RIDING ON DIGITAL SOLUTIONS, B&F PROJECTS RACE AGAINST TIME TO MAKE UP FOR LOST GROUND
Across segments and geographies, B&F projects are racing against time to make up for lost time and ground caused by the pandemic. A measure of this feverish action can be seen at the Hyderabad International Airport expansion project where Project Director, C H Anil Kumar, and his team have been focusing all their energies to commission a crucial taxiway. “The 2.3 km long Taxiway – B (Parallel) bisects the terminal and the runway, and its commissioning was critical considering the operational difficulties of constructing in a fully functioning airport.” The junctions of this parallel taxiway were significant considering the operation of stands and ICAO norms. The team had to execute each junction in 10 days as per the stringent NOTAM period along with operational realignment.
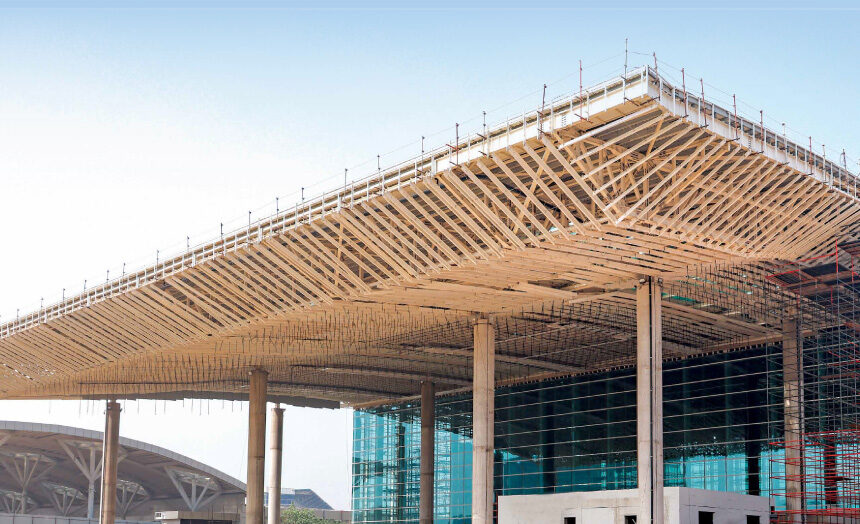
Work in Progress for Arrival Part of the Terminal Building at DIAL, T2 Project
“The 2.3 km long Taxiway – B (Parallel) bisects the terminal and the runway, and its commissioning was critical considering the operational difficulties of constructing in a fully functioning airport.”
C H Anil Kumar
Project Director, HIAL Expansion Project
“We meticulously planned the operation like shutdown works with hourly schedules including flight movements and GSE access,” informs Deputy Project Director, P Venugopal Kurup. “We carefully estimated our resource requirements and mobilized them appropriately before taking up the critical works. Very significantly,” he adds, “the taxiway was commissioned along with the Taxiway Centerline Light which is perhaps accomplished for the first time in a fully operational airport.”
“We carefully estimated our resource requirements and mobilized them appropriately before taking up the critical works. Very significantly the taxiway was commissioned along with the Taxiway Centerline Light which is perhaps for the first time in a fully operational airport.”
P Venugopal Kurup
Deputy Project Director, HIAL Expansion Project
Other significant milestones accomplished by the Airside team at HIAL led by Airsides Head, Rajesh Shukla supported by Airsides In-charge, Pankaj Rai amid constraints within the operational airport were to commission the West Apron (6 Stands) including taxiways, South Remote Apron (24 Stands) including taxiways and the fuel hydrant systems. The project involves expansion of the terminal building, Airside works, 1.7 lakhs sqm of rigid pavement, 3.7 lakhs sqm of flexible pavements and increasing the number of stands from 39 to 98 to meet the forecasted needs of 34 MPPA.
