TWO WET IC PROJECTS REMAIN FOCUSED ON DELIVERY & PROFITABILITY
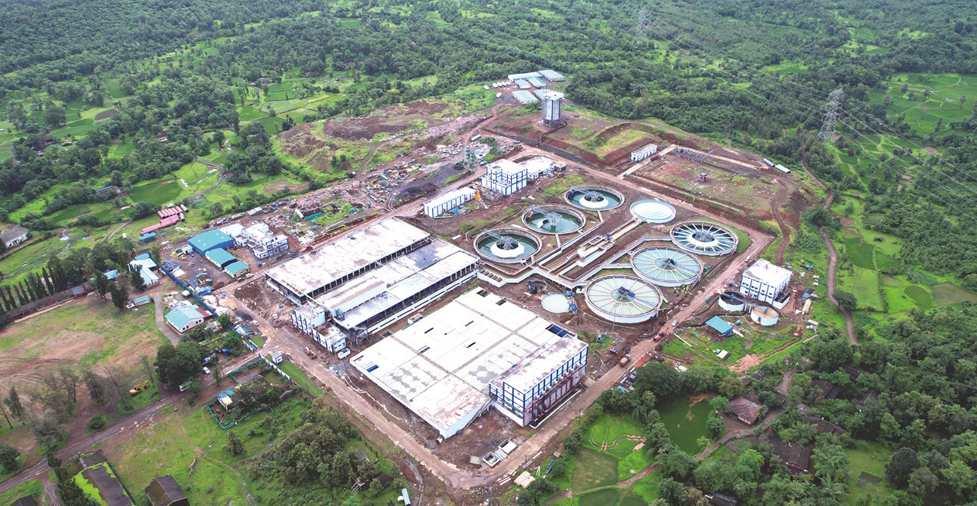
SURYA WATER SUPPLY SCHEME
The Surya Regional Water Supply Scheme involves the construction of a 707 MLD Intake Well from where the raw water is lifted at the Kawadas pickup weir (downstream of the Surya dam) and pumped through a 2.2 m dia. MS pipe for 2 kms to reach a 419 MLD Water Treatment Plant (WTP) at Surya Nagar. Post treatment, the water is pumped through another 2.2 m dia. MS pipe for 0.6 kms to reach the Break Pressure Tank (BPT) which provides the required head for transmitting water through gravity flow via another underground 2.2 m dia, 56-km-long MS pipeline and through the
1.7 km Mendhwankhind Tunnel to reach the 38 ML Master Balancing Reservoir (MBR) at Kashidkopar for further distribution to the Vasai-Virar City Municipal Corporation. Water is also diverted at the Kashidkopar location and clear water supplied through a 21 km MS pipeline (1.8 m dia) and through the 4.6 kms Tungareshwar Tunnel to reach the
