TEAM BIAL, BEATING ALL ODDS TO
THE FINISH LINE!
Amidst the scissor and spider lifts, the BIAL Terminal 2 project site is a beehive of activity. Even as workmen
scurry around, engineers shout instructions, materials get loaded and unloaded, Project Director, J K Shivaraj, and
Deputy Project Director, K P Maheswarappa, can be spotted having an animated discussion with the team. In the background, are the golden hues of the engineered bamboo ceiling and the bells and veils section distinctive of
the new Terminal 2. The duo exudes an air of purpose, confident in the knowledge that their team will deliver the
mandate comfortably. They wouldn’t have it any other way, in any case.
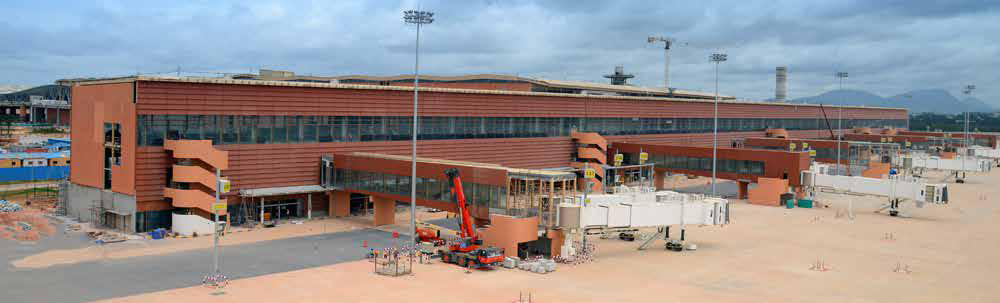
“Things, however, were dramatically different to start with for us,” comments Shivaraj. “As a team we have had to go through a lot. Ours is really a story of struggle and triumph, overcoming disruptions to bring to reality what is conceived as an ‘airport terminal inside a garden’.”
“Things, however, were dramatically different to start with for us. As a team we have had to go through a lot. Ours is really a story of struggle and triumph, overcoming disruptions to bring to reality what is conceived as an ‘airport terminal inside
a garden’. “
J K Shivaraj
Project Director
Green Terminal – an integration of natural elements
Pivoted on the concept of ‘a terminal in a garden’, the architecture of Terminal 2 integrates several natural elements such as clay, bricks, bamboo, rattan, and extensive landscape. A lagoon with a big artificial forest belt around it, a multimodal transport hub, including the Metro, provisions for solar panels on the roof, artificial waterfalls, elevated walkways, and green seating areas are among its standout features.
Embracing innovation to overcome execution challenges
While the structural system of the passenger terminal building is a conventional RC beam slab system supported by nonductile RC columns, its envelope is designed with a standing seam metal roof system resting on steel beams and tapering girders supported on built-up cruciform steel columns raising above the departure & retail mezzanine levels (levels 3 & 4). The 18 m main steel beam spans connect the steel columns and secondary steel beams with intervals
at 6 m, bifurcating the spans into 3 segments.
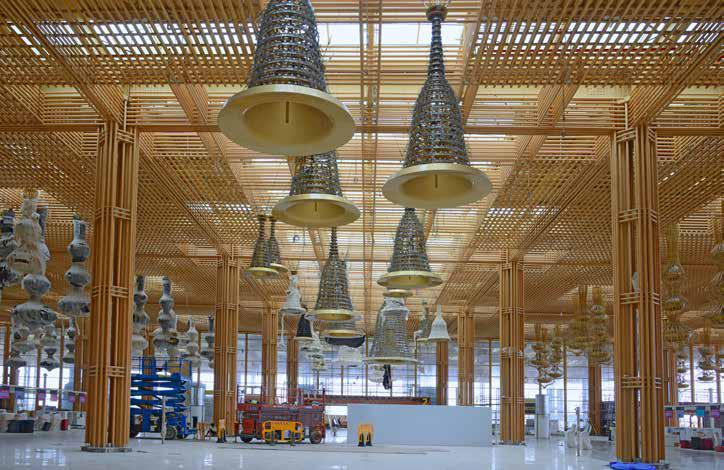
K P Maheshwarappa speaks of several innovative methods adopted to overcome challenges, save cost, and speed up execution. “We realized that on the Departure level RCC slab, heavy cranes could not be mounted. An option would have been to use 750 tonne cranes at the ground level which were not viable in terms of cost, time, availability and so on. We came up with a solution of having a supporting structure or an enabling platform on top of the RCC slab supported on main beams from which we could use much smaller 50/60 tonne cranes to do the structural steel erection. This out of the box thinking helped us complete all the structural steel works above the departure level of the terminal and that, in turn, greatly helped in hastening the works in the piers, forecourt, elevated corridors, multi modal transport hub facility and structural steel work for all pavilions, terminals and ancillary structures.”