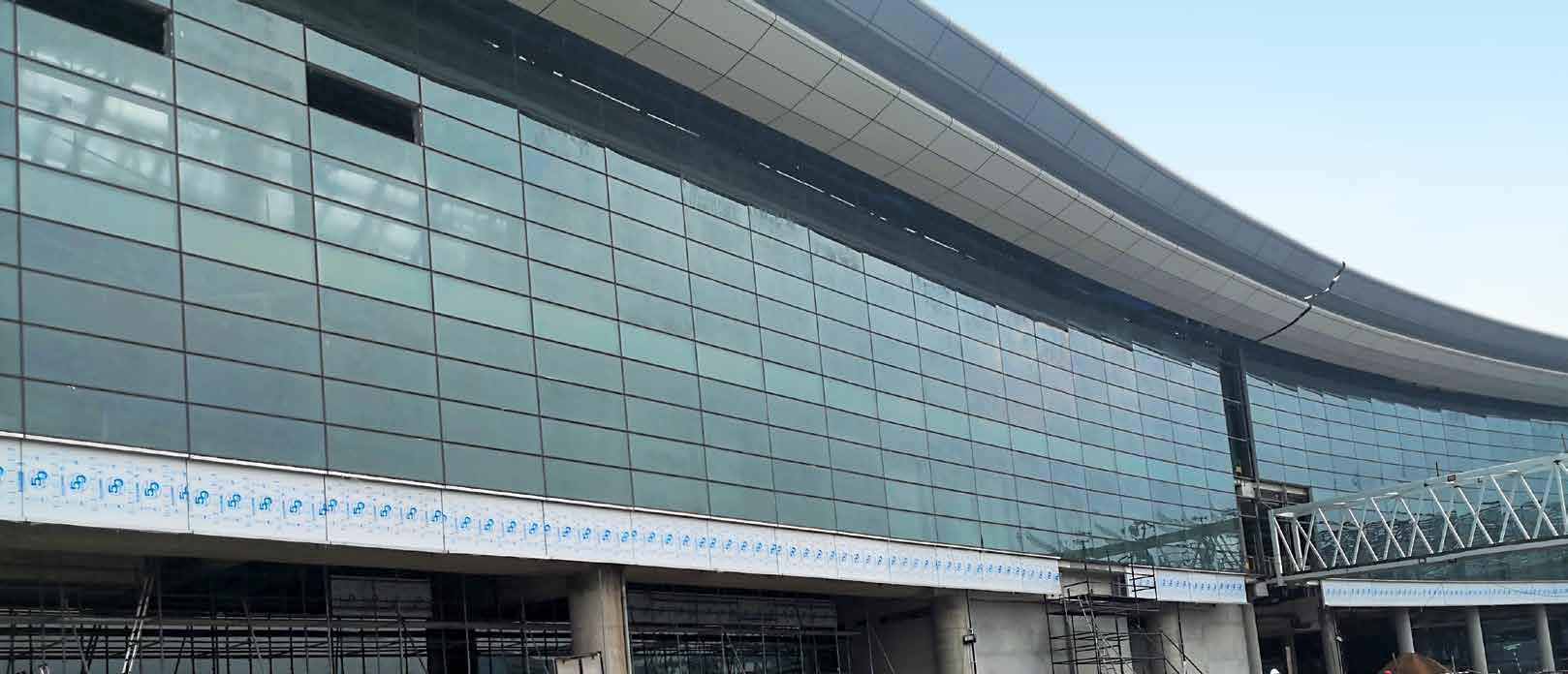
Hyderabad International Airport Expansion Project
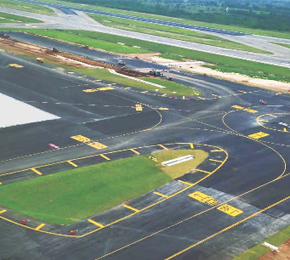
Runway at HIAL Expansion Project
DIAL lands a major milestone
Since the commencement of the Delhi International Airport project in March 2019, it has been a saga of start, stop, fly, halt, restart and take off for Project Director-DIAL, B&F, Jitender Aggarwal and team. Seven months of design development and setting up of infrastructure was followed by three months of aggressive procurement only for work to be halted in its tracks by the NGT ban. Thereafter, pace was just picking up when the pandemic struck. “We, L&T-ites, are known for taking setbacks in our stride,” says Jitender with a shake of his head, “so with some smart thinking, strategizing, adopting digitalization and advanced monitoring techniques, we have started to catch up on lost time.” The most critical task before them was to complete the high side MEP installation works along with the remaining civil works to clear the front for services.