45 ML MBR at Chene for further distribution to the Mira-Bhayander Municipal Corporation.
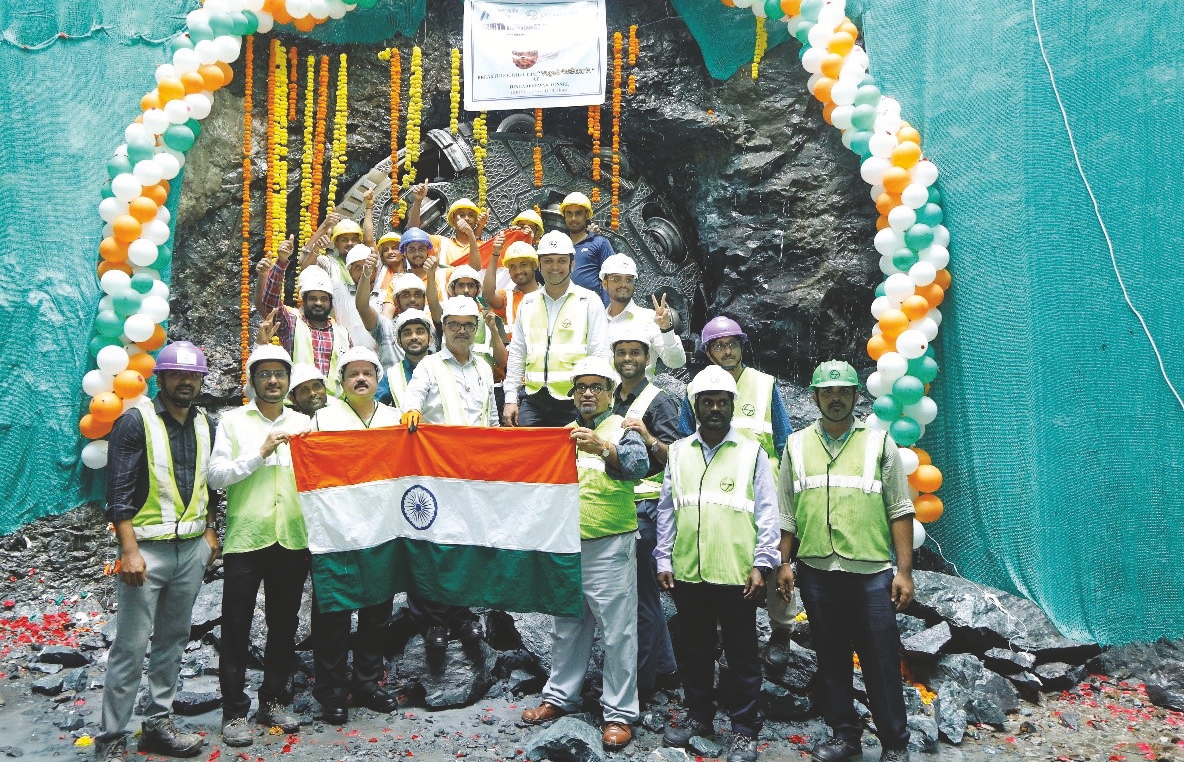
Celebrating the TBM breakthrough at the 4.6 km Tungareshwar Tunnel
Project Director, Colin Nonis’ hands are full, but he exudes an air of quiet confidence. “Phase 1 of the project has been successfully commissioned which includes the 707 MLD intake, a 419 MLD WTP, 61.3 kms of MS pipeline, 1.7 kms of the Mendhwankhind Tunnel and the 38 ML Kashidkopar MBR,” he ticks off points of progress. “With the recent TBM breakthrough of the 4.6 km Tungarehswar Tunnel, we have achieved a significant milestone of completing L&T’s longest tunnel with TBM and with the completion of 9 kms of pipeline out of 21 kms and 45% physical progress at Chene MBR, Phase 2 works are also in advanced stages.” He pauses and adds that his responsibilities additionally include dealing with and procuring clearances from a variety of authorities such as NHAI, Forest Department, CRZ, Maritime Board, State Highway, Zilla Parishad, PWD, DTEPA, High Court, and more, all of which have been secured now.
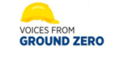

“With the recent TBM breakthrough of the 4.6 km Tungarehswar Tunnel, we have achieved a significant milestone of completing L&T’s longest tunnel with TBM and with the completion of 9 kms of pipeline out of 21 kms and 45% physical progress at Chene MBR, Phase 2 works are also in advanced stages.”
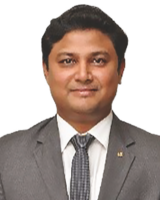
Colin Nonis
Project Director
Project commissioning has been split into two phases. Phase1 will supply 185 MLD of bulk water to the Vasai-Virar City Municipal Corporation & 17 villages en route, meeting the demands of approximately 14 lakh people. “At present the testing and cleaning of the pipeline and MBR have been completed and supply of treated water to VVCMC should commence in October 2023,” informs Colin.
A saga of permissions & opposition
The initial mobilization activities were speedily taken up after the award of the contract involving setting up office & storage yards, conducting survey & geotechnical works, designing the project components, procuring MS pipes, placing orders for tape coating material and a customized TBM along with ancillary equipment, all imported.
