TWO PT&D PROJECTS STRIVE FOR EFFICIENT DELIVERY
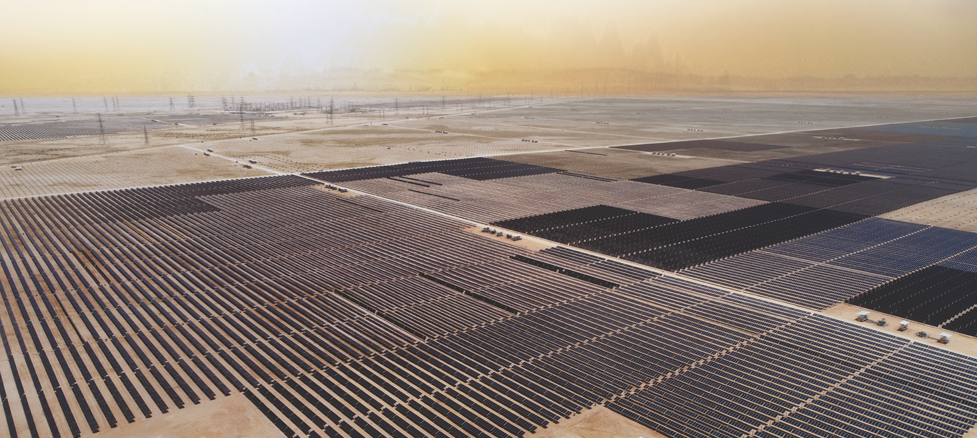
SUDAIR SOLAR PV IPP
Steel equivalent to construct 9 Eiffel Towers
An area that can span 2,735 football grounds
Cables that can cover two-thirds of the Earth’s circumference
These fascinating facts constitute the 1.6 GWac Single-Axis Tracker Plant at Sudair, the first GW-scale solar PV project in Saudi Arabia and the first under the Public Investment Fund’s (PIF’s) renewable energy programme. Located
165 km from Riyadh, the plant has solar PV technology using bi-facial panels with trackers and a state-of-the-art automated robotic cleaning solution.
A project of ‘giga’ scale
The scope of work for the project includes three components: three groups of Solar PV of 1,612 MWac
(806 MWac + 403 MWac + 403 MWac), two 33/380 kV Pooling Substations (PSSs), and a 380 kV Overhead Tower Line (OHTL) between the PSS and Electrical Special Facility (ESF) Gantry. “This is the largest single-contracted solar PV plant in the world and the largest of its kind in Saudi Arabia, for which the long-term Power Purchase Agreement has been signed for 25 years,” observes Bharathi Kumar, Task Force Leader. “A project of significant magnitude, with the second-lowest cost globally for solar PV electricity production at USD 1.239 cents/kWh, its mega impact will be translated to energize 185,000 homes and offset nearly 3 million tons of emissions.”
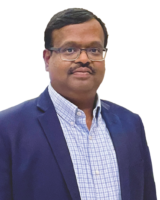
Bharathi Kumar
Task Force Leader
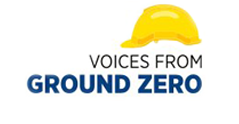

“Our energizing 450 MWp of solar capacity in a single month is an unprecedented achievement and sets a new industry standard, showcasing the potential for rapid large-scale renewable energy deployment with all elements of a project aligned seamlessly.”
A few numbers to put the scale of the project into perspective:
- 3.2 million bifacial PV modules
- 33,014 solar PV trackers
- 5,048 automated robot cleaning systems
- 516 solar inverters of 3.125 MVA, and much more
Despite the size and complexity of the project, Project Control Manager, Vikas Shetty, is a happy man. “As per our progress plan, we were to have completed 87.99% at this point in time. However,” he pauses suspensefully, “we have actually achieved 90.52% progress thanks to coordinated teamwork!” he adds with a flourish.
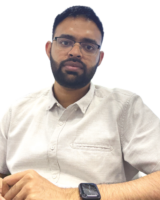
Vikas Shetty
Project Control Manager
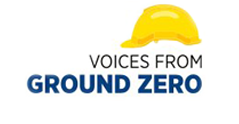

“As per our progress plan, we were to have completed 87.99% at this point in time. However, we have actually achieved 90.52% progress thanks to coordinated teamwork!”