“We, L&T-ites, are known for taking setbacks in our stride so with some smart thinking, strategizing, adopting digitalization and advanced monitoring techniques, we have started to catch up on lost time.”
Jitender Aggarwal
Project Director – DIAL, B&F
“We quickly achieved our objective of ordering all the major high side equipment within just four months from July to October 2020 with the help of Primavera supported by Procube,” shares a satisfied Head – Construction, Ravi Kadam. The equipment started arriving and getting installed at site by November and the team commenced standalone testing of the equipment by February 21. “Our success is thanks to our excellent planning of interfacing, sequencing, categorizing activities, mobilizing adequate workmen with the required skill level with all the necessary tools, plants and machinery prepared and tracked,” sums up Ravi.
“Our success is thanks to our excellent planning of interfacing, sequencing, categorizing activities, mobilizing adequate workmen with the required skill level with all the necessary tools, plants and machinery prepared and tracked.”
Ravi Kadam
Head – Construction, Delhi International Airport
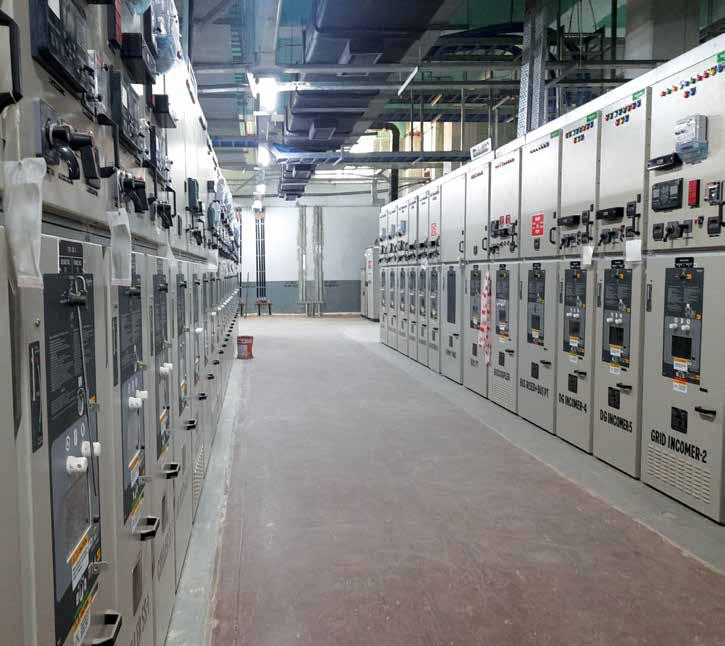
Electrical Room – DIAL T2
The construction process is notorious for its unpredictability, construction managers must be adept to manage several variables, many at the same time, just as Anuj Chauhan, Head – Mechanical Works and his team were facing. “Apart from the stringent pandemic restrictions, there were stage checking and inspections in between installations with interlinked installations involving various services.” Maintaining their workmen was another tough task but the team succeeded in creating back-up manpower that came in handy when the farmer agitation in Delhi threatened to disrupt progress yet again.
Digitalization makes a huge difference
“Tracking with IoT showed us our actual rate of progress against the asking rate,” says Ravi, “while Power BI helped to align resources and monitor resources cost effectively to assess the asking and achieved rates and assetwise & vendor-wise productivity.” 4D BIM is proving extremely useful for the execution team to understand workflow processes to reduce rework and improve productivity. The adoption of precast construction for the curved column shutters and the service tunnel, a critical deliverable for Phase 1 as the tunnel links the Utility Building with the Terminal Building through a Node, helped ensure that civil, finishes and MEP works could be executed parallelly.