Just as planned manufacturing & laying of the MS pipes commenced after receiving NHAI’s permission to utilize the Right of Way on NH-48, the team’s progress was almost immediately halted on the instructions of the local authorities due to opposition from the local villagers on issues of compensation. When meetings & negotiations failed, the team was directed to procure working permissions in the forest areas from the State & Central Forest Department, another tedious process. While an expert agency was engaged to expedite Stage-I clearance that came through in October 2018, work at important locations could not commence without Stage-II clearance as the project was termed a ‘Hybrid Project’.
SOME SALIENT DELIVERABLES
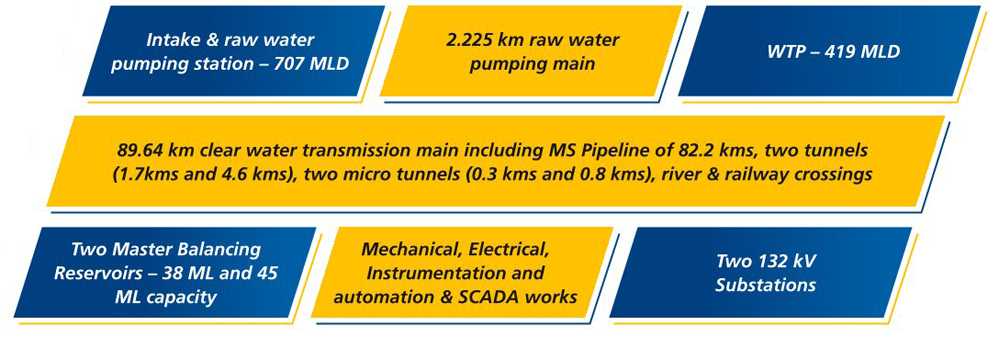
However, with Stage-I clearance, pipeline works commenced and were streamlined under police protection. Stage-II clearance was another long, drawn-out affair with delays owing to issues related to the Old Surya Dam but finally secured a year later in October 2019, thanks to the team’s determined efforts and consistent follow ups. Key structures like the WTP & 10.2 km pipeline fall in the Dahanu Taluka that required permission from the Dahanu Taluka Environment Protection Authority (DTEPA) and although the team received the requisite go ahead, it was again long delayed due to the non-appointment of the authority’s Chairman!
As the permissions were ‘extracted’, the team faced opposition from the local villagers for the construction of both the WTP and the reservoir at the Kashidkopar MBR and civil work could only commence under massive police protection. No sooner had the team got into action, they were broadsided by the pandemic that disrupted all their well-laid plans.
Facing & overcoming a plethora of technical challenges
Each of their activities were fraught with challenges. For the intake works, the team discovered that the water level in the Kawdas Weir remained constant all year round. “We did not have a dry period and constructed the coffer dam in water of 9 m depth, dewatering at 10 m depths,” says Akhilesh Singh, Construction Manager (Civil), seriously. Exposed rock was available only at 85 m levels and excavating hard rock for the intake well at 30 m depth was tough, as was excavating in the vicinity of the existing dam and pump house. The team control blasted taking all the necessary safety precautions to expedite progress, though vehicular movement, and machinery operation for various activities in slushy, wet and windy conditions was a nightmare.
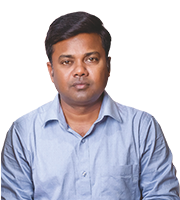
Akhilesh Singh
Construction Manager (Civil)
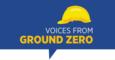

“We constructed a 55-m deep inlet shaft in extreme hard rock, a back shunt of up to 50 m and a front shunt up to 10 m both using the drill blast method and the entire tunnel in a single drive of 4.6 km at a depth of
55 m.”