Prudent strategies keep the ball rolling
Given the undulated terrain at the site, installing 33,014 trackers was a huge challenge. “We took some calculated risks as per the terrain, which worked in our favour,” remarks Pradeep Raj Kumar, Assistant Manager (Civil), calling it a defining moment in the project. “Using a laser level machine for the ramming and tracker activities, we have achieved a 10% increase in tracker installation productivity, aided by on-site training and continuous guidance with proactive
follow-ups.”
As per contract, the team were to excavate 20,000 cum hard rock in the prescribed timeline. However, during execution, the team encountered 60,000 cum of it on braking the surface to accelerate the durability tracks that were critical to the project. Additional resources and crashing subsequent special surfaces saved the day. Anticipating the risk of parabola asphalt paving during the tendering stage, the contract team collaborated with the site execution team to redesign the mini parabola with a 33” slope in the performance track, to accommodate the parabola portion.
The team learned, unlearned, and developed inhouse technologies for the specialized flexible steel drum roller, pneumatic tyre roller and curved parabola paver which are digitally controlled machinery to ensure compaction of asphalt in the parabola of 0* to 44* angles that varies every meter in the transition portion. Effective use of frontier technologies helped to ensure workmen safety, improve productivity, optimally organize activities and avoid manual errors and reworks in making the parabola profile.
“We introduced advance technology in the form of a non-nuclear asphalt density gauge that tests the density of asphalt in real time saving hugely on time and cost,” shares Manager (QA/QC), M James Iruthayaraja.
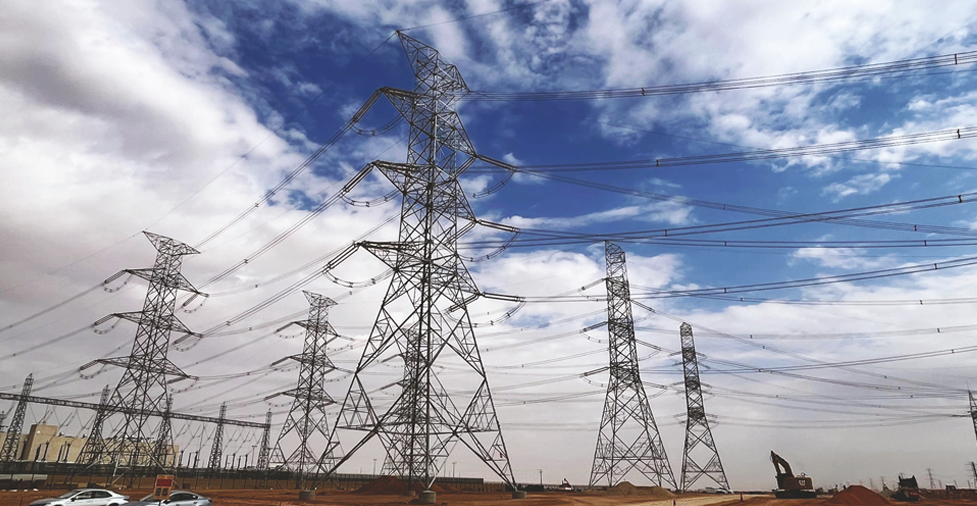
Cutting and grading were challenging too, owing to the mismatch in the topography levels and the ground. The vertical posts were installed as per the actual land profile thanks to the new ramming methodology that has reduced rework and improved progress. “For laying cables, instead of single-run MV cable drum pulled through a winch machine, we implemented a two-run cable pulled simultaneously by a V-shape cable roller,” says Adil Khan, Assistant Manager (ELEC), which has increased productivity, while the modified LV/MV cable layouts have optimized cost.