“We came up with a solution of having a supporting structure or an enabling platform on top of the RCC slab supported on main beams from which we could use much smaller 50/60 tonne cranes to do the structural steel erection.”
K P Maheshwarappa
Deputy Project Director
Erection of bells and veils in the Departure level ceiling amidst the intricately spaced engineered bamboo ceiling has been a big challenge. The conventional chain-pulley system adopted initially was very time consuming. “We overcame the challenge by an innovative erection scheme involving a 25 T capacity crane with an additional jib,” recalls Maheswarappa, with a sense of satisfaction. Another innovation was to replace the combination of blockwork cladded with wire cut brick cladding in the building façade by brick-embedded precast panels.
“All our MEP & Airport systems are equipped with seismic resistant supports, that have all been commissioned on time,” remarks Head – MEP, Anne Sriram Kumar. The systems comprise HVAC (with a unique feature of Photo-Catalytic and Gas-phased filtration system), Fire Fighting system, Electrical, PHE, VHT (Lifts, Escalators & Travelators), ICT systems (Automated Flight Announcement including regional language announcement) systems integrated with Public Address System, Networking – active & passive with software designed access (SDA), 5G-compatible Distributed Antenna Systems, Trunk Mobile Radio Systems, ELV Systems, and Airport Systems like Baggage Handling System with unique tilt-tray sorters, Self-Baggage Drops, Passenger Boarding Bridges, Security Screening systems – all with end-to-end integrated testing and commissioning.
“There are several firsts,” remarks Anne like conducting an Integrated Test and having simulation labs at site for testing, simulating the IT systems, BHS HLC and LLC (high- and low level controls), combined wash & dry faucets in rest rooms with ADA compliance, LOD 400 (clash free shop drawings developed in BIM 360 Cloud) & Cobie (asset management system integrated with BIM platform). “We conducted Virtual FATs (factory acceptance tests) along with the customer for both imported and indigenous equipment and our MEP systems have been installed with complete mechanization (duct lifters, pipe lifters, etc.) with prefabrications to expedite process and progress,” he says, proud of his
team’s efforts.
“We conducted Virtual FATs (factory acceptance tests) along with the customer for both imported and indigenous equipment and our MEP systems have been installed with complete mechanization (duct lifters, pipe lifters, etc.) with prefabrications to expedite process and progress.”
Anne Sriram Kumar
Head – MEP
Planning Head, Santanu Guha mentions, “Procuring the right material to meet the architectural intent, many of which are first-of-their-kind was tough as was procuring about 16 lakh architectural bricks for the internal brick cladding as well as for the external brick façade as the readily available wire cut bricks in the market were neither meeting the client’s aesthetic expectations nor that of our EDRC architects. We used modular brick embedded precast panels ‐ a first of its kind in India, in the exterior facade for faster execution and optimizing manpower,” adds Santanu, sharing the team’s insightful solution.
“We used modular brick embedded precast
panels ‐ a first of its kind in India, in the exterior facade for faster execution and optimizing manpower. ”
Santanu Guha
Planning Head
“In the initial phase of the project, we completed all the RCC works for the terminal as per the project milestones,” shares S Kaliyan ‐ Head Construction (Terminal), with a sense of purpose. Post COVID, the team faced the challenge of mobilizing workmen and vendors to execute the finishing works for which they rigorously followed up and
re‐mobilized the entire workforce. “We realigned our strategy and prepared a detailed plan for 750+ Back of House Rooms which were required for the operations team. In addition, we created a separate team to focus on the passenger movement areas” informs Kaliyan. “Detailed interface plan with all trades were prepared and works were monitored daily to complete all the rooms and passenger movement areas.”