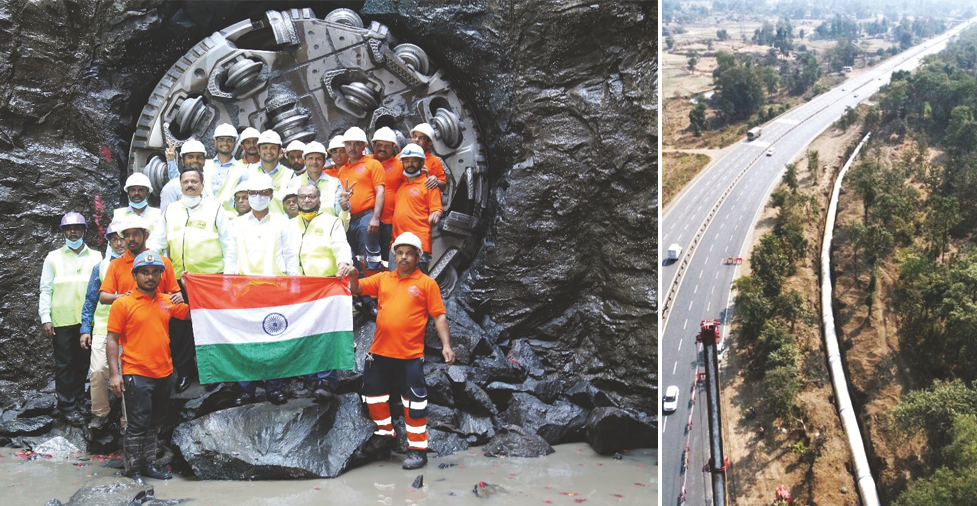
Celebrating the TBM breakthrough of the 1.7 km Mendhwankhind Tunnel
In the WTP works, concreting the BPT wall during slipform movement, BPT roof slab at 30-m height was difficult too owing to the altitude and high wind speed as was formwork and concreting the pumphouse roof slab at 10 m height on a complicated filter bed. The team successfully overcame these challenges to complete the 15.5 m tall BPT wall in just 72 hours.
More challenges awaited the team underground after they conducted extensive geotechnical investigations up to a depth of 200 m at the Tungareshwar Tunnel. “We constructed a 55-m deep inlet shaft in extreme hard rock, a back shunt of up to 50 m and a front shunt up to 10 m both using the drill blast method,” reveals Akhilesh, “and the entire tunnel in a single drive of 4.6 km at a depth of 55 m,” he adds with vigour. The water tunnel was constructed using the segmental lining method. Almost the entire pipeline terrain was challenging with hard rock encountered at 1 m below ground level. Laying the MS pipeline involved controlled blasting of extremely hard rock along an active national highway, facing collapsible soil in several areas, when constructing the coffer dam for the river crossing and managing highway & railway crossings.
Value engineering profitable progress
“By proposing a Common Finished Internal Diameter of 2.85 m for both tunnels, we utilized our resources better, saved time, increased productivity, and saved the cost of buying a new TBM and specific materials,” remarks Colin, with a satisfied look, adding, “There was a significant improvement of 32% in advance rate in the Tungareshwar drive over the Mendhwankhind drive, that was wholeheartedly appreciated by the customer.” The proposal to reduce the encasement thickness of the MS pipeline from 300 mm to 200 mm for the 11.6 km of NH encasement that was duly vetted by IIT Bombay and accepted by the Customer, resulted in nearly 30% less RCC works with other obvious benefits.
Initially, the specifications were mandated for a PCC bedding before laying the MS pipes. The team were proposed a granular graded material instead for a pipeline stretch of 80 kms as the strata was mostly weathered or hard rock that significantly increased productivity and eased execution along with cost savings. Opting for precast concrete segmental lining instead of RCC in-situ lining for both tunnels translated into significantly faster cycle times and improved the productivity of tunnel boring.
Using advanced construction methodologies to fast-track activities
“Using slipform methodology for wall casting at the intake and BPT improved productivity, saved approximately 2 months and allowed us to work through the monsoon since we completed the outer walls prior to the onset of the rains,” points out Assistant Construction Manager (MECH), Ashutosh Shukla.