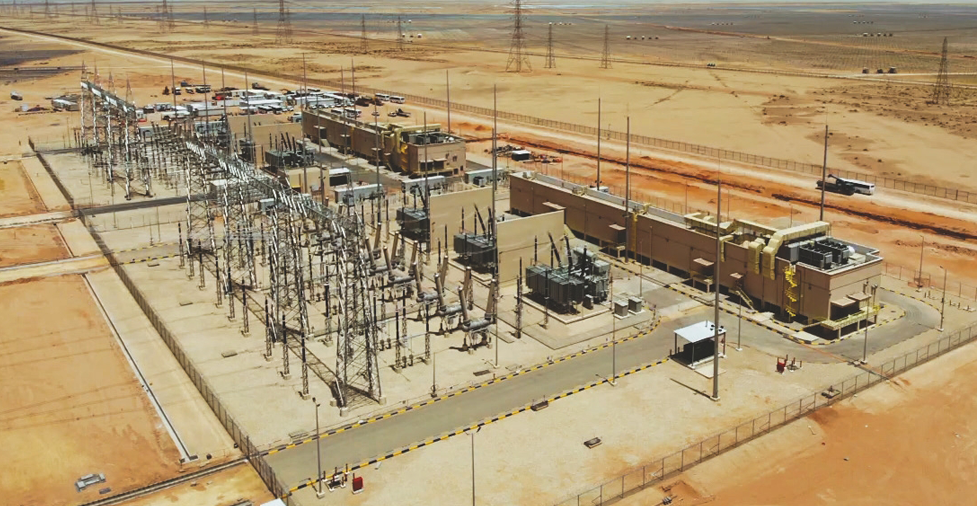
“By deploying a modified Bobcat to move the posts and a drone for topography surveys, we have saved time and improved productivity,” informs Vikas, adding that they use a laser machine for tracker alignment instead of the conventional line dori method, and a specialized impact wrench for tightening bolts and nuts to ensure secure fastening within the tracker structure. The team has realized cost reductions to the tune of USD 150,000+ thanks to these initiatives.
Bharathi Kumar and team have reasons to cheer, achieving 19.5 MWp of module installation in a single day, 450 MWp energized in one month, 1,700 MW of mechanical completion other than modules, and safely unloading 90 containers of modules in a day. “Our energizing 450 MWp of solar capacity in a single month is an unprecedented achievement and sets a new industry standard, showcasing the potential for rapid large-scale renewable energy deployment with all elements of a project aligned seamlessly,” Bharathi exclaims. Digital initiatives have further enhanced progress: the QIR app for quality, SHEILD for safety, SharePoint for database management, timelapse cameras and drone surveys for geospatial, RFID cards and the WISA app for administration, Align for project monitoring, and BIM for engineering.
Resource mobilization has been another tough nut to crack for the team. The Russian aggression in Ukraine dried up supplies from Europe, while the lingering impact of the pandemic disrupted material delivery from China. Appreciating the criticality of the situation, the team swung into action, organizing weekly meetings with suppliers and micro-monitoring raw material procurement right from the manufacture of equipment to delivery at site. “In case the supplier faced any raw material delivery issues, we immediately changed tracks with the client’s approval for an alternative make to ensure that material delivery was stream-lined,” shares K Dhandabani, Construction Manager (ELEC), reflecting their urgency.
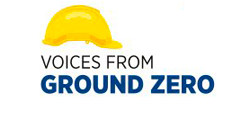

“In case the supplier faced any raw material delivery issues, we immediately changed tracks with the client’s approval for an alternative make to ensure that material delivery was stream-lined.”
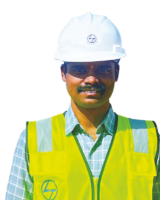
K Dhandabani
Construction Manager (ELEC)
Safety and sustainability at Sudair
Achieving 9+ million safe manhours as of 9th September 2023 with zero LTIs and fatalities is a wonderful statement on their EHS efforts. “We have won the RoSPA Gold and the Annual EHS Award for HSE performance, both in 2022–23,” Pradeep Kumar, EHS In-charge, proclaims with a proud thumbs-up. “We have clocked more than 235,000 training manhours and have successfully completed all HSSE audits without any NCRs or major findings.”
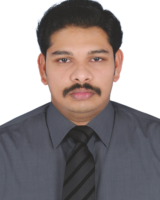
Pradeep Kumar
EHS In-charge
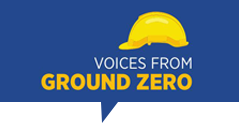

“We have won the RoSPA Gold and the Annual EHS Award for HSE performance, both in 2022–23. We have clocked more than 235,000 training manhours and have successfully completed all HSSE audits without any NCRs or major findings.”