“We realigned our strategy and prepared a detailed plan for 750+ Back of House Rooms which were required for the operations team. In addition, we created a separate team to focus on the passenger movement areas. Detailed interface plan with all trades were prepared and works were monitored daily to complete all the rooms and passenger movement areas.”
S. Kaliyan
Head Construction (Terminal)
The elevated corridor with the Departure Forecourt and the road network, were logistically constrained in all sides with the MMTH, metro tunnel, lagoon, air-side boundary, and the CUP building. “The elevated corridor consists of Void Form Slabs, PT Slabs, a signature bridge (connecting the existing Terminal 1 to the main exit road),” informs Pranab Krishna De ‐ Head Construction (Elevated Corridor, Forecourt & At-Grade Roadworks). The bridge bearings of this elevated network (of varying load bearing capacity), had to be tested 100% as a stringent quality assurance measure by EDRC as against one of each type as per codal provision prior to installation. “With very few test facilities available in the country to test such higher capacity bearings, we proactively engaged with stakeholders, identified the facility, and ensured that the bearing testing was not an impediment to site progress and completed the bridge as per the project timelines.” Pranab’s triumphant expression says it all. “The signature bridge was the project’s first major milestone (related to operation readiness) to be completed, that was inaugurated on April 25th, 2022, in the presence of our senior management and BIAL senior management,” he adds proudly.
“With very few test facilities available in the country to test such higher capacity bearings, we proactively engaged with stakeholders, identified the facility, and ensured that the bearing testing was not an impediment to site progress and completed the bridge as per the project timelines.”
Pranab Krishna De
Head Construction
(Elevated Corridor, Forecourt & At-Grade Roadworks)
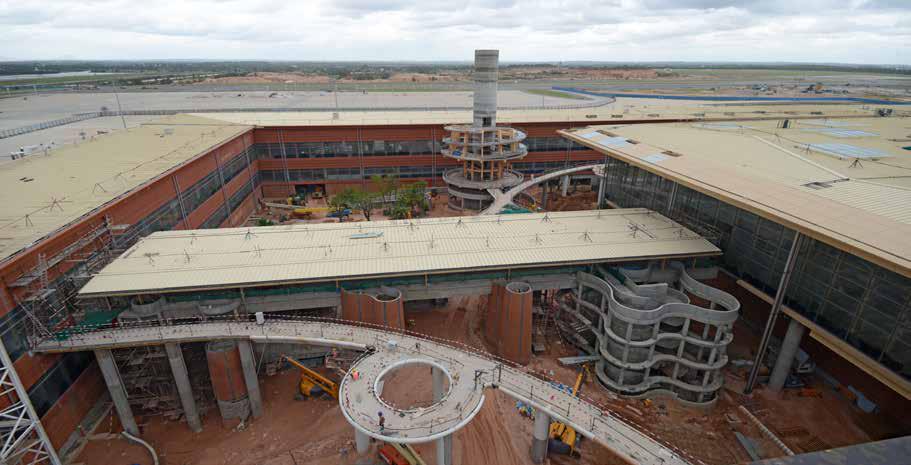
“Executing about 1.35 lakh sqm of granite flooring and cladding selected from various quarries from across India was a huge task,” remarks Anil Dureja, Head ‐ Special Finishes. “Right from selecting the stone blocks in the quarry, processing the stone slabs, till delivery at site was monitored by our people placed at every location to track the supply chain, which is key to delivering such massive expanse of natural stone flooring and cladding.”
“Right from selecting the stone blocks in the quarry, processing the stone slabs, till delivery at site was monitored by our people placed at every location to track the supply chain, which is key to delivering such massive expanse of natural stone flooring and cladding.”
Anil Dureja
Head – Special Finishes
“While COVID 19 certainly caused enormous disruptions to progress, we from the Admin team, have done all that it takes to ensure that the impact was lessened,” recalls N. Sridhar, Head ‐ Finance, Accounts & Administration. “Be it liaising with the Railway Ministry to allocate dedicated trains for workmen to travel to Bengaluru, obtaining special approvals from the Health Minister of Karnataka to reduce the quarantine period for workmen who tested negative in Rapid Antigen Tests, and more.”