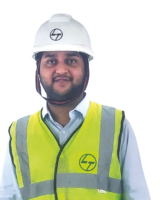
Ashutosh Shukla
Assistant Construction Manager (MECH)
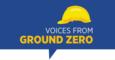

“Using slipform methodology for wall casting at the intake and BPT improved productivity, saved approximately 2 months and allowed us to work through the monsoon since we completed the outer walls prior to the onset of the rains.”
Opting for hollow core slabs instead of cast in situ for the master balancing reservoirs and clear water reservoir served the team well while using mobile formwork to construct the MBRs appreciably reduced cycle time and increased productivity. Flux core arc welding for field joints of the MS pipeline instead of the traditional method of shielded metal arc welding has shown promising results with improved product quality and approximately 50% better productivity. Another smart ploy has been to use a Mechanical Screener to sieve excavated soil below 10 mm size for bedding & backfilling the pipeline trench that improved productivity by a whopping 8 times.
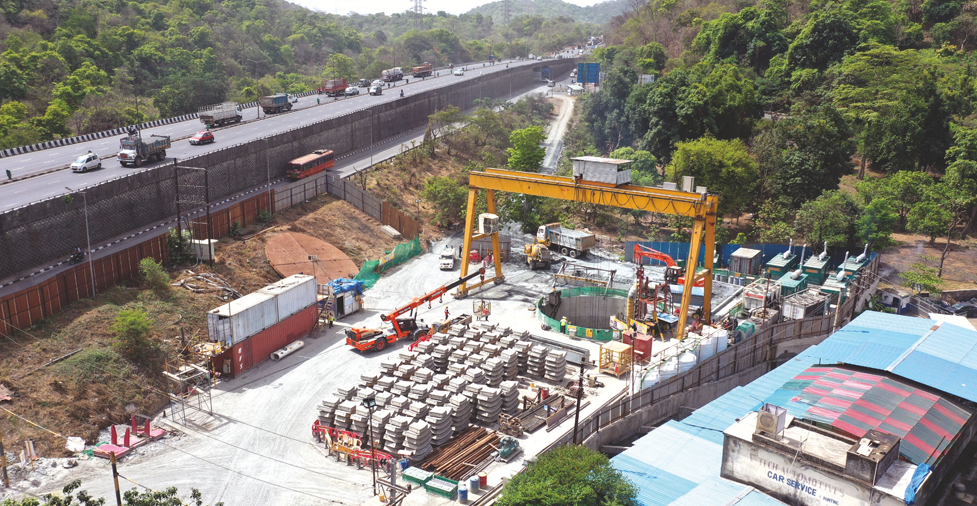
Engineer (MECH), Jitendra Thombre Prakash is glad that IoT devices have enhanced the efficiency of their project that is spread across 80 kms, alongside a highway. Assistant Construction Manager (CIVIL) – Planning, Surajit Mondal adds, “Fuel sensors have been installed on more than 50% of the assets, diesel dispensing is being monitored by an RFID- based. system, the first of its kind, and diesel distribution is through an automated FDMS system.” While e-Pragathi tracks project progress, real-time asset monitoring is through a web portal and a mobile application called SPOTRACK, accessible to all key stakeholders.
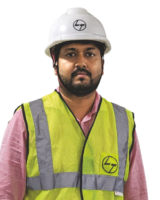
Surajit Mondal
Assistant Construction Manager
(CIVIL) – Planning
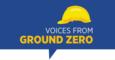

“Fuel sensors have been installed on more than 50% of the assets, diesel dispensing is being monitored by an RFID- based system, the first of its kind, and diesel distribution is through an automated FDMS system.”
Although the team has achieved a lot, there is still some distance to go before delivering their project. “Bulk water supply of 218 ML to Mira Bhayander Municipal Corporation and 27 villages in Vasai-Virar City Municipal Corporation area covering some 16 lakh people is planned by end May 2024,” shares Colin. Testing, trial runs and commissioning are also planned by then, and going by their track record, there is no doubt that Colin and his team will certainly deliver.