Being a renewable energy project, sustainability is at the core of the Sudair Project team’s strategy. The robotic cleaning system to clean the solar panels will save water and reduce human intervention, and the entire lighting at the PV plant will run on solar power. All the wood used as packing material is being reused at site for temporary facilities and barricading. All submissions are done through Thinkproject, avoiding hardcopies. “We ensure that all reptiles found during construction are safely relocated to their natural habitat,” informs Pradeep. “We only use municipality-approved contractors for waste disposal at approved locations and diesel spill kits to avoid contaminating the earth with designated, separate concrete washout areas. Disposable plastic bottles are banned at site; only reusable ones are allowed.” The project is a frequent top contributor on World Environment Day (which falls on 5 June) and has been recognized twice for its WED initiatives in 2022 and 2023.
One of the world’s largest solar PV plants demands innovation and efficiency, and Bharathi and team with their
cutting-edge solutions for enhanced productivity have propelled the project forward, promising a cleaner, greener, and more sustainable future.
THE IRCON T74R & T77 PACKAGE
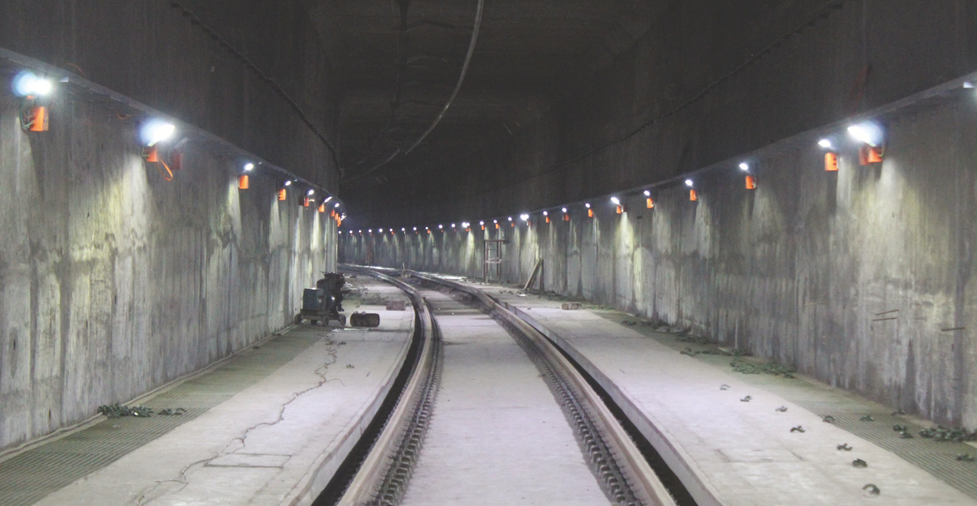
“Our IRCON project is of national importance that will impact the whole of the Kashmir Valley,” declares Manoj Kumar, Project Manager, describing the T74R & T77 Package that is an integral part of the larger Udhampur–Srinagar–Baramulla Rail Link (USBRL) project aiming to connect the Kashmir Valley with the rest of India. “This rail link will give the people of the region access to better education, healthcare facilities, and business opportunities, which will in time boost economy, tourism, and cultural exchange,” he adds.
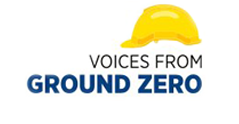

“Our value engineering does not compromise on the design requirement but adheres to all contractual requirements, all the while maintaining the L&T standard of quality.”

Manoj Kumar
Project Manager
Wisely managing resources in tough, trying conditions & terrains
The harsh and unforgiving terrain and conditions are Manoj Kumar and his team’s biggest impediments, operating in hilly terrains with extreme weather conditions where the temperature plummets to −7°C with snow falls during winter. “The roads are extremely dangerous and often closed due to landslides,” Manoj shares grimly, “so, resource mobilization is tough and, to add to these, we face local disturbances, security hassles, and local ROW issues.”
The team under his leadership is standing firm, committed to deliver.
The onus on Planning Manager Prince Mishra is to arrange for materials and drawing approvals from the European consultant appointed by IRCON exactly as per the specifications mentioned in the contract documents, for which they have had to identify new vendors. Considering the criticality of efficient resource mobilization and allocation, the team focuses on the most important tasks, utilizing resources for those ear-marked activities by identifying suitable staff and subcontractors for a particular work based on their ability and past work experience.

Prince Mishra
Planning Manager
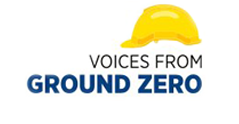

“We decided to train local workmen and developed local vendors to fulfil our requirements. Developing local vendors to take up cost-effective civil works like doors, windows, rolling shutters, and false ceiling work has given us better control over execution.”