“While COVID 19 certainly caused enormous disruptions to progress, we from the Admin team, have done all that it takes to ensure that the impact was lessened.”
N. Sridhar
Head – Finance, Accounts & Administration
Safety, the No. 1 priority
“We are leaving no stone unturned when it comes to safety, committed to achieving and sustaining zero accident performance through continuous improvement,” affirms R. V. Sudhakar, Head- EHS. ‘Visual Impact Training’ is helping engineers and workmen understand real life safety scenarios, while safe material is being used instead of mastic asphalt which is hazardous to workmen.
All lifts including the critical ones, using 60 T crane over the RCC slab at 12 m levels, were carried out in consultation with the CMPC Department. MEWP – mobile elevated working platforms – have been used extensively instead of scaffoldings, another unique safety feature while 110v hand-held power tools make operations safer for workmen. Roof works, a critical activity was completed efficiently and safely.
“We are leaving no stone unturned when it comes to safety, committed to achieving and sustaining zero accident performance through continuous improvement.”
R. V. Sudhakar
Head- EHS
No compromise on Quality
The Terminal 2 is spread over about 20 acres of footprint area with a basement and 4 upper levels which will typically take a person about 3 days to visit every nook and corner of the terminal in detail. For former Quality Head,
V. Yegappan, who retired recently, the project was his best shot in terms of quality adherence. Not only did the project win the internal rolling B&F Quality Trophy in 2019-20 but has also consistently won the client’s appreciation, which was no mean achievement, he grins. “We achieved many exciting milestones simply because we didn’t quit when faced with challenges and worked together as a team to give the best output.”
“We achieved many exciting milestones simply because we didn’t quit when faced with challenges and worked together as a team to give the best output.”
V Yegappan
Former Head – Quality
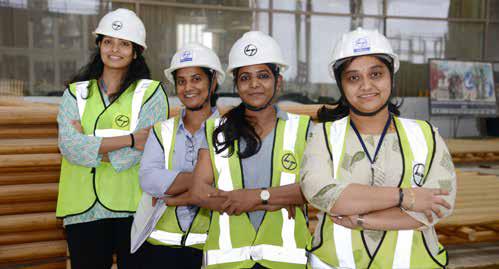
The 4 lakh cum concrete required was entirely produced in house, managed and supplied by the project’s Quality & P&M teams. About 1.5 lakh sqm of screed floor was executed meeting the stringent requirements from the client for pull out tests on screed, soundness testing for the screed by a methodology as per British Standard with the BRE test procedure. A third-party inspector was appointed to inspect the work along with the in-house quality team as an additional quality assurance to the client. This first of its kind activity of pull-out and BRE tests on screed were completed much to the client’s delight.
Around 13,000 MT of structural steel having AESS (Architecturally Exposed Structural Steel) was fabricated externally and brought to site with two dedicated QA/ QC Engineers deployed at factory for strict inspection & adherence.
“Another big challenge was casting the circular columns of 1.2 & 1.8 m diameter of 12 m height in a single pour without intermediate lifts,” shares PL Alagappan – Head-Formwork, with the hint of a frown. “By devising a proper methodology and through our dedicated team, we cast 400 plus columns in a single lift that saved us time and cost. Generally, we construct such long columns in multiple lifts.”