GANGADHAR MEHER LIFT IRRIGATION PROJECT
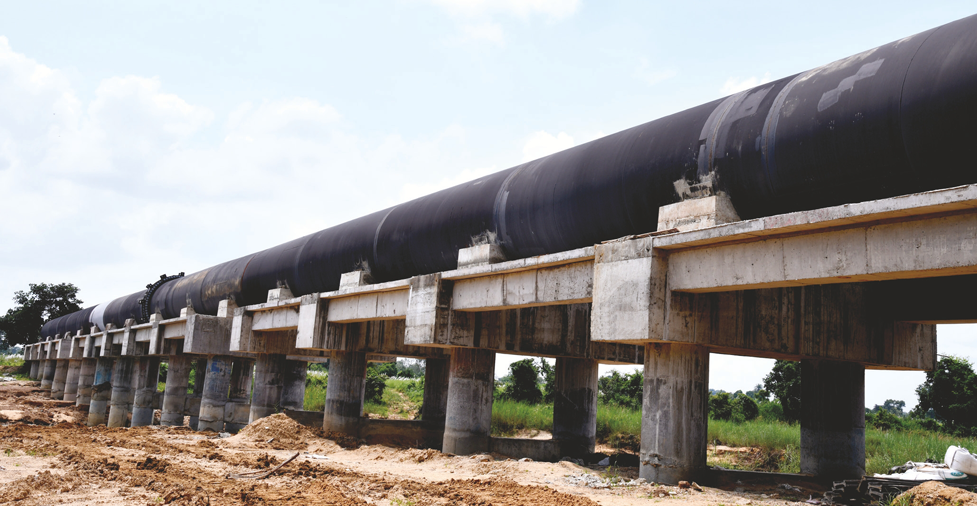
The Gangadhar Meher Lift Irrigation Project, awarded in March 2021 by the Department of Water Resources (DoWR), Government of Odisha, involves constructing an intake structure with pressure main from RD 0.00 Km to 34.10 Km along the right bank of Bargarh Main Canal (BMC) on an EPC turnkey basis, including a power connectivity system and O&M for 5 years. The project envisions to meet the irrigation needs of 25,600 Ha upland areas in the districts of Bargarh and Sonepur. Project Manager, Rajasekar S, can afford to smile at the progress and profitability of his project.
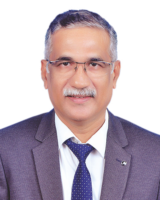
Rajasekar S
Project Manager
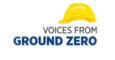

“We have completed 93% of the project as of July 2023 thanks to our careful planning, precise and timely mobilization and procurement, and effective stakeholder engagement.”
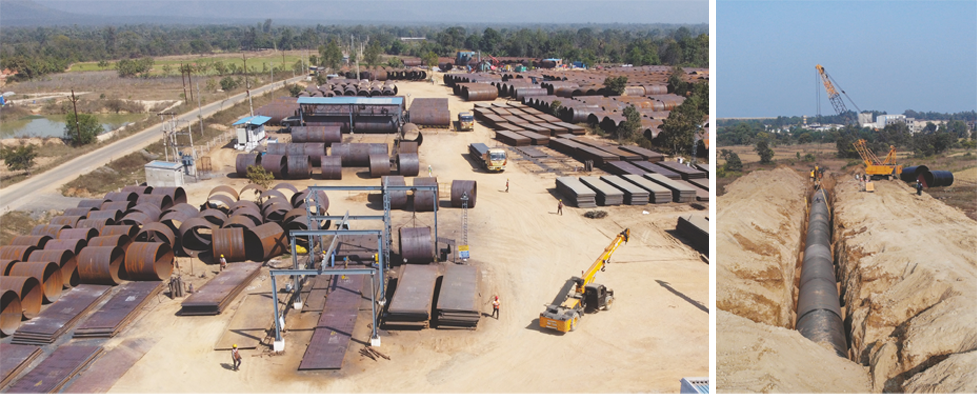
Valuing that time is of the essence
Using RTK (Real Time Kinematics) drone survey to finalize the intake structure and pressure main alignment dramatically reduced the survey time, which in turn helped the EDRC team to finalize the design on time. Optimizing certain design concepts, have reduced the cost of construction too. Another favourable turn for the team has been timely approvals and procurement, thanks to the good coordination between the EDRC team, the Consultant and Client.