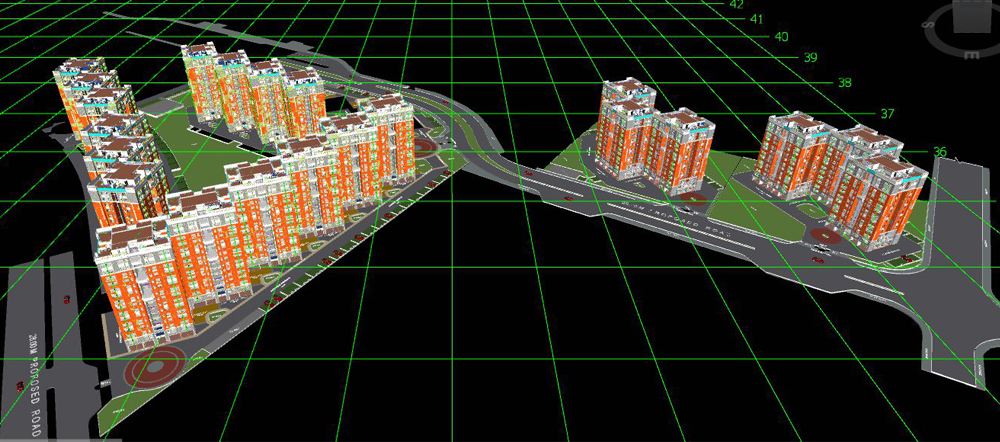
BIM Model – CIDCO Package IV, Bamandongri, Navi Mumbai
BIM is proving to be a huge boost to fast-forward progress at the residential CIDCO project in New Mumbai with the mandate to construct some 23,000 units in a record 42 months. Considering the enormity of the project and its demanding schedule, Project Director, O V Divakar had little option but to adopt digital tools that have, as he says, with a chuckle “become a way of life during execution.”
“Early adoption of BIM strengthened the site team’s arm to plan, monitor progress and eventually invoice on time, based on automated quantity take-offs of the completed work.”
K Senou
Head – Technical Services
The EDRC and BIM teams took up the challenge of building the tower models that include architectural, structural and MEP detailing. “Early adoption of BIM strengthened the site team’s arm to plan, monitor progress and eventually invoice on time, based on automated quantity take-offs of the completed work,” says K Senou, Head – Technical Services. Presently, they interact daily with more than 500 drawings and 80 models on various RFIs with the latest versions of drawings with 3D models instantly available on the BIM 360 platform. Not only major quantities such as concrete and shuttering but also the generally time-consuming quantity take-offs for finishes such as doors, jambs, conduits, tile skirtings are measured on models. Project progress is tracked on Navisworks 4D models with Planned versus Actual status while the Forge platform allows for automated comparison of actual progress to planned progress and flag deviations.
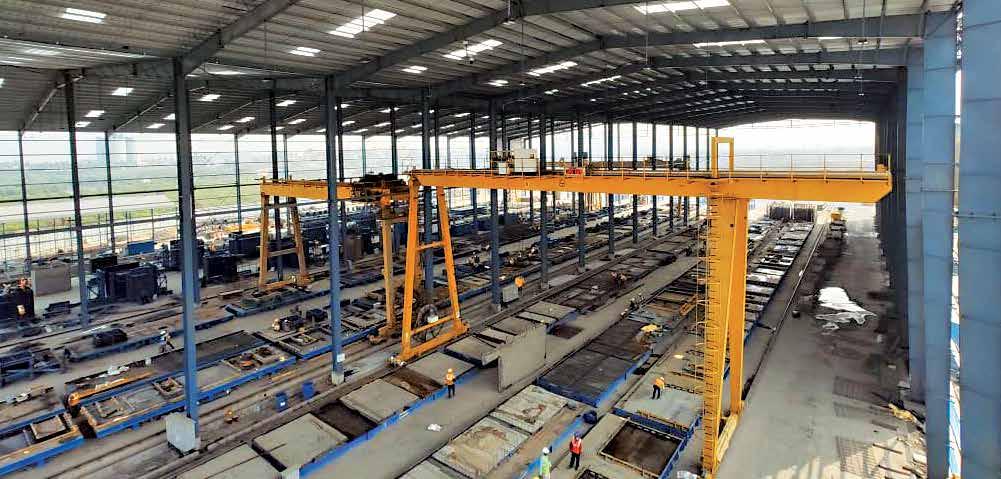
Precast Yard – CIDCO, Navi Mumbai
Precast DigiCast App is making life easier at CIDCO
Head – Initiatives (Precast), Amit Barde, has a lot to deliver: about 7,400 units, 1.15 lakh elements translating to 35 floors a month and about 10 flats a day. “It is almost impossible to deliver such a massive element count with conventional tools, so we opted for the Precast DigiCast App,” he says, “that provides mould to element mapping, yard storage configuration, trailer master to track each element right from mould preparation to site installation through its lifecycle with digital checklists and Bill of Materials extracted by BIM.” The Tekla Precast BIM, the backbone of the DigiCast App, developed by EDRC, models typical towers with even reinforcement, connection detailing along with all MEP conduit routings such that 2D production drawings can be generated directly through the 3D model at a click. Tekla tracks production of precast elements in interlinked stages with timely notifications on pending activities for efficient production, based on QR code scans. The despatch team that struggles with about 150 elements to ship a day at peak, has found life easier as each produced element, stored in a predetermined yard location, can be easily looked up on the portal.