“By devising a proper methodology and through our dedicated team, we cast 400 plus columns in a single lift that saved us time and cost. Generally, we construct such long columns in multiple lifts. ”
PL Alagappan
Head-Formwork
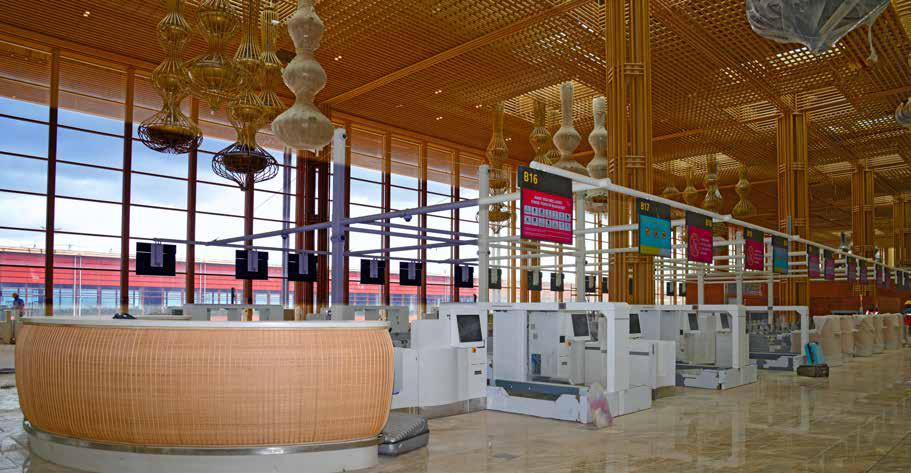
Digital Transformation through BIM, COBie
“Being the country’s first project to integrate a full BIM lifecycle for the entire project cycle meant that we had to hand hold the teams through the process as our vendors were used to 2D,” shares Narin Gobindranath, Design Head.
“Being the country’s first project to integrate a full BIM lifecycle for the entire project cycle meant that we had to hand hold the teams through the process as our vendors were used to 2D. The BIM model is the complete source of information, and we are proud to be early adopters.”
Narin Gobindranath
Design Head
Today the entire team can access all information and take informed decisions. “We are leveraging the full extent of digital design under the Autodesk suite from design to onsite construction, asset and facilities management and are extensively using COBie (Construction Operation and Building information exchange) which is a framework for collecting and storing information within the elements during the design and construction stages to utilize during operations and maintenance. The BIM model is the complete source of information, and we are proud to be early adopters,” enthuses Narin.
The BIAL project site looks like a giant pitstop with every person playing a key role. Senior Principal Architect, Nandedkar Suchita walks energetically and points at the granite flooring and says, “All the dry lay inspections of granites have been carried out by me personally day in and day out to meticulously ensure that the extensive granite flooring at various levels of the terminal are of the best quality and aesthetics.”
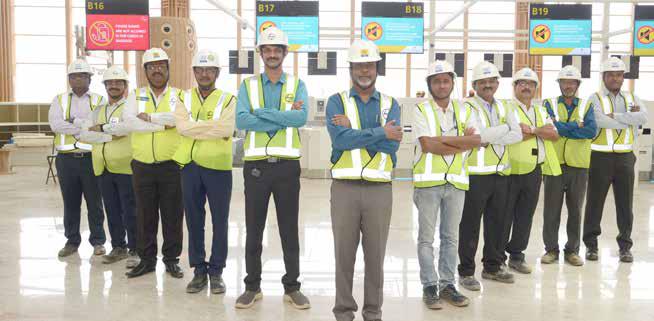
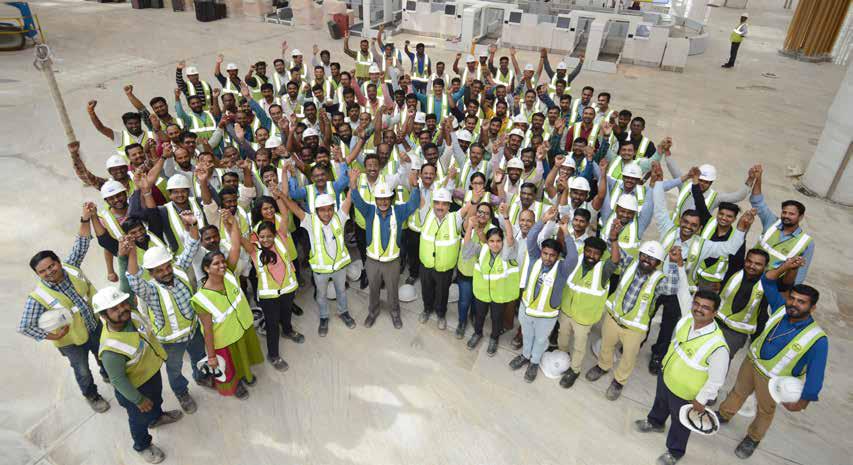
Meanwhile, at another section, K. P. Maheswarappa is having a sunset huddle with the team. He easily walks about 20,000 steps everyday around the site, and you can sense the fire in his belly as they plan their day’s work. “Hats off to our execution team and the various service departments for their tremendous dedication, with most of them voluntarily coming on Sundays and other holidays in rotation to ensure that the project is completed on time which has earned the appreciation of the client,” remarks Maheswarappa, with a sense of gratitude.