“After our initial effort to source workmen from other parts of the country failed, we decided to train local workmen and developed local vendors to fulfil our requirements,” remarks Prince. “Developing local vendors to take up cost-effective civil works like doors, windows, rolling shutters, and false ceiling work has given us better control over execution.”
A refined process for smooth execution
Manoj cannot afford to let his guard slip, constantly monitoring processes and optimizing project design to reduce costs and increase the scope of items with higher gross margins. “Our value engineering does not compromise on the design requirement but adheres to all contractual requirements, all the while maintaining the L&T standard of quality,” he avers.
Fully aware that speed of execution translates to time saving and better margins, the team has introduced smart methods like using a Winch Machine to lay the 33 kV, 11 kV, and LT cables, which has made the cable laying inside the tunnel 4–5 times quicker, using power tools during erection to reduce time, and prefabricating roof truss structures that saved time to install roof trusses. By focusing on completing the civil work and equipment foundation on priority, they have succeeded in installing the electrical equipment directly, thus reducing double handling of equipment.
Shifting heavy machinery and material over the tough terrains has been another uphill task, specifically the 10–12 ton heavy 33 kV cable that had to be laid inside the tunnel. “As our access was cut off after the ballast-less track was laid by the civil agency, we fabricated a dip lorry with a capacity of 15 tons with the available resources at site to shift and lay the cable drums easily,” shares Vikas Dhamanna, Construction Manager (ELEC), adding that their ‘innovation’ also facilitated shifting the 11 kV cable drums, LT cable drums, and LT panels inside the tunnel.
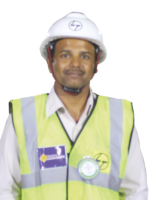
Vikas Dhamanna
Construction Manager (ELEC)
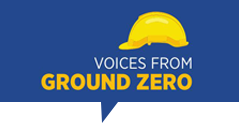

“As our access was cut off after the ballast-less track was laid by the civil agency, we fabricated a dip lorry with a capacity of 15 tons with the available resources at site to shift and lay the cable drums easily.”
“We successfully shifted and installed a 1,500 kVA DG set weighing around 24 tons, four 3.15 MVA power transformers weighing around 8 tons each, four 800 kVA transformers, and 33 kV & 11 kV GIS panels, despite severe space constraints, optimally utilizing resources, manpower, and time,” adds Vivik Kumar, Construction Manager (ELEC).
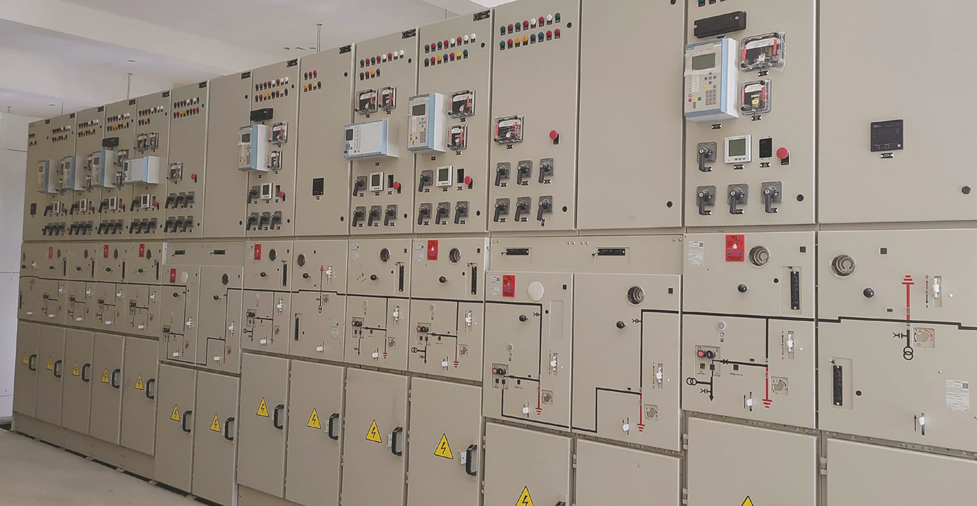
The TMT reinforcement and structural steel fabrication was carried out by a separate team parallelly at a centralized store to complete the cut-and-bend process in advance and reduce wastage in the process. Tower cranes mobilized for activities above the first floor saved lead time to shift material, which improved productivity. Further, to combat the unpredictability of the weather to an extent, the team plans their work according to reliable 10-day forecasts, while work proceeds uninterrupted inside the tunnel even on rainy days.