“DigiCast tracks project progress in terms of daily production, ‘live’ asking rates with customized dashboards for quick snapshots on tower wise progress as well as overall material consumption.”
Amit Barde
Head – Initiatives (Precast), CIDCO Project, Mumbai
Amit is grateful to Sudheer Bommi, the SPOC from EDRC and his team, for DigiCast. “It tracks project progress in terms of daily production, ‘live’ asking rates with customized dashboards for quick snapshots on tower wise progress as well as overall material consumption,” shares Amit. “It even tracks consumables and material consumption making procurement much easier.”
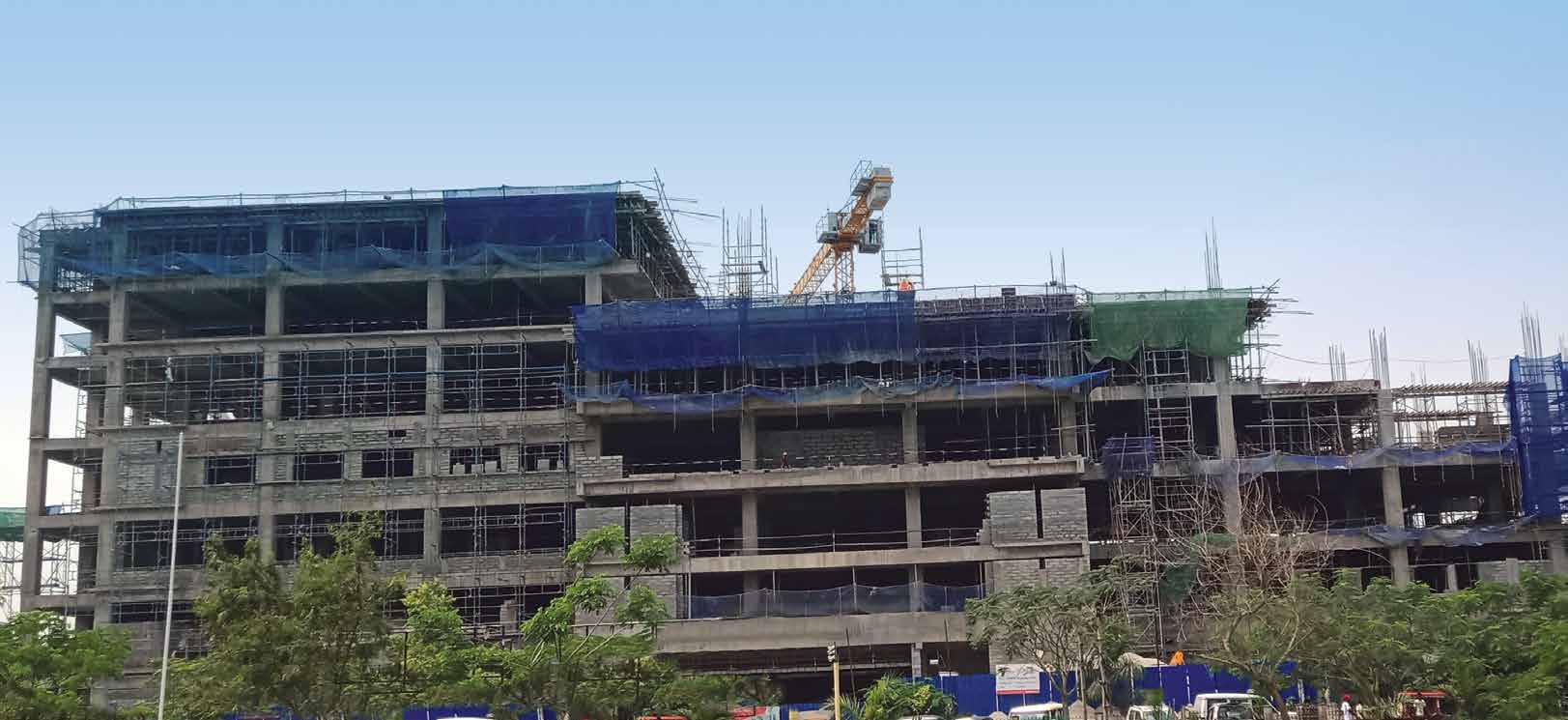
Assam Cancer Care Foundation Hospitals, Barpeta
BIM works just as well with hospitals as with an educational institution
The Assam Cancer Care Foundation Hospitals (ACCF) is a landmark project of 18 hospitals spread across the state of Assam of which work is proceeding at 10 locations presently. “We have implemented BIM 4D at the State Cancer Institute, Guwahati which is the largest in terms of both value and built-up area,” informs Project Director, Anjan Mohapatro, “that integrates the construction schedule with the 3D model.” In their effort to overcome the retarding impact of the pandemic, the team has incorporated both the original baseline schedule as well as the catch-up one in BIM 4D to gauge and monitor progress across structural, architectural and MEP disciplines. “To ensure that maximum people have access to the latest to monitor project progress, we have taken the 4D model ‘live’ to our in-house FORGE VIP platform, which runs on the cloud on any web browser,” informs Biplab Bhattacharjee, (Assistant Manager – Civil).