“My team has done an excellent job against all odds,” says Shivaraj proudly. And as they march closer to the finish line together, of late he has been asking them only one thing, “How is the josh?” “High Sir”, they roar in unison.
A MATTER OF PRESTIGE!
Spread over 32 acres with 5 Buildings & 15 Towers, 3571 flats with each tower having 2 to 3 Basements + Ground Floor +30 Floors, the Prestige Jindal City residential project paints a majestic picture in the dense residential area of Bengaluru. For Project Director, K Ravichandran and team, it was time to celebrate, entering the last leg of completing a project which was initially marred by several disruptions. As the team cheered in tailormade sherwanis made for the occasion, Ravichandran remarks, “the timely completion and commendable progress of the project are only because the team stood by each other undeterred by challenges. An indication of the quality of our work, is that we have bagged more high value projects from Prestige.”
“The timely completion and commendable progress of the project are only because the team stood by each other undeterred by challenges. An indication of the quality of our work, is that we have bagged more high value projects from Prestige.”
K Ravichandran
Project Director
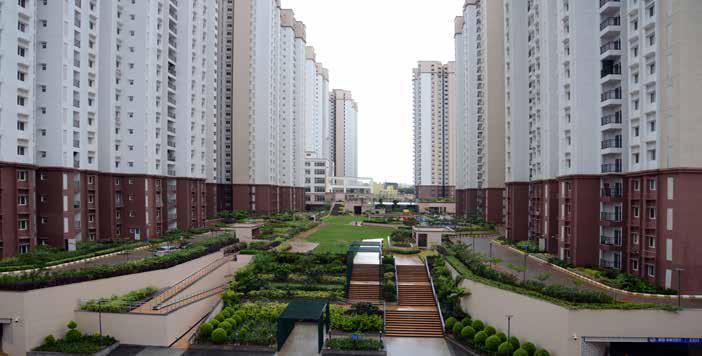
Every challenge is an opportunity to excel
Located in a residential area, the team only had a restricted 7 am ‐ 7 pm window for construction activities during which they had to complete 500 ‐ 750 cum of concrete in 12 hours and maintain equipment at the highest levels of efficiency and availability, with zero breakdowns. Elaborating, Head Finishing- A Subramanian shares, “Our challenges were not to create any noise after 7 pm and take extreme care to minimize dust by using vacuum grinding machines, and sprinkling water around the clock. I am equally thrilled that we have been able to maintain the highest levels of quality and consistency even while working with multiple agencies and workmen.”
“I am equally thrilled that we have been able to maintain the highest levels of quality and consistency even while working with multiple agencies and workmen.”
A Subramanian
Head Finishing
“During the second wave of COVID, the team faced challenges for the transit of workmen from their habitat to site due to the stringent guidelines announced by the State Governments,” informs Vegu Sreenivas, Head Accounts, “but we managed with impeccable co-ordination and strictly following all SOPs.”
“During the second wave of COVID, the team faced challenges for the transit of workmen from their habitat to site due to the stringent guidelines announce by the State Governments but we managed with impeccable coordination and strictly following all the SOPs.”
Vegu Sreenivas
Head – Accounts
Triumphing the COVID phase
COVID-19 and the subsequent lockdown saw the workmen of the site stuck in their colony at a different location. The local villagers demanded the workmen be vacated and almost took siege of the colony. It took constant reassurance and negotiation from the project team to appease the villagers and convince them that there were no infected workmen in the colony. In addition, they reached out to them with initiatives such as arranging medical camps and
conducting tests.
Vadivelu Rajendran, Head EHS shares “Post lockdown, through our excellent planning and coordination, we have successfully mobilized the required workforce to achieve and, in some cases, exceed our targets with Safety
and Quality.”
