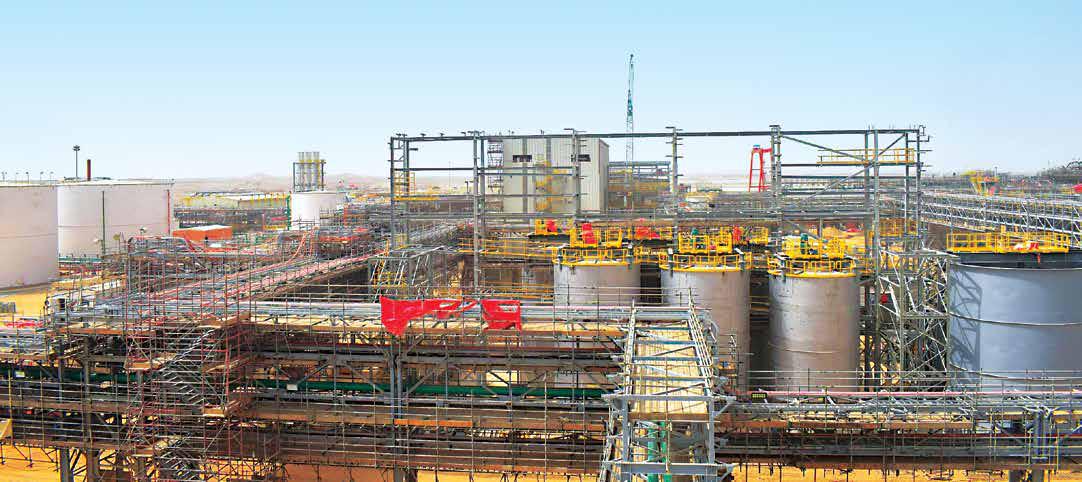
A view of Neutralization Tanks and Raw & Filter Water Storage
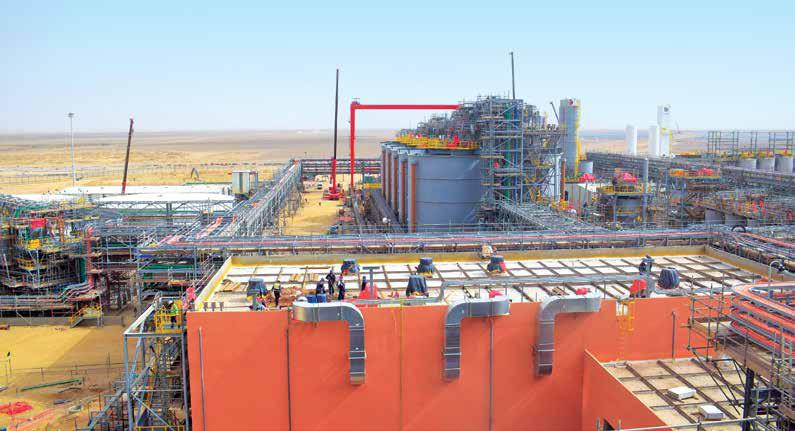
Bird’s-eye view of the Carbon in Leach, Cyanide Storage, and Intense Leaching Process
The project has thus far clocked 10 million safe manhours, and EHS In-charge Bikash Parida’s efforts are to maintain his clean safety record. “We have a School of Risk Management that has recorded 1.5 million training manhours covering > 25,000 participants, defect-free weld rate of 99.25% in API 650 tanks, 100% defect-free weld in ASME piping, and zero failure of concrete test cylinders in compressive strength tests.” The site has recorded two consecutive weeks of progress more than 1.9%.
“We have a School of Risk Management that has recorded 1.5 million training manhours covering > 25,000 participants, defect-free weld rate of 99.25% in API 650 tanks, 100% defectfree weld in ASME piping, and zero failure of concrete test cylinders in compressive strength tests.”
Bikash Parida
EHS In-charge,
Mansourah–Massarah Gold Project
As the project guns for completion, Pranava says, “All systems and subsystems have been mapped, and dedicated taskforces work with the senior project leadership’s monitoring.” The next three months of January, February, and March have been earmarked for No Load and Load Trials leading up to the Integrated Test Run. “This includes 21 km GRE pipeline bringing water, the most important utility in the gold process, from the Take Over Point to storage tanks,” informs Quality In-charge E Sivasubramani. “In addition, the communication circuit (Crushers, Screens, Apron and Belt Conveyors, Ball Mill, 10,000 T Storage Silo with associated electrics, firefighting, etc.), hydrometallurgical circuit, and the tailing management facility are in place.” The power plant, which is also under L&T’s scope, will have the engines online progressively in phases to match the commissioning plan.