“We have implemented BIM 4D at the State Cancer Institute, Guwahati which is the largest in terms of both value and built-up area that integrates the construction schedule with the 3D model.”
Anjan Mohapatro
Project Director, Assam Cancer Care Foundation Hospitals
The advantages of 4D BIM to the ACCF team are many: they can plan for an extra pour to cast the slab in the hospital portion that was evident only from the visual model due to the peculiar shape of a small portion of the slab. It visually and accurately depicts delays in construction, element-wise and floor-wise quantification of concrete helps to plan pour schedules, it reveals potential clashes and gives the team a comprehensive grasp of actual deliverables.
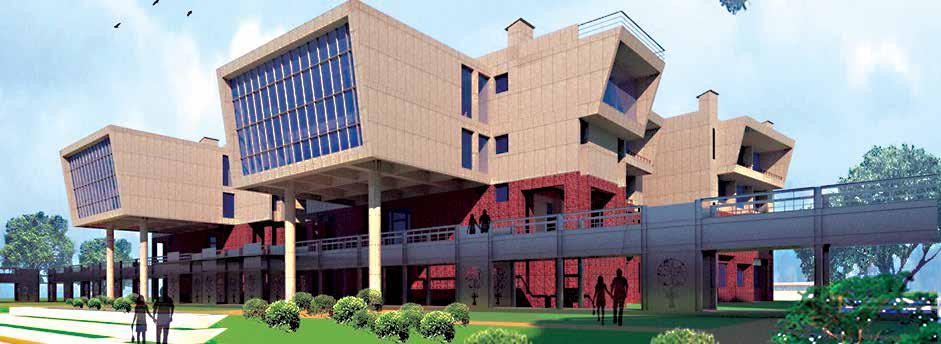
IIT Bhilai
Project Manager, Rajesh Shukla is happy with the progress that his team is making at his IIT, Bhillai project for progress monitoring is easy for him and his team with BIM. “BIM is helping us across functions like document management, quantity take-off for client invoicing & billing, procurement and shuttering models, BBS generation & shop drawings for reinforcement models, develop shop drawings and identify constructability issues.”
“BIM is helping us across functions like document management, quantity take-off for client invoicing & billing, procurement and shuttering models, BBS generation & shop drawings for reinforcement models, develop shop drawings and identify constructability issues.”