Some of the team’s prime challenges were to sustain the increasing prices of transportation despite the spike in fuel prices, steel prices and all consumables, retain and timely re-mobilize vendors and sub-contractors for all the activities.
“Post lockdown, through our excellent planning and coordination, we have successfully mobilized the required workforce to achieve and, in some cases, exceed our targets with Safety and Quality.”
Vadivelu Rajendran
Head EHS
“With stringent planning at task level, active resource mobilization, workmen and P&M allocation, and strict monitoring of site progress, we achieved several milestones, well ahead of time,” happily grins
Head ‐ Planning, Ms. V Ramani.
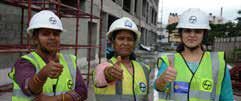
“With stringent planning at task level, active resource mobilization, workmen and P&M allocation, and strict monitoring of site progress, we achieved several milestones, well ahead of time.”
V Ramani
Head – Planning
Achieving milestones galore
“Completing 63, 68, 546 lakh sq ft of built up area of a residential development of this scale in the span of 40 months by working only 12 hours a day is not an easy task,” shares Ravichandran, who is proud of his team’s several timely milestones: 3,32,401 cum concrete, 5,71,871 sqm of tiling works, 23,900 MT of TMT works, 650 MT of structural steel works. The team achieved 250 flats of tiling, 250 flats of gypsum and 200 flats of waterproofing in a single month which is a new benchmark for residential projects in Bengaluru.
Another huge challenge for M. Sivanthilingam, Head Structure, “was to complete the 19 Lakh sq ft of non-tower area structure with almost 9 ancillary building structures of STP, UG Sump, DG rooms at the 3rd & 2nd basement levels.” he huffs with relief. “The IPS flooring for the 3 basements was a tall ask with the logistics of pump placing, transit miller movement with all finishing works and ground works progressing in tandem. But here we are today, all set to handover the project,” he says with a quick smile.
“The IPS flooring for the 3 basements was a tall ask with the logistics of pump placing, transit miller movement with all finishing works and ground works progressing in tandem. But here we are today, all set to handover the project.”
M. Sivanthilingam
Head Structure
“I am proud that the team effectively implemented QMS systems and digital checklists at site. We have received several accolades from the client and recently, we were awarded the best high-rise structure from the American Concrete Institute which was only possible because the team had a common vision and worked in tandem with each other,” states Manikandan P – Head Quality.
“We have received several accolades from the client and recently, we were awarded the best high-rise structure from the American Concrete Institute which was only possible because the team had a common vision and worked in tandem with each other.”
Manikandan P
Head Quality
Ensuring on-time delivery through BIM
Building Information Modelling (BIM) has been extensively used in the project especially for the school building. One of the most valuable benefits of BIM is its ability to improve the coordination between multiple design disciplines, thus reducing errors and improving outcomes. Using BIM, the team could effectively visualize the final design model, share information, quantify key building elements, plan monthly activities, monitor schedules, progress & cost for on-time project delivery.
Ravichandran or “Captain” as the team affectionately calls him looks proudly as they rally around each other in easy camaraderie, knowing that in a few weeks, they will congratulate each other on their latest triumph and move on to other projects to do what they do best – changing cityscapes together!