Once the design was approved, 33,735 MT of MS plates were purchased from SAIL, Tata and JSPL and delivered before the contractual milestone to fabricate 3.00 m dia MS pipes. “This reduced the cost of procurement as steel prices have gone up after placing the order,” remarks Rajasekar, adding, “During the initial stage of the project, we completed three inlet ducts connected with the Bargarh Main Canal and tail race channel of the hydro power plant within 2 months, as shutdown work commenced during the monsoon.”
After searching the entire stretch of the pressure main alignment, the project team finalized land for the fabrication yard in the middle of the alignment that reduced the cost of shifting the pipes and additionally, identified government lands in close vicinity to stack them. With the pipe fabrication yard located away from the nearby villages, the team was free to work smoothly without any local hindrances. The pipe fabrication and coating works commenced in top gear in two shifts, and they completed the work two months in advance. The factory licence and statutory approvals too were obtained by the site team on time.
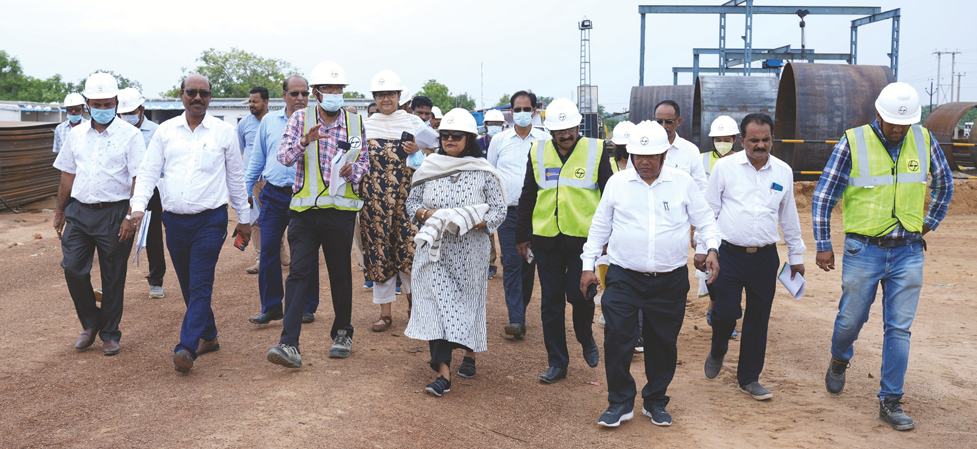
Sudarsan Dutta, Assistant Construction Manager (Civil), is thrilled at the appreciation from the client and consultants for the automated process of applying food grade epoxy coating inside and coal tar epoxy coating outside the pipes that have saved them considerable time. “We completed the pipe fabrication and coating works 2 months in advance against the planned target,” he shares with a thumbs up, “that gave us the confidence that we could complete this project on time.”
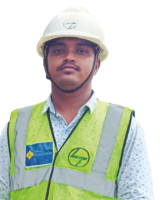
Sudarsan Dutta
Assistant Construction Manager
(Civil)
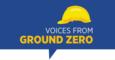

“We completed the pipe fabrication and coating works 2 months in advance against the planned target, that gave us the confidence that we could complete this project on time.”