Rajesh Shukla
Project Manager, IIT, Bhillai Project
Digitalization drives efficiencies at RAMCO
“Initially, erecting, lifting and stabilizing a single truss of 74 MT and 60 m long in the circular lime storage shed would take us 11 days,” explains Project Manager, Girish Kumar P at his RAMCO site in Kolimigundla, “but we have optimised it to a cycle time of just 3 days using a 500 MT crane achieved for the first time in a cement plant!” With the Last Planner System (LPS), they identified that using the same manpower for both assembly and erection was delaying the subsequent process of lifting the truss. “We arranged for separate teams for non-truss assembly and erection,” informs Fayaz Ahmed, Manager – Mechanical, “and we were immediately able to reduce cycle time by about 3 times!” Similarly, in Clinker Silo 1, to construct a 40 m high silo wall, the cycle time for a 3.6 M lift was 15 days. “With LPS, we studied the cycle time for two lifts,” shares Jagadeeswaran, Senior Engineer – Civil, “and then changed the fitter-to-helper ratio for Jumpform installation. We also reviewed our subcontractors cycle time for their PT works and by establishing better protocols for better monitoring and coordination, we gradually reduced the cycle time from 15 to 10 days.”
“Initially, erecting, lifting and stabilizing a single truss of 74 MT and 60 m long in the circular lime storage shed would take us 11 days but we have optimised it to a cycle time of just 3 days using a 500 MT crane.”
Girish Kumar P
Project Manager, RAMCO, Kolimigundla
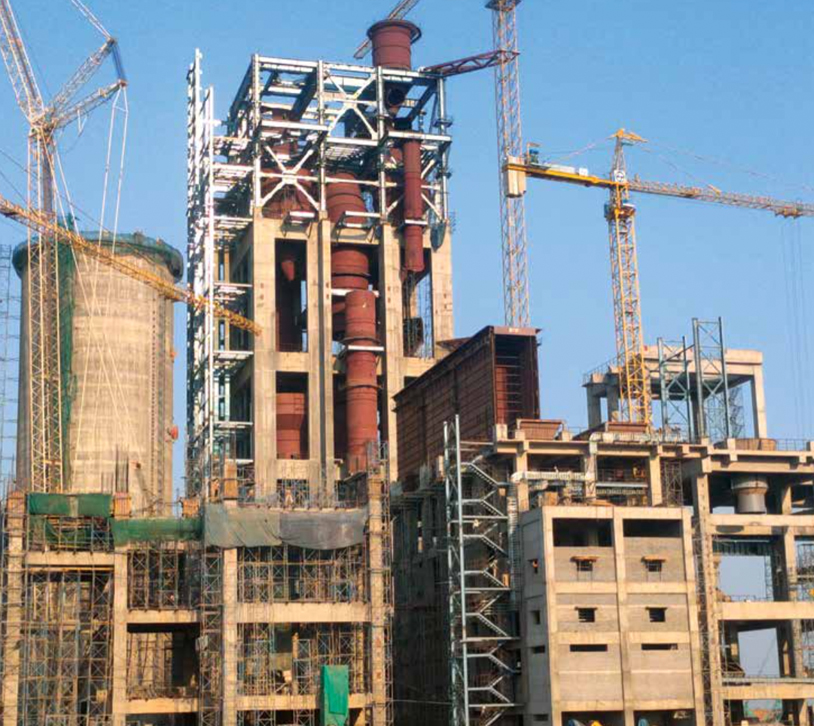
RAMCO Kolimigundla
LPS came in handy again for the team to complete a concrete slab of 2,000 cum in a matter of three and half days, 172 MT of reinforcements and 30 MT of insert plate works in the Clinker Silo 2, in July 2020 with just 40 workmen. “We minutely monitored daily progress on a daily track sheet, extending working hours as per the schedule to complete the entire exercise in just 25 days,” says a pleased Reegan Paul Singh, Construction Manager – Civil.
Although the return to normalcy has been an uphill struggle, project leaders and their teams at B&F are doing their best to come to terms with the new normal and maintain progress. We wish them the very best!