Key focus on EHS & Quality
Maintaining high EHS standards is imperative for progress, and apart from vigorously monitoring near-miss incidents and lead indicators, the team ensures proactive risk identification, assessment, mitigation, and monitoring. “Tunnel E&M works are first of their kind for PT&D,” informs Avinash Kumar, EHS Officer. “We have identified and analysed potential risks, meticulously prepared and are implementing EHS SOPs for each activity as warranted by the location and project requirements.” Special precautions are being taken to ensure safety in landslide-prone areas, securing offices, staff, and workmen establishments.
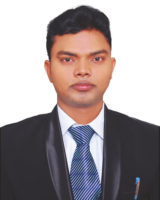
Avinash Kumar
EHS Officer
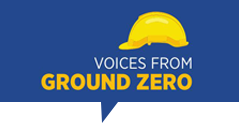

“Tunnel E&M works are first of their kind for PT&D. We have identified and analysed potential risks, meticulously prepared and are implementing EHS SOPs for each activity as warranted by the location and project requirements.”
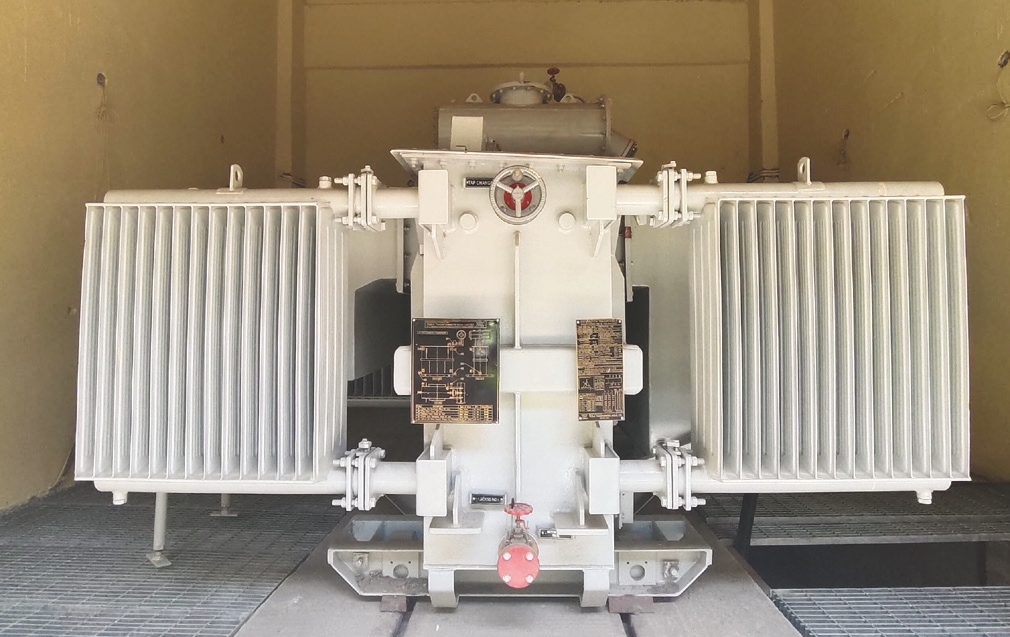
“Our team systematically monitors and evaluates progress and output by identifying and addressing any deviation from the desired quality and client-approved method statements, performs thorough root-cause analysis for corrective and preventive actions to prevent recurring issues,” asserts Manoj. “Our success is because we are all aligned and focused on the project milestones and roles,” he smiles broadly.
The project location is greener with the 1,250+ saplings the team has thus far planted, of which 1,215 are alive and thriving. These include apple, walnut, chinar, and pear, along with 1,000 local trees planted in 3 days as a part of Project GreenHands. As a community outreach, the project team contributes towards education through book donations and digital classrooms. “Apart from providing 50 sets of books through the district administration for underprivileged students to help them prepare for their UPSC examinations, we are working with two different schools to set up digital classrooms by October,” informs Prince.
Manoj and team are committed to making their project a success despite an uphill struggle, and that they are succeeding is reflected in their improved margins; here is wishing them the very best to deliver handsomely.