Timely mobilization of resources
All the resources like workmen, materials, and machinery, including higher-capacity cranes for pipe laying works, have been speedily mobilized, keeping the project on track. “The pump, motor and electro-mechanical materials were procured on time,” states Syed Najaf Hussain, Assistant Construction Manager (Planning). “In fact, we unloaded two
20 MVA transformers directly onto a pedestal to save time and avoid possible damages.”
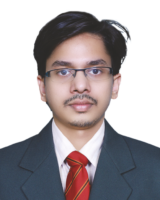
Syed Najaf Hussain
Assistant Construction Manager
(Planning)
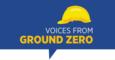

“The pump, motor and electromechanical materials were purchased on time. In fact, we unloaded two 20 MVA transformers directly onto a pedestal to save time and avoid possible damages.”
Effectively addressing engineering challenges
The pipe carrying structures at the three river crossings at Jira, Grisul and Danta spanning around 500 m was completed within three months much to the client’s delight, made possible due to the dedicated efforts of Narayan Patra, Tapan Kumar Giri, Sudarsan Dutta, Israel Sheik and Sakthivel during peak summer. The proposed pressure main alignment crosses the ACC cement railway line, and the work was carried out meticulously to restore the railway line within 48 hours by an open cut method involving Narayan Patra, Rajkumar, Abhijit Ghosh, and Barada Kant Nayak.
Suvendukrishna Pattnaik and Prabhakar Baral managed timely possession of ROU/ROW by coordinating with the local villagers, farmers, landowners, client & district administration. The crop compensation was paid in time through DDs to the affected farmers in the proposed alignment, which helped the team to execute pipe laying without having to leave any gaps.
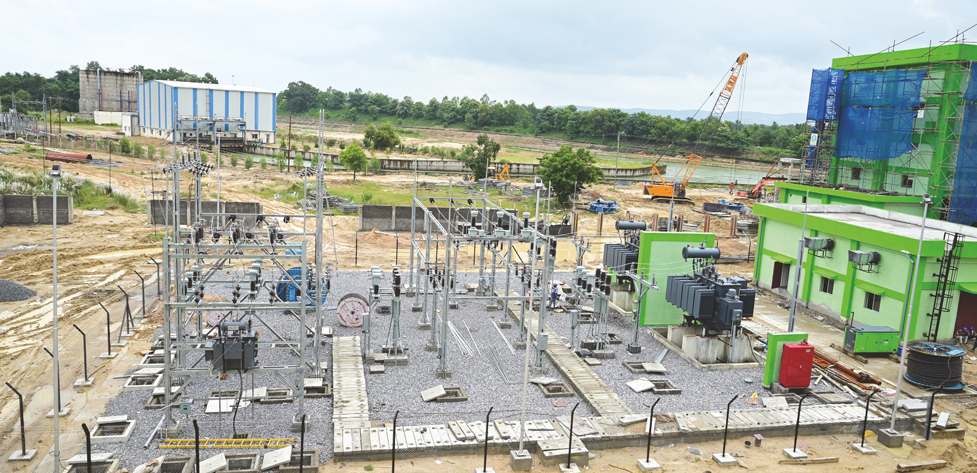
“In some locations, we dug 8 m wide x 0.6 m deep trenches in advance before cultivation to lay the pipes that helped us to smoothly complete around 9 km of MS pipe laying,” mentions a beaming Saleem Raza, Construction Manager (MECH).
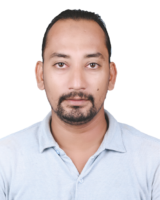
Saleem Raza
Construction Manager (MECH)
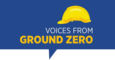

“In some locations, we dug 8 m wide x 0.6 m deep trenches in advance before cultivation to lay the pipes that helped us to smoothly complete around 9 km of MS pipe laying.”
Delighted that his team has ensured timely payments from the Client to maintain a positive cash flow, Rajasekar sums up. “We have completed 93% of the project as of July 2023 thanks to our careful planning, precise and timely mobilization and procurement, and effective stakeholder engagement.” He is equally glad that the Chief Secretary, Additional Chief Secretary, Engineer in Chief (DoWR) and other government officials who visited the pumphouse and pipe yard locations have appreciated for the project team’s efforts. With just finishing touches required, the team is well on their way to deliver a winner!