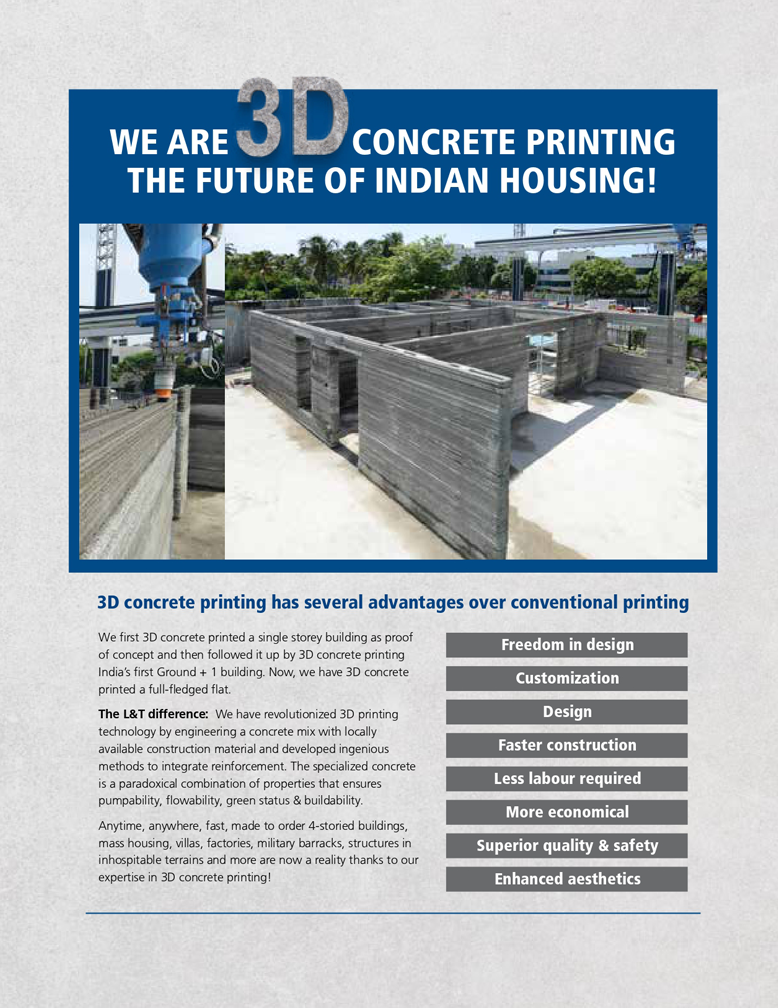
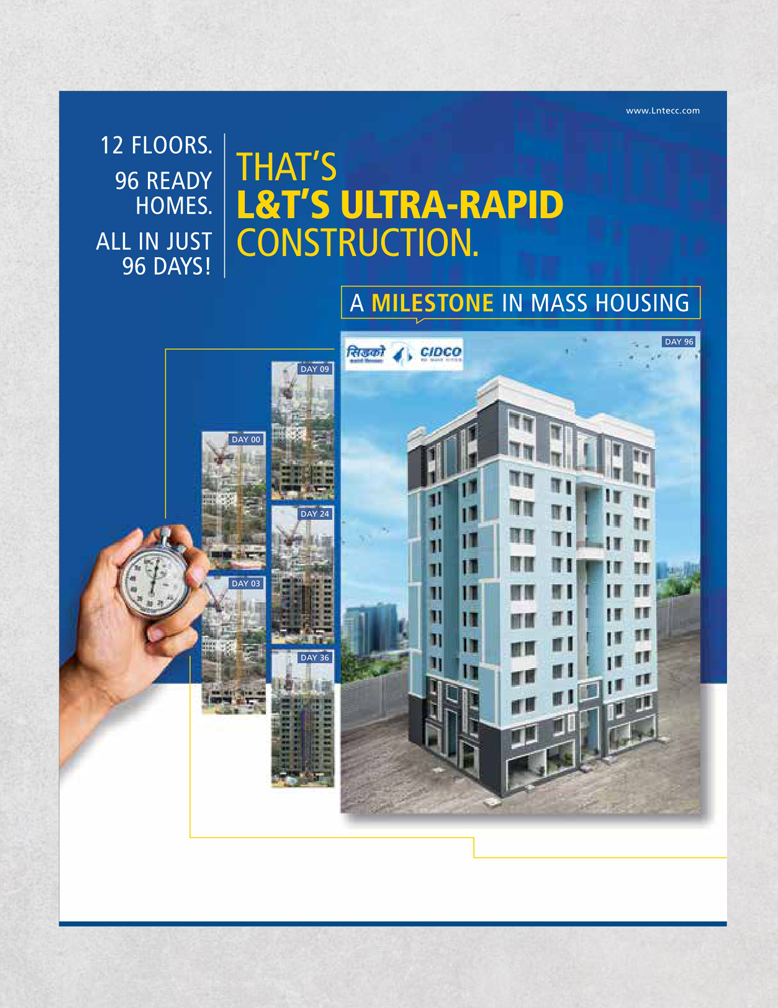